线切割机床单边松丝的分析与处理
经常有线切割会发现丝一边松、一边紧,用过很多种方法去处理,未能彻底解决。以下是北京凝华处理一台单边松丝的机床的过程,可以提供给大家参考。
处理流程:
1、用切割加工的方法首先复现故障现象,详细记录加工的各种参数、切割时间等指标。故障现象复现以后,要让相关人员确认现象相同。
2、处理的时候分步骤,按顺序验证,每一步处理,按照分析-方案-备案-验证-记录的流程。
3、分析故障原因,并制定出解决方案和处理办法,报技术主管备案。
4、开始实施处理方法,处理以后验证结果,并详细记录。
5、如果没有解决问题,再次按照这个流程重复处理。
处理过程记录
1、故障复现切割工件厚30,长200,45#钢一件,重新上丝,紧丝后开始切割,脉宽8US,脉宽64US,电压100V,电流1.5A共计切割4小时,丝筒正反转切割进给速度基本一致。钼丝未见松动。钼丝未换,切割工件厚100,长80,45#一件,脉宽32US,脉宽240US,电压100V、电流2A共计切割5小时,3小时后丝筒正反转切割进给速度开始有差异。现象是丝筒顺时针运转机床进给缓慢,丝筒逆时针运转机床进给快,用手触摸丝筒两边的钼丝有一边松一边紧。切割工件厚100,长80,45#一件,脉宽32US,脉宽240US,电压100V,切割现象同上,切割50MM断丝。时长2小时切割工件厚100,长150,45#一件,脉宽32US,脉宽240US,电压100V,切割现象同上。丝筒正转进给0.15mm,丝筒逆转进给0.08mm。时长5小时
2、问题分析观察机床冲水正常,根据上述反应推断丝筒在正反转时钼丝在产生抖动或变位现象,而且有阻力致使钼丝在运行中产生紧丝一样的外力,观察机床后导轮虽然转动比较灵活但已经让钼丝勒出一条不太明显的小沟,断丝保护的导电块和下丝架导电块已经松动钼丝在正反向运动时导电块有明显转动,且比一般机床导电块安装位置稍高,将钼丝抽掉测量丝筒的圆跳动<0.02mm符合国标,为了辨别丝筒在直线移动时有没有上下起伏和前后移动脱开丝杆推动丝筒用千分表分别测量丝筒的侧母线和上母线测量值为<0.025mm,丝筒这种情况不会造成钼丝一边松一边紧。经过我们工程师的探讨分析是由钼丝在上下运动时受到不同的阻力所致,根据分析原因应该出在这里,后对整个丝架进行测量后(包括刚性、抖动、导轮组件安装孔的的形位)进行适当调整,将导轮组件、导电块组整体更换。准备进一步测试推断问题是否还能出现。
3、再次切割切割工件厚100,长150,45#一件,脉宽32US,脉宽240US,电压100V,切割现象略有改进。丝筒正转进给0.15mm,丝筒逆转进给0.1mm。切割4小时后钼丝还是有松动现象。
4、对比测试将工件放于另一台调试合格的DK7732A机床,切割工件厚100,长150,45#一件,脉宽32US,脉宽240US,电压100V,钼丝运动正常,冲水完好冷却液完全包络钼丝,切割现象:“丝筒正转进给0.15mm,丝筒逆转进给0.13mm。切割现象正常,0.02进给量的差异根刚性和钼丝运动以及一些机床本身精度有关,切割4小时后观察钼丝没有松动现象。将工件放于另一台调试合格的7732B机床,切割工件厚100,长180,Cr12一件,脉宽32US,脉宽240US,电压100V,钼丝运动正常,冲水完好冷却液完全包络钼丝,切割现象:“丝筒正转进给0.15mm,丝筒逆转进给0.13mm。切割现象正常,0.02进给量的差异根刚性和钼丝运动以及一些机床本身精度有关,切割4小时后观察钼丝没有松动现象。
5、均衡阻力测试根据对比试验推断这台机床还是有问题,但已理论分析原因只能出在阻力这个原因上,经过仔细思考后,去除后导轮和断丝保护导电块,将钼丝在上丝架和下丝架的阻力约设为相同,装新钼丝后切割测试。切割工件厚100,长150,45#两件,脉宽32US,脉宽240US,电压100V,钼丝运动正常,切割3万平方毫米两边钼丝松紧没有明显差别,丝筒正反转工作台进给量几乎相等(0.27):
问题的原因基本出现,又重新穿上钼丝经过后导轮但去除断丝保护导电块,切割测试。切割工件厚100,长150,45#一件,脉宽32US,脉宽240US,电压100V,钼丝运动正常,切割1.5万平方毫米两边钼丝松紧没有明显差别,丝筒正反转工作台进给量0.28正反转相差0.05。又去除后导轮和断丝保护导电块,将钼丝在上丝架和下丝架的阻力约设为相同,装新钼丝后切割测试。切割工件厚100,长150,45#两件,脉宽32US,脉宽240US,电压100V,钼丝运动正常,切割1.5万平方毫米两边钼丝松紧没有明显差别,丝筒正反转工作台进给量0.28丝筒正反转差异0.03。
总结,根据上述试验,可以给出结果丝筒单边松丝的现象这台机床有,原因出现在上丝架导电块安装位置比较高,后导轮运转不够灵活,致使丝筒在正转时丝筒到后导轮这段钼丝收紧,导致丝筒运转时间一长,右边的丝比左边的紧,1、3段钼丝较松,2、4段钼丝稍紧于1、3段,5段钼丝比较松,由于这个阻力不是很大所以钼丝不是紧的很快,丝筒反转时标记为5的那段钼丝收紧, 4、2段钼丝稍松于1、3段钼丝,致使4段钼丝位置移动,最后阻力导致丝筒到后导轮这段钼丝比较松,由于这个阻力不是很大所以钼丝不是松的很快,丝筒在长时间正反转工作的情况下钼丝逐步出现了一边松一边紧,而且很有规律性,由于4段钼丝在丝筒正转和反转时的松紧程度不一致导致进给速度一边快一边慢。如果将后导轮和断丝保护的导电块去除这种现象有明显好转。北京凝华以后如果出现这种情况我推荐维修方法是:将上丝架两导电块下移减少阻力,将上丝架的后导轮调致灵活松动,改善冲水条件,调整上丝架整体刚性。进行穿丝,受阻情况与图近似,检查各导轮运转灵活,导电块固定有效,冷却液使用不新不旧,重新紧丝(使钼丝松紧程度均衡),运丝后观察钼丝在丝筒顺逆转动时没有抖动后,让机床运丝空转10分钟,然后在等高架上夹装一件厚度91的Cr12材料,调整电参数:电压100V,脉宽32,脉间8倍,平均电流2.2A后进行L1方向切割40mm观察,进刀2mm后观察丝筒正转工作台进给量为0.3mm,丝筒反转工作台进给量为0.32mm,加工情况基本和正常机床相同,加工效率为63mm2/min 加工面积3640mm2,切割完毕观察钼丝没有松动。(用时间90分)
一件厚度91的Cr12材料,调整电参数:电压100V,脉宽32,脉间8倍,平均电流2.2A后进行L3方向切割40mm观察,进刀2mm后观察丝筒正转工作台进给量为0.3mm,丝筒反转工作台进给量为0.32mm,加工情况基本L1方向相同,加工效率为63mm2/min加工面积3640mm2,切割完毕观察钼丝没有松动。(用时间60分钟)两件厚度91的Cr12材料,调整电参数:电压100V,脉宽32,脉间8倍,平均电流2.2A后进行L3方向切割40mm,L1方向切割40mm,供切割80mm,观察丝筒正转工作台进给量为0.3mm,丝筒反转工作台进给量为0.32mm,加工情况基本L1方向相同,加工效率为63mm2/min加工面积7280mm2,切割完毕观察钼丝没有松动。(用时间120分钟)两件厚度91的Cr12材料,调整电参数:电压100V,脉宽32,脉间8倍,平均电流2.2A后进行L2方向切割40mm,L4方向切割40mm,供切割80mm,观察丝筒正转工作台进给量为0.3mm,丝筒反转工作台进给量为0.32mm,加工情况基本L1和L3方向相同,加工效率为63mm2/min加工面积7280mm2,切割完毕观察钼丝没有松动。(用时间120分钟)根据上述切割试验,共计切割面积43680mm2,用时390分钟,没有出现单边松丝或者两个方向进给不一致的现象,由于我们推断是因为导电块和后导轮造成的单边松丝,所以请技术部加工组,检测机床精度后继续切割试验,推荐使用周期1个月,最好使用此机床切割100mm以上的工件,观察机床还有没有用户处所述现象
故障再次复现更换新钼丝,方法进行穿丝,受阻情况与图近以下图似,检查各导轮运转灵活,导电块固定有效,冷却液使用不新不旧,紧丝(使钼丝松紧程度均衡),运丝后观察钼丝在丝筒顺逆转动时没有抖动后,让机床运丝空转10分钟,然后在等高架上夹装一件厚度91的Cr12材料,调整电参数:电压100V,脉宽32,脉间8倍,平均电流2.2A后进行L1和L3方向切割共切割400mm,后观察丝筒正转工作台进给量为0.24mm,丝筒反转工作台进给量为0.3mm,现象复现,加工效率为63mm2/min 加工面积36400mm2,切割完毕观察钼丝没有松动。(用时间577.7分)
总结,丝筒正反转竟给速度不一致,和走丝方法有密切关系,根据实验结果我们可以看出,钼丝没有松到一定程度不会影响切割效果,更换了导轮、导电块组件后单边松丝的问题完全消除了,但丝筒正反转竟给速度不一致却没有完全去除,总之以后如果有某台机床出现上述情况,我们首先要着手检查的是:喷水是不是可以完全包络钼丝能使冷却液充分进入切割缝隙形成有效的放电和灭弧过程,检查上下丝架的刚性尤其是螺钉有没有有效的固定,另外一定要注意上丝架压压板后丝架的接触面和立柱刮削面是否有效的接触(如没有导轮孔会形成倾斜增大阻力),导轮转动一定要灵活,导电块高低最好稍高于导轮母线,穿装钼丝时要掌握钼丝受力最小且有效的接触导轮和导电块为宜,维修人员维修前可以先测量一下丝筒的圆跳动<0.02mm,辨别丝筒在直线移动时有没有上下起伏(方法:脱开丝杆推动丝筒用千分表分别测量丝筒的侧母线和上母线测量值为为起伏量),根据我个人分析起伏量小于0.05的情况下在短时间切割的情况下不会对切割效果有很明显的影响。如果是丝杠安装不当会造成运行中阻力不一致导致钼丝明显移位。
声明:本网站所收集的部分公开资料来源于互联网,转载的目的在于传递更多信息及用于网络分享,并不代表本站赞同其观点和对其真实性负责,也不构成任何其他建议。本站部分作品是由网友自主投稿和发布、编辑整理上传,对此类作品本站仅提供交流平台,不为其版权负责。如果您发现网站上所用视频、图片、文字如涉及作品版权问题,请第一时间告知,我们将根据您提供的证明材料确认版权并按国家标准支付稿酬或立即删除内容,以保证您的权益!联系电话:010-58612588 或 Email:editor@mmsonline.com.cn。
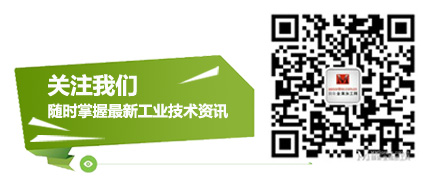
- 暂无反馈