铝加工知识共
影响剪切质量的主要因素有:(刀具质量)、(配刀工艺)、(设备状况)及(来料质量)。
分切的卷取质量主要是指(带材经缠绕后的端面质量),包括塔形错层和燕窝。
影响卷取质量的主要因素有(卷取张力)、(分离盘的配置)、(纸芯强度)、(对中机构)和(来料状况)。
铝箔轧制中厚度的测量方法有(涡流测厚)、(同位素射线测厚)、(X射线测厚)。
冷轧压下制度主要包括(总加工率的确定)和(道次加工率的分配)。
两次退火之间的总加工率称为(中间冷轧总加工率),控制产品的最终组织与性能所选取的总加工率称为(成品冷轧总加工率)。
轧制压力指的是(轧件对轧辊合力的垂直分量),即轧机压下螺丝所承受的总压力。
冷轧指的是(在再结晶温度以下的轧制生产方式)。
张力大小的确定要视不同的金属和轧制条件而定,但最大张应力值不能(大于或等于)金属的屈服程度。
X射线测厚仪的根本结构包括(放射源)、(检测器)、(标准块盒)。
铝材表面质量从轧制(表面粗糙度)、(表面光亮度)、(表面显微形貌)三个方面反映。
润滑轧制条件下,辊面粗糙度对铝材表面质量的影响程度会受到(轧件与轧辊之间油膜厚度与状态)的制约。
随着轧件原始表面粗糙度增大,轧后轧件表面粗糙度呈(线性)增加。
轧制时变形不均,出现一边长一变短的现象称为(镰刀弯)。
由于板形严峻不良,在铝箔卷取或展开时形成皱褶的现象称为(起皱)。
轧制前有水滴在箔面上,轧制后形成的白色斑迹,轻时会影响铝箔表面,严峻时发生断带的现象称为(水斑)。
铝箔表面周期性的横波称为(振痕)。
轧辊磨削的要害在于(控制表面粗糙度)。
轧辊磨削参数主要有(砂轮速度)、(轧辊速度)、(轴向进给量)、(径向进给量)。
砂轮的特性主要包括(磨料)、(粘度)、(硬度)、(结合剂)、(组织外形)和(尺寸)等。
选择砂轮的原则是(粗磨时切削性能好,金属切除率高)、(精磨时砂轮的等高性)、(微韧性好)、(磨学法热削)。
轧辊的组成部分是(辊身)、(辊颈)、(接头)和(顶尖空)。
边部波浪的调节方法(适当增加压下量)、(适当增加张力)、(适当提高轧制速度)、(增大边部喷淋量)。
中波的调节方法(适当减少压下量)、(适当减少张力)、(适当减小轧制速度)、(增大中部喷淋量)。
轧辊的凸度及辊形曲线是通过(轧辊磨床的成形机构)来实现的。
轧辊表面粗糙度的均匀性对产品的(板形质量)会发生影响。
是由于轧制时板带材宽度的各部位纵向延伸不一致所引起的现象称为(波浪)。
铝箔退火的方式有(普通空气电阻炉退火)、(保护性气体退火)、(变压退火)、(真空炉退火)。
退火后冷却速度的选择应考虑的因素是(铝箔卷的厚度)、(宽度)和(直径组织及性能)、(生产效率)。
(加热温度的高低)对铝箔的组织和性能影响最大。
铝箔退火时快速加热易得到(细小均匀)的组织,改善其性能。
轧机发生火灾应具备的3个条件是(可燃物)、(助燃物)、(火源)。
硅藻土是一种硅酸盐材料,具有(多孔性)、(较低的密度)、(较大的表面积)、(相对不可压缩性)及(化学稳定性)的独特性能。
过滤原理与工艺是(预涂周期 ) 、(根本供应周期) 、(滤层和过滤布的更换)
换工作辊后轧辊的预热时间为(10)分钟,换支撑辊后的预热时间不少于(30)分钟。
轧制进程中,轧辊发生(弹性)变形和(热)变形。
造成板中央和板边部单位厚度差所需要的轧制力称为(轧机横刚度)。
车间800冷轧机液压系统有(压上)系统、(弯辊)系统、(辅助)系统、(对中)系统;
油雾润滑系统主要运行参数:风压(0.35-0.7MPa),气温(50-70℃),油温(40-60℃) 。
轧机润滑方式主要种类有(稀油润滑)、(油雾润滑)、(干油润滑)。
退火炉主要巡检项目有(风机有无异响)、(皮带是否完好)、(循环水压力是否正常)、(料车轮及轴承有无磨损)
CO2自动灭火系统氮气瓶压力应保持在(5MPa)
工艺冷却系统要求工作时供油压力(0.3MPa);油温(35-45℃)
弯辊系统采用的是(比例减压阀),其要求油液洁净度为10μm;压上系统采用的是(伺服阀),其要求油液洁净度为3μm;
三辊展平装置主要有(2)根动辊,(1)根定辊;其润滑方式为(油雾润滑)
卷取胀缩轴的结构为(四斜楔式)
弯辊系统压力(10MPa);辅助系统压力(6.3MPa)
冷轧车间主要设备有(800冷轧机列)、(纵剪机列)、(退火炉)、(磨床及行车)等
冷轧机直流传动采用(调压和调磁)相结合方式,开卷、卷取机采用(恒张力控制系统)
厚度自动控制系统由(厚度检测部分)、(自动控制装置)、(执行机构和调节方式)等组成;厚度检测有(测厚仪)完成,其控制精度为(±5цm)。
厚度自动控制系统的监控投入条件:(开卷、卷取张力建立)(轧制速度必须大于传带速度)(测厚仪到位且正常测量)
1#厚调自动控制装置由(MSC)、(AGC)、(HOST)、(VDG)、(OPC)等五部分组成。
轧机压下系统一次压靠的轧制力为(40T),二次靠零压力为(80T)。
辅助、机列及油系统采用(PLC)控制形式。
炉子四周(1.5)米以内的地面,必须保持干燥,以防止液体金属溢出时炸伤人,更不答应将液体金属倒在(潮湿)的地方及(有水)的斗内。
熔炼炉、静止炉不答应(超容量)工作,最大投入量不允许超过(设计)量。
粘辊达(1/2)周时,要立刻停车,防止设备损坏。
凡倒炉时必须更换(控制钎子)。
静止炉在冲洗、清炉,换加热器元件时都必须(停电),操作完毕查看确认四周(无人)方准送电,炉墙电阻丝的保护(档板)不的随意摘下
前箱温度一般控制在(695-715)℃之间
熔铸车间的液压部分有(阀台)、(泵站)、(仪表箱)三部分组成
铸轧板的缺陷有(热带)、(气道)、(裂纹)、(夹渣)等
熔铸车间运用的铁剂含铁量为(75%)
铝液除氢技术的根本趋势是以(气泡浮游法)为主
停机后放跑流锭时,必须查看斗内有无(水)、确认(干燥),后方可放铝,以防止(爆炸)
每卷的末尾出截取(40--50)mm宽的铸轧板做(晶粒度)、(横向厚差)、(中凸度)的查看
生产进程中,过滤片的入流侧超过正常液面高度(5)cm时,说明堵塞,应立刻进行更换
轻质砖在运用前,应先在预热炉里预热,温度在(100-250)℃之间,保温(4)小时左右
铸轧前必须查看(水泵)、(铸轧机)、(卷取机)、(液压系统)、(高压泵)、(低压泵)、(润滑装置)是否正常,无问题时方可运用。
大小操作台应(专人)负责,他人不能随意乱动,铸轧机运行期间,严禁(外来人员)靠近。 google_ad_width = 468;
立板出现的各种异常现象,可通过调整(铸轧速度)、(前箱液面高度)等工艺参数,使异常现象消失,再正常立板。
开动轧机时,不允许用(钎子)、(渣刀)等物触动按钮开关,必须用(手)动,同时(发出信号),引起周围人注重。
铸轧结束后,将吊流槽预备好,严禁流槽中的残铝往(潮湿)的地面上倒。
2系合金的主要成份是:Cu
3系合金的主要成份是:Mn
4系合金的主要成份是:Si
5系合金的主要成份是:Mg
6系合金的主要成份是:Mg+Si
热轧机最大开口度是:380mm
声明:本网站所收集的部分公开资料来源于互联网,转载的目的在于传递更多信息及用于网络分享,并不代表本站赞同其观点和对其真实性负责,也不构成任何其他建议。本站部分作品是由网友自主投稿和发布、编辑整理上传,对此类作品本站仅提供交流平台,不为其版权负责。如果您发现网站上所用视频、图片、文字如涉及作品版权问题,请第一时间告知,我们将根据您提供的证明材料确认版权并按国家标准支付稿酬或立即删除内容,以保证您的权益!联系电话:010-58612588 或 Email:editor@mmsonline.com.cn。
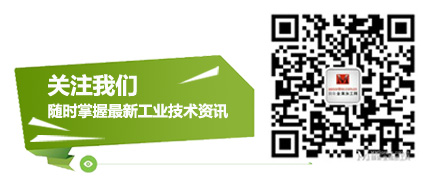
- 暂无反馈