分析:高速走丝电火花线切割加工断丝原因
对高速走丝电火花线切割加工断丝的主要原因进行的分析,并提出了解决的方案,最后从实证的角度,对生产中断丝现象进行的简单的故障排除的实证研究。
电火花线切割加工(WirecutElectricalDischargeMachining,简称WEDM),有时又称线切割。其基本工作原理是利用连续移动的细金属丝(称为电极丝)作电极,对工件进行脉冲火花放电蚀除金属、切割成型。电火花线切割机按走丝速度可分为高速往复走丝电火花线切割机,俗称快走丝;低速单向走丝电火花线切割机,俗称慢走丝和立式自旋转电火花线切割机3类。又可按工作台形式分成单立柱十字工作台型和双立柱型(俗称龙门型)。
1电火花线切割加工原理
电火花线切割属电加工范畴,是由前苏联拉扎林科夫妇研究开关触点受火花放电腐蚀损坏的现象和原因时,发现电火花的瞬时高温可以使局部的金属熔化、氧化而被腐蚀掉,从而开创和发明了电火花加工方法。线切割机也于1960年发明于前苏联,我国是第一个用于工业生产的国家。电火花线切割加工主要用于模具制造,在样板、凸轮、成形刀具、精密细小零件和特殊材料的加工中也得到日益广泛的应用。
其工作原理为:自由正离子和电子在场中积累,很快形成一个被电离的导电通道。在这个阶段,两板间形成电流。导致粒子间发生无数次碰撞,形成一个等离子区,并很快升高到8000℃~12000℃的高温,在两导体表面瞬间熔化一些材料,同时,由于电极和电介液的汽化,形成一个气泡,并且它的压力规则上升直到非常高。然后电流中断,温度突然降低,引起气泡内向爆炸,产生的动力把溶化的物质抛出弹坑,然后被腐蚀的材料在电介液中重新凝结成小的球体,并被电介液排走。然后通过NC控制的监测和管控,伺服机构执行,使这种放电现象均匀一致,从而达到加工物被加工,使之成为合乎要求之尺寸大小及形状精度的产品。
在切割加工时,工件安装在工作台上,工作台通常由X轴和Y轴电动机驱动。工具电极(电极丝)为直径0.02mm~0.3mm的金属丝,由走丝系统带动电极丝沿其轴向移动。走丝方式有两种:1)高速走丝,速度为9m/s~10m/s,采用钼丝作电极丝,可循环反复使用;2)低速走丝,速度小于10m/min,电极丝采用铜丝,只使用一次。脉冲电源加在工件与电极丝之间,一般工件接正极,电极丝接负极。工件与电极丝之间用喷嘴喷入工作液(乳化液、去离子水等)。控制系统根据预先输入的工作程序输出相应的信息,使工作台作相应的移动,工件与电极丝靠近。当两者接近到适当距离时(一般为0.01mm~0.04mm)便产生火花放电,蚀除金属。金属被蚀除后工件与电极丝之间的距离加大,控制系统根据这一距离的大小和预先输入的程序,不断地发出进给信号,使加工过程持续进行。
2电火花切割机
电火花线切割机主要。采用电脑控制系统,全中文自动绘图编程、控制软件。加工中有轨迹、时间显示,可随时了解加工情况中走丝具有多次切割功能特点通常来讲,电火花切割机的主要功能有:具有绘图、编程功能;镜像、对称、旋转、平移功能;短路自动处理、加工结束自动停机功能;反向加工、任意段加工功能;比例缩放功能;断电报护功能;自动找中心功能;人机对话功能。
3断丝主要原因
3.1与电参数选择及脉冲电源相关的断丝
一般来说,断丝的机率随着放电能量的增加而加大。这是因为加工中的脉冲能量靠电极丝来传递,如果电极丝载流量太大时,本身的电阻发热会使它固有的抗拉强度降低很多,所以很容易造成断丝。可将脉冲间隙参数设大些,以有利于熔化金属微粒的排出。同时峰值电流和空载电压不宜过高,否则容易产生集中放电和拉弧。由于电弧放电是造成电极丝(负极)腐蚀损坏的主要因素,只要电弧放电集中于某一段,就会引起断丝。
3.2与运丝机构相关的断丝
机床的运丝机构精度变差,会增加电极丝的抖动,破坏火花放电的正常间隙,易造成大电流集中放电,从而增加断丝的机会。这种现象一般发生在机床使用时间较长、加工工件较厚、运丝机构不易清理的情况下。因此在机床使用中应定期检查运丝机构的精度,及时更换易磨损件。在上丝后应空载走丝检查电极丝是否抖动,若发生抖动要分析原因。
3.3与电极丝相关的断丝
电极丝的材料应根据加工情况而定,否则会引起断丝。对于数控高速走丝电火花线切割加工,广泛采用钼丝。因为钼丝耐损耗、抗拉强度高、丝质不易变脆,不易断丝。采用钨丝加工,可获得较高的加工速度,但放电后丝变脆,易断丝,应用较少,一般在弱电规准时使用。钨钼丝(钨、钼各50%)加工效果比前两种都好,故使用寿命和加工速度都比钼丝高,但价格昂贵。
3.4与工件相关的断丝
未经锻打、淬火、回火处理的材料,钢材中所含碳化物颗粒大,并且聚集成团,而分布又不均匀,存在较大的内应力。如果工件的内应力没有得到消除,在切割时,有的工件会开裂,把电极丝碰断,有的会使间隙变形,切缝变窄而卡断电极丝。为减少因材料引起的断丝,在电火花线切割加工前最好采用低温回火消除内应力。应选择锻造性能好、淬透性好、热处理变形小的材料,钢材中所含碳化物分布均匀,从而使加工稳定性增强。如以电火花线切割加工为主要工艺的冷冲模具,尽量选用CrWMn、Cr12Mo、GCr15等合金工具钢,并要正确选择热加工方法和严格执行热处理规范。
3.5与工作液相关的断丝
工作液在较长时间使用后,变得脏污、综合性能变差是引起断丝的重要原因。根据加工经验,新换的工作液每天工作8小时,使用两天后效果最好,继续使用8d~10d则易断丝,须更换新的工作液。对要求切割速度高或大厚度工件,其工作液的配比可适当淡一些,约5%~8%的浓度,这样加工较稳定,不易断丝。用纯净水配置的工作液加工较自来水配置的工作液在加工中更稳定,较少断丝。
4断丝解决对策
下面从实际生产的角度出发,以DK7725高速走丝电火花线切割机断丝的问题,总结高速走丝线切割机断丝的普遍原因,找出减少断丝的具体方法。
4.1选择更换钼丝
一般来说,钼丝的质量直接关系到断丝现象的发生,最简单的更换名牌钼丝厂生产的钼丝。高速走丝线切割机进行加工时,一般来说,须选用质量好的较粗的电极丝。如:用南京钻石牌钼丝调试一下。在选择钼丝时,并不是越大越好,应根据用电参数进行选择。
4.2选择合适的加工件
在实际生产中,如果加工工件质量不过关,如有焊点、多层、两种材质、以及材料里有气泡和碳渣等杂质时,在加工中很容易发生断丝。遇到这种情况,最简单的办法就是直接调换一块加工材料。
4.3调整合适的用电参数
在加工时,一定要依照说明书根据不同厚度和不同材质选择适合的电参数。无论怎样加工,必须调整到加工电流相对稳定,否则也会经常引起断丝。
4.4适时检查可能夹断钼丝的构件
长期运行后,可能会在运丝机构上产生一些槽沟等影响运行精度的,而致钼丝夹断。所要要定期检查并及时更换轴承、导轮、导电快、挡丝棒等运丝部件。更换周期为:轴承大约为3个月更换一次,导轮为半年更换一次。
4.5精心选用乳化液
乳化液是走丝运行的润滑剂,按切削液说明配比工作液,可大大减少断丝现象发生。有条件的可以用纯净水。切削液尽量用名牌产品。如:南京达兴牌(油基型)浙江佳润牌(水基型)。
4.6全方位提高操作人员素质
断丝现象的发生,与操作也有极大的关系。实践证明,操作得当,断丝现象能够得到极大的减少。为此,在上丝、穿丝操作时应仔细认真、规范操作。同时,要在自动找中心时,如果工艺孔壁有油污、毛刺或某些不导电的物质,当电极丝移动到孔壁时未火花放电,致使机床不能自动换向,最后勒断电极丝。因此加工前一定要将工艺孔清理干净。某些时候需要手动切割时(人为控制进给),应眼观电流表,不得超过正常切割时的变频速度,否则极易断丝。
5实证研究
故障现象1:DK7725工作台工作中,火花放电突然变为蓝色的弧光放电,电流超过限值,电极丝烧断,停机更换电极丝后,开机运作,故障依然存在。接下来用用示波器测输入端和振荡部分都无波形输出,故判断故障出在振荡部分,检修振荡部分,高频电源恢复正常,工作台运转正常。
故障现象2:DK7725工作台工作中加工电流很大、火花放电异常断丝。根据经验判断,故障原因是因为脉冲电源的输出已变为直流输出所致。故从脉冲电源的输出级向多谐振荡器逐级检查波形,发现元件按损,更换后,检查输出标准的脉冲波形。开机运行,故障解除。
6结论
高速走丝电火花线切割加工断丝问题发生,只要掌握了基本的原理,再通过经验积累,是很容易解决的,如果出现不能解决的问题,一定要及时与生厂维修厂家联系,共同加以解决,决不能盲目蛮干导致工作台受损致更大损失。同时,要生产的各个环节,要注意及时发现和解决问题,并不断总结积累经验。
声明:本网站所收集的部分公开资料来源于互联网,转载的目的在于传递更多信息及用于网络分享,并不代表本站赞同其观点和对其真实性负责,也不构成任何其他建议。本站部分作品是由网友自主投稿和发布、编辑整理上传,对此类作品本站仅提供交流平台,不为其版权负责。如果您发现网站上所用视频、图片、文字如涉及作品版权问题,请第一时间告知,我们将根据您提供的证明材料确认版权并按国家标准支付稿酬或立即删除内容,以保证您的权益!联系电话:010-58612588 或 Email:editor@mmsonline.com.cn。
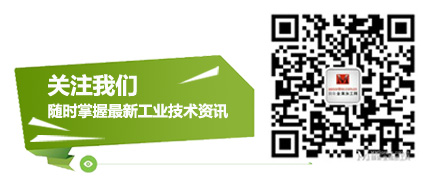
- 暂无反馈