针对直接驱动系统的测量技术
随着现代机床向高速、高精、高表面品质和高稳定性的方向发展,直接驱动技术的应用日益扩增。直接驱动系统的优势,只有在控制系统、电机和测量系统相互协调和配合之下才能得以充分发挥,测量系统对于体现直接驱动系统性能而言至关重要。基于光电式单场扫描技术的直线光栅尺/角度编码器具有高精度、高分辨率和细分误差小的优势,非常适合直接驱动应用。
从控制理论方面看,由于半死循环机床控制系统无法克服机床传动机构产生的传动误差、高速往复运动时传动机构的热变形误差和磨损,全死循环作为可以消除传动误差的控制理论已越来越多地应用到现代机床控制中。驱动技术方面,因直接驱动与传统驱动相比具有高精度、高动态特性、低摩擦、维护简单和高效率等特点,在机床行业获得广泛应用。测量技术方面,由于绝对式编码和界面技术、光电式单场扫描技术等的应用,测量反馈组件的精度、分辨率和安全性有了很大提高。
数控机床的效率提高有赖于控制系统、电机、机械部件和测量系统等的相互协调与配合。正确选择测量系统,对于机床的性能特别是直接驱动系统具有重要作用。直接驱动系统效率的表现在很大程度上取决于位置测量组件的选择,对测量组件有极高要求:①高的测量精度;②小的细分误差;③高的分辨率;④无干扰。
直接驱动技术
直接驱动的最大优势在于其驱动组件(直线电机或力矩电机)和被驱动组件(工作台或转台)之间没有其它传动部件,连接刚性高,因此直接驱动系统的控制环系统增益可远远大于传统驱动系统。高增益有其优点,但同时也增加了对测量组件输出信号品质的要求,于直线电机而言为直线光栅尺,于力矩电机而言则为角度编码器。
图1 直接驱动系统全死循环控制
图2 直线电机和力矩电机示意图
图3 细分误差对表面品质的影响
直接驱动系统没有专用于速度控制环的旋转编码器,其位置控制环和速度测量环共享同一测量组件(见图1)。速度控制环需要有很小的信号周期,由此,测量组件的分辨率需要足够高,从而保证机床低速运行时也能进行精确的速度控制。
直接驱动用直线光栅尺/角度编码器
直线光栅尺或角度编码器的光栅刻线采用光刻工艺刻制在玻璃或钢带基体上,这种刻线栅距极小且边沿清晰、均匀。配合非接触的光电式单场扫描技术和优质的信号处理电路,直线光栅尺和角度编码器可为直接驱动系统提供高精度、高分辨率和小细分误差的高品质信号,对污染相对不敏感(压题图中,红色区域为污染),最终保证驱动系统的位置测量精度、速度稳定性和较为恒定的温度,确保系统的平稳运行。
细分误差对直接驱动的影响
测量组件在采用增量式或绝对式测量方法获得两个相位差为90°的位置信号后,需进行进一步细分来达到所需分辨率。实际输出位置信号由于扫描方式、污染和后续电子处理等原因,会与理想正弦信号有偏差。在进行细分时,这种偏差会在一个信号周期内产生周期性的高频误差,即单信号周期内的误差或细分误差。
细分误差取决于测量组件的信号周期、刻线品质和扫描品质。目前采用光电式单场扫描的位置测量组件可将细分误差限制在信号周期的1%左右,例如信号周期为20µm的直线光栅尺,其细分误差为0.2µm。
细分误差不但影响直接驱动系统的定位精度,更会影响速度控制环的稳定性。控制系统的速度控制环按照进给系统的定位误差对驱动系统的工作电流进行计算,进而控制直线电机或力矩电机实施加减速。数控机床进给速度较低时,进给系统跟随细分误差。直接驱动系统由于高增益由此控制带宽大,在一个较大的速度范围内受细分误差影响较大。在铣削工件时,由于细分误差的影响,工件表面会有波纹状加工痕迹,严重影响到工件的表面品质,如图3所示。一般说来,波纹状痕迹的波长和振幅与细分误差成正比。
由于细分误差的存在,直接驱动的电机内部会产生附加电流,从而产生额外的热量和噪音。细分误差和电机进给速度越大,电机发热量和噪音越大。此外,控制系统从测量组件获取位置值时,若位置信号分辨率与细分误差较为接近,细分误差会被辨识为机床进给系统的运动误差,控制系统会随机性地向进给系统发送补偿信号。这会导致控制系统震荡,直线电机的导轨等机床运动部件长时间高频往复运动,从而加速磨损、降低使用寿命。
直接驱动系统的动态特性
直接驱动系统具有良好的动态特性,经常有高速、高加速度进给运动,这要求测量系统有良好的信号品质、 高的电气运动速度和优异的抗振、抗冲击性能。光电式单场扫描直线光栅尺和角度编码器的信号品质高,光栅刻线和读数头之间的无接触测量使其无磨损,且抗振、抗冲击性能良好,电气运动速度可达180 m/min。
综上所述,针对直接驱动系统的应用特点,光电式单场扫描直线光栅尺和角度编码器为其位置控制环和速度控制环提供了高精度、高分辨率、小细分误差的高品质信号,保证了驱动系统的高效、平稳运行,最终能够实现高速、高精、高表面品质和高稳定性的加工。
声明:本网站所收集的部分公开资料来源于互联网,转载的目的在于传递更多信息及用于网络分享,并不代表本站赞同其观点和对其真实性负责,也不构成任何其他建议。本站部分作品是由网友自主投稿和发布、编辑整理上传,对此类作品本站仅提供交流平台,不为其版权负责。如果您发现网站上所用视频、图片、文字如涉及作品版权问题,请第一时间告知,我们将根据您提供的证明材料确认版权并按国家标准支付稿酬或立即删除内容,以保证您的权益!联系电话:010-58612588 或 Email:editor@mmsonline.com.cn。
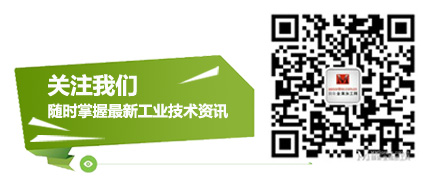
- 暂无反馈