工业CT在航空航天领域的应用:透视航空航天零配件的精密之眼
在航空航天这个充满挑战与高精度要求的领域,每一个零部件的质量和可靠性都关乎着整个项目的成败,甚至是宇航员的生命安全和飞行器的飞行使命。工业CT(计算机断层扫描)技术就像一把神奇的钥匙,为航空航天领域各类零配件的检测、设计优化和质量控制打开了新的大门。
一、航空航天领域零配件的特殊性与检测需求
航空航天零配件具有极高的复杂性、多样性和对可靠性的严苛要求。这些零配件包括发动机叶片、涡轮盘、航空电子设备中的电路板、各种精密连接件以及结构复杂的机身框架部件等。
发动机叶片工作在高温、高压、高转速的恶劣环境下,其内部结构的微小缺陷都可能导致叶片的断裂,进而引发严重的飞行事故。涡轮盘需要承受巨大的离心力,对于材料的均匀性和内部结构完整性要求极高。航空电子设备中的电路板,尽管体积相对较小,但上面集成了大量的电子元件和精细的线路,一个微小的短路或者开路都可能影响整个航空电子系统的正常运行。精密连接件的尺寸精度、内部应力状态以及连接的可靠性都是必须严格把控的关键因素。机身框架部件不仅要具备高强度和轻质的特性,其内部结构的完整性也直接影响飞机的整体结构强度。
传统的检测方法,如目视检测、超声波检测和射线照相检测等,在应对这些复杂零配件的检测时存在诸多局限性。目视检测只能发现表面缺陷;超声波检测对于形状复杂、内部结构不规则的零件检测效果有限;射线照相检测虽然能够检测内部缺陷,但成像为二维平面图像,对于复杂三维结构内部缺陷的定位和定量分析不够精确。
二、工业CT的工作原理及其在航空航天领域的优势
工业CT的工作原理基于X射线的衰减特性。当X射线穿透被检测的航空航天零配件时,由于零件内部不同的材料(如钛合金、铝合金、复合材料等)和结构对X射线的吸收程度不同,探测器会接收到不同强度的X射线信号。通过围绕零件进行多角度的扫描,并利用计算机算法对采集到的大量数据进行重建,就可以得到零件内部三维结构的详细图像。
在航空航天领域,工业CT技术具有显著的优势。首先,它能够在不破坏零配件的情况下进行检测,这对于成本高昂且制造工艺复杂的航空航天零部件至关重要。其次,工业CT提供的是三维图像,可以清晰地展示零配件内部的结构细节,准确地定位缺陷的位置,无论是内部的微小裂纹、气孔,还是材料不均匀性等问题都能被精确检测。再者,工业CT的检测精度极高,可以满足航空航天领域对零配件高精度检测的要求
三、工业CT在航空航天各类零配件中的具体应用
(一)发动机部件
发动机叶片检测
发动机叶片的形状复杂,内部冷却通道结构精细。工业CT可以检测叶片内部冷却通道是否存在堵塞、裂纹等缺陷,还能精确测量叶片的壁厚,确保其符合设计要求。例如,在涡轮风扇发动机的高压涡轮叶片检测中,工业CT能够发现隐藏在叶片内部靠近叶根处的微小裂纹,这些裂纹在传统检测方法下很难被发现。
涡轮盘检测
对于涡轮盘,工业CT可以检测其内部的疏松、夹杂物等缺陷。通过对涡轮盘进行全面的扫描,能够准确评估材料的均匀性,确保涡轮盘在高速旋转时的可靠性。
电路板检测
航空电子设备中的电路板集成度高。工业CT能够检测电路板内部的线路连接情况,如是否存在短路、开路或者线路间的微小间距不符合标准等问题。同时,它还可以检测电子元件与电路板之间的焊接质量,发现虚焊、焊点内部空洞等缺陷。
螺栓、螺母等连接件检测
在航空航天领域,螺栓和螺母等连接件的质量直接关系到整个结构的安全性。工业CT可以检测连接件内部是否存在裂纹、夹杂等缺陷,并且可以精确测量螺纹的尺寸精度,确保连接件的连接可靠性。
(二)航空电子设备
(三)精密连接件
(四)机身框架部件
框架结构检测
机身框架部件通常是大型复杂结构。工业CT可以对其内部的加强筋、预埋件等结构进行检测,检查是否存在结构缺陷或者装配问题。例如,检测框架内部的复合材料层间是否存在分层现象,这种分层可能会严重影响机身的整体强度。
四、工业CT技术对航空航天工程的推动作用
工业CT技术的应用为航空航天工程带来了多方面的积极影响。在设计阶段,通过对零配件的工业CT扫描,可以获取精确的内部结构数据,帮助工程师优化设计方案,提高零配件的性能和可靠性。在生产制造过程中,它可以用于质量控制,及时发现生产过程中的缺陷,降低废品率,提高生产效率。在产品的维护和检修阶段,工业CT能够对服役中的零配件进行检测,提前发现潜在的安全隐患,保障航空航天设备的安全运行。
工业CT技术在航空航天领域的应用就像一个无形的守护者,通过精确的检测和分析,确保航空航天零配件的质量和可靠性,为航空航天事业的发展提供了强有力的技术支撑。随着工业CT技术的不断发展,它将在航空航天领域发挥更加重要的作用,助力人类探索更加遥远的宇宙空间。
( rico 量标三维检测)
声明:本网站所收集的部分公开资料来源于互联网,转载的目的在于传递更多信息及用于网络分享,并不代表本站赞同其观点和对其真实性负责,也不构成任何其他建议。本站部分作品是由网友自主投稿和发布、编辑整理上传,对此类作品本站仅提供交流平台,不为其版权负责。如果您发现网站上所用视频、图片、文字如涉及作品版权问题,请第一时间告知,我们将根据您提供的证明材料确认版权并按国家标准支付稿酬或立即删除内容,以保证您的权益!联系电话:010-58612588 或 Email:editor@mmsonline.com.cn。
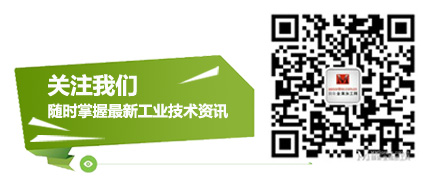
- 暂无反馈