英国零碳飞行电推进系统路线图分析
英国航空航天技术研究院( ATI )的零碳飞行( FlyZero )项目研究发现,液氢是实现飞机零排放的最可行能源,并提出支线、窄体和宽体3型氢动力客机方案,其中支线客机采用基于氢燃料电池的电动螺旋桨推进。为牵引电推进技术的发展,零碳飞行项目给出了相应的发展路线图。
零碳飞行项目路线图包括氢燃料电池和电推进系统,本文对后者进行了重点分析。零碳飞行项目的氢支线客机对标ATR72-600飞机,设计为75座、航程为1500km、航速为600km/h,其电推进系统使用质子交换膜(PEM)燃料电池为电源,电机驱动螺旋桨配备相关转换器和分配系统。分布式和模块化电推进带来的一个重要优势是可以更灵活地设计飞机。经初步评估,氢燃料电池的电推进系统比同功率的燃气涡轮发动机的质量大得多,因此系统的功率密度(功率与质量之比)最需优化。但相比同功率的氢燃料涡桨发动机,电推进系统的效率更高,大概在55%~60%,而氢燃料涡桨发动机大概44%。
路线图概述
为充分发挥分布式推进系统的优势,零碳飞行氢支线客机采用了6个电动螺旋桨和6个独立电气通道。由于是模块化的电推进系统,多个通道不会显著增大质量,相反提高了飞机的可用性。虽然该方案对单个螺旋桨的轴功率需求只有大概0.75MW,但为了解系统的扩展性,项目评估了0.5~4MW的功率范围。对于电力传输,需要1~3kV的高电压,若电压低于该水平,电能消耗和电缆质量将使电力传输变得不太可能。除提高系统的功率密度外,热管理系统(TMS)也是需要优化的关键领域。
电推进系统构成
整个电推进系统的质量构成中电力系统占38%,燃料电池堆占24%,热管理系统占21%,空气供应系统占17%。虽然电力系统占比最大,但后三者合称为电源及配套系统,质量占比高达62%,比电力系统高得多。电力系统的38%则由电机和变速器(14%)、直流-直流(DC-DC)转换器(12%)、逆变器(8%)和分配器(4%)组成。
技术指标
电推进系统技术指标主要是多个部件的功率密度,包括电机、逆变器、DC-DC转换器、燃料电池堆、热管理系统、空气供应系统及总的电推进系统,如表1所示。
表1 不同结构传热路径对比
按照当前的认知,技术的发展可分为3个阶段:到2026年,随着低温燃料电池、多功能/集成控制、先进永磁电机、增材和复材制造、高电压(1~3kV)传输等技术的应用,电推进系统功率密度(功重比)达到1.0~1.5kW/kg;到2030年,利用高温超导电机、低温冷却、先进压缩和热管理技术,电推进系统功率密度达到1.5~2.0kW/kg;到2050年,最终利用高温燃料电池和超导电力系统,电推进系统功率密度达到3.0~3.5kW/kg。
电推进系统技术发展阶段
关键技术
除燃料电池系统外,电推进系统主要涉及电机、电力电子和热管理等3类技术群,也是该路线图布局的重点。
电推进系统技术路线图
电机技术群
一般而言,对于确定拓扑结构的电机,可以通过略微牺牲效率的方式来提高功率密度。以500kW、2000r/min的电机为例,在能接受效率降低2%的情况下,功率密度可从4kW/kg提至7kW/kg。功率密度会随着转速的增加而升高,在低速域尤为明显;高转速(>6000r/min)时,若能采用更高的基频,那么通过提高转速来增大功率密度的优势能更加明显。对于高功率(>1MW)推进电机,利用变速器有可能实现更高的整体功率密度,特别是在采用高频元器件设计的情况下。
电机拓扑结构 电机拓扑结构主要包括以下几种技术。
一是与变速器结合的高速永磁电机。针对0.5~4MW的方案,高速表贴式永磁(SPM)电机与变速器相结合,能实现比电机直驱更大的功率密度;但要提高功率密度,还需开发关键技术。高速(约15000r/min)表贴式永磁电机的成熟度最高,且具有将电机功率密度提高到13kW/kg以上的潜力。此类电机所需的变速器技术已较成熟,但还要在大功率密度电机开发,以及其与轻质的变速器集成等方面做工作。
二是双气隙电机。径向双气隙电机也显示出在功率密度提高上的巨大潜力,由一个外转子和一个内转子组成,由海尔贝克(Halbach)阵列制成并安装在钛环上,多个定子齿夹在两转子之间。得益于双气隙布置,这种结构无需转子铁芯。与传统SPM拓扑结构相比,双气隙、双转子的电机功率密度预计能提高30%以上。
三是超导电机。超导电机在降低铜损和减少热管理负荷方面有优势,能显著提高功率密度。虽然超导电机效率也有所提高,但考虑到现有SPM电机的高效率,该优势很小。在较高功率(>4MW)时,SPM电机的功率密度和效率互相矛盾,使用超导电机可缓解该问题。高温超导(HTS)电机的功率密度已达到23kW/kg以上,展现出无需变速器直接驱动的巨大潜力。但高温超导电机只适用于飞机的特定场景,如为了最大限度地减轻低温冷却系统的质量,电机要靠近低温冷却剂;并且其优点仅在较高功率(>4MW)时才能显出。对于未来氢动力飞机,液氢燃料可以兼作低温冷却剂。
总的来说,采用高性能材料的径向表贴式永磁电机是当前最先进的技术,可以说是当前航空电推进的首选。该电机通常采用高能量密度钐钴(SmCo)磁体、低损耗钐铁(CoFe)叠片,以及用于降低高频交流损耗的线圈;再加上直接冷却和传统制造的铝/钛轻质无源元器件,使电机能够在1500~2500r/min范围内实现4~6kW/kg的功率密度。使用较低技术成熟度(TRL)或可制造性(MRL)的拓扑结构,如双转子径向表贴式永磁电机和永磁游标电机,能实现更高的功率密度,有可能将功率密度分别提高30%和50%。前者需解决机械设计和装配方面的问题;后者则要仔细评估电机功率密度的优势以及对电力电子(PE)转换器的影响,如伏安额定值、损耗等。对于高温超导动力系统,不仅要设计超导电机,还需进一步评估超导动力系统的整体性能。超导动力系统的测试和开发基础设施也普遍存在空白。
线圈绕组和电磁线 线圈绕组和电磁线主要包括以下几种技术。
一是纳米填料与300℃的聚醚醚酮(PEEK)绝缘线。电机工作温度通常由漆包电磁线的绝缘层决定。更高的工作温度允许更大的电流和更有效的热管理,从而提高功率密度。通过在聚酰亚胺基体中添加薄镍镀层和纳米填料,电磁线的额定温度已达到280℃。对于进一步提高漆包电磁线的绝缘温度,陶瓷涂层可实现高达500℃的极高耐温性。陶瓷材料已在其他高温环境中应用,但考虑其脆性特征,要在电磁线涂层中的使用仍存在挑战。目前禁止在密封装的漆包线中应用薄陶瓷绝缘层,但只要研发取得进展,该技术就有希望能显著提高电机的功率密度。
二是铜包铝线。电磁线发展的另一个方向是改进导线材料本身。铜包铝线融合了铜高导电性和铝低密度的优点,表面套上电绝缘层,实现了组合解决方案。此类电线近期已进入商业市场,但在电机上的应用仍受到限制。由于很高的成熟度和可用性,该方法似乎在加快提高功率密度方面有很大优势。相比传统铜或铝的导电性,碳纳米管(CNT)实现了导电性的跃升。由碳纳米管制成的漆包电磁线能在极低的密度下显著提高导电性,从而提高电机的整体功率密度。虽然该技术目前技术成熟度很低,但有巨大潜力。
三是先进的绕线排列。电机线圈的封装方法对性能也有很大影响。铜随机缠绕线圈的封装密度非常低(40%),导致绝缘材料的比例较高,从而降低了整体热导率。对此,预成型线圈和转置线圈包装这两种前景技术能实现更高的封装密度(>70%),从而改善电机的导热性和减轻整体质量。
总的来说,高频(>1kHz)、高封装密度(>80%)的预成型线圈与高温绝缘材料(300℃)相结合,具有将SPM电机功率密度的当前上限提高200%的巨大潜力。
磁性材料 磁性材料主要包括以下几种技术。
一是软磁材料(SMM)。软磁材料用于引导线圈绕组产生的磁通,会导致电机的铁损,减少该损耗对于发挥更高频运行的优势至关重要。汽车行业的高性能电机正在改用0.2mm厚的硅铁(SiFe),如NO20级的硅铁在1kHz的基频下能将磁芯损耗降低40%。提高硅含量可以进一步降低铁损。如果使用中要进一步减轻质量,可使用具有更高饱和磁通密度的钴铁(CoFe),但钴铁的性能提高伴随的是极大成本溢价,成本约是硅铁的10倍,当然对于航空应用来说或是可以接受的。
二是高温硬磁材料。电机使用的硬磁材料(HMM)也受到温度限制。常用硬磁材料的工作温度较低(<180℃),随着钐钴等高温材料的进步,可以实现较高的工作温度(500℃)。另一个有巨大潜力的是氮化铁(FeN)磁体。与钐钴硬磁材料相比,氮化铁磁体有可能将能量密度提高40%;另一个优势是氮化铁不含稀土,这引起了材料制造领域的重大关注。
总的来说,永磁电机目前最具高功率密度的潜力,比当前可用的其他方案更高效。磁通源和关键磁通路径、硬磁材料和软磁材料在电机的设计和性能中发挥着关键作用。汽车领域的硬磁材料以硼化钕铁(NdFeB)为基础,而钐钴永磁体尽管功率密度较低,但有更高热稳定性的优势。与硼化钕铁磁体相比,氮化铁和氮化钐铁(SmFeN)等有前景的新型合金可提供极高的能量密度,但尚未商用。钴铁是目前高功率密度软磁材料的首选,但诸如应力等一些工作磁特性当前还不是很清楚。同时,环境和社会可持续性及供应安全也尤为重要。其中,钴尤其需要特别关注,硬磁材料可能会受到供应链问题的影响。与2018年的水平相比,到2050年,钴产量需求将增加500%。
增材与复材制造 增材与复材制造主要包括以下几种。
一是无源元器件的增材和复材制造。电机几乎一半的质量来自无源元器件。这些元器件由传统技术制造,若改用增材制造和复合材料可显著减轻质量,有可能将无源元器件质量降低50%,电机功率密度提高30%。
二是磁体的增材制造。增材制造技术可以应用于制造特定形状和尺寸的磁体,有助于减轻实现相同磁通密度所需的磁体质量。该技术仍然很新颖,需要大量工作来开发具有所需磁性的增材制造方法。
总的来说,增材制造和复合材料技术已在航空领域的安全关键结构上得到积极应用,是经过验证的成熟技术;虽然在电机设计应用中还很有限,但被认为是最早在2024年就能带来收益的最成熟的技术。
电力电子技术群
通过集成设计能实现电力电子和高压直流电(HVDC)系统的最大性能,同时,电机、逆变器和DC-DC转换器的设计在提升整体性能,尤其是功率密度方面有很大潜力。中点钳位式转换器(NPC)或有源NPC通过提高波形质量和降低半导体元器件的整体感知电压显现出有前景的结果。兆瓦级动力系统需高传输电压,因此要探索减轻高压局部放电的技术。这些技术已存在汽车等其他行业,但若应用于航空,还有大量工作要做。
拓扑与集成 拓扑与集成主要包括以下几种技术。
一是功能集成。电机和能源(燃料电池和电池)都需控制系统来有效监控和操作。通过消除对专用控制器的需求,可大幅减轻系统质量。集成逆变器使其兼具电机控制器功能,能显著减轻整个系统质量。该技术已应用于电动汽车。同样,燃料电池管理系统也可集成到DC-DC转换器中。
二是部件集成。为进一步减轻质量,替换单独的DC-DC转换器和逆变器,逆变器设计成能应对直流电压的变化。该逆变器可嵌入电机内,成为现场可换单元(LRU)。这需要电源和电机的紧密结合,但确实能将系统的功率密度提高一个数量级。
三是多电平转换器。采用NPC或有源NPC拓扑创建多电平(而不是更常规的2电平)转换器来执行功率转换,主要两个优点:在相同开关频率下可获得更高质量的波形,从而减少对无源滤波元器件的需求,而后者一般都很重;半导体元器件不会感受到传输总线的总电压,而是低得多的电压,这就允许使用如氮化镓(GaN)的较低击穿电压元器件,消除了对高电压航空专用半导体元器件的需要,进而使用常规生产的较低电压元器件,既显著降低成本,又无须等待制造定制元器件。
半导体元器件 半导体元器件主要包括以下几种技术。
一是高电压绝缘栅双极晶体管(IGBT)。根据零碳飞行项目评估,电动飞机的商业化需多个兆瓦级推进系统,要采用1~3kV电压。为在短期内有效地达到该目标,需要开发航空用的高电压碳化硅(SiC)半导体元器件。
二是绝缘栅型金属氧化物场效应晶体管(MOSFET)电源模块。氮化镓和氧化镓(Ga2O3)元器件在高频运行中显示出巨大潜力。特别是冷却至75K低温时,GaN在效率和散热方面显著改善,而这可利用现有的机载低温冷却剂来实现。镓元器件可与超导电机结合使用,共用冷却系统和较低工作电压。另外,当使用多电平转换器拓扑时,也可用在提议的高压系统。现有的镓元器件的电压限制能通过使用多电平转换器拓扑来解决。
三是封装与制造。阻碍利用高频操作来优化功率密度的主要限制之一是高功率模块封装设计。这涉及到在每一层包装上集成不同材料的多种技术。芯片贴装、封装、基板材料和互连等技术,对以最小电压过冲保持高频开关操作和半导体芯片上均匀电流共享至关重要。直至目前的研发都主要集中在硅元器件上,但还需进一步改进碳化硅和氮化镓的封装。随着电动汽车的进步,其中一些研发将被汽车行业所覆盖,但还需进一步优化封装,以满足航空用所需的性能水平和使用环境。尽管碳化硅和氮化镓/氧化镓已完成制造和测试,但可靠的批量生产仍然落后,使得其实施成本极高,需要与设备制造商进一步协调才能制定可行的商业策略。
高压直流电系统 高压直流电系统主要包括以下几种技术。
一是故障管理。高压电力系统面临着减轻电弧和局部放电等故障的挑战。为处理这些故障,最关键的技术之一就是研发此类事件的检测和隔离。在研究检测技术方面已开展了大量工作,但由于半导体元器件的技术进步,特别是开关频率的增加,使检测变得更具挑战性。应用行波检测或阻抗测量等技术对于实现电推进系统的高压直流电系统至关重要。
二是电磁干扰管理。伴随着高频开关和高功率,电磁干扰(EMI)是需要克服的另一个障碍。目前的飞机配电标准是针对低得多的功率水平制定的,都偏于保守;在概念阶段还没有用于了解EMI的模拟工具。开发模拟工具来帮助了解高压系统的敏感性和辐射特征很有必要,有助于更新适用于电推进系统的高压电气系统标准。
热管理技术群
探索油冲击和油喷射等新型冷却技术能够提高系统性能,虽然这对于效率高于97%的设备来说可能显得微不足道,但由于需要重型元器件来传热散热,因此对功率密度有很大影响。另一个有潜力的领域是半导体元器件的低温冷却,氮化镓元器件在75K的低温下性能可提高5倍。随着动力系统向超导方向发展,电力电子设备需要充分发挥可用冷却系统的潜力。
冷却方案 冷却方案主要包括以下几种技术。
一是油冷却。冲击冷却是一种将流体直接喷射到物体表面的技术,可有效地在物体表面和流体间传递大量热。冲击冷却技术已普遍用于使用气体的工业场景中。使用液体油冲击冷却技术能极大地改善电机的传热性,允许更高的电流密度。油喷射是另一种有前景的冷却技术,显出比油冲击冷却更具提高热性能的潜力,其工作原理是将油滴喷射到待冷却的表面。这两种技术都可应用于电机和转换器(DC-DC转换器和逆变器)。
二是低温冷却。低温冷却对实现超导电机至关重要,需要与高温超导电机同步开发。超导电机已在实验室研发用于非航空领域,但在地面低温系统的小型化方面还待研究,如金属作为绝缘体和直接冷却等新技术。尽管当前技术的成熟度较低,但高温超导电机和相关的低温冷却系统预计能实现电推进系统功率密度的跃升。一旦该技术被开发用于超导电机,也可以用于转换器。镓元器件在低温下的性能也会提高。
结构与材料 结构与材料主要包括以下几种技术。
一是新型传热复合材料。电力电子液冷系统的开发主要涉及冷板、热管的新材料、结构及液冷技术。在近期的发展中,会出现新的导热复合材料,如铝碳化硅、金刚石/铜复合材料、电子材料和铜钨合金等,这些材料能提高导热性并有助于降低冷却系统的总体要求。
二是微通道、热管和均热板。在中长期的发展中,会出现更先进的材料和制造技术,使冷却系统部件结构更精细,改善散热性能;且通过设计冷板内的微通道及基板内的微翅片,将进一步改善散热性能。对于热管,可以用灯芯结构优化形状,并配之振动或脉动,增加液体整体流量而无需活动件。
材料基础
路线图中的技术实现,离不开以下几种材料研发的进展。
硅材料
当前的半导体元器件是硅基的,尽管硅材料是成熟技术,但也决定了重要性能的上限,阻碍了具有竞争力的高压(>1kV)电力系统和电驱动系统技术。具体而言,硅元器件的最高工作温度、开关速度、额定电流和电压,以及与硅基电驱动系统相关的能量损失导致电驱动系统相对庞大、笨重且低效,需要配备复杂的冷却系统。
硅的宽能隙和超宽能隙材料的替代品有许多优越的特性,有可能在效率、简单、体积和质量方面实现性能改进。
高性能半导体材料
碳化硅和氮化镓是高性能宽能隙半导体技术,在所有硅替代材料中具有最高的技术成熟度和可制造性,且已用于某些较低电压和较低功率场景。碳化硅材料和元器件技术在高压、高功率的航空电力系统方面有最具前景的潜力。氮化镓技术更适合功率相对较低的电力系统。超宽能隙技术,如氮化镓和金刚石,理论上有产生最大影响的潜力,但仍处于探索和概念论证的早期研究阶段。
需要对使用碳化硅和氮化镓元器件,以及超宽能隙技术进一步研究。
高温超导材料
高温超导材料的技术成熟度和可制造性过低是阻碍航空用超导动力系统的关键技术之一,但液氢的低温特性(20K)为超导提供了可能。
目前,要在有限的电压水平下为当下飞机匹配轻型、高效的电推进系统面临着技术挑战。对于任何高于10MW级的电推进系统,都存在一个关键问题:传统的电推进系统即使采用强制低温冷却,在不显著提高电压水平的情况下,也无法满足功率密度的要求。
稀土钡铜氧化物(ReBCO)和二硼化镁(MgB2)等材料在液氢低温下具有超导性,可用于超导动力系统零部件,包括超导电机、超导电网电缆和超导总线。电压低于1kV时,超导材料在以最小能量耗散承载大电流方面表现出巨大潜力。因此通过材料创新,可以在无须大幅提高电压的情况下开发20MW以上的超导推进动力系统。零电阻特性确保了动力系统的整体高效率,降低了燃料使用量和缩小了储罐尺寸。
采用低温和超导动力系统可以与核聚变研究一起进行,两个行业可能会共用一些制造能力和供应链,如超导磁体、高电流引线和接头、低温支撑部件以及超导电缆。
结束语
发展电动航空既是实现绿色航空的重要途径,也是技术响应市场需求的必然。电池的能量密度要超过1(kW·h)/kg才可能成为电动航空的主要电源,而这在未来10年或更长时间内不太可能达到,因此发展基于燃气涡轮发动机的混合电推进系统将是很长时期内的主要技术路线,大功率、高功率密度的推进系统是发展重点。短期来看,永磁电机最具航空电推进应用可能,但从长远发展来说,超导电机结合低温液氢燃料的混合电推进系统的技术优势明显,值得加强研究。磁性材料、半导体、超导材料等各类高性能材料是航空电推进的核心关键技术,其基础研究、开发与认证工作还需提前开展。
( 李明 航空动力 期刊)
声明:本网站所收集的部分公开资料来源于互联网,转载的目的在于传递更多信息及用于网络分享,并不代表本站赞同其观点和对其真实性负责,也不构成任何其他建议。本站部分作品是由网友自主投稿和发布、编辑整理上传,对此类作品本站仅提供交流平台,不为其版权负责。如果您发现网站上所用视频、图片、文字如涉及作品版权问题,请第一时间告知,我们将根据您提供的证明材料确认版权并按国家标准支付稿酬或立即删除内容,以保证您的权益!联系电话:010-58612588 或 Email:editor@mmsonline.com.cn。
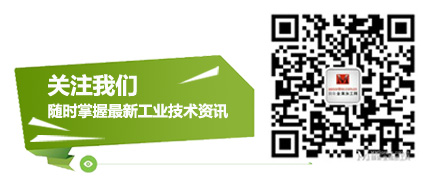
- 暂无反馈