航空发动机涡轮叶片接触式测温技术应用进展
导语
航空发动机涡轮叶片测温技术能够揭示涡轮叶片的温度分布情况,对其开展性能评估、失效分析和优化设计具有重要意义。涡轮进口温度的不断提升对应用于航空发动机涡轮叶片的测温技术提出了更高的要求。现有的航空发动机涡轮叶片接触式测温技术可采集叶片表面温度和近表面气流温度,本文主要介绍了三种应用于涡轮叶片的接触式测温技术,包括薄膜热电偶、测温晶体和示温漆,简要说明了三种测温技术的工作原理,归纳了国内外应用现状,总结了各自的优势与不足,并对其发展方向进行了展望。
航空发动机作为航空飞行器的“心脏”,集中体现了国家科技水平、工业设计制造水平和国防实力[1]。高马赫数、高推重比和高涡轮进口温度现已成为航空发动机重点发展方向[2-3]。推重比为10的第四代发动机一级涡轮进口温度已达1 973 K[2,4],未来推重比为15 的第五代发动机一级涡轮进口温度预计可达到2 000~2 250 K[2]。涡轮叶片作为航空发动机重要的热端动力输出部件,在高温、高压的环境下长时间工作易出现损伤失效,威胁到发动机的正常运行[1,4]。因此,测量工作状态下涡轮叶片表面或近表面温度,探究涡轮叶片的温度分布情况和耐高温性能,可以为涡轮叶片的结构设计和服役工况提供重要的试验数据和评价依据,保证发动机可靠性的同时降低了研发测试成本。
按照传感器与待测对象是否接触将航空发动机涡轮叶片测温技术分为接触式和非接触式两大类。接触式测温技术主要通过温度传感器与被测对象直接接触至热平衡,已知测量信号值与温度之间的映射关系反推得到测温结果,简单可靠且测量精度较高,但两种介质接触可能会影响待测对象表面温度场分布[5]。非接触式测温技术无需与待测对象接触,可应用于远距、带电、含腐蚀性成分的环境,但测量结果易受环境因素干扰,测温精度波动较大[6]。在实际航空发动机试验中,接触式测温技术应用广泛。
本文主要针对三种航空发动机涡轮叶片接触式测温技术进行介绍,包括薄膜热电偶、测温晶体和示温漆三种。对三种测温技术的工作原理进行了概述,归纳了其国内外发展应用现状,总结了各自的优势与不足,并基于现有研究水平展望了未来航空发动机测温技术的发展方向。
1 薄膜热电偶
1.1 测温原理
薄膜热电偶是基于塞贝克效应的一种无源传感器,如图1 所示。两种不同材质的导体作为电极连接组成闭合回路,一端称为热端也即测量端,另一端称为冷端也即参考端。使用时将两导体的一端进行焊接作为热端固定至待测点位,冷端分别接入测量仪表中。当冷端和热端存在温度差时,电极之间产生热电势。由于热电势的大小只与电极材料和冷热端温度差有关,因此可以根据热电势与温度之间的映射关系得到测温结果。薄膜热电偶相较传统热电偶最大区别在于电极呈薄膜状,可以减少对接触面温度场分布的干扰,在保证测温精度的同时也提高了响应速度。
图1 涡轮叶片薄膜热电偶安装示意图[7]
Fig.1 Schematic diagram of thin film thermocouple installed on turbine blade[7]
1.2 研究现状
航空发动机涡轮叶片表面为复杂曲面,通常采用高温胶或焊接方式进行热电偶的安装固定,但引入高温胶的同时也增加了热阻,影响测温精度。采用焊接方式固定热电偶仅适用于部分金属材料,应用范围受限。除此之外还有埋偶法,应用此方法需要在待测试件上开设预埋槽,破坏了机件结构完整性。薄膜热电偶可以原位集成于涡轮叶片表面,对结构的破坏性相对较小,同时也降低了热电偶安装固定对试件温度分布的影响,有效提升了测温结果的可靠性,且能够应用于带有陶瓷涂层的叶片表面。得益于镀膜技术的发展,薄膜热电偶成功应用于航空发动机涡轮叶片表面进行温度测量。
20 世 纪50 年 代 初 期,D.Bendersky[8]使 用 钢管、表面绝缘处理过的镍丝经蒸镀后制成厚度为1 μm 的薄膜电极。真空蒸发镀膜是指在真空状态下对镀膜材料进行加热蒸发,使之以分子或原子形态进入空间后经沉积形成薄膜,操作简便但生成的薄膜附着力较小,力学强度不足。使用溅射工艺制备薄膜,显著提高了薄膜沉积速度、沉积效率和质量。美国GE 公司使用溅射镀膜方法制备了Au-Pd 薄膜热电偶[9],有效地将响应时间缩短为140 μs。鉴于薄膜热电偶测温性能良好、响应速度快,R.Dila 等[10]提出在发动机热端部件上使用溅射工艺制备薄膜热电偶。为验证薄膜热电偶高温下的工作性能,H.P.Grant 等[11]在涡轮叶片上集成了2 μm 的Pt/Pt10Rh 薄膜热电偶,完成了1 250 K、1 个标准大气压下长达60 h 的71 次热循环试验,薄膜电极从试件表面脱落失效累计平均时间为47 h。英国罗罗公司研制了测量不确定度为±2%的Pt-Rh/Pt 薄膜热电偶[12],并进行了高达1 200 ℃的导向叶片温度分布测试。20 世纪末,美国NASA 的路易斯研究中心采用平行间隙焊接和溅射工艺制备出可以应用于高温合金、陶瓷和陶瓷复合材料以及金属间化合物的Pt/Pt13Rh 薄膜热电偶,如图2(a)所示,在930 ℃、16 MPa 试验环境下对涡轮叶片进行了热震试验。经试验证明,该型薄膜热电偶可以在低于1 000 ℃的环境下监测涡轮叶片温度[13-14]。此外,还将其应用于陶瓷材料,完成了1 000~1 500 ℃、150 h 稳态高温试验,进一步验证了该薄膜热电偶的工作稳定性[15]。
国内薄膜热电偶的研制起步较晚。1992 年,沈阳航空发动机研究所采用真空溅射镀膜的方式[7],在涡轮叶片表面集成了可以在最高温度1 000 ℃下正常工作3 h、经历5 次以上冷热循环的PtRh10/Pt 热电偶,测温误差在±3%以内,实现了航空发动机涡轮叶片表面薄膜热电偶的原位集成;王亦然[16]使用磁控溅射方法在预处理后的涡轮叶片表面制备PtRh/Pt S 型热电偶,经静态标定试验得到该型热电偶可以在300~1 000 ℃的温度范围内实现涡轮叶片表面温度的测量。由于磁控溅射技术仅适用于导体材料,为了实现在陶瓷基材料上制备薄膜,刘海军等[17]使用射频磁控溅射和掩模图形化技术在陶瓷基片上沉积Pt/ITO 薄膜热电偶,经退火5 h 后最大测量误差仅为16.03 ℃,可以在400~1 100 ℃热循环试验中稳定工作约20 h。射频溅射技术可以在靶材上产生自偏压效应,击穿电压和放电电压显著降低,实现了在非导体材料上进行薄膜沉积。为了提升薄膜致密程度,杨柯[18]使用射频溅射在陶瓷基底上制备In2O3/ITO 薄膜热电偶后也进行了退火处理。
随着微机电系统(Micro-Electric-Mechanical System,简称MEMS)的发展,实现了在涡轮叶片表面利用光刻技术进行微米至毫米尺寸微图案的印制,使得监控涡轮叶片榫槽边缘及叶片尖端的温 度 成 为 可 能。段 力 等[19]、Duan F L 等[20]使 用MEMS 技术在涡轮导向叶片表面制作微米量级的薄膜热电偶,如图2(b)所示,有效提高了定位精度,攻克了涡轮叶片大曲率位置微小区域薄膜热电偶原位集成及温度测量的问题,通过高温振动冲击试验验证了该薄膜热电偶具有稳定的机械性能;Xie Z 等[21]提出了一种更为简便的薄膜制备方法,如图2(c)所示;Weng H 等[22]使用MEMS 技术在涂敷有热障涂层的涡轮叶片表面安装了薄膜热电偶,并通过振动冲击、热震等试验证明了改进后的热障涂层以及薄膜热电偶均具有稳定的工作性能;张久斌[23]结合MEMS 工艺使用干法刻蚀和湿法腐蚀制备Pt/Pd 薄膜热电偶和Pt/PtRh13 薄膜热电偶,经测试Pt/PtRh13 薄膜热电偶可以在1 300 ℃下稳定工作14 h;Ji Z 等[24]使用MEMS 和磁控溅射技术,在涡轮叶片表面原位集成了1 μm PtRh/Pt 薄膜热电偶阵列,如图3 所示,该阵列响应时间为10 μs,通过多次高温试验验证该阵列具有稳定的测温性能,并使用MEMS 技术在陶瓷基底上制备了可以测量1 500 ℃的薄膜热电偶,测量误差小于±0.2%,响应时间为10 μs[25],为下一代智能发动机的高精度温度测量提供了技术支持。
图2 不同制造工艺制备的薄膜热电偶
Fig.2 Installing thin film thermocouples on the turbine blades by different methods
图3 涡轮叶片表面薄膜热电偶阵列[24]
Fig.3 Thin film thermocouple array on the surface of turbine blade[24]
除了使用广泛的溅射技术以外,也有部分研究者采用了更为简化的镀膜工艺进行薄膜热电偶的制备。Xie Z 等[21,26]针对航空发动机内部结构复杂部件提出了一种手工绘制Pt/PtRh 薄膜热电偶的方式,简化镀膜工序,如图2(c)所示,该热电偶可以在1 000 ℃的温度范围内稳定工作,测温误差在±1%以内。
为了进一步提升薄膜热电偶在高温下工作的稳定性,徐毅等[27]为涡轮叶片原位集成的薄膜热电偶增设保护层;陈寅之[28]在镍基高温合金上沉积 了10 μm NiCrAlY 薄 膜 和50 nm 铝 薄 膜,并 对NiCrAlY 薄膜进行析铝处理,有效提升了薄膜热电偶绝缘层的附着性能。为了缓解电极材料在高温下易氧化、热电性能衰减的问题,可以使用铟锡氧化物(ITO)代替PtRh 薄膜制备ITO/Pt 薄膜热电偶,添加氮化硅/ITO/氮化硅“三明治”结构阻止氧元素扩散[9]。为了测量航空发动机中由陶瓷基复合材料(Ceramic Matrix Composite,简称CMC)制造的热端部件表面温度,K.Rivera 等[29]设计了一种ITO:SiC CMC 薄膜热电偶,并添加铟锡氧氮化物(ITNO)保护涂层,有效提升了其工作稳定性。考虑到引线暴露在高温下可能导致信号传输不稳定,在燃气冲击情况下易发生熔断损坏,邓进军等[30-31]在涡轮叶片上使用通孔引线技术,结构如图4 所示,为了保证引线和涡轮叶片镍基合金基底相互绝缘,使用耐高温的粘结材料将陶瓷管固定于孔内,抗震、防腐性能极大提升。
图4 涡轮叶片通孔结构图[30-31]
Fig.4 Structural diagram of the turbine blade through-hole[30-31]
从薄膜热电偶发展历程来看,制备方法从原有的真空蒸发镀膜发展至磁控溅射、射频磁控溅射以及结合MEMS 微制造技术,逐步提升了薄膜热电偶的质量和性能,同时也扩大了薄膜热电偶的应用范围。薄膜热电偶电极材料抗氧化性能的提升、引线的安装和保护以及薄膜层级结构的优化等,也进一步保证了薄膜热电偶的高测量精度和工作稳定性,促使其成为航空发动机涡轮叶片温度实时监测的重要方式之一。但是,薄膜热电偶仍存在薄膜电极制备工艺复杂和造价高的问题,如何简化薄膜热电偶制备方法也是后续研究重点之一。
2 测温晶体
2.1 测温原理
测温晶体可以获取一定试验时间内测量点位所经历的最高温度。其工作原理是基于晶体材料的“温度记忆效应”[32-35],即经过高能粒子辐照后晶体内部会产生辐照缺陷,缺陷程度由晶体的物性参数表示,例如电阻率、热导率等。在经历高温退火后缺陷逐渐恢复,根据退火温度与晶体物性参数之间相互对应的稳定关系便可获取测量结果[36-38]。为了方便使用,一般选择易于测量的晶体参数进行传感器标定。对经过试验后的测温晶体进行测试获得晶体参数,对照标定曲线反推最高温度值。在应用过程中,需要保证标定用测温晶体和试验用测温晶体的一致性,这也是制备测温晶体应该关注的重要问题之一。
2.2 研究现状
晶体温度传感器尺寸小且无需引线易于安装,对待测对象表面或近表面温度场分布的影响小,多用于精确测量叶片各点位及近表面气流在整个温度历程中的最高温度,适用于高速旋转等动态测试场景[39]。国外大约于20 世纪70 年代开展晶体测温技术的研究,俄罗斯、美国、乌克兰等国家发展较早且体系成熟[38-41]。国内相关研究大约在20 世纪90 年代末起步,目前大多处于理论研究和实验室验证阶段[39]。21 世纪以来,中子物理、晶体增长技术和X 射线辐照技术的发展和新型材料的开发,如表1 所示,有效地促进了晶体传感器在测温范围、测温精度、可靠性等多方面性能的提升,现已成为航空发动机涡轮叶片测温方式之一。
表1 测温晶体性能参数
Table 1 Parameters of crystal temperature sensor
关于晶体测温技术的研究,俄罗斯的库尔恰托夫I.V.原子能研究所研制出具有较大测温范围和抗腐蚀性的立方体SiC 单晶(β 相)测温晶体[48-50];美 国LGTech-Link 公 司 研 制 的 测 温 晶 体现已应用于航空燃气涡轮发动机、燃气轮机、火箭发动机、涡轮增压器和往复式发动机等[39]。在实际应用中,测温晶体可以测量叶片表面及其近表面的气流温度,涡轮叶片测温晶体安装方式如图5所示,对涡轮叶片损伤失效分析和结构优化设计起到了重要作用。A.A.Volinsky 等[43]将3C-SiC测温晶体安装于涡轮叶片、轮盘以及喷管中进行部件表面及气流温度测试;(暂不可见)voe 等[44]将测温晶体胶粘在叶片表面,或插入叶片气膜孔等孔洞处固定的陶瓷管中进行温度测量。AI-25TL 发动机涡轮导叶因氧化和积碳严重发生故障,通过晶体测温结果验证了改进后的导向叶片结构有效提高了系统冷却效果[32],如图6 所示。I.V.Bachuchin等[42]提出了一种基于金刚石和SiC 材料的测温晶体,在西门子公司额定功率47 MW 的航空发动机零部件结构设计合理性验证试验中,使用2 000 多个测温晶体、传统热电偶和示温漆对叶片等热端部件进行温度测量,该型测温晶体经过200~1 400 ℃温度标定后测温误差小于±10 ℃[51];西门子石油燃气公司为了验证涡轮热端部件耐热性能,在涡轮部分安装1 710 个测温晶体,其中176 个用于测量静叶和动叶进气温度,6 个用于测量动叶冷气道温度,如图7 所示,详细描述了叶片表面温度场分布情况和叶片近表面气流温度,为仿真模型计算提供了温度数据[52];霍尼韦尔公司某型发动机在试验中发生了叶冠氧化断裂、TBC 涂层剥落和基底金属损伤,之后在台架试验中使用测温晶体进行故障原因分析,获得的温度数据进一步证实了计算流体力学分析的可靠性,并验证排故改进措施的可行性[53-55]。
图5 涡轮叶片测温晶体安装方式[42,44-45]
Fig.5 Installation of crystal temperature sensor on turbine blade[42,44-45]
图6 涡轮叶片及其测温结果[32]
Fig.6 Turbine blade and temperature measurement results[32]
图7 涡轮叶片测温晶体分布图[52]
Fig.7 Distribution of crystal temperature sensor on turbine blade[52]
国内测温晶体研究起步较晚,现阶段主要针对测温晶体材料和制备方法进行研究。中国航发四川燃气涡轮研究院研制了0.2 mm×0.3 mm×0.3 mm 微型SiC 测 温 晶 体[45],测 温 范 围 为500~1 400 ℃,测量误差小于±1.5%。为验证测温晶体的性能,在高温、高压、高转速和热冲击的条件下对安装测温晶体的涡轮叶片进行试验,结果显示测温晶体未有损耗。微型SiC 测温晶体现已通过了工艺可靠性试验、热冲击试验和抗离心力试验,并应用于发动机型号研发中。为了进一步提升晶体测温能力,张志学等[47]成功研制了可以测量最高温度为1 600 ℃的6H-SiC 测温晶体,测温晶体误差小于±1%;Ruan Y F 等[46]为了测量发动机工作状态下运动部件的表面温度,研制了一种以6HSiC 为材料、低中子辐照加工的新型测温晶体,测温范围为700~1 300 ℃,测温相对误差小于5%。除了不断发掘新型测温晶体材料外,李杨等[54]为解决国外“最高温等效时间”标定方法中参数难以获取的问题,创新性地将“最高温恒温时间”作为输入时间参数来完成测温晶体的标定和温度判读。
测温晶体可以实现航空发动机热端部件表面各点位及近表面气流的最高温度测量,尤其是用于测量气膜孔、榫头等难以布置测温传感器的位置。但测温晶体制备过程要求严苛,试验后还需要对测温晶体进行测试分析才能够得到测量的温度值。目前国外测温晶体技术发展成熟,且已投入航空发动机实际工程应用中。与国外相比,国内测温晶体技术发展较为迟缓,主要集中于探索性试验研究,部分研究技术成果已通过试验验证阶段并应用于航空发动机研发测试中。未来需要针对测温晶体的制备及使用规范等多个方面开展进一步的研究。
3 示温漆
3.1 测温原理
示温漆主要由变色颜料、基料(成膜物质)、填料(助剂)和溶剂组成,当涂敷有示温漆的部件发生温度变化时,变色颜料会产生一系列的物理和化学反应,分子结构或组成成分变化会引起颜色变化,显式地表现为试件表面的颜色变化[56-57]。根据发生色变之后能否恢复分为可逆示温漆和不可逆示温漆,不可逆示温漆多用于测量表面最高温度。根据变化产生颜色的数量分为单变色和多变色不可逆示温漆两种[58]。单变色不可逆示温漆多基于变色颜料的升华、晶格转换、热分解反应、固相反应、氧化反应等进行显色[59];多变色不可逆示温漆变色机理较为复杂,主要包括物质热色连续变化和物质之间的相互作用,适用于获取试件大面积温度分布,可以用于发动机相关温度测试中[56-57]。示温漆漆质细腻,有明显变色且变色稳定,无需固定安装,可以耐受气流冲刷和结构振动,对被测结构和工作状态影响小,能够用于高速旋转、待测面积大、结构复杂的场景中。近年来,示温漆广泛应用于发动机涡轮叶片和涡轮盘等结构的温度测量,判读精度现已达到±5 ℃[60]。
3.2 研究现状
单变色不可逆示温漆发展较早且现国内外研究较为成熟,多变色不可逆示温漆也在持续提升测温性能和显色能力,现已成功应用于航空发动机相关温度测试中。英国、俄罗斯、德国、法国、美国、日本及中国的示温漆相关研制工作领先于其他国家。欧洲在高温多变色示温漆的研究和应用处于世界领先地位,日本侧重研究低温和可逆示温漆及其应用。国外对可逆示温漆实行技术封锁,国内相关研究发展较晚,鲜有相关公开资料。
1938 年,德国的I.G 法贝宁达斯公司开始研制示温涂料——热色线[61]。为了测量航空发动机高转速热端部件表面的温度分布,20 世纪50-70年代,国外对高温不可逆测温涂料进行了大量研究。美国航空航天局NASA 为了获取航空发动机大面积部件的温度分布,将示温漆应用于风洞试验中[62];英国罗罗公司使用示温漆来确定涡轮叶片等热端部件的温度分布情况[61];英国Thermindex 公司、德国的Faber Castel 公司生产的单变色示温漆无法获得温度分布线,故采取对同一试验件使用不同的示温涂料,测试后对测温结果进行综合评定[61]。20 世纪70 年代后,国外主要开展低温和可逆示温漆的研究[63-64]。除此之外,研究人员还针对示温漆及其在运动部件上的粘附力问题进行了大量研究[61]。
国内从20 世纪60 年代开始进行示温漆研究。研究初期,重点解决国产单变色不可逆示温漆变色不清、等温线辨识难的问题。自行设计了不可逆示温漆配方,建立了基于等温线辨识的全量程标定方法,研制出了示温误差为±5 ℃的单变色不可逆示温漆,以及示温误差为±10 ℃的多变色不可逆示温漆,测温范围覆盖100~1 100 ℃[65]。目前国内也开展了灵敏度高、精度高、响应快的熔融型单变色不可逆示温漆的相关研究,现有成果的一般测温范围为40~260 ℃[57]。北方涂料工业研究设计院对示温漆的研究处于国内领先水平[57,65],现其研制的多变色不可逆示温漆测温范围可以达到150~1350 ℃,但单品种测温跨度只有350~400 ℃,变色点数一般只有4~5 个;此外,还研制了SW-S 单变色不可逆示温漆系列和SM-M 多变色不可逆示温涂料系列,可以用于航空发动机热端部件的温度测量[57,65]。当使用变色点数少、测温范围大的示温漆时,通过示温漆颜色变化判读温度值时会产生较大的误差。因此如何缩小示温漆颜色变化的间隔、增加变色点数来提升测温精度也是研究的重点之一[57]。
国内外部分型号示温漆测温性能参数对比如图8 所示,国外不可逆示温漆性能参数如表2 所示,可以看出:国外不可逆示温漆普遍具有更大的测温范围、更短的响应时间、更多的变色点数和更小的示温误差。
图8 国内外部分牌号示温漆性能参数[57,61]
Fig.8 Performance of some temperature sensitive paint at home and abroad[57,61]
表2 国外不可逆示温漆参数[57,66]
Table 2 Parameters of irreversible temperature sensitive paint[57,66]
将示温漆涂敷于涡轮叶片表面获得区域温度分布,可以验证相关理论研究及结构设计方案的合理性。P.S.Mandavkar 等[67]通过对叶片热轮廓图像捕捉,研究叶片气膜孔冷却效果;熊庆荣等[68]使用自主研发的示温漆获取高压涡轮导向叶片表面温度分布,判读精度达到±10 ℃,如图9 所示。
图9 高压涡轮导叶各区域试验前后颜色分布[68]
Fig.9 Color distribution of high-pressure turbine guide vane before and after tests[68]
李杨等[69]使用多种单变色和多变色示温漆完成了某大型运输机辅助动力装置涡轮叶片的温度测量,包括一、二、三级涡轮叶片及叶盆和叶背的表面温度,验证了涡轮叶片理论温度分布。在高温燃气冲刷下,航空发动机涡轮叶片易出现裂纹、变形、烧蚀等损伤,严重威胁航空飞行器的安全及可靠性。示温漆测温技术有助于进行航空发动机热端部件的损伤失效分析。国外研制的第一代多变色示温涂料TP5、TP6 对早期的航空发动机高压涡轮叶片冷却方案的设计验证起到了重要作用,TP 系列示温漆发展至今大多适用于航空发动机涡轮叶片的温度测量,如表3 所示。
表3 国外部分示温漆应用环境[61]
Table 3 Application environment of some foreign temperature sensitive paints[61]
P.L.Rupesh 等[70]使用量程为350~1 270 ℃的MC350-8 示温漆进行叶片表面温度分析,经试验研究发现高温下材料内部会产生蠕变,长期处于恶劣工况下易发生断裂。
示温漆的研制对测量航空发动机热端部件区域温度分布具有重要意义,能够辅助进行故障分析。目前国内外均已有成熟的示温漆产品系列,经对比不难发现,国外示温漆在测温范围、测温精度、响应速度等方面优于国产示温漆。在可逆示温漆和熔融型示温漆研究方面,国内仍处于起步阶段,技术方面受到日本和欧美国家及地区的封锁,因此需要加大设备投入,进行自主设计研究,争取早日突破关键技术的壁垒。
4 展望
随着国内外航空发动机相关测温技术的进步,测温范围和测温精度都得到了显著提升。下一代航空发动机性能的提升对测温技术的要求也更加严苛,测温技术仍需进一步升级。
现有薄膜热电偶可以高精度实时测量涡轮叶片表面微小面积温度,国内外薄膜热电偶在工作寿命方面存在较大差异,需要对薄膜制备严格把关,改进现有镀膜技术提高薄膜质量和附着强度,继而保证薄膜热电偶工作的稳定性。目前薄膜制备工序复杂且制造成本高是限制薄膜热电偶被广泛应用于工程实践的重要因素。因此在保证薄膜热电偶质量的前提下可以考虑简化现有的镀膜工艺从而降低造价,例如结合3D 打印等智能制造技术进行薄膜制备,或者使用智能机器人进行薄膜绘制等。除此之外,研究新型抗氧化、耐高温、灵敏度高的电极材料和设计薄膜层间结构,解决材料间热膨胀系数差异带来的薄膜失效脱落也是薄膜热电偶的研究重点。
相较热电偶来说,测温晶体更适合测量涡轮叶片气膜孔处、近表面气流的温度。由于其具有较高的测温上限和稳定性,航空发动机涡轮进口温度的提升也增加了对测温晶体的需求。未来首先应针对如何提升测温晶体的测温性能加以研究,包括测温晶体材料的研发、测温晶体制备方法、标定技术等。此外,国内应完善测温晶体行业的制度规范,制定统一标准,推动测温晶体批量化生产制造,加速测温晶体广泛应用于航空发动机相关温度测试中。
示温漆在获取航空发动机涡轮叶片表面温度分布时无需高密度安装温度传感器,涂敷操作方便,结果直观,具有其独特的测温优势。目前国内各型示温漆测温能力与国外相比在测温范围、变色点数方面相差较大,尤其是可逆示温漆研究结果较少。未来应优化现有的不可逆示温漆,在原有配方基础上进行改良以提升测温范围、变色点数和颜色区分度。继续发展具有高灵敏度、高精度和响应快的熔融型单变色不可逆示温漆。研究可逆示温漆应从材料变色机理方面入手,夯实理论基础,并开展相关实验进行方案验证,致力于打破目前技术封锁的局面。同时,温度判读技术的选择在很大程度上影响示温漆测温结果的准确度,随着计算机视觉技术的发展,未来可以通过计算机图像处理技术进行图像颜色的校正统一和测温结果的判读,减少环境光照和人为主观因素对结果的影响。
5 结束语
航空发动机涡轮叶片测温技术对涡轮叶片结构设计方案的验证和性能评定具有重要参考价值和指导意义。测温技术在使用过程中应具有高温工作稳定性和优异的测量精度,并尽量减小对待测对象温度场分布的干扰。本文总结了薄膜热电偶、测温晶体和示温漆这三种接触式测温技术的研究情况和应用现状,并基于其现有不足展望了未来的发展方向。由于三种测温技术各自具有其不可替代的测温优势,仍有待进一步研究以实现性能上的提升。未来,随着新型敏感材料的研发和制造技术的发展,上述接触式测温技术将迎来更为广阔的应用前景。
(《航空工程进展》作者:胡娜 赵伟 晋小超 范学领)
声明:本网站所收集的部分公开资料来源于互联网,转载的目的在于传递更多信息及用于网络分享,并不代表本站赞同其观点和对其真实性负责,也不构成任何其他建议。本站部分作品是由网友自主投稿和发布、编辑整理上传,对此类作品本站仅提供交流平台,不为其版权负责。如果您发现网站上所用视频、图片、文字如涉及作品版权问题,请第一时间告知,我们将根据您提供的证明材料确认版权并按国家标准支付稿酬或立即删除内容,以保证您的权益!联系电话:010-58612588 或 Email:editor@mmsonline.com.cn。
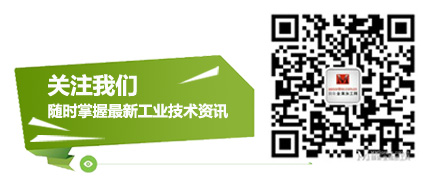
- 暂无反馈