民用航空发动机涡轮叶片材料研究
现代民用航空发动机总体设计已经定型,要想提升发动机的性能、提高推重比,必须在发动机制造材料上进行升级换代。如今,传统高温合金已经很难追上航空发动机的发展速度,研发新型高温材料取代高温合金是最有效的途径,陶瓷基复合材料是其中的选择之一。本文介绍了陶瓷基复合材料的发展以及应用现状,总结了目前航空发动机使用的高温合金制作工艺以及使用材料的发展历程,并指出了高温合金涡轮叶片的缺点,提出了相应的解决方案。随后介绍了陶瓷基复合材料的概念、制备方法以及性能,分析了目前陶瓷基复合材料存在的缺点和改进方法,对陶瓷基复合材料替代高温合金用于航空发动机涡轮叶片进行了分析。
1 前言
喷气式客机面世已有70多年时间,随着航空发动机综合性能的不断提升,现代的民航客机最大能够实现17000km的航程。目前,民用客机采用涡轮风扇发动机,对发动机的性能影响巨大,目前的涡轮叶片高温合金承温能力提升缓慢,难以匹配客机的发展。对于热端部件而言,CMC陶瓷基复合材料轻质、高强度、耐高温、长寿命的优点,是替代传统高温合金理想的材料。目前,国外已经成功将陶瓷基复合材料在航空发动机热端部件上进行试验,在发动机试验中取得了优异的成绩。随着制造工艺的优化,专家学者预测未来很有可能应用于制造涡轮叶片。
2 现代民用航空发动机涡轮叶片材料发展
2.1 高温合金制造工艺的发展
高温合金的发展经历了2次重大的变革。第一次革命是1950年真空熔炉的出现,美国的Darmava发明了真空熔炼炉,真空熔模铸造涡轮叶片在高温环境中具有更优秀的性能,涡轮组件的使用温度得以提高,即使在800℃的高温下也能持续工作,铸造叶片从此取代了锻造叶片。高温合金第二次重大变革标志是单晶合金的出现。在20世纪80年代,科学家在定向凝固技术的基础上,对工艺进一步改进,单晶合金研发以及应用从此得到了快速发展。对航空发动机的性能提升做出巨大贡献。
2.2 现代航空发动机涡轮叶片材料分析
由于镍基合金制造工艺比较成熟,以及性能优异,现代航空发动机涡轮叶片一般采用镍基高温合金制作,镍基合金中镍元素含量超过60%,除此以外还添加了其他难熔金属、稀有金属,如钴、铬、钨、钼、铼、钌、铝、钽、钛等。这些元素的添加可以改善镍合金的性能,提高强度和韧性,最重要的是提升了高温抗氧化性、抗腐蚀能力,使得镍基合金叶片在950~1100℃下长时间工作。
目前,数量最多、最具代表性是波音737系列客机搭载的CFM56-7B发动机以及空客A320系列客机搭载的CFM56-5B和V2500-A5发动机。这3款发动机都在上世纪80年代设计制造,使用了当时最先进的第二代镍基合金。其中CFM56-7B和CFM56-5B 2款发动机的高压涡轮叶片使用了GE生产的第二代单晶镍基合金Rene N5制造。Rene N5单晶合金与同代的单晶合金PWA1484、CMSX-4相比,Rene N5最大的不同是添加了硼、碳、钇元素,含有硼、碳元素的叶片在高温条件下寿命得到提高,稀土元素钇可以显著提高叶片在高温工况下的热疲劳性能。
2.3 目前航空涡轮发动机存在的问题与改进方法
2.3.1 存在的问题
目前,发动机燃气温度已经远远高于涡轮叶片材料自身的承温能力,工程师通过各种方法降低涡轮叶片工作时所承受的温度以提高其使用寿命,第一是对叶片进行冷却,第二是减少高温燃气对叶片的影响。于是,工程师设计出了表面带有气孔的空心涡轮叶片,并在叶片表面添加TBC热障涂层。
涡轮叶片的冷却气源是从高压压气机引入的气体,引气会引起压气机压力损失,降低增压比,影响发动机的性能。航空发动机高压涡轮运转速度高达12000转/min,而热障涂层的使用会增加高压涡轮整体质量,重量的增加会增大离心应力,增加叶片的负载,降低高压转子的转速,影响发动机的性能,同时,因为单晶高温合金中加入了铼、钴、钌等稀有金属,占用了很大比例的制造成本,使航空发动机制造成本过高。
2.3.2 改进方法
第一,提高叶片的高温性能。高温性能更好的材料可以减少发动机冷却引气量,提高燃气温度,实现提高发动机性能、改善发动机热效率和增加发动机使用寿命的目标。第二,发展新型高温材料。复合材料在航空航天产业上被逐步应用,将复合材料应用在发动机热端部件上成为世界各国的努力方向。专家学者经过多年的研究发现,陶瓷基复合材料、碳复合材料的高温性能优秀,是替代高温合金的理想材料。
3 陶瓷基复合材料叶片可行性分析
3.1 陶瓷基复合材料的概念
陶瓷基复合材料CMC(Ceramic Matrix Composite)属于无机非金属基复合材料,基体是陶瓷。陶瓷材料中SiC、SiN、AlO2等应用广泛,目前,对它们的研究较为全面。研究发现,若在引入增韧纤维后,单相陶瓷的脆性、对裂纹敏感等缺点在陶瓷基复合材料上得到明显改善,经实验室测试发现,在不对试验件进行冷却的情况下,陶瓷基复合材料可在1250℃的高温下持续工作,材料性能衰减缓慢。
3.2 陶瓷基复合材料的分类
根据增韧方式的不同,陶瓷基复合材料分为颗粒增强陶瓷基复合材料、晶须增强陶瓷基复合材料、层状增强陶瓷基复合材料和连续纤维增韧陶瓷基复合材料。目前,世界各国的航空发动机设计和制造企业都把研发重点放在抗氧化的纤维增强陶瓷基复合材料上。为了提高材料强度和韧性,研究人员对陶瓷基体发生断裂的行为深入研究,结果发现如果采用碳纤维或碳化硅纤维对陶瓷基体进行增强,引入的纤维束会在材料断裂时产生纤维断裂和纤维拔出的机制,这种机制能抑制断裂的现象,使得材料强度和韧性得到提高。
3.3 纤维增强SiC陶瓷基复合材料的不足与改进方法
3.3.1 纤维增强SiC陶瓷基复合材料的缺点
与实验室测试中模拟的环境不同,航空发动机真实服役工作过程中不仅仅吸入空气,受不同天气条件影响,发动机会吸入水蒸气和大量沙尘。高温燃气和水蒸气以及固体颗粒物形成的环境会加速SiCf/SiC复合材料的氧化以及腐蚀,进而造成材料的失效。这是因为热解碳PyC、六方BN等提高复合材料力学性能的界面相在类似环境中有加速氧化的倾向,而且陶瓷基复合材料制造时产生的孔隙和裂纹表面活性较大,同样容易被氧化和腐蚀。由此可见,当前制备工艺并未能生产出致密化更高的SiCf/SiC复合材料,目前SiCf/SiC CMC的抗蠕变能力和热稳定性等还并不能满足航空发动机的工作要求,必须提高SiCf/SiC CMC长时间抗高温氧化能力,满足叶片在高温空气和水氧耦合环境下的使用。
3.3.2 改进方法
(1)基体改性
在基体中加入自愈合相,引入Si-B-C基体,制备出自愈合SiCf/SiC CMC。有效提高致密程度,减少孔隙率,能大大降低氧化物质对基体的影响,提高基体抗氧化性。并且能与氧化性物质反应生成封填相,保护纤维和界面层,提高材料的氧化性能,延长使用寿命。
(2)界面层改性
界面层是纤维与基体之间一相,也是纤维表面的涂层,界面层对陶瓷基复合材料力学性能有很大影响,它能传递载荷,能抑制纤维裂纹偏转来保护纤维,提高复合材料的抗弯强度。其中,热解碳PyC和六方氮化硼BN是应用较多的界面层。目前,提高界面层的方法有2种,第一种方法是在界面层中加入硅,改善界面层抗氧化性;第二种方法是使用多层界面,一层提高力学性能,一层提高抗氧化性,如(PyCSiC)n或(BN-SiC)n,有望同时实现弱结合界面和提高抗氧化性的目的。
(3)EBC环境屏障涂层
高温合金抗氧化能力强,但承温能力不足需要在其表面制备能降低其表面温度的TBC热障涂层。与热障涂层不同,环境屏蔽涂层EBC主要应用于陶瓷基复合材料体系,其主要作用是抵御燃气环境对材料的腐蚀。同时,EBC涂层还要对基体具有一定的自愈合作用,从而有效地保护CMC-SiC构件,防止裂纹、孔隙扩大,提高其在燃气环境中的使用寿命。
4 总结
本文从航空发动机的发展趋势总结了航空发动机对于材料应用的要求,详细地介绍了应用于航空发动机涡轮叶片的高温合金发展历史,并总结了当前高温合金存在的问题,结合目前复合材料在航空工业上逐步普及的趋势,引出了使用陶瓷基复合材料制造发动机涡轮叶片的可能性,同时介绍了目前陶瓷基复合材料的研究、制备、应用现状。经过阅读文献进行理论研究得出,高温合金发展至今已经有数十年,通过改良制造工艺,可制造出强度更高的合金,通过优化合金成分,提高合金的综合性能。同时,采取在叶片内部设计复杂冷却通道以及在叶片表面添加热障涂层的方案,使得高温合金能够在高温、高应力的环境中工作。航空发动机发展带来的涡轮前温度大幅提升是不变的趋势,这对涡轮叶片原材料的要求越来越高,高温合金每更新一代的性能提升幅度不大,新材料应遵循“先静止后转动”的规则,后期可逐步在转动件上开展试验。
(《中国设备工程》 2022年第7期 P268-269)
声明:本网站所收集的部分公开资料来源于互联网,转载的目的在于传递更多信息及用于网络分享,并不代表本站赞同其观点和对其真实性负责,也不构成任何其他建议。本站部分作品是由网友自主投稿和发布、编辑整理上传,对此类作品本站仅提供交流平台,不为其版权负责。如果您发现网站上所用视频、图片、文字如涉及作品版权问题,请第一时间告知,我们将根据您提供的证明材料确认版权并按国家标准支付稿酬或立即删除内容,以保证您的权益!联系电话:010-58612588 或 Email:editor@mmsonline.com.cn。
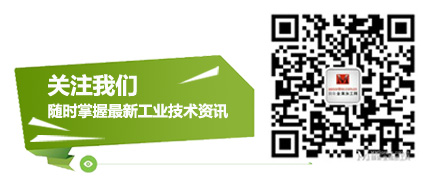
- 暂无反馈