如何有效缩短模具的制造周期
车型更新随着汽车行业竞争的日益激烈而越来越快,周期越来越短。模具开发部门需要对模具开发各环节进行总结分析,缩短开发周期,以达到提升模具开发效率的目的。
汽车覆盖件模具的开发分为设计与制造两个阶段。设计包括冲压SE、冲压工艺DL图设计、CAE分析与模面补偿设计、CAM模面设计、模具结构设计、FMC、结构以及模面编程,制造包括FMC制作、铸锻坯准备、一次加工、初组装、二次加工、装配、研配、调试以及品质提升与交付等过程。模具开发周期中,整车的模具设计周期通常约为4~5个月,而模具制造周期长达12个月,调试与品质提升占5~6.5个月,因此,提高模具的制造效率对于缩短开发周期意义重大。
覆盖件模具设计与制造现状
覆盖件模具的开发近几年在技术上已取得较大进步,大都已实现三维DL图设计,工艺进行全工序CAE分析,已开始模面补偿设计,模面进行不等间隙设计。模具结构进行三维实体设计,进行动态干涉模拟、废料滑出模拟以及冲压自动线模拟等。
模具制造上,已实行FMC三维加工,一次加工全程序化,二次加工自动化,模具淬火(推行中频淬火和火焰淬火),部分企业已开展激光淬火,推行火后型面精加工。模具制造已开展“一个流”的制造模式。
模具制造周期长的主要原因包括:部分零件装夹困难,凸凹模间隙不合适、研配工作量大,部分零件开裂、起皱和回弹等缺陷需反复调试整改,计划管理不当以及设计错误等。
工艺与模面设计问题
1.产品工艺性不合理,从冲压工艺上难以完全解决,零件达不到质量要求,调试难度大,造成模具更改或多次反复调试。
2.CAE分析参数设置不合理或者分析选用材料性能优于生产实际使用的性能,分析未考虑安全裕度或产品的特殊要求,从而造成工艺设计数据与制造调试结果偏差较大,造成调试的反复。
3.工艺数据或零件产品数据存在缺陷问题,造成后期要在调试中解决。
4.模面间隙设计不合理,造成后期研配的工作量较大,设计未考虑零件成形过程中材料的厚薄变化、机床的凹心补偿及零件的膨胀处理等。顶盖拉延模未着色部位,是按料厚间隙设计的,造成已着色部位的型面余量需要全研配掉,浪费30多小时。
5.修边刃口角度不合理,或正修侧修交接刀处易产生毛刺,常造成调试的反复。修边刃口展开精度不够或试料验证不准,造成刃口调整及补焊加工,特别是有时整改的刃口不垂直、不锋利以及间隙不均匀,产生毛刺,需多次调试。
6.模面设计未考虑清根或强压区域大,需要钳工清根或研配工作量大。
7.工艺信息传递不到位,如:钳工不了解模具各部位的研合要求,表面处理人员对淬火区域了解不到位,造成返工或信息确认时间长。
模具设计与制造工艺上的问题
1.模具排气孔、螺钉孔未设计出来,需要钳工自己打,钳工为让开背面的筋,找排气孔位置费时费力,螺钉孔配作,需要串行,周期长。侧向的孔钳工打孔效率较低。
2.斜楔和滑块等或部分小拼块的装夹困难,设计未考虑装夹工艺夹头,往往评审时在现场增加。未有夹头在加工时需要多次装夹才能完成,加工精度低;有的实型制作时是现场加的,编程不了解夹头位置,程序与实物不符,易造成撞刀的安全隐患,经常造成程序的反复。
3.模具标识无规范,设计实体无标识。特别是无图化生产,铸件拼块刚进厂时,零件的区分查找存在困难,浪费区分时间。
4.型面数铣加工参数有待优化。传统设定精加工余量为0.15mm,模面精铣后的精度±0.05mm,表面粗糙度达不到要求,尺寸精度差,研合工作量大,周期长。
5.工艺设计上,修边、翻整拼块型面和刃口在模座和拼块螺钉紧固一体后加工,模座和拼块加工的串行影响到模具的制造周期。
冲压工艺与模面设计注意事项
1.接到产品数模时就开展冲压SE,结合数据库、CAE分析结果和评审表单内容,应用FEMA技术进行分析,将产品问题以ECR报告的形式与产品设计部门沟通,最大限度地优化产品工艺性,在工艺方案设计时,考虑零件的质量保证。
2.CAE精算。建立内外板及典型件的CAE参数设置规范和评价标准,建立典型件的数模再造补偿方案库。例如CAE安全裕度的规定、材料的选定要求、各种材质减薄率要求、材料滑移要求以及全工序分析的零件合格率要求等,满足要求的才能下行。在模具上刻出收缩线、毛坯上设定网格,零件调试时,CAE与调试对比,将结果纳入到数据中。
3.设计流程中增加加工模面数据和产品数据的确认环节,CAE分析时对外板零件进行评价,对凹陷处增加模面补偿,减少钳工的大量研配工时。
4.建立模面间隙设计标准。拉延模面设计时考虑使用冲压机床的凹心(检测调试冲床和用户机床工作台、滑块的凹心,建立数据库),根据零件大小和种类进行模面揪起补偿;拉延模模面设计进行膨胀处理;拉延筋管理面强压和空开面的间隙处理;考虑零件功能面和解决回弹的强压和空开区的间隙处理;考虑材料变薄的模面间隙补偿;后序模具模面设计,压件器的强压区和整形拼块间隙负间隙;对材料变薄处的模面间隙补偿。
5.工艺设计重视修边毛刺问题,允许条件下优先分序修边,对刃口线展开的数据验证总结提升CAE分析精准度,保证毛坯展开准确,取消刃口线验证内容。
6.建立标准模面设计时对非重要圆角进行清根设计。
7.设计信息及时准确地传递到位是减少反复的重要一环,为保证信息的畅通,建立规范和信息单,如下发数据交接单、研配着色卡、翻整类模具的淬火区域指示图等,规范和信息单均放在PDM及ERP中。
模具结构设计与制造工艺优化
1.排气孔和螺钉孔。模具排气孔和螺钉孔设计出来,在数控铣上打出来,或者垂直的孔点窝,侧向的在数控铣上打出来,垂直孔钳工钻,缩短钻孔时间,提高精度。
2.建立异形凸模、斜楔和滑块等零件的装夹支撑系统规范,设计预留工艺夹头,可达到编程和加工的统一,提高加工效率和精度。设计滑块的夹头和装夹使用示例如图9所示。
3.模具标识。结合各用户和模具工厂的特点,建立模具标识标准,在铸件模座上和拼块上设计出标识或标识打印位置,在铸件上优先铸出来,操作者按照标识查找或对号安装即可,也方便了模具维修。图10所示为修冲模滑块和安装面标识示例。
4.对影响精度和效率的数铣型面加工工艺参数进行研究,结合零件的各部位特征,对刀具转速、进给、步距、切削方式和加余量设定优化规范。例如模面精加工余量调整为0.05mm、调整刀具转速和进给,模面的数铣半精和精加工效率提升40%以上,型面粗糙度、精度也得到大幅提升。
5.修边和翻整拼块加工工艺路线的调整。修边和翻整拼块型面和刃口分步加工到位,热处理后再组装,对于修边模具的刃口也只留火后精加工的余量,从编程上就分开实施,节约了拼块型面和刃口加工及热处理的周期。
结语
随着覆盖件模具数据库的完善和分析软件的深入应用,以及机床加工精度的提高,只要技术阶段各项设计工作细化,在设计阶段考虑前述各种问题,从产品设计、工艺设计和模具设计源头开始,进行充分的虚拟验证,对以前发生过的问题或分析发现的缺陷加以预防,及早采取措施,信息传递到位,就可减少装配、加工装夹及辅助时间,提高制造精度,必然会极大地减少研配时间和调试次数,满足冲压件质量要求,最终达到缩短模具制造周期的目的。
(模具达人)
声明:本网站所收集的部分公开资料来源于互联网,转载的目的在于传递更多信息及用于网络分享,并不代表本站赞同其观点和对其真实性负责,也不构成任何其他建议。本站部分作品是由网友自主投稿和发布、编辑整理上传,对此类作品本站仅提供交流平台,不为其版权负责。如果您发现网站上所用视频、图片、文字如涉及作品版权问题,请第一时间告知,我们将根据您提供的证明材料确认版权并按国家标准支付稿酬或立即删除内容,以保证您的权益!联系电话:010-58612588 或 Email:editor@mmsonline.com.cn。
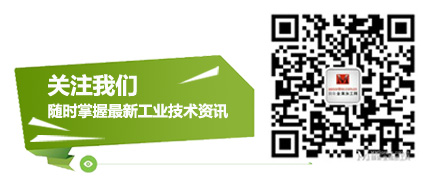
- 暂无反馈