航空发动机 | 商用航空发动机数字化装配工艺
产品装配是制造企业形成交付产品的重要环节,对产品质量和制造成本具有极其重要的影响,占用了企业大量的人力和物力。工艺设计是连接产品设计与产品制造的桥梁,是产品制造的关键环节。其中,装配工艺文件是指导零组件装配过程和工人操作的技术指导性文件,是集件配套、技术安排、生产准备等工作的主要依据。因此,优秀的装配工艺设计方案对于加速企业技术创新,提高产品的质量和可靠度,降低产品研发费用,缩短研发周期具有十分重要的意义。
对航空航天产品来说,基于模型的数字化装配设计是虚拟制造的核心技术之一,是实际装配过程在计算机上的本质体现[2],其与CAD 技术相结合,可以解决设计与装配对象在研制过程中难以实现的动态性能仿真[3]。随着计算机技术、网络技术的发展,欧美航空航天领域各制造大国均已全面采用3 维数字化设计和制造技术[4],波音公司的777 实现了整机的3维虚拟装配工艺设计与仿真[5],应用基于模型的预装配技术,使波音777 的制造成本降低了20%~40%[6]。
计算机辅助工艺设计(Computer Aided ProcessPlanning,CAPP) 是近年来发展起来的1 门机械制造企业应用系统,世界上第1 个CAPP 系统由挪威NAKK 提出,称为Autopros[7],从根本上改变了依赖于个人经验和人工编制工艺规程的落后状况,促进了工艺过程的标准化和最优化,提高了工艺设计的质量[8]。20 世纪70 年代以来,世界各国均有开发,如日本日立制作所的HIMTCS 工艺设计、美国的Miplan 系统、国际机械制造研究会(CIRP)的CAPP 系统等[9]。中国于20 世纪80 年代初,开始计算机辅助工艺设计(CAPP)的应用研究,近30 年来,在理论实践上均取得了重大成就,并于1995 年发布了JB/T7701-1995《计算机辅助工艺规程(CAPP)设计导则》[10],标志着中国CAPP研究开发进入成熟期。
基于现代工艺设计技术的发展现状,本文结合商用航空发动机生产实际,提出了基于Team Center &Cortona 3D 集成的CAPP 系统,构建基于模型的数字化装配工艺设计环境。该系统能够有效提高商用航空发动机装配工艺设计效率和质量,缩短产品研制周期。
1 装配工艺技术现状
中国的航空航天工业中,基于模型的定义(Model-based Definition,MBD) 技术已得到广泛的应用[11]。中国某企业较早实现了数字化装配工艺方面应用,基于工艺规划与设计基础平台(TeamcenterManufacturing,TCM) 实现工艺结构化, 将工艺(Process)、工厂(Plant)、产品(Product)、资源(Resource)统一关联管理[12],已经初步实现了零件装配、部件装配、组件装配以及整个发动机的装配工艺设计的数字化和虚拟仿真验证,输出各级装配的工艺指导文件。实现了工艺过程相关的业务管理,能接收设计产品数据管理系统(Product Data Management,PDM)的工程物料清单(Engineering Bill of Material,EBOM)和相关设计数据,保证工艺版本与研发过程中设计数据版本相匹配。然而,这与理想中三位一体、3 维可视化、系统全面集成、操作便捷、全面满足未来装配制造要求的设计系统仍存在较大的差距,具体表现在以下几个方面:
(1)工艺设计任务通过Excel 进行表单管理,管理效率低下,不直观。
(2)工艺分工以及工序、工步内容设计过程中没有有效地与产品3 维模型相结合,未形成连贯的基于模型的装配工艺设计业务流程。
(3)工艺知识库和工艺资源库未进行合理的建设,不便于工艺知识重用。
(4)工艺与工装设计、手动工具、设备、辅耗材等工艺设计资源未形成有效协同。
(5)没有生产现场工艺问题记录与反馈机制。
(6)工艺设计工具未与产品数据进行有效集成,无法充分复用前期工艺规划与设计成果,造成重复设计。
2 系统构建整体方案框架
全球权威产品全生命周期管理(Product LifecycleManagement,PLM) 研究机构CIMdata 认为,PLM是应用一系列业务解决方案,支持在企业内和企业间协同创建、管理、传播和应用贯穿整个产品生命周期的产品定义信息,并集成人、流程、业务系统和产品信息的1 种战略业务方法[13]。
根据CIMdata对PLM 应用成熟度的定义,自下至上分为初始级、规范级、精细级、优化级、智能级5 个等级。目前,中国已初步构建起工艺规划与设计基础平台(TeamcenterManufaturing,TCM)、装配工艺仿真系统(Tecnomatix)以及3 维装配工艺手册设计工具(Cortona 3D,C3D)3个维度的数字化装配工艺系统应用环境。目前实现了工艺设计资源的结构化及实时共享,为了更好地解决行业问题,满足自身业务需求,在数据规范、流程规范上开展了数字化装配工艺设计系统的技术研究。对于整体的解决方案框架最终落地有3 个层面。
第1 维度是系统质量,包括系统功能、系统架构的扩展和系统的开放性;第2 维度是实施方案质量,通过围绕方案的可执行性,有效、方便和规范标准化,结合行业的先进经验以及自身的流程体系进行实施方案的构建;第3 维度是基于系统质量和实施方案质量,最终实现基于模型的装配工艺设计的流程体系的构建,支持数字化装配工艺设计的体系和工程的交付能力、产品制造能力的提升。建设基于统一架构的数据化工艺设计平台,按照业务的需求实现系统功能,支持业务模型定义、属性定义、编码规则、分类、电子化流程等功能性要求扩展,从业务实施方案维度来说,所有系统功能的实现是为了满足业务导向实施方案的实现,基于模型的装配工艺设计关键业务方案主要包括装配工艺方案设计与评审、工艺物料清单(Process Bill of Material,PBOM)结构与管理、工艺资源库管理、基于模型的装配工艺规划、基于3 维环境下的装配工艺详细设计、工装协同设计管理、工艺仿真管理、工艺数据发布管理、工艺变更管理以及工艺台账管理等关键业务。
3 关键业务流程
通过根据业务问题点的梳理将装配工艺设计业务流程分为6 个阶段:装配工艺设计准备、装配工艺规划、工艺详细设计及工装设计、工艺仿真验证、工艺数据发布、装配工艺更。对这6个阶段与系统相关的关键业务场景进行描述,以指导技术人员在今后的工作中如何运用系统。
(1)装配工艺设计准备阶段。接收研发端的产品设计数据,并创建下发单进行产品研发数据的下发;创建型号项目工艺知识库结构,用于后续开展工艺设计、工装设计的数据统一管控;工艺资源的构建和维护,对已由工艺资源结构的创建和工艺资源的导入、工艺资源的废弃等业务过程管理。
(2)装配工艺规化阶段。进行PBOM 上层结构的创建以及与EBOM 的关联,指派EBOM 的零件数据;基于PBOM 的装配主单元进行工艺任务的可视化派工,PBOM 详细设计以及工艺任务进度状态的管控;进行装配工艺工艺清单(Bill of Process,BOP)的上层框架构建以及其他工艺文档文件的创建。
(3)工艺详细设计及工装设计阶段。进行装配工艺BOP 的详细设计,包含工艺、工序、工步的创建、PBOM 与BOP 的制造目标关联以及BOP中的零件消耗和工艺资源库的调用和指派;工装的申请、工装派工、工装的详细设计以及BOP 和工装数据的预发布。
(4)工艺仿真验证阶段。根据装配工艺方案业务要求进行工艺工装的仿真分析;基于工艺仿真任务模型(仿真内容、数据、检查项)驱动装配工艺仿真分析。
(5)工艺数据发布阶段。对装配工艺阶段产生的业务数据进行发布和归档管理,以达到数据的发布共享。
(6)工艺更改阶段。进行装配工艺阶段各业务数据的变更管理和各业务数据的台账创建维护及管理。下文将对装配工艺规划、工艺仿真验证、工艺详细设计及工装设计3 个主要业务场景进行介绍。
3.1 装配工艺规划阶段装配工艺规划阶段的主要任务是完成EBOM 到PBOM 之间的数据交换。EBOM是由设计部门提供的产品设计数据,包括产品名称、产品结构、明细表、汇总表、产品使用说明书及装箱清单等信息[14],在其编写过程中往往只考虑到产品的功能和设计需求,无法兼顾制造部门的产品制造过程和企业制造能力,需要处理后才能被生产制造部门所使用。PBOM 为工艺设计部门以EBOM 中的数据为依据,将EBOM 按照功能/ 系统进行分解后,重新按照装配制造顺序/ 区域进行构件的物料清单(Bill ofMaterial,BOM)数据,其中除了基本的BOM 信息之外还包含工艺计划、工序信息等生产所需数据[15]。EBOM与PBOM 的转化关系。通过定制化在系统中创建PBOM 顶层节点,依据装配工艺方案,按照实际装配过程重构EBOM,构建PBOM 中第1 级装配单元。在本装配工艺设计系统中,用户可以直观地通过3 维模型进行PBOM 结构的构件,并使用责信度检查确保相同零件在EBOM和PBOM 中的消耗数量一致,解决了过去装配工艺规划过程中表现形式不够直观的问题。
3.2 工艺详细设计及工装设计阶段通过继承PBOM 可以进行可视化装配工艺分工,在进行分工的同时可查看相关产品的数据、模型信息。分派任务的同时可通过资源负载查看工艺工程师当前时间段的任务负荷情况。任务下发之后会在工艺分工任务窗口中按照任务执行的状态情况,通过“红绿灯”的形式反馈任务的完成进度,使整体工作进度更加直观地表现出来,实现了工艺设计任务与产品研制任务的相匹配。装配工艺对象可以细化以装配操作最小单元,通过将装配资源有机结合的方式,将产品数据、装配工艺设计内容、装配通用要求、装配工装设备以及装配单元进行有机结合,实现工艺设计的“三位一体”,从而完成BOP 的设计,同时在设计过程中对装配资源可以进行可视化调用和典型工艺BOP 调用,将产品模型、工装模型、工具模型以及装配单元进行比对,实现快速装配路线设计的搭建和可行性分析。
采用定制化工艺资源库和知识库管理:工艺资源指工艺设计过程中所有与制造工艺相关的各类对象,常见的制造资源如标准件、通用工具、专用工装、量具、检具、设备、原材料、辅料等。通过对典型装配工艺进行归纳总结,梳理出具有典型装配工艺、工序、通用要求以及装配测量项,以此作为工艺模板,形成工艺知识库。在进行工艺设计时,工艺人员可参考或者直接调用典型工艺生成新的工艺,提升工艺设计效率与质量水平。在完成BOP 设计后,将结构化的工艺信息传递至3 维装配工艺设计环境中。
以BOP 为对象将工艺中工序结构化信息与产品、设备、工装、工具等对象的3 维模型建立关联并将信息转化为基于Web 的html文本和3D 工艺文件包。通过XML 中间件调用方式,使得3 维装配工艺设计环境可以访问3 维轻量化模型与装配工艺详细设计数据,进而生成结合2 维、3 维图形与结构化文本的装配工艺文件。包含轻量化的3 维模型数据与在工艺编制窗口中编写的工艺文本,根据文本中的模型引用信息,在文本与3 维模型之间自动建立关联。工艺设计人员进行3 维装配动作指令操作(Action)设计,可以复用装配标准动作集,同时设计环境支撑现有模型数据生成2 维技术插图与BOM 信息,以满足多样的工艺文件发布需求。
设计环境支持零部件图解目录技术文档设计,支持HTML、PDF、XML 等发布格式,同时支持ATA2200、S1000D、DITA 等适航技术出版物的标准。3 维工艺数据由PLM 平台进行统一管理并完成最终发布。通过采用3 维工艺设计环境实现了工艺设计与设计资源对象的交互协同、3 维工艺设计环境下的装配工艺设计以及3 维装配工艺文件的管理,过程中设计数据资源的高效协同、数据共享与利用,同时生成的装配工艺文件可以直接作为装配现场的工艺数据供制造执行系统进行调用。
3.3 工艺仿真验证阶段装配工艺设计为按照自顶向下的顺序搭建BOP,因此需要按照自底向上的顺序逐层进行仿真检查。在装配工艺设计过程中,需要在搭建完工序还未加入工装与完全搭建完成这2 个阶段进行工艺规程预发布并输入仿真软件进行仿真干涉检查,如若出现问题,搭建者重新搭建并再次检查,直到没有问题发布最终的工艺装配顺序。在进行仿真验证之前,首先填写评审任务计划,通过验证项库逐一添加验证项对象,并将BOP与评审任务关联;之后输入到工艺过程仿真环境中,结合具体装配工步要求,确定零部件安装顺序,创建零部件的安装路径进行仿真分析。如无法通过仿真检查,则由工艺编制人员重新调整BOP 结构、工艺资源或者装配顺序并再次进行仿真验证直至验证通过。
4 结束语
针对商用航空发动机装配工艺设计工具应用问题,本文采用MBD 技术提出了基于TCM&C3D 集成方式设计思路,解决了工艺设计未建立有效的装配工艺设计任务管理机制、工艺设计未形成连贯的基于模型的装配工艺设计业务流程、工艺设计不便于工艺知识重用、工艺与工装设计、手动工具、设备、辅耗材等工艺设计资源未形成有效协同,工艺设计没有生产现场工艺问题记录与反馈机制以及工艺设计工具未与产品数据进行有效集成等问题,将装配过程的仿真如装配单元仿真、装配工艺过程仿真、可维护性仿真融入到工艺设计过程中,并在商用航空发动机产品核心机装配工艺设计上进行了应用。通过系统定制化为改进商用航空发动机产品装配制造过程提供了1 个全新的方法和手段,进行装配工艺数字化、产品可装配性分析、装配工艺优化、装配质量控制、装配工装验证,达到提高产品质量,缩短产品生产周期的目的。
(航空发动机)
声明:本网站所收集的部分公开资料来源于互联网,转载的目的在于传递更多信息及用于网络分享,并不代表本站赞同其观点和对其真实性负责,也不构成任何其他建议。本站部分作品是由网友自主投稿和发布、编辑整理上传,对此类作品本站仅提供交流平台,不为其版权负责。如果您发现网站上所用视频、图片、文字如涉及作品版权问题,请第一时间告知,我们将根据您提供的证明材料确认版权并按国家标准支付稿酬或立即删除内容,以保证您的权益!联系电话:010-58612588 或 Email:editor@mmsonline.com.cn。
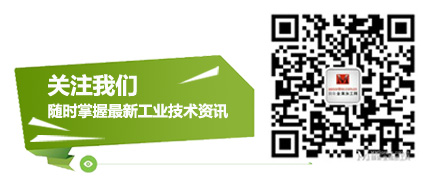
- 暂无反馈