航空发动机涡轮后机匣支板熔模铸造工艺优化
针对涡轮后机匣支板熔模铸造工艺,利用Procast软件对铸件充型过程、型腔内压力演变、铸件缩松、缩孔缺陷等方面进行模拟计算,深度剖析缺陷形成原因。采用改进排气通道、调整支板浇注位置与时长、铸件凝固顺序等措施优化工艺,同时进行数值模拟。结果表明,优化工艺的充型过程稳定、型腔内未形成“憋气”现象,支板内无缩松、缩孔缺陷,经浇注验证,铸件质量满足ASTM E192标准要求。
涡轮后机匣因承载航空发动机的推力与振动载荷,是发动机承力体系内不可缺少的一部分,其与涡轮盘、叶片、涡轮轴称为航空发动机4大关键部件。目前,涡轮后机匣结构件逐渐向大型化、复杂化、薄壁化等方向发展,其设计直径超过1 400 mm,厚度不超过2 mm的薄壁面积占整体结构件表面积的80%以上,因而很难通过精密铸造工艺制造。采用“机匣+支板”分体的熔模铸造,同时借助焊接工艺完成大型复杂薄壁涡轮后机匣结构件制造。关于制备尺寸较小的复杂薄壁机匣已拥有一定的科研成果与铸造经验,对于采用“机匣+支板”分体式铸造过程中的机匣制备可提供一定的借鉴与指导。但是,对于涡轮后机匣支板的制备则难于借鉴,且相关研究鲜有报道。因此,如何制备冶金质量优异且检验合格的涡轮后机匣支板已成为亟待解决的问题。
针对上述问题,若采用传统的铸造方法,需多组次“经验试制-缺陷分析-工艺优化”的研发,方能获得较为合理的工艺,这很难满足高品质和短交货期的市场竞争要求。然而,借助数值模拟技术探究铸造工艺流程,不仅可结合模拟结果中合金液流动过程、铸件凝固顺序、宏微观缺陷等预测信息对工艺进行多轮次迭代优化,进而明确相关技术参数与控制要点,还能大幅度缩短产品的研发周期、降低工程技术成本、提高设备利用率等。
涡轮后机匣支板材质为K4169高温合金,其结构由承重吊耳、浮板及叶片3部分组成,轮廓尺寸为347 mm×286 mm×382 mm,结构三维图见图1。承重吊耳的厚度为31 mm,此部位为铸件的※厚区域,需设置较为合理的冒口或浇口,避免因热节而形成的缩松、缩孔缺陷。浮板呈内凹型,※大深度为64 mm,厚度在2.5 ~8 mm之间,此区域需避免浇注时因“憋气”现象而导致铸件产生浇不足的问题。
此外,叶片由不规则曲面组成,厚度为3 mm,其内部包含两根加强筋,每根加强筋上包含一个10 mm×10 mm的通孔,且叶片与浮板所成锐角约为67。,此部分应考虑与浮板的连通性、合理控制合金液的流入速率,避免叶片底端产生浇不足或形成缩松、缩孔等缺陷。
图1 支板结构三维图
01
初始工艺模拟分析
基于对支板结构的分析,先利用ProCAST模拟软件对支板铸件完成初始浇注系统的绘制,然后建立相对应的有限元模型,其初始浇注系统见图2。支板采用熔模铸造工艺,由于铸件与型壳为两种不同的材料,且两者在同一界面存在温度差,为确保模拟结果的准确性与区别界面两端的温度,将铸件与型壳的界面节点进行双重处理。
图2 初始浇注系统
从充型过程与型腔压力演变对支板初始浇注系统的设计进行分析,这样不仅可有效表征合金液在铸件内的流动状态,减少紊流,还可以避免因型腔压力分布不均或局部区域压力过大,使浇注系统内因“憋气”现象而引起铸件缺陷的问题。同时,以支板充型过程的流动分析为基础,增加型腔压力演变分布状态分析,既对初始支板浇注系统设计的合理性进行双重评判与补充,又为后续支板浇注系统的优化提供理论参考,其支板充型过程与型腔压力演变的数值模拟结果分别见图3和图4。
图3 支板充型过程数值模拟结果
图4 型腔压力演变数值模拟结果
图5为支板缺陷的数值模拟结果。叶片的边缘、中心、加强筋区域均存在不同程度的缩松、缩孔,中心区域的缺陷尤为突出。这是因为在充型过程中,合金液快速将叶片区域充满,而边缘与薄壁区域的冷却速率大于中心与加强筋区域,导致中心与加强筋区域凝固时仅有少量合金液补充,再结合叶片与浮板连接处附近区域的合金液流速波动较大,极易形成紊流区域影响叶片内合金液的温度梯度分布、凝固顺序等,致使上述叶片产生缩松、缩孔。
此外,在浮板区域存有2处缩松、缩孔,这是由于在充型过程中合金液的流速波动较大且分布无规律,致使浮板因合金液紊流而形成缩松、缩孔。承重挂耳区域由于顶部存有较大的补缩区域,而未形成缩松、缩孔。
图5 支板缺陷数值模拟结果
02
优化工艺模拟分析
基于数值模拟结果与分析可知,初始支板铸造工艺存在较为严重的充型憋气、合金液紊流、铸件缩松缩孔缺陷问题,因此本部分对初始铸造工艺进行优化。首先,将原有浮板区域的1处排气通道改造为3处,并将浇注时长调整为原初始方案的1.5倍;初始铸造工艺的砂箱尺寸为440 mm×360 mm×600 mm;随后,将支板以3处排气通道所成平面的法相方向旋转15°放置于砂箱内,并在叶片中心与加强筋两侧添加20 mm厚铁砂;最后,利用ProCAST软件完成上述优化方案的有限元模型建立与模拟参数设置,优化浇注系统见图6。
图6 优化浇注系统
图7~图9分别为优化后支板充型过程、型腔压力演变及支板缺陷的数值模拟。从图7和图8分析可知,当充型比例为20%时,合金液沿承重挂耳单侧区域经浮板流入叶片,未充型叶片部分与外部相连区域面积远大于初始工艺。此时,型腔内各处压力分布均相同且正常,其值均小于00.7 MPa;叶片内合金液的平均流速仅为初始工艺的0.56倍。随着充型比例达到40%时,叶片部分已完成充型,浮板与排气通道相连附近区域及一只承重挂耳未被合金液充满,另一只承重挂耳基本充满,此时型腔内各处的压力值分布仍小于0.7 bar,未出现“憋气”现象,且浮板部分的合金液流速分布较为稳定,其平均流速仅为初始工艺的0.27倍。
图7 优化后支板充型过程数值模拟结果
图8 优化后型腔压力演变数值模拟结果
当充型达到60%时,支板主体部分已全部充型,仅剩排气通道与补缩浇冒口未被充满。此时,型腔内的压力值均在0.7~1.3 MPa内,虽相比于前期充型阶段有所提高,但所处区域为排气通道与补缩冒口,其影响可忽略不计,随后合金液继续平稳充型直至充型结束。通过图9可知,支板整体部分未发现缩松缩孔缺陷存在,仅在排气通道与补缩区域有缩松缩孔缺陷。由此可见,优化后工艺的充型过程稳定、合金液流速平缓、型腔内未形成“憋气”,解决了支板在初始工艺中的缩松、缩孔缺陷。
图9 优化后支板缺陷数值模拟结果
03
生产验证
基于数值模拟优化后涡轮后机匣支板的铸造方案,采用熔模铸造生产,完成首批5件试件。利用数字实时成像检测技术对全部试制件内部进行探伤检测,其结果均满足ASTM E192标准中气孔、夹杂、缩松等要求,见图10。这表明涡轮后机匣支板铸件检验合格,验证了数值模拟计算与结果分析的准确性。此后,再次采用熔模铸造工艺,小批量制备了40件支板,其探伤检测结果均满足标准要求。
图10 数字实时成像检测系统的成像结果
04
结语
(1)利用Procast软件对涡轮后机匣支板初始熔模铸造工艺进行数值模拟,通过流动、压力及缺陷等模拟,判断初始工艺存在较为严重的合金液紊流与型腔憋气现象,及支板形成缩松、缩孔缺陷。通过添加砂箱与铁砂、改造排气通道、设置支板摆放位置、调整浇注时长等操作,对初始涡轮后机匣支板熔模铸造工艺进行优化与数值模拟,获得较为合理的熔模铸造工艺。
(2)基于优化后涡轮后机匣支板的熔模铸造工艺分别进行了首批试制与小批量生产,其探伤结果均满足ASTM E192标准要求,验证了数值模拟计算与结果分析的准确性。
引用格式:杨新娣,田智星,路涵博,等. 涡轮后机匣支板熔模铸造工艺数值模拟及优化[J].特种铸造及有色合金,2021,41(9):1184-1188.
(特种铸造)
声明:本网站所收集的部分公开资料来源于互联网,转载的目的在于传递更多信息及用于网络分享,并不代表本站赞同其观点和对其真实性负责,也不构成任何其他建议。本站部分作品是由网友自主投稿和发布、编辑整理上传,对此类作品本站仅提供交流平台,不为其版权负责。如果您发现网站上所用视频、图片、文字如涉及作品版权问题,请第一时间告知,我们将根据您提供的证明材料确认版权并按国家标准支付稿酬或立即删除内容,以保证您的权益!联系电话:010-58612588 或 Email:editor@mmsonline.com.cn。
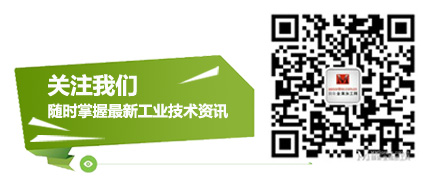
- 暂无反馈