白皮书 | 基于VCSEL技术的9.6 kW晶圆加热系统
摘要
此白皮书向我们展示了使用分散但密集的高功率VCSEL发射器进行均匀大面积加热的可能性。
应用示例采用Ø 300 mm硅晶片和用于大面积热处理的9.6 kW VCSEL加热系统,就使用VCSEL加热模块对硅晶片进行快速热处理 (RTP) 的好处进行讨论。在白皮书中,展示并阐述了应用结果。此外,该白皮书中以光学模拟的形式突出展示了为潜在系统适应性提供的进一步的可能性和灵感,以此来满足客户的需求。
01 晶圆加热的挑战
在将晶圆切割成单个芯片之前,半导体器件的生产需要在晶圆上进行许多不同的生产步骤。
在晶圆加工过程中,对温度的要求需要不同程度,最高需达到1000°C且具有非常好的均匀性。
为了达到预期的工艺效果,通常必须快速加热晶圆。
此外,使用VCSEL加热系统,可以在制造过程中节省大量时间,减少副作用,从而提高良率。
图 1: 通快位于乌尔姆的VCSEL无尘室生产线。
02 VCSEL加热系统的应用设置
通快光电器件部在亚琛的互连技术中心里,配备了紧凑且安全的激光装置,可用于各种应用测试。该装置配备了红外摄像机、光学摄像机、高温计、热电偶和快速线性轴。
加工件和VCSEL加热模块的灵活安装性,可以满足不同的应用需求。
与客户一起进行可行性测试,可以让客户现场体验大功率VCSEL模块。
从2.4到9.6 kW的标准模块均可进行测试。并可满足特殊模块需求。
对于接下来要讨论的晶圆加热应用,我们建立了一个专用的9.6 kW加热模块。
图 2: 亚琛互连技术中心里的设备。激光室配备有冷却单元、驱动单元和控制电脑。
03 VCSEL解决方案应用于晶圆加热
首先,通过光学模拟以优化标准VCSEL发射器的分布,以实现晶圆的均匀照射(图4)。分析表明,仅使用24个标准发射器和一个镜管(图3),就可以在晶圆层面上达到完美的均匀性。加热速率和工作距离可以通过改变发射器的数量来控制,从而优化系统的性能和成本。
根据这些模拟结果,在第二步中,构建了一个9.6 kW的晶圆加热系统(图 5,不带镜管的模块)。最初的测试是在裸硅晶片上进行的。晶圆加热器可以扩展到75.2 kW,加热速率提高8倍以上。
图 3: 带有特定排列发射器的晶圆加热器布局。
图 4: 在不同工作距离下使用外反射镜进行光学模拟:30/200/450 mm。虚线圆圈代表一个Ø 300 mm的晶圆。
图 5: 9.6 kw晶圆加热器的VCSEL加热系统
04 晶圆加热的实验装置
在亚琛互联技术中心,配备了9.6 kW的晶圆加热器(图6和图7)。
首次测试使用的是Ø 300 mm黑色涂层不锈钢仿真晶圆和Ø 300 mm裸硅晶片;使用导热系数低的支架将晶圆安装在三个点上。所有实验均在正常气压下进行。在加热过程中,用红外摄像机记录温度和均匀性。相机的发射率设置是按照裸硅或黑色钢涂层来进行校准的。
图 6(上): 激光室介绍: 在VCSEL模块前面,可以看到长度为 450 mm的六边形镜管。
图 7(下): 安装Ø 300 mm晶圆。晶圆背面涂有黑色涂层,用来实现准确的温度测量。
05 硅晶片加热
用9.12 kW代替仿真时的9.6 kW的红外功率来辐射硅晶片。对VCSEL加热模块的激光功率分布进行微调,从而提高了硅晶片温度的均匀性。为了防止中间过热和补偿由于从晶片底部到顶部的热空气流动造成的对流损失,功率分布的调整是必要的。
低温(25~230℃)时,升温速率为51 K/s;在625 °C时,由于热晶圆重新发射的对流和长波长辐射,升热速率降低到16 K/s。
垂直安装的晶圆在空气中的平均升温速率为32 K/s,具有良好的均匀性。平均晶圆温度达到640 °C需要20秒。
垂直安装的Ø 300 mm晶圆在空气中的温度均匀性为±8 K。
图 8: 红外相机在峰值温度下拍摄的二维图像和水平温度廓线。图中还显示了ROI 1到5的位置。
图 9: 温度-时间图:平均值和ROI 1到5。在测量过程中,红外相机使用快门进行定期校准,从而出现温度曲线扭结。
06 结论(一)
一种新型可应用于大面积区域加热的VCSEL模块,它被证实了具有很高的加热速率和非常好的均匀性。
该系统配备了24个精心分布的VCSEL发射器,总红外功率为9.6 kW。对于Ø 300mm硅晶片,可以实现高达51 K/s的升温速率,空气中的温度均匀性为±8 K。
这个模块概念可以通过更密集的发射器封装来扩展到更高的性能。Ø 300 mm晶圆加热器可使用的最大发射器数量为188个,这意味着总红外功率为 75.2 kW。该模块的光学模拟如图10到13所示。图中的圆圈代表Ø 300 mm晶圆。
图10展示了在20 mm工作距离下的红外功率分布模拟。此配置可适用于旋转晶圆的应用。
为了获得更均匀的照射,应在侧面增加镜子,工作距离也应该会更大。图11展示了工作距离约为250 mm的模拟,适用于70 W/cm²的均匀红外辐照。这可使硅晶片的升温速率高达 260 K/s。
然而,均匀的照明不一定会得到均匀的温度分布,例如,由于与应用相关的冷却效应。VCSEL加热系统的一大优势是:188个发射器的每个区域的功率水平可以单独控制。由于每个发射器有两个区域,所以每个模块可以有376个不同的功率设置。
图12和图13演示了这一优势。在模拟中,发射器的一圈被关闭。图12展示了在20 mm距离处的强度分布和被关闭的发射器。图13着重展示了在250 mm工作距离下的强度模式。
图 10: VCSEL模块应用于晶圆加热的光学模拟:具有188个发射器,工作距离为20 mm。
图 11: VCSEL模块应用于晶圆加热的光学模拟:具有188个发射器,工作距离为250 mm。
图 12(左) / 13(右): VCSEL模块应用于晶圆加热的光学模拟:具有188 个发射器,工作距离为20 mm和250 mm。
06 结论(二)
取决于应用,较低密度封装的发射器也同样具有优势。较低密度的包装会产生更多空间,可用于集成光学计量,用于在加工过程中对晶圆进行温度测量。因此,在使用VCSEL系统对晶圆进行辐照时,测量可以从同一侧进行。辐照可以来自顶部或底部,总之, VCSEL仅发射特定波长的激光辐射(在本应用示例中为980 nm)。因此,通过适当过滤VCSEL的辐射,可以抑制对光学计量的干扰。
从晶圆背面测量温度将排除晶圆正面发射率不均匀性的负面影响,不均匀性是由于结构造成的。
使用VCSEL高功率加热系统加热晶圆的更多优势:
选择性加热: 通过激光辐射,硅晶片选择性加热,在980 nm时,硅可以有较高的吸收性。
VCSEL芯片寿命长,可靠性高。
激光模块的纤薄设计。
非常低的服务投入。
易于定制: 总功率以及系统成本可以在9.6到75 kW之间选择,只需安装适当数量的发射器即可。
通过这些晶圆加热的应用测试和模拟,已经证实了可以使用高功率VCSEL发射器进行大面积加热。它是可行的、可扩展的、具有成本效益且可靠的。此外,它还为快速热处理 (RTP) 提供了新的可能性。
(通快光电器件部 通快)
声明:本网站所收集的部分公开资料来源于互联网,转载的目的在于传递更多信息及用于网络分享,并不代表本站赞同其观点和对其真实性负责,也不构成任何其他建议。本站部分作品是由网友自主投稿和发布、编辑整理上传,对此类作品本站仅提供交流平台,不为其版权负责。如果您发现网站上所用视频、图片、文字如涉及作品版权问题,请第一时间告知,我们将根据您提供的证明材料确认版权并按国家标准支付稿酬或立即删除内容,以保证您的权益!联系电话:010-58612588 或 Email:editor@mmsonline.com.cn。
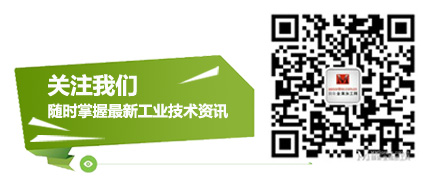
- 暂无反馈