冲压模具丨影响量产结构问题:断螺丝、拉伸破裂、不脱料解决方案
新模组装完成后需要完成上机、打样,也就是打一些产品作为样品去品管部进行管控尺寸测量,看是否合格。当完成这一步后,模具将进行量产阶段。而在模具量产过程中就很可能出现各种结构、设计思路问题。
01拉伸(深)破裂
原因:
1>.凸凹模之间隙过小(包括整体间隙和凸凹模偏移之局部间隙)
2>.凹模无圆角粗糙度过大
3>.材料材质过硬,塑性不好
4>.拉深高度超过材料塑性变形的极限(拉深次数为一次)
5>.第二次拉深材料未到位
6>.压边边不够,拉深后凸台边缘起皱或凹陷
改善对策:
1>.将凸凹模间隙修整至正常值
2>.按产品要求研磨至正常值
3>.如果材料超规太多则更换材料,另可相应加大凹模R角及光亮度可避免
4>.可以分几次拉深
5>.调整定位使其能正确定位
6>.凹凸模之胶料板加弹弹力,增加压边力
02抽芽破裂及偏差
原因:
1>.抽芽冲头预冲刃口断掉
2>.凸凹模偏位(一次性抽芽)
3>.凸模与凹模间隙过小(预冲孔抽芽)
4>.预冲孔毛边过大或冲头断掉,孔未冲出
5>.凸模破裂(抽芽冲头工作部位崩缺)
改善对策:
1>.更换抽芽冲头
2>.调整凸凹模位置
3>.将凸凹模间隙调整至适中
4>.更换预冲冲头
5>.更换抽芽冲头
03抽芽高度不够
原因:
1>.预冲孔孔径太大
2>.抽芽冲头工作部位进入凹模深度不够
3>.抽芽了冲头直径太小,与凹模间隙太大(或凹模直径太大)
4>.预冲孔之材料到抽芽工站时错位,以致抽芽后一边高一边低
改善对策:
1>.将预冲孔修改至适当之直径(如果预冲孔太小,导致抽芽后偏高)
2>.加长抽芽冲头工作长度
3>.将抽芽冲头修改至所需要的直径,凹模也一样
4>.调整抽芽或预冲孔两个工站的定位,视抽芽孔的位置来调整
04脱料不顺
原因:
1>.模板磁性太大
2>.定位太紧
3>.脱料销弹簧失效(脱料板也一样)
4>.脱料板上无脱料销
5>.材料受压线挤压宽度增加在后工序定位不良造成
6>.材料变形平面度不良
7>.产品折边或成形后模具上避位不够
8>.滑块被卡死,活动不顺
9>.对于复合模,材料与废料未完全分开
改善对策:
1>.将模板退磁
2>.依产品定位的位置正确性调整定位
3>.更换脱料销弹簧(脱料板也一样)
4>.在脱料板上追加顶料销
5>.最好能采用内定位,或定位在没有变异的位置
6>.调整材料的平面度
7>.加大模具上之让位
8>.修整滑块,使其能滑块顺畅
9>.上下模追加顶料销,使材料与废料能顺畅分开
05螺丝易断
螺丝断裂:分正常损坏与非正常损坏
正常损坏之原因:
1>.螺丝本身的受力设计就不够(规格不对或数量不够)
2>.螺丝本身的材质太差
3>.螺丝的正常人损耗冲次已到而断
改善对策:
1>.将螺丝规格改大,如M8或M10数量增加(视实际情况不够)
2>.更换新材质之螺丝
3>.保养模具对更换
非正常损坏:
1>.二块板之间错位而强行紧固
2>.凸凹间隙过小(特别是成形模具)
3>.对于有气垫之模具,顶杆过长,气垫压力过大,导致下模螺丝断掉
4>.折边、成形模、冲压二片料或冲二次
改善对策:
1>.扩孔或重新鑽孔
2>.调整凸凹模间隙
3>.顶杆与模具气垫板标准化
4>.尽量避免冲二次或二片料
(冲压模具达人)
声明:本网站所收集的部分公开资料来源于互联网,转载的目的在于传递更多信息及用于网络分享,并不代表本站赞同其观点和对其真实性负责,也不构成任何其他建议。本站部分作品是由网友自主投稿和发布、编辑整理上传,对此类作品本站仅提供交流平台,不为其版权负责。如果您发现网站上所用视频、图片、文字如涉及作品版权问题,请第一时间告知,我们将根据您提供的证明材料确认版权并按国家标准支付稿酬或立即删除内容,以保证您的权益!联系电话:010-58612588 或 Email:editor@mmsonline.com.cn。
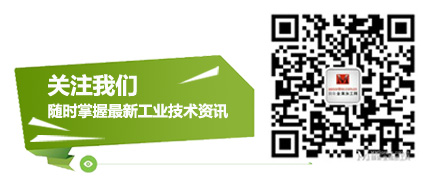
- 暂无反馈