DeburringTec:去毛刺&表面精加工技术的四个等级
在工业制造领域,有很多零件需要在焊接、铸造、成型或加工后进行后处理,包括打磨、抛光及去毛刺。例如首饰工艺品;汽车行业的发动机缸体、缸盖、汽车轮毂以及各精密金属部件;一般行业的卫浴五金;硬质塑料、塑胶自动车床零件;航空与能源行业的发动机叶片,涡轮叶片;3C行业的笔记本电脑、平板电脑、手机的外壳和内部元件;半导体硅片晶圆等。
去毛刺一直是零件制造商的“心腹之患”,在金属加工过程中无处不在。毛刺类型主要有飞边、尖角、细丝、飞溅、突出、粉末等不符合产品设计要求的金属残余,常见在钻孔、车削、铣削、切割、研磨、抛光等工序中。毛刺对工件的表面质量和机械性能有重要影响,以下是毛刺存在会导致的一些问题:
1、安全系数降低,锋利的金属边缘会为操作员带来安全影响;
2、操作过程中压力增加,会导致工件抗断裂,缩短疲劳寿命;
3、易受腐蚀,与材料厚度的差异有关;
4、尖角容易集中电荷,从而增加了静电释放的风险;
5、运动部件中的毛刺会增加不必要的摩擦和热量;
6、进行粉末涂料或电镀等精加工过程时会产生干扰;
7、由于毛刺碎屑的污染以及界面周边的磨损,会影响后期精加工过程中加工剂/抛光液工作质量。
一般情况下, 可将去毛刺与表面精加工方法按照柔性等级分为四大类,其中超精密去毛刺/研磨抛光方法与传统的金属表面处理方法有本质的区别。
1. 粗级:一般为人工去毛刺的硬接触类,普遍有切削、磨削、锉刀及刮刀加工等。
2. 普通级:一般为研磨去毛刺设备的柔软接触类,有砂带磨、研磨、弹性砂轮磨削及抛光等。
3. 精密级:属于半自动化和工业机器人的柔性-精密类,有冲洗加工、电化学加工、电解磨削、滚动加工、工业机器人打磨抛光等。
4. 超精密级:属于自动化、智能化的超精密类,有磨粒流去毛刺、磁力研磨去毛刺、电解去毛刺、热能去毛刺、密镭强力超声波去毛刺;超声波研磨抛光、离子束抛光、化学机械抛光(CMP)、 液面研磨抛光、水合研磨抛光等。 这类超精密的去毛刺/抛光技术可使零部件表面获得足够精确的加工精度。
我们综合全面考虑选择去毛刺和金属表面精加工技术时,既要保证质量、兼顾成本、环保高效,又要把控零件材料属性、结构形状、尺寸大小和精密程度,尤其要注意表面粗糙度、尺寸公差、变形以及残余应力等变化。
传统的金属表面处理方法广泛应用于基础工业制造。随着工业化和自动化程度的提高,在汽车工业、航空航天、半导体、仪器仪表等应用领域中,对机械零件制造精度要求和机构设计的微型化需求越来越高,这对去毛刺和表面精加工技术更加趋向于精密级和超精密等级,且更加智能化和自动化,提升了产品质量,提高了生产效率。
展会网站:https://www.deburringtec.com/
关注DeburringTec去毛刺展掌握一手行业快讯:DSTEXPO
联系方式:
电话:+86 10 5867 7200
邮箱:ming.ouyang@icleanexpo.com
声明:本网站所收集的部分公开资料来源于互联网,转载的目的在于传递更多信息及用于网络分享,并不代表本站赞同其观点和对其真实性负责,也不构成任何其他建议。本站部分作品是由网友自主投稿和发布、编辑整理上传,对此类作品本站仅提供交流平台,不为其版权负责。如果您发现网站上所用视频、图片、文字如涉及作品版权问题,请第一时间告知,我们将根据您提供的证明材料确认版权并按国家标准支付稿酬或立即删除内容,以保证您的权益!联系电话:010-58612588 或 Email:editor@mmsonline.com.cn。
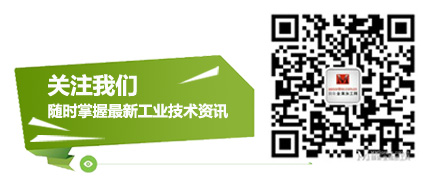
- 暂无反馈