数字化造船,提升我国造船竞争力的必然选择
在众多工业产品中,船舶无疑是建造复杂程度最高的产品之一。造船是一项系统工程,环节多、链条长、作业面广、设计制造周期长、劳动力成本高,近年来,面对国际船舶市场持续低迷、劳动力成本上涨等情况,造船方式正在展开一次商业模式创新和转型的数字化变革。加快智能化转型,造拥抱先进数字化技术,古老而传统的造船业正迸发出无限可能。近日,中国船舶集团旗下黄埔文冲首次完成支线集装箱船全船舱内导架数字化模拟试箱,实现了我国数字化造船又一创新。
数字化在造船领域用途广泛
数据可靠性、一致性和互连性,以及整个船舶设计和建造过程中最大限度地实现数据处理的自动化,是释放更大效率、提高生产率和提高盈利能力的关键因素。在数字化造船中,数据流在各专业、各阶段以及各船型之间都是可靠的、一致的且可复用的。数据驱动贯通整个船舶建造过程,同时将数据处理的人工干预缩减到最小,以此来维护数据完整性并优化船舶建造过程。
在造船过程中的各阶段都可能需要进行变更修改,而数据的高端数字化和互连性则意味着造船工程师可以在保持数据一致性的同时有效地进行上游和下游更改。
在以数据为动力的造船愿景中,一致的数据流实现零图纸生产和无纸化运营。IT智能允许以适合生产的数字格式提供数据。例如,在CADMATIC提供的数据中,第一个3D模型浏览器eBrowser于2000年在市场推出时,船厂的直接评估是他们能够将生产所需的工程图数量减少30%。
不仅如此,在管理上,数字化也可以大显神通。据介绍,以往的船厂堆场管理凭经验管理为主,根据调度人员的经验及场地安排堆位,随意性很大,致使堆放顺序换乱,也就增加了查找的时间成本和人工确定钢板的人力资源。在钢板流程的操作基本处于人工或者半人工的阶段,由于缺乏全流程的数字化管理,倒垛工作量大,增加了堆场吊机的负荷。外高桥造船的相关技术人员通过行车无人化智能改造实现钢板转运小车自动驾驶、钢板智能定位技术、钢板作业智能调度系统、钢板堆场疏运量智能化预测等关键技术的攻关,实现对港口钢板物流信息的实时跟踪,解决错漏难题,增强安全可靠性,提高运行效率,降低运营成本,迈出了码头及钢板堆场的信息和智能化服务水平的一大步。该科研成果的直接经济效益会非常明显,中国船舶外高桥造船负责人表示:“我们预计通过项目实施,可以提升翻板效率20%,大概节约电力能耗成本20%和人工成本300万元/年。”
通过区块链融资筹措造船资金,这是造船业的最新玩法。德国航运企业Vogemann近日宣布,将通过基于区块链的绿色船舶代币(Green Shipping Token)融资来筹集5000万美元,最低投资额为1000万美元。这笔资金将用于购买灵便型环保散货船。代币(token)融资是一种崭新的融资方式,利用区块链代币向投资者融资,通常投资者投入的是数字货币(如比特币),获得代币作为出资证明。代币也具有和比特币一样的区块链技术属性,不可篡改,可以转让,保证唯一。融资后,投资者可以将代币出让给其他投资者。融资主体未来回馈投资者时,投资者凭代币获取相应的权益。
颠覆传统的造船模式
“以前造一艘船需2—3年,现在最快的只需一年,为什么?就是因为造船方式发生了巨大变化。”中船集团上海船舶工艺研究所副所长谢新说。
造船工程着实复杂,但往简单里说,就是分解与组合两大步骤。所谓分解,就是在设计阶段建构整船模型,并逐级拆分为分段、组件、部件、零件;而组合,就是在生产阶段再将零件依次装配为分段、整船。
过去造船之所以耗时,很大程度上是“分解”做得不够智能。在船舶领域,由于行业特性和历史传承,设计与制造相对分离——总体所进行总体设计时,一般较少从建造角度考虑如何合理、高效;到了总装厂,还要再进行生产设计,重新进行三维建模,进一步明确“怎么造船”“怎么组织造船”。
“按传统方式,设计环节要尽快出图,建造中遇到问题再返工解决。”中船集团江南造船公司江南研究院副院长朱明华表示,这一模式带来了明显的弊端——同样做一处修改,在设计阶段花1个小时就能完成,若到建造阶段再发现、解决,就可能因为重新设计、采购物料、返工而耽误100个小时。
“推行现代造船模式,最重要的基础就是数字化。”谢新说,现在造船业常说“傻瓜造船”,指的是让一线工人的操作尽量转为“傻瓜式”的简单劳动,而在分解过程中依靠强大的数字化手段和三维设计能力实现高度智能。
据了解,数据驱动造船的关键部分是造船生命周期中使用系统的集成。传统意义上,在船舶设计和造船中产生的许多数据都是孤立的,效率也因此无法提高。CAD,CAM,ERP,MES,PDM和PLM的集成可以提供具有真正价值的数字双子。对于从设计、预制到生产实行垂直整合的造船集团而言,尤其如此。数字化造船可以共享所有实时信息源,从而实现所有专业之间的紧密协作,集成流程,并确保端到端的连续性。这种单一信息源可帮助船厂加快产品上市时间、降低成本、缩短交货时间,并减少在设计、制造和供应链中的质量问题。它通过数据驱动的流程和决策来释放效率的潜力,提高生产率并确保盈利。
传统造船方式的数字化转变也推动了船厂的转型升级,以外高桥造船为例,近年来,外高桥造船大力推进数据智能基础设施配置,搭建“数智工厂”,已初步实现了SWS-TIME建设、SEM系统升级,基本完成了基于大型邮轮工程的协同管理能力升级。同时,通过数字新基建打造工业互联网平台,逐步实现由企业内部界面管理,向多级供应能力管理转型;由传统批量化生产组织模式,向强项目制生产组织方式转变;由船舶产品全生命周期服务管理,向为船东提供数字化智能船舶和运维服务转变。
提升我国造船竞争力的必然选择
推进数字造船也是我国造船企业增强竞争力的重要选择,一方面,人工智能将成为船舶行业提高生产效率,降低企业成本的主要方式,帮助行业更好地优化生产流程、更好地配置整合资源,贯穿制造体系全流程。另一方面,人工智能的应用发展将改变现有的传统制造模式与商业模式,引入外部竞争者,或将改变传统产业格局。近年来,作为劳动密集型产业的船舶业正面临着劳动力成本上涨带来的压力。据江南造船公司党委副书记朱煜介绍,从2010年到去年,我国一线造船工人的月平均收入在3000元—4000元的基础上翻了一番,高级焊工、高级打磨工很难找,减少用工、提高效率、降低成本显得尤为紧迫。
中、日、韩三国造船相比,日本造船数字化技术应用整体水平最为先进,其次是韩国,中国与日本、韩国造船业差距很大。我国专家曾经以国际通用的68个要素、340项标准评估我国骨干船厂,发现我国与世界先进造船国家的综合水平有较大差距,尤其是精度控制技术、组织与管理体制、信息技术应用等方面差距更为明显。
造船企业数字化的关键在于信息集成。但由于缺乏一体化、集成化的设计系统,与生产进程联系不够紧密。虽然国内很多企业引进了一些集成程度较好的设计系统,但各自应用程度不一,仅仅解决了大部分“甩图板”的工作,其生产设计图纸中物量及制造信息没能充分及时反映,相关数据库有待建立与充实。
中国工程院院士、船舶先进制造技术专家组组长林忠钦表示,近10年来,中国国内骨干船厂每修正总吨工时平均消耗从44降到30(个别先进企业达到20左右),但与日本的10、韩国的15相比,差距明显。按照业内评估,造船业国际先进水平正在从工业3.0向4.0过渡,而中国国内,大部分船企处于2.0阶段。相对于汽车行业,造船业的自动化水平大为落后。中国造船业在完成订单、新增订单等方面远超日韩,但随着要素成本上升,中国的优势正在失去,如果不抓紧时间转型升级,过去的优势将改变。
江南造船公司董事长林鸥表示,造船业只有加快智能化转型,才能真正提升质量和效益,实现高质量发展。
专家表示,全面推进数字化,中国造船业需补三门课:要补的“第一课”是厂所协同,构建初步设计、详细设计、生产设计基于统一数据库的三维模型,在设计前端打通数据流。要补的“第二课”是厂内协同,让三维模型所包含的造船各专业数据直接传输到生产现场,不再通过二维出图。要补的“第三课”是船舶检验的协同,实现船厂内检与船级社检验的一致性,提升统一数据模型下检验的效率。
(来源:中国水运网 编辑: 国际船舶网)
声明:本网站所收集的部分公开资料来源于互联网,转载的目的在于传递更多信息及用于网络分享,并不代表本站赞同其观点和对其真实性负责,也不构成任何其他建议。本站部分作品是由网友自主投稿和发布、编辑整理上传,对此类作品本站仅提供交流平台,不为其版权负责。如果您发现网站上所用视频、图片、文字如涉及作品版权问题,请第一时间告知,我们将根据您提供的证明材料确认版权并按国家标准支付稿酬或立即删除内容,以保证您的权益!联系电话:010-58612588 或 Email:editor@mmsonline.com.cn。
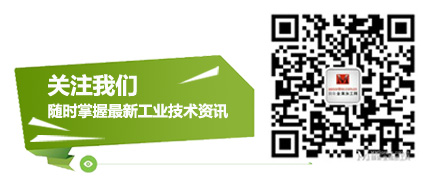
- 暂无反馈