航空企业持续改进,何去何从?
荆棘当道步难行
“后发优势”、拼搏的精神,让我国的航空工业技术在短短数十年的时间,缩短了与西方国家的差距,成为了世界上为数不多的4代机技术掌握者。解决了从无到有的问题,下一步都在瞄着如何从有到优,一方面是技术的成熟度提升,一方面是如何降低管理难度,实现大批量的生产和成本的降低,将技术更好的用于实战。
曾有专家说过,中美航空工业技术上差了10年,而管理上差了50年,虽然这种说法有些夸张,但是国内航空企业浪费严重、库存堆积、延期交付、生产前松后紧的情况确是普遍现象。无论集团公司,还是企业自身,都已经认识到了这个问题,试图摆脱原有依赖于技改、大干等传统手段的方式提升产能和交付能力的现状。5s、精益、六西格玛、平衡记分卡、架构、系统工程,无数的理论和方法都在或主动、或被动的引进了进来,我们取得了一些成果,也面临很多挑战。
面对内外部压力,在持续不断的梳理、优化、改善中,很多企业遇到了这样那样的困惑。例如,方法工具这么多,如何筛选称心如意的法宝呢?有没有一招制敌的方法工具?推进了这么多的方法工具,为何成效不大?为什么管理的变革这么困难?面对着一步一坎的现状,我们在推进改善的过程中应该何去何从呢?
需求为先依实情
我国航空工业经过了60年的发展,研究所、主机厂、配套厂、供应商全国遍布,不计其数。由于起步不同、产品特点不同,各企业的发展水平也不尽相同,一些企业认识起步较早,加上软硬件、政策条件的支持,早一步走上了以管理支撑技术,以技术带动管理的良性循环;而一些企业起步较晚,或一些条件的不具备,仍然以较为传统的方式运行。有些企业的部分车间已经实现了数字化的初步建设,逐步的在深度数字化,甚至是向智能化上发展,而有些企业则停留在1.0-2.0之间,考虑着如何将作业标准化、流程固化。因此说,不同企业,甚至不同车间,面对的问题是不同的。
任何理论、套路都不是绝对的,需要有一定的宏微观背景作为前提。不同现状下的企业,需要依据自身情况将好的理念实践,实现本地化、标准化,而不是直接复制粘贴,企业需要抱着怀疑的态度看待事情,不要试图用固有的方法解决每一个问题,尤其是新的问题。以现在比较流行的工业4.0、智能制造的研究和实践为例,其本身就是一个不成熟的课题,没有绝对的对与错,也没有太多的案例可以完全复制。如果一个企业,当前状态下没有ERP系统,没有MES系统,仍需要大量人力进行操作、统计等作业,那更应该解决的是如何将系统流程梳理、固化并验证,让工作合理化、简单化、精准化,逐步摆脱人为的干预,为信息化上马奠定基础,而不是短时间内硬性的对标标杆企业去减少岗位;如果当前状态下,大量的操作依然依赖于工人的经验,工艺人员不了解现场,过程中存在着巨大的波动,那更多的任务应该是建立标准化的工艺、标准作业指导书、建立程序/刀具库、建立产品病历本等,而不是去追求零库存,更不用提喊出短时间内建设智能化车间的口号,水中捞月。
想要解决什么问题是核心,继而才是什么时间解决、如何解决、谁来解决等问题,一些目标和口号很完美,但不一定适应于企业当前的状态。一言以蔽之,结合未来发展方向的基于当前SQCDP等关键能力提升的实际需求,是驱动企业管理创新、持续改进的第一驱动力。
咬定青山不放松
精益、六西格玛、TQM、平衡记分卡、成熟度、架构等等,这些方法无论是从宏观理论层面,还是从微观技术方法层面,都是成熟模型,也有成功的案例,但最终要的是两个字——坚持。
丰田1937年提出JIT的概念,直到1950年大野耐一参观美国工厂,才由超市的补货,启发出看板生产的信息传递模式,而直到70年代的全球危机,才逐渐显示出丰田模式的威力。丰田花了40年的时间,由百废待兴,发展壮大到一个全球化的标杆公司。
1981年摩托罗拉喊出5年内有10倍的质量改善,1987年才总结方法,创立了六西格玛管理,继而在次年获得波多里奇国家质量奖。
在需求明确后,所有的理论都是方法、工具,解决的更多的是如何做、如何做到的更有效率、更全面的问题。从某种意义上来说,科学管理、精益、六西格玛、德鲁克、稻和盛夫、TOC、TQM、零缺陷等等经典理论,并没有特别严格的界面,各自互相支撑,互相启发,都是为了实现企业目标的服务工具。在江湖中流行着一句话——会一万招,不如把一招练一万遍,在目标需求牵引下,认定了一种方法,即需要举全企业之力沿着这条路坚定的走下去,在探索中摸索和应用,披荆斩棘,不断转化成为自身的运营管理体系,同时也能够培养一批相关管理、技术人才,若干年后,再不行的企业也会在某些领域有所成就。
高层支持稳如钟
管理方面的改进,更多的是改变大家固有的观念,依托于人的意识转化,单靠一两个点的质变无法解决实际问题,某种程度上来说比技术的改进难度更大。因此,领导的支持和坚定就更为重要。
在个别领导心中,批准了某些方案、活动,或者说没有否定掉所有的活动,就是最大的支持,但对于持续改进这样的一场变革来说是远远不够的。高层领导不仅要有政策的支持,让听见炮火的人发号指令,更需要亲自参与到改善活动的团队中来,甚至作为实施者身体力行的加入到改善活动当中,努力让自己成为听见炮火的人。
全员参与共转型
多年以来,很多企业一直处于生产放权给基层单位/员工,而指挥、考核抓在顶层人手上的矛盾之中,在很多企业改善、改革的过程中,也纠结于究竟是精英驱动还是全员驱动的模式。实际上,在航空行业60年发展模式的大背景下,中基层人才在多年的实践中积累了无穷无尽的想法和经验,需要企业发挥精英式的引领性作用,将基层人才的知识经验进行整合,更好的服务于企业的发展需求和目标。但是实践中,很多企业所做的改善提案、班组建设等全员参与活动,缺少相应的目标引导,缺少公平、透明的判定标准和鼓励机制,更缺少高层的大力支持,全员参与仅停留在了责任和义务层面,没有与实际工作真正结合。比如,喷漆作业是否真正的为员工职业健康着想,做了作业空间隔离?过重的搬运,是否提供了匹配的省力工装器具?精细作业的座椅高度、角度是否合适?如果没有站在员工的角度,忽略一些小问题的解决,让大家觉得是负担,与岗位内容相脱节,那么相应的,企业改善,则成为了员工口中“他们的改善”。
不积跬步莫谈行
我国的航空工业事业发展多年,在这个由快催动到由质催动的转型期,遗留的很多传统方法,暴露出了很多的问题。比如,如前文讲到,有些企业多年发展依赖的是在某些岗位上的能人,而非公司的公开化的合理制度和规范,随着人员的退休、信息量的增大,逐步显示出了不适应性。因此,需要花费大量的精力回过头来搞好基础能力建设,比如生产/采购基础数据的收集、基础管理责任的划分、计划的投产原则、产品配套表/定额正确性的核对,甚至是库房的账物一致等。很多人不屑于做这些基础性的工作,首先见效慢,短时间内很难见效果,属于前人栽树后人乘凉的工作,其次当前生产任务紧急,基础能力工作往往都排在了重要但不紧急的维度,大家更愿意关注于眼前,而非长远,最后大家已经习惯于这种模式,互相“帮衬”,不愿意暴露问题,出现问题后第一句话是以前是怎么解决的,秉承的原则是你好我好大家好,法不责众。
中国有一句俗话,叫好饭不怕晚。精益里面有带人字旁的自働化的概念,都是为了及时发现问题,无论多小,都要停下来问5个why,直到确保问题不再发生,绝对不让一个马掌钉的脱落导致一场战争输掉的事情发生。适时地停下来是必要的,需要将那些临时性措施遮掩过去的问题适时暴露出来,系统性的总结,从一点一滴做起,尤其是那些看起来不显眼的一些小事,走好每一步——停是为了不停,慢是为了更快。
总而言之,企业的持续改进是一个大议题,需要各方努力,也需要系统性的思考,处理好未来与现状关系的发展方向问题,处理好参与者的心态问题,更要处理好切入点的问题。纸上得来终觉浅,绝知此事要躬行,我国的航空行业有着自己的特点,面对着独特的国情,无论是管理,还是技术,我们在当前实践上无处可以抄袭,也无法抄袭,但也不能故步自封,裹足不前。事实证明,吸星大法和金钟罩铁布衫都不是良策,唯有借由北冥神功充分汲取各方精华,以易筋经加以凝练和落地,再用斗转星移催动出来,才能真正的为我国航空企业的持续改进提供动力。
声明:本网站所收集的部分公开资料来源于互联网,转载的目的在于传递更多信息及用于网络分享,并不代表本站赞同其观点和对其真实性负责,也不构成任何其他建议。本站部分作品是由网友自主投稿和发布、编辑整理上传,对此类作品本站仅提供交流平台,不为其版权负责。如果您发现网站上所用视频、图片、文字如涉及作品版权问题,请第一时间告知,我们将根据您提供的证明材料确认版权并按国家标准支付稿酬或立即删除内容,以保证您的权益!联系电话:010-58612588 或 Email:editor@mmsonline.com.cn。
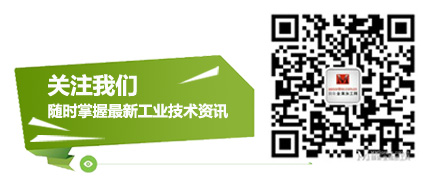
- 暂无反馈