航空航天装备电子元器件,国产化替代质量控制探讨
随着航空航天装备不断向高集成度、多功能、低功耗方向发展,迫切需要小型化、高性能、高效率、高可靠性的电子元器件。近年来,随着新品等项目的牵引和国内各元器件研制单位的技术攻关,国产电子元器件的性能水平取得了长足发展,部分国产电子元器件的性能已接近或达到了国际先进水平;但大规模集成电路、大功率器件、光电器件等元器件仍有部分依赖进口。
我国是电子元器件的生产大国,同时也是应用大国。以集成电路为例,2011年我国的需求量约占全球需求量的50.3%到2013年已增加到约54%。使用进口电子元器件不仅会在信息安全、质量控制等方面存在隐患,同时因器件禁运、停产导致的生产保障困难等问题也已经严重制约了我国航空航天装备的发展。
元器件国产化的必要性和意义
电子元器件是航空航天装备的基本单元,电子元器件的可靠性是保证航空航天装备可靠性的基础。由于功能、性能、质量、研制进度等因素,航空航天装备选用了部分进口电子元器件。当前进口电子元器件在航空航天装备中的使用存在以下问题。
1保障困难
随着新工艺、新技术的发展,电子元器件更新换代周期缩短。以集成电路为例,按照摩尔定律,每18个月其尺寸缩小一半,而集成度提升一倍。由于元器件的升级换代,以及国外厂商合并重组等原因导致的元器件停产,给很多已服役和仍在生产的航空航天装备的维护和生产带来了很大困难。
同时,以美国为首的西方国家形成联盟,长期对我国实行严格的出口限制政策。以美国为例,制定了严格的政策和相关措施限制高新技术及产品出口。美国商务部制定了商品管制清单(CommerceControlList,CCL),严禁将清单内的电子元器件出口到相关国家和地区。部分电子元器件的禁运也给我国高性能航空航天装备的研制和生产造成了一定影响。
2安全隐患
由于西方国家的技术先进性和国家间利益冲突,进口电子元器件可能会在设计、制造、封装、测试等环节被人为植入后门,如IP核可能被嵌入后门、掩膜制版及高端封装也可植入后门。这些后门可窃取我国装备的数据甚至摧毁设备,并可能进一步通过网络传播病毒和木马,严重影响我国的信息安全。2008年,美国国家安全局的一台发电机控制系统受到攻击后造成物理损坏。2010年,德国发现首个专门针对工业控制系统芯片的破坏性病毒。可见,在国防和信息安全建设中如果不能实现电子元器件的自主可控,则会始终处于受制于人、被动挨打的局面。
3质量风险
由于各种客观因素,航空航天装备使用了部分工业级元器件,这些工业级元器件大多通过代理商购买,无法获取相关的质量证明文件,个别已停产元器件甚至是翻新件。同时,部分大规模集成电路国内也无相应的测试手段。因此,部分进口电子元器件的性能参数、可靠性水平等往往只能随设备进行测试,无法预先开展检测和筛选工作,导致在设备使用过程中可能存在参数异常、早期失效等情况。进口电子元器件存在的质量风险已严重影响了航空航天装备的研制、生产和质量保证。
在进口元器件形势日益严峻的今天,元器件的国产化控制显得尤为重要。2006和2011年,我国分别颁布了相关要求和管理办法,对进口元器件的使用提出了规格比和数量比的量化指标要求,贯彻了总装关于加强武器装备使用进口电子元器件管理,从严控制、量化考核的指示精神。
元器件国产化替代中的问题
随着国际斗争的复杂化,航空航天装备关键电子元器件形势日益严峻。航空航天装备使用进口电子元器件保障困难,在安全隐患、质量风险等方面存在诸多问题。因此,大力推进进口电子元器件的国产化替代,已经成为一项构筑国家信息安全、保卫国家独立外交能力的紧迫而艰巨的任务。近年来,我国已在元器件国产化替代方面加大投入并取得了很大进展,但由于各单位在元器件国产化替代方面执行力度不一,元器件国产化替代仍存在一些问题。
1缺乏指导性文件
由于顶层管理文件不完善,目前国内尚无指导性文件规范国产新研电子元器件的研制、生产、鉴定和应用验证等工作,无法对元器件国产化替代工作进行有效的控制和监督。同时,部分装备研制单位虽然自行制定了单位内部的元器件国产化替代制度,但由于设计、工艺、加工等因素,国产化替代验证只能结合实际的模块、整机统筹开展,难以全面验证元器件的性能。
2参数体系不完整,测试覆盖不全
我国电子元器件生产起步晚,早期主要以仿制进口电子元器件为主。受各种客观条件和进口电子元器件知识产权保护的限制,仿制元器件无法保证设计、材料、工艺与进口元器件完全一致,且由于参数体系不完整、性能指标测试覆盖不全,测试合格的元器件仍然可能存在未被激发的缺陷。如某国产可编程逻辑器件(CAL)只能在某些特定的电路中做开关,而无法进行时序管理。
3工艺设计缺陷
为满足小型化需求,航空航天装备选择了部分进口表贴电子元器件。由于管壳工艺差异等原因,对应的国产化替代元器件可能存在封装无法完全兼容的问题。同时,考虑到研制进度和技术风险,整机单位多选用原位替代的国产化方案,且应用验证试验多为性能、工艺和环境适应性验证,难以暴露因管脚或工艺不匹配导致的问题。如某国产A/D转换器,管脚间距与进口产品存在微小差异,封装不完全兼容,在长期使用后会出现脱焊。
4缺少批量交付应用经历
军品的特点是多品种、小批量,且很多电子元器件是针对特定装备定制,导致国产新研电子元器件用量较少,元器件研制单位缺少批量交付应用经历。在元器件设计中存在的缺陷无法充分暴露,容易出现技术状态不稳定的问题,可能会存在不同单位或不同设备使用时,技术状态不稳定甚至失效的现象。
同时,除宇航元器件外,国内电子元器件缺少完善的产品批次内一致性、批次间一致性等产品生产一致性相关的评价方法。元器件研制单位缺少精细化评价元器件质量水平的方法,部分元器件在首次验证和首批应用时满足使用要求,而后续批量交付时,个别批次无法达到使用要求。
元器件国产化替代质量控制建议
1制定顶层规章制度
制定基于过程管理的元器件国产化替代质量控制细则,规范元器件的全寿命周期管理,使元器件研制、生产、鉴定、应用验证、处置及反馈过程透明、可视,确保元器件国产化有法可依,有据可循,有效保证国产化元器件的批次一致性、验证充分性和使用可靠性。
2加强用研双方技术沟通
为避免国产新研元器件研而不用所导致上机率低的问题,整机单位和元器件研制单位应加强交流,对元器件的技术需求、工艺、环境适应性等要求进行充分沟通。整机单位可结合以往类似元器件的使用经验,协助元器件研制单位改进提升。元器件研制单位应开展与进口元器件的全参数对比分析和验证,包括性能指标、外围电路匹配、环境适应性等,确保国产化元器件的性能水平能够与进口元器件全面相同,充分满足整机单位的使用需求。如电源模块,除了满足功率要求外,还应开展拉偏情况下的带载能力、纹波等的验证。
同时,整机单位应优化设计,通过系统的解决方案弥补国产化产品的不足,使系统的整体能力达到国外同类产品的水平。同时可加强微系统集成技术研究,弥补因国产化带来的重量、功耗增加等问题。如结合航空航天装备特点,根据系统处理架构、处理算法等开发专用处理芯片,减少对FPGA,PowerPC,DSP等高端芯片的依赖。
3加强设计和试验验证
对于封装与进口元器件有差异的元器件,元器件研制单位应结合整机单位的使用需求,提高设计能力,充分利用热仿真、力学仿真等仿真设计手段,尽可能确保优化封装后的国产化元器件能够满足整机的可靠性要求。如某国产元器件在设计研制阶段,开展了热仿真、应力仿真,优化结构设计,增加加固措施,经温度循环验证,成功解决了多次温度循环后元器件的脱焊问题。
4开展可靠性强化试验和补充验证
为避免部分缺陷无法在应用验证中充分暴露的问题,可针对重要元器件,如大规模集成电路、大功率器件等开展可靠性强化试验,确定元器件的使用边界,针对暴露的问题展开分析,制定相应的改进措施。
对于已有其他整机单位使用过的国产化元器件,整机单位可结合工程实际情况开展补充验证,重点针对匹配性问题或指标无法体现的特性进行验证,确保国产化元器件能够满足整机单位的需求。如涉及到工艺或环境适应性的改进,元器件研制单位可推广到其他整机单位.有利于提升装备质量。
5加强元器件研制单位的质量控制
整机单位应向元器件研制单位及时传递顶层质量要求,并对元器件研制单位的设计和制造过程进行审查和监控,明确关键参数的质量一致性要求。元器件研制单位应加强元器件、原材料的选用控制,制定相应的质量控制细则,控制元器件的设计、生产和检验过程,尤其要加强对特殊过程、关键工艺技术的控制,以确保元器件批次内、批次间的质量一致性。
6建设国产元器件的信息化系统
为了更有效地推广国产元器件的应用,在国家层面建设国产元器件的信息化系统。国产元器件信息化系统可定期对元器件相关信息,如研制背景、性能指标、研制情况、鉴定情况、验证情况、整机使用情况等进行更新和维护,提高国产化替代元器件的选用效率,让更多的整机单位了解国产元器件的信息。整机单位也可将验证和使用过程的问题共享到信息系统中,为国产化替代验证提供有力的支撑,其他同行也可避免再走弯路,提高国产元器件的设计和使用质量。
声明:本网站所收集的部分公开资料来源于互联网,转载的目的在于传递更多信息及用于网络分享,并不代表本站赞同其观点和对其真实性负责,也不构成任何其他建议。本站部分作品是由网友自主投稿和发布、编辑整理上传,对此类作品本站仅提供交流平台,不为其版权负责。如果您发现网站上所用视频、图片、文字如涉及作品版权问题,请第一时间告知,我们将根据您提供的证明材料确认版权并按国家标准支付稿酬或立即删除内容,以保证您的权益!联系电话:010-58612588 或 Email:editor@mmsonline.com.cn。
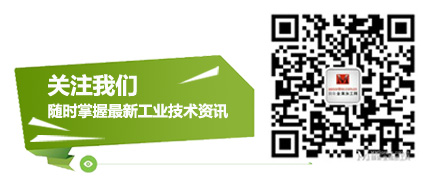
- 暂无反馈