对标德国,中国模具企业有哪些不足?
德国的工业水平是全世界都有目共睹的,其模具制造水平同样也是处于世界先进水平。对于中国模具行业来说,如果能对德国顶尖模具企业进行深度的研究,并对标自身做深入的分析,必将会为行业的发展带来全新的灵感。
在中国模具工业协会携手WBA(德国弗劳恩霍夫应用研究亚琛模具研究院)合作开展的一项模具企业基准分析项目中,WBA的专家通过对中国模协遴选的10家模具企业开展基准分析问卷调查及现场调研,发布了中国模具企业对标德国基准分析整体评价的报告,介绍了中国模具企业与德国顶尖模具企业的对标结果,分析了中国模具企业的优势以及与德国模具企业相比存在的差距,其中比较有代表性的几个方面包括:时效性、质量、生产率、加工能力和自动化水平。
一、中国模具行业相对德国模具行业的优势
中国模具行业在劳动力成本和设备规模方面的优势非常明显。中国模具企业的员工平均每天比德国模具企业的员工多工作2个多小时,而且中国模具企业的员工每小时的工资要比德国低得多。从下图中可以看出,设计领域的小时费率德国是中国的4倍,中国模具行业在加工和试模领域同样具有这种优势。
员工每天工作时间比较
不同领域小时费率比较
如下图所示,除了人力成本较低外,这种竞争优势也是由中国模具企业庞大的设备规模所支撑的,可以实现较短的交货期。尽管设备已经具备了相当的规模,但中国企业仍在不断地投资于新设备,中国的设备平均使用时间比德国少2-3年,并且许多中国模具企业在精铣的关键技术上进行了战略性投资。因此,中国模具企业由于相对较低的时薪和大型现代化的设备园区而具有竞争优势。
设备情况的比较
二、几个关键领域落后于德国最佳模具企业
KPI的对比分析表明,中国模具企业在一些关键领域落后于德国最佳模具企业。从下图可以看出:时效性和质量上的差距,中国模具企业出现延时交货和模具存在质量问题的情况较多。在客户二次检查模具后,中国模具企业生产的模具中仍有21%没有达到客户的质量标准,而德国最好的10家模具企业生产的模具中这种情况发生的概率只有9%。
时效性和模具质量的比较
此外,如下图所示的有助于提高效率的自动化手段在中国模具企业中使用得很少,只有一半的中国模具企业使用了工件堆垛系统。在我们调研的中国公司里还没有一家在模具制造过程中使用机器人,而在德国最佳模具企业中,制造过程中使用机器人几乎是一种标准化配备。
自动化水平的比较
三、中国模具行业需要关注的四个具体行动领域
正如我们已经看到的,中国模具企业在时效性方面存在不足,考虑到中国员工每年比德国员工多工作380h,规划效率有限的原因就变得很明显了。坦率而言,如果中国员工减少加班时间,那么时效性会降低到一个可怕的程度,因此有效的规划是中国模具行业需要关注的重点领域之一。
(1)规划
为了提高时效性,项目和零部件都应该详细规划,在模具项目级别和每个单独零部件的级别上进行规划是实现时效性的关键。因此,大多数成功的德国模具企业采用规划系统,通过系统化方法和规划软件提高流程清晰度。规划系统能够详细规划所有流程步骤并提供产能概况,以使相关人员掌握对每一项技术的需求和相应的可用产能。为了提高时效性,规划系统中还应有进一步的算法来寻求生产作业的最优顺序。基于平板或智能手机应用,管理层可以随时跟踪关键项目的状态。
采用规划系统实现有效的规划
此外,应该通过标准化的流程来提高交货时间的可预测性。提高时效性的第三个工具是定期的车间会议,首先在每个小组中讨论问题并直接确定解决方案。不能直接解决的问题,在所有部门领导参加的每日短会上讨论。
(2)自动化
第二个关键行动领域是自动化,自动化解决方案有助于提高设备利用率。观察图9中制造成本在整个流程链中所占的比例,就很容易看出德国模具企业采用自动化解决方案的益处。在德国,模具的成本只有34%用于制造,而中国模具企业制造环节在成本中分摊的比例为52%。主要原因是德国模具企业在铣削和电火花加工方面高度自动化。自动化是德国模具企业在过去10年里取得很大进步的关键领域之一。
制造在整个流程链中分摊成本的比较
不同加工设备自动化水平的比较
因此,建议中国模具企业在自动化领域加大投入。企业可以根据实际生产需要,引入大型自动化生产线,也可以考虑引入自动生产单元和自动夹紧系统,以显著降低制造成本。自动化生产线可以集成各种不同类型的加工设备、测量装置以及工件转移、清洗、储存装置等。自动化生产线上的所有设备都是相互连接在一起的,编程完成后,工人只需要将工件放入工件堆垛系统,机器人在不同加工设备和测量设备之间转移工件,最后工人只需要在所有步骤完成后从仓库系统中收集工件。这种自动化系统可以显著减少不同过程步骤之间的等待时间,使生产区域内没有任何工人在场的所谓“幽灵班”成为可能。
自动化生产单元
线切割机床的自动夹紧系统
(3)数字化和可视化
对许多中国模具企业来说,质量仍然是一个挑战。为了减少质量错误,重要的是在订单完成过程的早期识别错误。从下图中可以看出,中国模具企业有两成左右的错误是在流程链的晚期发现的,如在试模时,这会大幅增加纠正错误所需的成本和时间。
质量错误发现早晚的比较
早期发现并纠正质量错误的关键是对质量问题的数字化跟踪以及在数字化车间看板上实现可视化,此外,也可以考虑帮助识别几何偏差的应用程序。大多数德国模具企业都意识到业务数据可视化的积极影响,因此,所有关于质量和改进措施的关键指标都在数字化车间看板上跟踪显示。下图是WBA采用的可视化车间看板的示例,业务数据在模具车间的所有区域都有可视化的展示,并且设置预定义参数以持续监控制造过程。任何指标有显著偏差时,则会通知管理层。
数字化车间看板
支持数字化错误跟踪
WBA采用的可视化车间看板
(4)刀具管理
为了进一步提高加工效率,结构清晰的刀具管理是实现高效率制造的关键因素。刀具管理不合理导致了中国模具企业在加工过程中需要更多的准备时间。通过集中管理刀具数据和专注于一定数量的标准刀具,可以有效提高生产效率。具体可以采用数据矩阵码(DMC)对刀具进行标记,并采用中央刀具管理系统登记、管理和调用刀具数据。这样,中央刀具管理系统可以记录刀具磨损情况,并在编程和加工过程中调用刀具的实际数据,提高加工精度。同时,结构化的刀具管理可以节省时间和空间,而刀具的标准化可以减少工件准备中的错误,便于更加清晰地排列刀具及其配件。
准备时间与加工时间的比较
刀具数据的中央收集
专注于标准刀具
综上所述,中国的模具制造基础非常好,中国模具企业可以通过规划、自动化、数字化和刀具管理这四个具体行动领域来提高时效性、生产效率、产品质量和工艺质量,缩小与德国最佳模具企业之间的差距,进而提高国际竞争力。
(前沿数控技术)
声明:本网站所收集的部分公开资料来源于互联网,转载的目的在于传递更多信息及用于网络分享,并不代表本站赞同其观点和对其真实性负责,也不构成任何其他建议。本站部分作品是由网友自主投稿和发布、编辑整理上传,对此类作品本站仅提供交流平台,不为其版权负责。如果您发现网站上所用视频、图片、文字如涉及作品版权问题,请第一时间告知,我们将根据您提供的证明材料确认版权并按国家标准支付稿酬或立即删除内容,以保证您的权益!联系电话:010-58612588 或 Email:editor@mmsonline.com.cn。
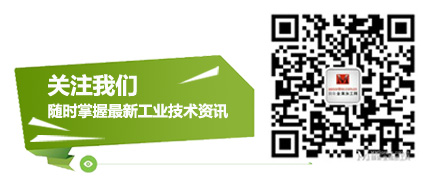
- 暂无反馈