对飞机大型复杂结构件数控加工过程关键技术的研究
在我国飞机发展过程中,飞机结构件大型化、整体化、薄壁化和精确化等要求十分突出,尺寸增加但公差成倍压缩、壁厚减小但加强筋缘条增高、尺寸精度提高的同时增加了重量容差指标、单个结构件多特征集成导致形位精度严格,长寿命轻量化要求加工表面粗糙度普遍提高1~2个等级,由于所有飞机结构件100%进行数控加工,加工质量与加工效率的矛盾突出。
飞机研制生产过程中,数控加工面临三大难题——加工损伤、加工失稳和加工变形。成飞与北航自2007年起,在航空工业多个项目支持下,“十年磨一剑”,成功地解决了上述难题。
加工损伤、失稳和变形的本质原因,来源于数控加工过程“机床-刀具-工件”工艺系统动力学交互作用。传统的基于经验以单因素为主的理论和方法,已不能解决上述难题。
总体思路是针对问题,通过建模,分析“过载→损伤”、“颤振→失稳”和“应力→变形”的力学本质,从理论预测进行“防”和工艺装备进行“消”两方面入手,防消结合,软硬兼施,突破如下关键技术:
1)难加工材料及复杂结构加工切削力/热载荷均衡预适调控加工技术;
2)大型薄壁结构件稳定高速铣削加工技术;
3)大型复杂结构件加工全过程残余应力及加工变形预测与控制技术。
成飞与北航合作自主开发出了:数控铣削时变切削力预测及参数优化软件和微量润滑装置、数控切削动力学仿真优化软件和被动阻尼吸振装置、加工变形仿真软件和“热-振”复合应力均化装置等,应用于飞机大型复杂结构件数控加工过程,解决加工失稳、损伤和变形的难题。
关键技术研究及应用:
1.难加工材料切削力/热载荷均衡预适调控加工技术
加工损伤问题,其本质是数控加工过程切削力/热载荷大而且变化剧烈,引起的对刀具、工件冲击产生机械损伤和表面烧伤,在难加工材料数控加工中尤为突出。
传统避免和减少加工损伤的途径是大幅减小切削用量和大量使用切削液,显著牺牲切削效率。面对新的加工需求,在动态切削力建模基础上,考虑工艺系统多重约束,提出一种变螺旋曲线径向分层局域循环铣削方式,进行刀轨优化和切削参数预适调整,实现切削力均衡,对切削力过载和冲击现象进行“防”。
已开发了飞机结构件数控铣削时变切削力预测及参数优化软件,形成了应用规范;开发了三种准干式切削精准润滑装置。在TC4钛合金超大型整体框上的筋条、缘条、内外形等复杂结构进行加工测试,实现稳定切削速度150m/min以上,关重部位表面粗糙度达到Ra1.6~Ra0.8。
2.大型薄壁构件稳定高速铣削加工技术
加工失稳问题,本质是薄壁和高筋等结构导致工艺系统动力学特性恶化,出现切削颤振。面对新的加工需求,以工艺系统相互作用分析为基础,建立“机床-刀具-工件”动力学模型,通过测试和辨识,仿真计算出颤振稳定域曲线,在工艺系统多约束条件下,给出优化切削参数,实现无颤振的高速高效切削,实现对加工失稳的“防”。
基于颤振模型,开发了多种阻尼消振装置,安装在被加工结构件或机床的相应部位,抑制或减弱出现的振动,实现加工振动的“消”。
自主开发了辨识测试硬件和X-Cut/e-Cutting软件、阻尼消振装置,在大量试验基础上建立了工艺数据库。飞机铝合金中机身框的实例测试表明:
实现了弱刚性缘条的无颤振稳定加工;
材料去除率提升了1倍以上;
关重部位表面粗糙度达到Ra0.8μm。
3.加工全过程残余应力及加工变形预测与控制技术
大型复杂构件加工变形,主要来源于:1)毛坯中的残余应力在切削加工过程中不断释放和重新分布产生的变形;2)在切削力作用下刀具和工件(包括装夹)之间产生的相对变形。
因此,飞机结构件中残余应力的形成及弹性让刀变形的演化规律,是预测和控制加工变形的核心。针对飞机大型复杂构件,开展从毛坯到结构件成品全过程残余应力仿真分析,预测残余应力分布状态和加工变形规律,通过优化工艺及参数,控制毛坯残余应力状态,实现对后续数控加工变形的预“防”;研制了“热-振”复合残余应力均化装置,通过对工件施加“点穴”式热和振动复合作用,进行残余应力均化以“消”除工件变形。
中国机械工业联合会在成都组织召开了成果鉴定会,鉴定委员会认为:“该项目成果整体技术达到国际先进水平,在切削力/热载荷均衡预适调控加工技术方面达到国际领先水平”。项目的成果也得到国内外同行知名专家的积极评价。
项目成果显著提高了我国飞机制造技术水平,已推广应用于一批飞机制造企业,还推广应用到航天、航空发动机、兵器和机床等行业,对于制造业科技进步和提高竞争力具有重要作用和意义。
声明:本网站所收集的部分公开资料来源于互联网,转载的目的在于传递更多信息及用于网络分享,并不代表本站赞同其观点和对其真实性负责,也不构成任何其他建议。本站部分作品是由网友自主投稿和发布、编辑整理上传,对此类作品本站仅提供交流平台,不为其版权负责。如果您发现网站上所用视频、图片、文字如涉及作品版权问题,请第一时间告知,我们将根据您提供的证明材料确认版权并按国家标准支付稿酬或立即删除内容,以保证您的权益!联系电话:010-58612588 或 Email:editor@mmsonline.com.cn。
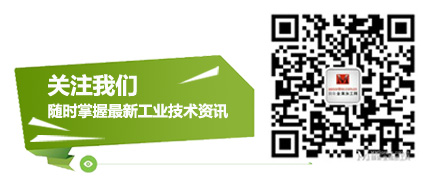
- 暂无反馈