电机企业如何把握好车用市场发展趋势争取技术上的反超?
电机技术并没有我们想象的那么简单,车用永磁同步电机国内厂商相对国外落后5年左右,差距在于设计理念、原材料和设备、以及需要避开国外专利(目前国厂商专利少说4000多份)。另外在材料损耗,工艺,关键参数的控制方面与国外都有差距,产品更新速度也较慢。未来电机产品的发展趋势是更高输出密度、更宽调速范围、更低制造成本、更易集成(目前最有意义的集成是电机,变速器和控制器集合在一起)。未来在技术与客户响应上能够做到突破的公司有望胜出。
一、电机磁场及工作原理
电磁力原理:电磁力指的是通电导线在磁场里受到电磁力的作用,电磁力是异性相吸,同性相斥的。这里的异性相吸肯定是对的,但是同性相斥这里的同性指的不是极性相同,而是指电磁磁位性质相同。目前的电机产生力主要靠吸力作用。
发电原理:导体在发电的磁场里被感应出来电压,使得电路形成回路产生电流。
永磁同步电机工作原理:定子通交流电后产生旋转磁场,该旋转磁场吸引转子磁场,是转子跟随定子磁场旋转。
这里需要注意的是车上使用的电机大部分都是永磁同步电机,而其中绝大部分都是内嵌式同步电机,主要原因是内嵌式同步电机很好的利用了磁阻扭矩。磁阻扭矩对电机系统的影响在于:
在相同的电机反电势系统下,实现相同的扭矩可以减小释放的电流,从而有利于提高电机低速大扭矩情况下的效率,还为降低控制器主要部件成本创造条件。
在相同的控制器硬件条件下,高磁阻扭矩电机比低磁阻扭矩电机具备更高的空载转速,有利于提高电机高速小扭矩的工作效率,改善电磁噪音,提高了电机系统的调速范围。
二、车用驱动电机的主要性能参数及解读
衡量车用驱动电机的主要性能主要看下面几个数据:
1.满功率输出的最低工作电压:(额定电压不重要)这里需要注意的是车用电机用的都是交流电,但是厂商一般给的数据都是直流电数据需要转换成交流值,直流电转换成交流电时要经过控制器,这一步骤需要消耗一部分电压。
2.最大工作相电流:不能用主机厂给的数据,要结合控制器的IGBT能力。
3.峰值扭矩:对商用车客户可能的是堵转扭矩值。
4.峰值功率:应该明确是什么转速下的峰值功率。
5.额定功率/扭矩:长时间允许运行的工作点叫额定功率,但是对整车厂来说合理额定功率应当是持续的扭矩和功率,比如车高速时的电机运转功率可以当作额定,应该考虑缝制转速下的额定功率。
6.最高工作转速:最高工作转速包括了最高工作转速下的功率,最高转速下的反电势,最高转速下机械应力(是不是能在高速下稳定运行)。
7.NVH:低齿槽扭矩和负数反电势谱波。
8.效率:这里需要关注的数据是电机最常用的效率,同时还要注意高效区要合理匹配客户的需求。
三、发展趋势
1.更高输出密度-(拳头那么大最好输出200kw)
有没有什么材料,成本低廉还能效率高
2.更宽调速范围(0-18000转,甚至0-20000转)
有没有新原理能把成本降下来
3.更低制造成本
新工艺(例如有没有什么好的绝缘材料能把耐温提高)
4.更易集成
新应用(目前最有意义的集成是电机,变速器和控制器集合在一起)
四、IPMSM磁路结构
1.常用的磁路结构
2.车用永磁同步电机磁路结构发展趋势
趋势主要概括为:高功率密度,低材料损耗,高速旋转,控制灵活。具体表现为:
适应高磁阻扭矩性能和低磁钢消耗
满足电机和变速箱一体化需求,追求转子尺寸和薄型设计
新型磁钢工艺或高性能硅钢片材料的发展
迎合创新控制策略对电机磁路参数的特殊需求变革
五、永磁同步电机相关设计参数及取值
1.I,P,Z,n取值(电机设计最相关的参数)
a)极对数p
极对数越多,越有利于提高电机的扭矩密度和功率密度
在不考虑转子漏磁的情况下,电机的极对数越多,电枢对转子的电枢反应越弱。
考虑到实际工艺能力和定转子机械强度问题,过多的极对数,会导致漏极系数过大,缩匹配的电枢槽面积过小,反而不利于功率密度的提高
极对数决定了电机在一定转速下的工作频率,因此可以根据电机锁匹配控制器开关部件的能力和电机锁工作到最高转速来获得电机允许的最高极对数
优先级推荐:满足电机可控性-满足电机可制造性-取尽可能多的磁极。
b)指数Z(一般情况下,必须先决定p再决定Z)
(概念:每组每相槽数Q=Z/(3*2*P),Q为整数时被称作整数槽绕组,否则称之为分数槽绕组)
车用大功率电机若是选择了集中绕组,那么电机的Q=0.5,那么槽数Z=3*P,也有少数小功率电机8极9槽或者10极12槽。
Q值越大,电机的反电势谱波越小,电机齿槽扭矩和力矩波动幅度越小,但根据经验Q>3后,对谱波的改善效果可以忽略。
由于驱动电机的功率较大,电机单相串联匝数较少,那么很多时候需要选择合适的槽数Z,来保证电机匝数的合理
电机常用的Q值推荐为:Q=0.5;Q=1.5;Q=2;Q=2.5;Q=3(对于车用驱动电机Q取较大值时往往应用扁铜线绕组工艺。
C)匝数N
匝数增加,电机的反电势系数增加,相同电流下的扭矩增加
匝数增加,意味着导体的截面积减少,可能带来电枢热负荷过高的问题
改变电机的体积,就改变了电机的磁通面积,改变了磁路结构可以更改气隙磁密合极弧系数,为调整电机匝数创造了条件
2.主要尺寸确定
1)电枢外径取值
一般情况下,根据整车的尺寸需求,去除外壳厚度即得到定子铁芯外径,电机机壳的厚度随电机的外形尺寸和机壳工艺不同而不同,近年来越来越广泛应用的一体化水冷却机壳,其机壳的厚度建议在18至30mm不等
2)电枢内径取值
定义:定子外径尺寸确定后,才能确定电枢内径尺寸,即关键是设计电机的内外径比例值kd
影响:Kd值越大,电机电枢磁势影响力越小,但转子磁通量增大,转子磁势增强,易于提高电机的功率能力,但需要增大了电机的铜损,反之将减少电机的功率能力,但能给提高电机效率创造条件,Kd值同样影响了电枢槽尺寸与形状,Kd值越小,槽越深,电枢槽口越小,槽漏抗增加
3)电机定转子气隙选取
气隙越小越有利于提高电动机的性能,但电动噪音也喜欢过小的问题,过小的间隙要求过高的零部件的装配精度,也无法适应转子高速时的离心力变形,所以电机的该尺寸能做多小主要取决于相关的工艺水平和高速条件下转子的形变情况。
3.磁密取值
a)出力和磁密的关系磁密取值
电磁力:F=BIL
电磁扭矩:Te=BINLfeR=BJV
电机的扭矩密度取决于电机空气间隙内的负载磁密和定子内导体的电流密度
b)电机获得较高的磁密可以有两个途径:
磁力取高(提高磁场强度)
电流密度取高(提高物质材料的磁导率,目前技术来看比较困难)
C)空、负载磁密的取值问题
空载:在满足反电势大小的前提下,建议取较低的空载定子磁密,合理的转子磁密
峰值负载:
适当调节电机交直流电流分配比例,在基本不牺牲电机扭矩的条件下,缓解磁路饱和程度
定转子多为饱和状态,但应通过磁路优化减少电枢漏抗带来的磁路饱和
4.反电势取值
a)反电势对电机及控制器的影响
在电机的工作电流一定的条件下,电机的输出扭矩正比于电机的反电势。在相同的输出扭矩下,增大电机反电势可以降低电机的工作电流
电机在不弱磁工作时,在电机电压一定的条件下电机的工作转速于反电势成反比,对于控制同步电机来说,反电势的大小基本确定了电机峰值扭矩的拐点位置
最高反电势威胁到控制器主要元件(电容和IGBT)的安全,过高的反电势可能会导致器件损坏
b)反电势的取值
一般来说市场现有的薄膜电容可承受低于500v的反电势;对于300v左右的供电系统若定制器件,该值一般小于700v,现实中超过650v,不管工作是否,薄膜电容会被击穿,所以很多厂要求取值低于450v。
六、永磁同步电机的仿真手段
1.导致性能和实测数据偏差的主要问题有:
A.材料定义不完善
B.实际尺寸偏差
C.材料性能余量估计不足
D.模型等效带来的偏差
E.网络划分不合理带来的偏差
F.仿真数据处理不当
2.仿真条件的注意事项:
A.材料属性
B.铁损表受实际工艺影响的变化值
C.网格划分(很多软件是自动进行划分的)
D.力学求解器(MAXWELL力和虚功力的理解)
LD/LQ计算和判断
一般规律:Ld随电机弱磁升速和扭矩增加,数值基本不变。Lq随扭矩增加(或磁密饱和)而减小,随弱升速(磁密降低)而增大
电机进行FOC控制时,电机的交轴电流都是同时加载,在同一定转子冲片磁路下,交直轴的磁路是相关影响的。仿真求解和加载条件必须相同的。
七、永磁同步电机的设计输出参数
在永磁同步电机的设计时,以下数据是一定要算的:
反电势或空载磁链(随温度变化的很多数据)
短路电流(稳定值等于空载磁链/Ld)
最大相电流和最高工作电流频率(是否和控制器IGBT一致)
Ld/lq表(对应ID/Iq,两个要同时加)
负载特性(特别是峰值轴距,功率时直轴电流和短路电流的关系)
齿槽扭矩
0N.m最高转速下需要的最小相电流个磁密分布(非常重要,电动车上高速要深度弱磁的,所以这个数据越小,就会越节能,电池安装数量就少)
效率MAP
电流密度和热负载判断
槽满率
绕组端部尺寸
声明:本网站所收集的部分公开资料来源于互联网,转载的目的在于传递更多信息及用于网络分享,并不代表本站赞同其观点和对其真实性负责,也不构成任何其他建议。本站部分作品是由网友自主投稿和发布、编辑整理上传,对此类作品本站仅提供交流平台,不为其版权负责。如果您发现网站上所用视频、图片、文字如涉及作品版权问题,请第一时间告知,我们将根据您提供的证明材料确认版权并按国家标准支付稿酬或立即删除内容,以保证您的权益!联系电话:010-58612588 或 Email:editor@mmsonline.com.cn。
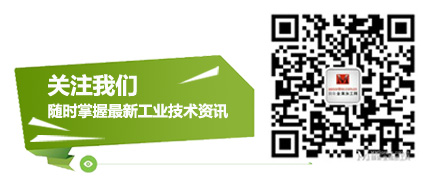
- 暂无反馈