钣金加工技术发展趋势——智能化
“工艺就是技术”“工欲善其事,必先利其器”。近半个多世纪以来,钣金加工技术的发展及钣金加工行业的崛起、振兴,进一步印证了这一事实。
现代钣金加工技术与传统钣金加工技术相比已有本质的飞跃。传统钣金加工技术是以手工技艺为基础;而现代钣金加工技术是以数控钣金加工设备为核心,配以齐备的工、模、夹具及辅助设备等,形成坚实的现代高新技术基础。从这个意义上讲,现代钣金行业是新兴行业,钣金加工工种是新生工种,现代钣金加工技术则是当代领先技术,并为促进整个制造业的发展发挥着巨大作用。
当今社会,在人们的生活中,可以说钣金加工产品无处不在,已被广泛用于航空、船舶、轨道交通、汽车、计算机机箱、通信机箱机柜、医疗器械、仪器仪表等领域。
随着技术的进步与社会的发展,人们对钣金加工产品的需求有增无减,这为钣金加工企业提供了商机。企业在转型升级的过程中,其焦点自然集中在技术上,特别是集中在关键技术的突破上。
早在1952年,美国麻省理工学院成功研制了世界第一台数控铣床,开创了数字控制技术用于机器制造的新纪元。我国,清华大学于1958年研制了中国第一台数控机床。至此,我国制造业步入了以数控技术为核心的新时代。进入20世纪60年代,世界第一台数控压力机问世,1960年美国人梅曼发明了激光器,1965年全球第一台CO2激光器在美国诞生。
现代中国钣金行业的发展始于20世纪80年代末到90年代初。2000年以后,数控技术在钣金加工业的应用与发展进入了高峰期。如果说,20世纪后半叶是数控技术进入钣金加工业的话,那么,到了21世纪,智能化必将在技术进步的进程中担当主角。
在钣金加工行业,智能化程度或水平主要应体现在如下几个方面:
1.智能制造装备
智能制造装备是具有感知、分析、推理、决策及控制功能的制造装备的统称,是先进制造技术、信息技术、计算机技术和智能技术在装备产品上的集成和融合,体现了制造业的智能化、数字化和网络化的发展要求。智能制造装备的水平已成为当今衡量一个国家工业化水平的重要标志。
2.智能柔性生产线
在智能技术的基础上建立柔性生产线是钣金加工生产的发展趋势。当前,由于国内钣金加工企业规模不大,产品多属多品种、小批量,对柔性生产线的需求尚不迫切。随着技术的进步和成熟,智能柔性生产线必将迎来高速发展期。
3.机器人
机器人是自动执行工作的机器装置。它既可以接受人的指挥,又可以运行预先编写的程序,也可以根据以人工智能技术制定的原则纲领行动。它的任务是协助或取代人的工作。
在钣金加工行业,已有用于工作条件较差的焊接、打磨等工艺的机器人,也有用于下料、折弯成形工艺的机器人。从总体上看,目前还处在试验与起步阶段,尚未达到推广应用的程度。其中,有成功应用的实例,也有投放市场的产品。机器人已被业内普遍关注。有些企业从设计、工艺到生产加工针对机器人进行研究,发现问题,加以分析,提出办法加以解决。
4.信息化管理
钣金加工技术的自动化、智能化发展趋势,必然促使钣金加工企业的管理变革。建立信息化管理体系势在必行。在信息化管理体系中,诸如物流管理系统、生产管理系统、工艺技术系统、质量管理系统、自动报价系统、成本管理系统、安全保障系统等均按预先策划的要求运行,并有效控制。
当前,在规模较大的钣金加工企业中都引进了ERP、PAL等信息管理体系。但使企业感到困惑的是,这些信息管理体系拥有很强的功能,而进入体系的有效信息量却很小,使信息管理体系远不能充分、有效应用;另外,对于以外接图样加工的企业来说,外来图样“五花八门”,不统一、不规范,不执行相关标准,随意“简化”,以至于将有用的信息也缺失了,使信息管理体系无法正确使用,甚至无法使用。为此,要求图样规范化、标准化的呼声越来越高。
信息化管理是现代钣金加工企业转型升级的重要标志之一。要提高信息化管理的有效性必须从根本上解决问题。我协会经过几年的调查研究,召开各专业的技术、管理研讨会,集思广益,得出如下共识:
(1)总体策划、顶层设计以企业标准体系为龙头,建立规范化的技术管理系统;以产品结构设计为重点,全面提升设计文件的水平和质量;以自动化、智能化为目标,深入工艺研究,固化工艺技术成果;以人才的引进、招聘、使用、培训为基础,提高企业的综合素质。
(2)理清主次、分步实施当务之急是解决产品的结构设计问题。首先是图样标准化、规范化;其次,应对各企业的结构设计师加强业务培训,提高结构设计师的业务技术水平及图样的质量和标准化水平。
(3)重视人才、提升素质不仅企业应重视人才,使用、培训人才,营造人才成长的良好环境和氛围;技术院校也应根据企业的需求,输送专业对口的员工,使人才源源不断地涌现,这是钣金加工行业兴旺发达的根本保证。
本文以钣金加工产品的制造工艺流程(粗略)为主线,扼要说明以数控技术、自动化生产为核心技术的钣金加工技术的现状和以智能化制造技术为主流的发展趋势。
另外,环境保护、生态平衡、绿色制造也是倍受关注的热门课题。其高新技术的应用、更新和发展也与产品制造技术同步进行,应引起行业重视。
声明:本网站所收集的部分公开资料来源于互联网,转载的目的在于传递更多信息及用于网络分享,并不代表本站赞同其观点和对其真实性负责,也不构成任何其他建议。本站部分作品是由网友自主投稿和发布、编辑整理上传,对此类作品本站仅提供交流平台,不为其版权负责。如果您发现网站上所用视频、图片、文字如涉及作品版权问题,请第一时间告知,我们将根据您提供的证明材料确认版权并按国家标准支付稿酬或立即删除内容,以保证您的权益!联系电话:010-58612588 或 Email:editor@mmsonline.com.cn。
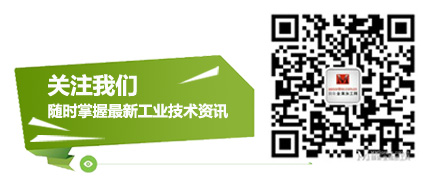
- 暂无反馈