凸轮轴磨削加工新方法:立式磨削
近年来国内汽车工业的发展迅速,对发动机及其零部件的性能、技术水平、质量和产量等方面均提出了许多新的要求,从技术上看,汽车工业的发展对内燃机及其零部件的质量和生产效率的要求越来越高。
凸轮轴是内燃机进、排气系统的关键零件之一,整个进、排气系统是由凸轮轴驱动。由于凸轮轴具有形状复杂、刚性差、加工精度要求高等特点,一直是汽车内燃机零部件制造的难点之一。而磨削是凸轮轴加工的关键工序之一,在加工工艺中处于重要地位。磨削的质量影响到整根凸轮轴乃至发动机的性能。
目前国内凸轮轴加工均采用单砂轮卧式磨削的方式进行精加工,但卧式磨削加工因磨床结构的限制,始终无法很好的消除砂轮对工件的作用力及重力带来的变形,极大的制约到凸轮轴各关重精度的提高。如何能避免细长杆类零件磨削时因产品自重和切削力导致的产品变形一直制约着细长杆类零件加工精度的提升,成为细长杆类零件加工中亟待突破技术瓶颈。
凸轮轴磨削的工艺特点
1、加工工艺性差
汽油机凸轮轴均属细长轴类零件,因为其结构细长,所以刚性差,在加工过程中易受到切削力、夹紧力及重力等外力作用,产生变形,使零件的加工精度降低。热扩散性能差,在切削热的作用下,会产生较大的线膨胀,而磨削加工时轴的两端为固定支撑,工件会因伸长而弯曲。磨削时容易产生弯曲变形,并产生磨削振动,影响加工零件的尺寸一致性和磨削表面质量,加工工艺性较差。
2、加工表面容易产生波纹
由于凸轮轴属细长轴类零件,且凸轮部位与圆柱面不同,其磨削余量大且不均匀,带来的是磨削加工中凸轮表面的受力变化大。变化的磨削力容易引起磨削振动,加上凸轮轴本身刚性差则会使这种情况愈加严重,其后果则是在磨削表面产生直线波纹,甚至达到肉眼就可看出的程度。
3、加工精度要求越来越高
随着汽车工业的迅速发展,节能和环保日益成为人们关注的焦点。新的凸轮轴设计标准对加工设备提出了更高的要求,凸轮轴的加工精度的高低直接影响到发动机的的质量、寿命、废气排放和节能。因而,对发动机的关键零件凸轮轴的制造精度的要求也越来越高。
4、加工节拍和效率高
汽车发动机生产中为提高加工效率,减少生产线上机床数量,在工艺上将多道工艺进行组合。用高速、超高速磨削取代传统的粗加工(如车、铣等),实现以磨代车、以磨代铣,从而在加工工艺上实现突破,将多道工序合并成一道工序,以提高生产效率[2]。
立式磨削
1、立式磨削原理分析
传统的凸轮轴磨削是采用机械靠模仿型磨削法。一般采用卧式磨床,工件夹在两顶尖之间。由于工件夹具的重量以及夹紧力的影响,凸轮轴挠曲变形较大,加工精度较低。
与卧式磨削不同,立式磨削是将工件竖直固定在机床底座内的一个旋转卡盘上,磨削主轴竖直布置,从工件上方开始作上、下运动,从而实现工件的磨削加工。如图1所示。
图1 立式磨削与卧式磨削原理对比图
立式磨床内侧床身上安装了两个独立可行走的十字滑台,十字滑台采用双轴模式,即x轴和z轴,并集成了磨头。工件在加工区中心通过尾架和头架夹紧,尾架安装在下方并且固定,头架安装在上方可上下行走,这种结构为实现左右同步磨削创造了条件。凸轮轴立式磨削示意图如图2所示。
图2 立式磨削示意图
2、立式磨削优势分析
工件垂直放置,克服自重导致的变形
在卧式磨削中,工件水平安装,凸轮轴会因自重而产生弯曲变形,如图3所示。
图3 立式磨削示意图
夹具所施加的夹紧力一方面要抵抗磨削力,另一方面还必须抵抗工件自重,导致施加在工件上的夹紧力较大。在立式磨床上,工件竖直安装,重力作为夹紧力的一部分,施加到下顶尖上,夹紧力只需抵抗磨削力。因此立式磨削相对卧式磨削夹紧力较小,产品在夹紧后的变形量小,在磨削完成工件自由回弹后,产品依然能保证精度。
双轴磨削,克服法向力
立式磨床采用双轴模式,法向力可以互相抵消。普通磨削时加在工件上的主要力是法向力,多数情况下法向力是切向力的3至4倍。当两个砂轮对置时,法向力可以互相抵消,如图2所示。通过两个砂轮的逆向旋转,由法向力造成的扭矩也互相抵消,当工件只是通过头架侧的摩擦力带动时,这种抵消效应的优势会更加明显[3]。
便于装卸,提高效率
立式磨削相对于卧式磨削装卸工作更为简便,能够提高装卸作业的效率,缩短作业时间[4]。
卧式磨床装卸工件时,操作者需双手同时作业,同时由于工件重力的影响,找芯作业比较繁琐;在立式磨床上,操作者只需简单地将工件向下安装到卡盘中即可,同时也保证了作业的安全性,如图3所示。
结论
立式磨床采用工件竖直安装的装夹方式,攻克细长轴类磨削中重力对精度影响的工艺难题攻克了细长杆类零件加工中因工件自重和切削力导致产品变形这一难题。通过双轴磨削克服磨削法向力减少加工中因磨削力导致的产品变形,提高了磨削效率。立式磨削技术,可以实现凸轮轴的高效高精度加工,减轻工人工作强度,节约生产成本,将在凸轮轴的加工中得到更为广泛的应用。
声明:本网站所收集的部分公开资料来源于互联网,转载的目的在于传递更多信息及用于网络分享,并不代表本站赞同其观点和对其真实性负责,也不构成任何其他建议。本站部分作品是由网友自主投稿和发布、编辑整理上传,对此类作品本站仅提供交流平台,不为其版权负责。如果您发现网站上所用视频、图片、文字如涉及作品版权问题,请第一时间告知,我们将根据您提供的证明材料确认版权并按国家标准支付稿酬或立即删除内容,以保证您的权益!联系电话:010-58612588 或 Email:editor@mmsonline.com.cn。
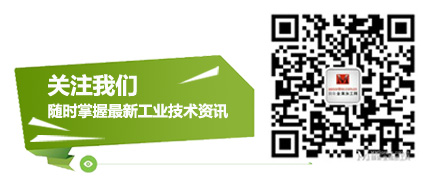
- 暂无反馈