上汽通用:从制造到“智”造 见证中国汽车工业20年
2017年的汉诺威工业博览会刚结束不久,这场全球工业领域的盛会刷新了展会历年的参观人数之最,而其中中国成为这次展会外国参展商和参观人数的领跑者,仅参观人数就高达9000人,可见国内制造业对于工业4.0发展的关注。
汉诺威工业博览会是全球机械工程行业最大的盛会,也是工业4.0概念的提出者。而从今年的展会中发布的数据来看,工业4.0如今已经成功度过了试用阶段,并且已在应用中创造真正的价值。
以目前的汽车行业为例,在互联网行业快速发展的助推和企业对提升生产效率、改善生产品质需求的双驱动下,目前国内一些汽车工厂已经迈向了“智”造级的世界领先水平,并且已经在工业4.0的概念下受益。在这方面,今年迎来20岁生日的上汽通用早已走在了前列。
从“制造”到“智造”,工业以太网全面应用
上汽通用凯迪拉克金桥工厂和上汽通用武汉二工厂都是中国目前最先进的汽车制造工厂之一,代表了当今汽车制造的全球领先水平。从过去的生产大部分依赖人力操作设备,到人力逐渐被自动化设备取代,再到如今生产管理的智能化、物联网化,这两座 “智”造级工厂可以说是上汽通用这二十年在中国由制造到“智”造的见证者。
它们能达到“智”造级的高度一方面源于,在过去汽车工业发展最迅速的二十年中,上汽通用通过采用先进的GMS通用全球制造体系,结合国情和企业特点,对在国内推出的产品进行平台化、标准化设计,实现各平台产品的兼容性,总结了各工厂在自动化、物联网化建设方面的经验;另一方面源于一张网的布局,工业级全以太网。凯迪拉克金桥工厂和武汉二期工厂都是通用全球体系中首批全面应用工业级全以太网络系统的智能工厂。
工业以太网是智能工厂核心,如果说第三次工业革命的自动化,仅是将生产操作设备作为对象,让数控信息技术得到应用。工业4.0就将信息技术的应用大幅扩大,进而衍生出“智能工厂”的概念,它的关键技术是信息技术的快速交换、处理,而工业级以太网就是目前全球公认的局域网络通信协议的最佳选择方案。具体而言,智能工厂不仅是生产的自动化,通过远程监控制程,确保生产顺畅,还可协助制造业者整合各厂生产管理、物流管理及仓库管理,实时匹配产能的需求与规模,避免大兴土木,同时迅速提高产能,满足客户定制化订单的实时生产需求。
具体到汽车领域的智能工厂,我们可以拿凯迪拉克金桥工厂和武汉二期工厂的一些工业级以太网布局的案例来说明工业4.0是如何将信息技术的应用大幅扩大,从而将传统的工厂制造变为“智”造。
自动化、以太网布局齐发力,全球领先的“智”造工厂
如果说一家汽车智能工厂的硬件是自动化设备(焊接机器人、抓取机械手臂、AGC物料配送机器人等)的投入数量的话,那么软件就是能让这些自动化设备的工作节拍、物料的投递根据生产的需求,进行联网化控制,协同工作,让工厂能根据市场变化而进行精确生产管理的工业级以太网布局。
这样的案例我们在凯迪拉克金桥工厂的汽车四大工艺生产车间可以看到很多。比如在车身车间,过去工人搬运冲压钣金、扛着焊枪操作的画面已经远去,取而代之的都是391台联网化的AGC钣金焊接件投递机器人、自动化抓取手臂,柔性的焊接机器人在井然有序工作的画面。
通过工业级以太网的控制,可以根据市场对凯迪拉克车型的订单,来决定每天对车身车间投递多少板材来冲压钣金件,AGC物流机器人则根据冲压件的数量来决定运输的速率和数量到焊接生产线,而焊接机器人则根据运送物料的多少来决定焊接的时间。
传统工厂,工人们手扛焊枪
凯迪拉克金桥工厂车身车间机器人在焊接车身
物联网化、智能化的车身车间也让生产实现了最大化的柔性化,车间柔性化生产可以减少厂房和设备的投入,让传统的平台化生产概念在金桥这座工厂变成过去式。凯迪拉克金桥工厂的车身车间可以最大支持7种车型共线生产,是业内自动化柔性最大的工厂之一,它的出现也为国内其他汽车企业在车身制造领域向“智”造转型提供了参考的模板。
比如在总装车间,总装车间是最能评估一家汽车厂生产线智能化的地方,总装生产线的节拍决定了一座工厂最终的产能。传统总装车间在受到人工操作效率、车间物流供给效率的影响,每小时仅能装备25台车左右。
传统总装车间的人工装配工位
而在凯迪拉克金桥工厂的总装车间,零配件的物流已经实现了高度的物联网化,GVC运输机器人、总装机械手臂等自动化设备之间可以相互“交流”,它们之间信息的“交流”则通过以太网实现。在这座总装车间,底盘拼接可以实现自动巡航装备,座椅、轮胎、车门系统、轮胎这些大件都能实现自动线输送,自动上线率达到了70%,而输送的速率、装配的节拍则通过以太网的控制去根据市场订单来决定。
高度的智能化让金桥这座工厂的生产节拍可以达到每小时生产65台车的产能,相比传统生产线提升了2倍多,让一辆车的总生产周期缩短到了15小时左右。
这条自动化总装线还有一个特点就是它的柔性能够支持7款不同车型的装配,而且通过业界领先的智能物联网系统可追溯每一个关键螺栓、螺母等紧固件的扭矩信息,构建起世界级数字化装配体系,让每一辆车的装配环节都可实现自动化监测、追踪以及后期产品售后管理,即节省了产线设备的投入、也为生产和售后管理提供了快速查询的数据库。
凯迪拉克金桥总装生产线为快速发展中的自主品牌们提供了一个快速提升装配产能的样板,也指明了一个方向:提升产能不只是靠新建厂房来解决,也可以通过对现有生产线进行智能化改造来进行实现,即节省土地和厂房的投入,也节省人力成本的开支,同时大大提升产能。
凯迪拉克金桥工厂的自动化总装车间
凯迪拉克金桥工厂开启了上汽通用的“智”造时代,为后续的新建工厂中“智”造的体系提供了参考的依据,比如同样布局了工业级全以太网的通用武汉二汽工厂,在自动化设备的投入上甚至超过了目前的金桥凯迪拉克工厂。上汽通用凯迪拉克工厂是首批汽车行业工业4.0概念的受益者,在生产效率的提升、单车生产能耗的精细化管理(能耗降低了10%)、生产的环保性等方面都有了显著改善,是“中国制造2025”战略的绿色智能样板工厂。
结 语
从制造到“智”造,上汽通用见证了中国汽车工业发展最快速的二十年。从初建时一个基地、一个工厂、一款车型的萌芽绽露,到今天,拥有四大基地、9个整车生产厂、4个动力总成厂的全国布局,以及全年500万辆级的产能实力。上汽通用从制造到“智”造的发展历程给国内的汽车企业提供了前瞻性布局以及现阶段的制造转型参考的模板,值得国内企业去深入研究和学习。
上汽通用的二十年也给中国市场带来了太多改变市场格局的优秀产品,君威和君越双子星的引入让B级车市场的格局进入道了日德美三强鼎立的格局,别克凯越让我们见证了一款车13年200万辆销量的辉煌成绩,凯迪拉克CT6重新在中国市场定义了美式豪华新旗舰等等。未来上汽通用已经在着手布局2020年之后的国内新能源汽车市场,已经将其全球领先的新能源汽车逐步向中国市场投放,比如新君越30H,迈锐宝XL全混动、CT6 PHEV,别克VELITE 5等。未来市场属于新能源汽车市场,我们有理由期待上汽通用能在接下来的二十年“智”造一个更辉煌的成绩。
声明:本网站所收集的部分公开资料来源于互联网,转载的目的在于传递更多信息及用于网络分享,并不代表本站赞同其观点和对其真实性负责,也不构成任何其他建议。本站部分作品是由网友自主投稿和发布、编辑整理上传,对此类作品本站仅提供交流平台,不为其版权负责。如果您发现网站上所用视频、图片、文字如涉及作品版权问题,请第一时间告知,我们将根据您提供的证明材料确认版权并按国家标准支付稿酬或立即删除内容,以保证您的权益!联系电话:010-58612588 或 Email:editor@mmsonline.com.cn。
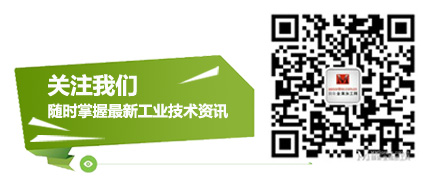
- 暂无反馈