制造强国指日可待 且看中国制造这一年!
《中国制造2025》实施一年有余,我国装备制造业取得不错成绩。“制造大国”迈向“制造强国”路程逐渐缩短,在过去的2016年里,我国制造业又发生了哪些大事?
自国务院去年5月正式颁布《中国制造2025》以来,政策实施一年有余。
这一年,工业和信息化部会同有关部门编制实施了“1+X”体系,发布实施了五大工程实施指南及服务型制造、装备制造业质量品牌提升、医药产业发展等三个行动及规划指南,相关政策细化落地。《中国制造2025》由文件编制进入全面实施新阶段。
世界上规模最大、技术和施工难度系数最高的升船机———三峡升船机,最大提升高度可达113米,只需10分钟,船舶就可以完成近40层楼高度的垂直升降,而且安全稳定,就连立在船上的硬币都全程不倒。
这一年,作为“三步走”战略第一阶段的行动纲领,《中国制造2025》迈出了坚实的第一步。中国制造业强化基础能力建设,更加注重质量和效益提升,由中国制造到中国创造、中国速度到中国质量、中国产品到中国品牌的转变不断加速。
正值“十三五”开局之年,制造业转型升级正在为我国经济发展注入新动能,强国战略的种子正在神州大地生根发芽,累累硕果值得期待。
完善顶层设计 工业强基工程稳步推进
夯实制造之基,不仅关乎一国制造的品质,更决定制造业发展的潜力。在新一轮产业变革下,与发达国家的同台竞技中,基础能力的缺失直接影响到我国整个工业化进程,成为制约我国制造业赶超的最大短板。《中国制造2025》将工业强基列入五大工程重点推进。
工业强基工程就是要在先进基础工艺、关键基础材料、产业技术及核心零部件(元器件)方面实现突破。为加速科技成果转化进程,工信部实施了“一揽子”突破行动,解决了《中国制造2025》中十大重点领域标志性基础产品和技术,促进科技创新成果的工程化、产业化,解决了高端装备和重大工程发展瓶颈。
世界上规模最大、技术和施工难度系数最高的升船机———三峡升船机,最大提升高度可达113米,只需10分钟,船舶就可以完成近40层楼高度的垂直升降,而且安全稳定,就连立在船上的硬币都全程不倒。其“稳”劲儿得益于严丝合缝的工艺。目前,以三峡升船机为代表的一批先进制造业不断刷新世界纪录。
随着互联网日新月异的普及,信息“神经”的“中国造”使我国彻底摆脱了对国外技术路径与产业的依赖。光纤预制棒,被誉为光纤产业“皇冠上的明珠”,占据了光纤产业约70%的价值。
在2010年之前,我国的光纤预制棒大部分依靠进口。依靠技术引进、消化、吸收、创新,位于武汉的长飞光纤光缆股份有限公司打破了国外多年的技术封锁。目前,长飞是全球惟一同时掌握PCVD(等离子体化学气相沉积法)、OVD(外部气相沉积法)和VAD(气相轴向沉积法)三种预制棒制备技术的公司,同时,还自主研发出了VAD工艺平台。长飞公司目前已成为全球第一大光纤预制棒及光纤供货商、全球第二大光缆供应商。
“包括光纤光缆行业在内的中国制造业必须在核心技术上进行自主创新,这是中国从制造大国升级为制造强国的必由之路。”国家制造强国建设战略咨询委委员、中国人民大学教授徐佳宾表示,核心技术最终需要自己进行自主创新。否则,永远只能作为技术的接受者。
去年以来,工信部发布了《工业强基工程实施指南(2016~2020年)》、《工业“四基”发展目录》等实施方案,“成体系”地完善了工业强基工程顶层设计。今年以来,围绕战略性产业和重点行业,工信部新核定了23家工业产品质量控制和技术评价实验室,对首批54家实验室进行了复核,发挥了实验室在支持质量攻关、质量改进等方面的作用。
走进湖南华署高科技有限责任公司用3D打印机进行生产的车间,一排排义齿正在机器中被打印。华署高科总经理、高分子复杂结构增材制造国家工程实验室副主任侯培林介绍,这样的打印设备,在6个小时内可以造出150颗义齿,比传统的手工生产效率高8.5倍。以前包埋铸造的过程牵涉到二十几道工序,现在因为有3D打印工序的调整,成品率从88%~90%提升到了99.7%。
坚持“质量为先”方针,依托工业强基工程,工信部发挥产业技术基础公共服务平台作用,以《中国制造2025》十大战略性产业为重点,梳理了机械、电子等重点领域的非竞争性质量共性技术问题。今年以来,针对行业非竞争性共性质量技术问题解决方案的推广应用进行了项目招标,着重解决了高端装备伺服系统和旋转机械中转子系统的可靠性问题,并向不少于50家行业企业进行了推广。
落实制造强国战略,工信部先后安排了253个示范项目,总投资约379亿元,高端航空紧固件、高标准轴承等一批“卡脖子”问题得到解决。
科技创新取得实效 重大技术装备硕果累累
推进行业关键共性技术取得突破,通过创新引领和带动新一轮中国制造业的发展是制造强国战略的应有之义。为引导社会各类资源集聚,推动优势和战略产业快速发展,去年9月,国家制造强国建设战略咨询委员会发布了〈中国制造2025〉重点领域技术路线图(2015版)》。明确了新一代信息技术产业等十大领域的发展方向和目标。
经过一年多的实践,十大重点领域创新发展成绩斐然。德国法兰克福国际超算大会公布了新一期全球超级计算机TOP500榜单,我国的“神威·太湖之光”以超第二名近三倍的运算速度成为“世界最快计算机”。今年6月,我国首架国产支线客机ARJ21正式进入航线运营。7月,AG600大型灭火救援水陆两栖飞机总装下线。8月,“海斗”号无人潜水器完成最大下潜深度10767米。9月,我国自主研制的、世界上规模最大的长江三峡升船机试通航取得成功。这些成绩的取得,树立了我国制造业的新高度。
通过科技重大专项的实施,我国一批重大技术装备实现创新突破及产业化发展。例如,28纳米芯片制程工艺进入量产、C919大型客机总装下线、运-20大型运输机交付部队列装、我国主导的TD-LTE技术成为4G主流国际标准之一。此外,我国还积极推动了核心电子器件、高端通用芯片及基础软件产品,新一代宽带无线移动通信网,高档数控机床与基础制造装备,大型飞机四个科技重大专项的实施。
国家制造业创新中心建设是构建国家制造业创新体系的重要举措。今年6月,我国首家制造业创新中心———国家动力电池创新中心正式成立,推动了国家和省级制造业创新中心的建设步伐。目前,国家增材制造、工业机器人创新中心建设方案已通过论证,我国江苏、湖北、广东等省建设了19家省级制造业创新中心。按照《关于完善制造业创新体系,推进制造业创新中心建设的指导意见》规划,到2020年我国将重点形成15家左右国家制造业创新中心,到2025年形成40家左右国家制造业创新中心。
落实制造强国战略,我国工业领域技术创新经过模仿创新、集成创新、引进消化吸收再创新等多个阶段,现在正由跟随式创新向引领式创新转型。
智能制造展开试点示范 两化深度融合渐入佳境
网络信息技术发展日新月异,并与制造技术融合发展,成为新一轮科技革命和产业变革的重大趋势和主要特征。《中国制造2025》明确提出,要以加快新一代信息技术与制造业深度融合为主线,以推进智能制造为主攻方向,推动我国从制造业大国向制造业强国转变。
去年以来,工信部编制并推动出台了《信息化和工业化融合发展规划(2016~2020年)》。持续开展两化融合管理体系国家标准制定工作,并顺利完成了年度贯标试点工作。
2016年,我国新增600家两化融合管理体系国家级贯标试点企业。全国范围共计3500余家企业开展了贯标工作。截至11月,新增342家企业通过两化融合管理体系评定,全国通过评定企业共计542家。进一步完善了两化融合管理体系工作机制与顶层设计。近60个细分行业的70000余家企业开展了两化融合自评估、自诊断、自对标。在企业评估诊断数据基础上,全国两化融合服务联盟绘制了《全国两化融合发展数据地图》。
顺应技术、产业发展趋势,工信部推动发布实施了《国务院关于深化制造业与互联网融合发展的指导意见》。组织实施制造业与互联网融合发展试点示范、智能制造试点示范和智能制造专项,智能制造标准体系框架初步形成,基于互联网的双创平台快速成长。目前,我国数字化研发设计工具普及率、工业企业数字化生产设备联网率分别达到61.8%和38.2%,制造业与互联网融合不断深化,制造业数字化、网络化、智能化发展水平不断提高。
作为两化融合的主攻方向,智能制造试点示范成效显著。海尔通过实施互联工厂,产品开发周期缩短20%以上,交货周期由21天缩短到7~15天,能源利用率提升5%。湖南红太阳光电科技有限公司通过智能物流传输及仓储系统、制造执行系统、智能制造管控平台等系统建设,实现了车间的数字化管控,产品不良品率降低30%,研制周期降低30%,能源利用率提高15%,生产效率提高了20%。美的集团武汉分公司通过对空调生产线进行自动化和信息化改造,将单条生产线的一次组装合格率由97%提升至99.9%,减少仓储面积46万平方米,将供货周期由24天降至9天。
去年以来,我国先后确定了109个智能制造试点示范项目,在各细分行业积累了可复制可推广的经验和模式。从去年启动的46个试点示范项目实施效果看,企业生产效率平均提升了38%,能源利用率平均提升了9.5%,运营成本平均降低了21%,产品研制周期平均缩短了35%,产品不良品率平均降低了27%。
经过一年多的实践,我国制造强国战略已经扎实迈出了第一步。“下一步,要继续推进部省联动,调动各方面积极性,抓好统筹协调,做好规划衔接和政策配套。”工业和信息化部部长苗圩强调,加快推进《中国制造2025》政策落地,要按照制造强国领导小组提出的要求,把战略规划变成年度计划,把年度计划变成实际的行动,把实际行动转化为实际成果,把规划目标细化为具体工作,逐步落实。
声明:本网站所收集的部分公开资料来源于互联网,转载的目的在于传递更多信息及用于网络分享,并不代表本站赞同其观点和对其真实性负责,也不构成任何其他建议。本站部分作品是由网友自主投稿和发布、编辑整理上传,对此类作品本站仅提供交流平台,不为其版权负责。如果您发现网站上所用视频、图片、文字如涉及作品版权问题,请第一时间告知,我们将根据您提供的证明材料确认版权并按国家标准支付稿酬或立即删除内容,以保证您的权益!联系电话:010-58612588 或 Email:editor@mmsonline.com.cn。
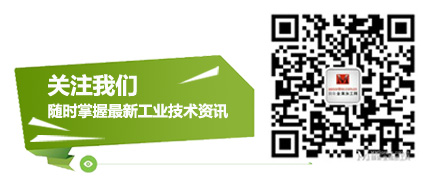
- 暂无反馈