工控机在电弧炉控制系统中的应用
随着计算机技术的普及与应用,数字技术已经渗透于各行业之中,特别是在一些传统工业的改造与创新中,发挥了重要的作用。本文介绍的工控机参与自动控制系统对电弧炉的控制,使控制系统技术含量大大提高。经过生产实践证明,该系统在安全性、可靠性、灵敏度等方面大大优于传统的模拟控制方法。
1系统组成
本系统由一台研华5X86/133工控机,输入输出电路板(D/A板,A/D板和触发脉冲板),WB系列电流电压传感器,富士G11型变频器(四台,其中一台备用)以及交流异步电动机组成。系统组成框图如图1所示。
本系统采用电气传动控制电极上下运动。经计算,选用功率为7.5kW的异步电机,并以此为依据选用变频器。本系统选用富士G11型变频器,其特点是:不需要正负转换信号,仅根据给定频率控制输出电压的大小和极性即可控制电机的转速与转向。
由于电极的电弧电流太大(约为25kA),所以传感器从电流互感器进行采样。因为A/D转换卡的输入信号为电压型,故我们选用电磁隔离、感应式的WBI412as1Q型电流—电压传感器。而对于电弧电压(一般为250V左右),则不需要中间环节,直接选用电磁隔离、感应式的WBV414asQ型电压-电压传感器即可。
为了易于控制与维护,电极的每一相都为一套独立设备(包括传感器,变频器,电机和印刷线路板),为此在控制软件的设计中采用分相进行独立控制的原则。此外,额定电流的设定和电源模块的供电所需要的0~12V电源,可通过小型变压器和WY1?7812,WY2?7912等组成的电路来实现,此处不一一详述。
2硬件设计
系统的控制原理如图2所示。
本系统选用研华公司开发的PCL?730型A/D转换卡,此卡提供32路DIO(DigitalInputOutput)通道,其中包括16路输入和16路输出。每路都带有光耦隔离,用于提高系统的抗干扰能力。选用分辨率为12位的PCL?728型D/A转换卡作为输出卡,此板卡具有2个通道,其输出电压范围可利用板卡的跳线设定到-10V~+10V之间,便可直接控制变频器。在上述系统中,选用分辨率为12位的PCL?813型A/D转换卡,它可以提供32路模拟输入量,故仅需一块便可实现电弧电流、电弧电压和电流设定值等的模数转换。
图1系统组成框图
图2控制系统框图
图3模拟系统与数字系统切换
图4变频器及相关电路
图5变频器开关
本系统分为手动和自动两种工作状态,其中自动工作状态又分为模拟状态和数字状态。在自动工作状态时,通过转换开关,可使继电器触点选择模拟通路或数字通路(其中数字通路一般接常闭触点),切换结构如图3所示。手动工作状态下,电路实现较为简单,它不经过中间电路和信号处理过程便可直接驱动变频器。所以它的优先级较高,故适用于在紧急情况下的应急操作,其与自动状态下的切换如图4所示。
富士变频器端子12为设定电压输入端,端子11为模拟信号公共端,FWD为运行/停止命令端,CM为接点输入公共端。因为不能采用直接接通与断开主电路电源的方法来操作变频器的运行与停止。采用图5所示的电路,在保持主电路接通的情况下,只需按按钮开关SB,使交流接触器线包带电,吸合KM?1使指示灯亮,KM?2给变频器送电(见图4)。
此类变频器通过键盘,面板操作体系(画面转换层次结构)来设定,监控,查询。操作者通过LCD监视器与操作键来设定自己所需确定的参数,如最高频率,额定电压,加速时间,转矩特征等。在运行过程中选择自己所关心的数据(如输出电压)作为实时监控对象。设计者还可根据系统的实际要求设计适当的制动电阻,处理报警输出信号及抗干扰措施等等。
3软件设计
电弧炉控制系统的软件是根据各个炉子的实际情况而开发的。在本工程中系统软件由界面模块,运算模块和打印模块三大部分组成。其中界面程序提供了一个人机对话窗口,操作者可以清楚地了解到电炉目前的各个参数,从外部输入的模拟量的数字化值的大小(如档位电压)。另外,外部参数的修订也都是利用人机界面从键盘输入实现的。本系统的界面是用BORLANDC和汇编语言编制而成,在编制过程中力求达到美观、直观、易操作的目的。
输入输出采集运算是本系统的核心部分,在沿袭前辈工作经验的基础上,通过跳线和小型转换开关,选择出适合于系统的输入输出通道与形式(PCL为高集成板,提供了多种功能选择,如可以电压形式输出,也可以电流形式输出等)。在控制运算过程中根据电弧炉的点弧期,熔化期,精炼期以及钢水出炉前弧流弧压的不同状况,在控制子程序的算法实施上应有所区别,其程序流程图如图6所示。在控制过程中充分利用了G11变频器电压速率的特点(如图7所示),降低了硬件的设计复杂度。电流设定值和电压设定值的确定,根据外部电路所能提供的电源电压而选择不同的转换算法。软件中仅仅考虑采集与转换是不够的,本系统对于数据处理采用的是PID控制算法。控制方式上,模拟系统通过硬件电路来实现,而软件设计则是通过PID算法来完成的。为了保证冶炼的温度恒定,又要电极的运动不会出现太大波动,就在控制系统中增设给定积分环节。对电路的参数设定可借鉴模拟调节器的参数,衰减曲线法等,取得良好的比例积分(PI)控制参数。
图6运行程序流程图
图7速度—电压曲线
图8电流曲线及功率曲线
(a)电流曲线(b)功率曲线
由于PC机的介入,控制软件中也应该考虑到数据的记录与保存问题,尤其一些重要参数,功率曲线,电流曲线及电压曲线都应打印出来,以对日后的故障诊断、维修以及设备的改进提供一手资料。
另外,对于所涉及的参数预先进行估计与计算,定出其最大值,以确保取得或处理后的数据在其值域内,不会溢出。既保证结果的合理与执行的可靠性,又避免了数据的跳跃,引起元件寿命缩短与机械损伤。
4现场抗干扰设计及运行结果
冶炼炉工作环境一般较为恶劣,干扰比较严重,针对现场存在的问题,采取了以下措施:
(1)由于钢厂电压偏高(有时控制电压达270V
左右,子夜更高),为此,工控机电源必须加稳压器,以保证工控机正常工作;
(2)电弧炉在冶炼过程中产生极强电磁场,电磁
干扰严重影响了控制线路的精度,故变频器和工控机的输入输出线路全采用屏蔽线,显示器选液晶型的(电子枪式显示屏会在磁场中受到干扰,使画面扭曲,无法正常工作);
(3)变频器、工控机电源地线与固定零线短接;
(4)现场空气中含有大量金属粉尘,对于易受污
染的电器设备进行密封,并定期用皮老虎进行除尘。
采用以上措施,干扰基本排除,图8(a)是冶炼期得到的电流曲线图,图8(b)为功率曲线图,其中0~t1为点弧初期,t1~t2为熔化期,t2~t3为精练期。
5结语
本系统经过调试期的试运行,以其操作简便,电极起落平稳,电流稳定,节约电能,操作简便,较模拟系统有较大的优越性,而得到工厂各部门的好评,该控制系统可在此行业中进一步推广使用。
声明:本网站所收集的部分公开资料来源于互联网,转载的目的在于传递更多信息及用于网络分享,并不代表本站赞同其观点和对其真实性负责,也不构成任何其他建议。本站部分作品是由网友自主投稿和发布、编辑整理上传,对此类作品本站仅提供交流平台,不为其版权负责。如果您发现网站上所用视频、图片、文字如涉及作品版权问题,请第一时间告知,我们将根据您提供的证明材料确认版权并按国家标准支付稿酬或立即删除内容,以保证您的权益!联系电话:010-58612588 或 Email:editor@mmsonline.com.cn。
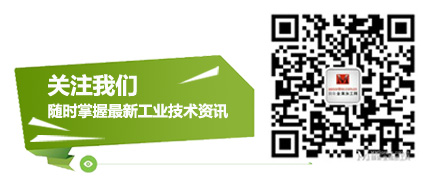
- 暂无反馈