注塑件常见成型缺陷及解决方案
【编者按】注塑是一种工业产品生产造型的方法。产品通常使用橡胶注塑和塑料注塑。 注塑还可分注塑成型模压法。和压铸法。注射成型机(简称注射机或注塑机)是将热塑性塑料或热固性料利用塑料成型模具制成各种形状的塑料制品的主要成型设备,注射成型是通过注塑机和模具来实现的。
本文针对塑件在成型过程中出现的各种注塑缺陷,主要是:短射,困气,发脆,烧焦,飞边,分层起皮,喷流痕,流痕,雾斑(浇口晕),银纹(水花纹),凹痕,熔接痕,成型周期过长,翘曲变形,分析了问题产生的可能原因,从原材料、塑件或模具设计、成型工艺等各方面,提出解决方案。
一、短射
短射是指模具型腔不能被完全充满的一种现象。
短射形成原因:
1、模温、料温或注塑压力和速度过低
2、原料塑化不均
3、排气不良
4、原料流动性不足
5、制件太薄或浇口尺寸太小
6、聚合物熔体由于结构设计不合理导致过早固化
短射解决方案:
材料:选用流动性更好的材料,如toolox44。
模具设计:
1、填充薄壁之前先填充厚壁,避免出现滞留现象
2、增加浇口数量和流道尺寸,减少流程以及流动阻力
3、排气口的位置和尺寸设置适当,避免出现排气不良的现象
注塑机:
1、检查止逆阀和料筒内壁是否磨损严重
2、检查加料口是否有料或是否架桥
工艺条件:
1、增大注塑压力和注塑速度,增强剪切热
2、增大注塑量
3、增大料筒温度和模具温度
二、困气
困气是指空气被困在型腔内而使制件产生气泡。
困气形成原因:
它是由于两股熔体前锋交汇时气体无法从分型面、顶杆或排气孔中排出造成的。困在型腔内气体不能被及时排出,易导致出现表面起泡,制件内部夹气,注塑不满等现象。
困气解决方案:
结构设计:减少厚度的不一致,尽量保证壁厚均匀
模具设计:
1、在最后填充的地方增设排气口
2、重新设计浇口和流道系统
工艺条件:
1、降低最后一级注塑速度.
2、增加模温
三、发脆
塑件发脆是指制件在某些部位出现容易开裂或折断。
发脆原因:
1、干燥条件不适合;使用过多回收料
2、注塑温度设置不对
3、浇口和流道系统设置不恰当
4、熔解痕强度不高
发脆解决方案:
材料:
1、注塑前设置适当的干燥条件
2、减少使用回收料,增加原生料的比例.
3、选用高强度的塑胶.
模具设计:增大主流道、分流道和浇口尺寸
注塑机:选择设计良好的螺杆,使塑化时温度分配更加均匀
工艺条件:
1、降低料筒和喷嘴的温度
2、降低背压、螺杆转速和注塑速度
3、通过增加料温,加大注塑压力,提高熔解痕强度
四、烧焦
焦痕是指型腔内气体不能及时排走,导致在流动最末断产生烧黑现象。
烧焦原因:
1、型腔空气不能及时排走
2、材料降解:过高熔体温度;过快螺杆转速; 流道系统设计不当
烧焦解决方案:
模具设计:
1、在容易产生排气不良的地方增设排气系统
2、加大流道系统尺寸
工艺条件:
1、降低注塑压力和速度
2、降低料筒温度
3、检查加热器、热电偶是否工作正常
五、飞边
飞边是指在模具分型面或顶杆等部位出现多余的塑料。
飞边产生原因:
1、合模力不足
2、模具存在缺陷
3、成型条件不合理
4、排气系统设计不当
飞边解决方案
模具设计:
1、合理设计模具,保证模具合模时能够紧闭
2、检查排气口的尺寸
3、清洁模具表面
注塑机:设置适当大小吨位的注塑机
成型工艺:
1、增加注塑时间,降低注塑速度
2、降低料筒温度和喷嘴温度
3、降低注塑压力和保压压力
六、分层起皮
分层起皮是指制件表面能被一层一层的剥离。
分层起皮原因分析:
1、混入不相容的其他高分子聚合物
2、成型时使用过多的脱模剂
3、树脂温度不一致
4、水分过多
5、浇口和流道存在尖锐的角
分层起皮解决方案
材料:避免不相容的杂质或受污染的回收料混入原料中
模具设计:对所有存在尖锐角度的流道或浇口进行倒角处理
工艺条件:
1、增加料筒和模具温度
2、成型前对材料进行恰当的干燥处理
3、避免使用过多的脱模剂
七、喷流痕
喷流痕(jetting):由于熔胶流动太快引起的一种喷射痕迹,一般呈蛇纹状。
喷流痕原因分析:
1、浇口尺寸太小,又正对着截面积很大的产品面;
2、充填速度太快
喷流痕解决方案
模具设计:
1、增大浇口尺寸
2、将侧浇口改为搭接式浇口
3、浇口正前方增加挡料销
工艺条件:降低刚通过浇口处的充填速度
八、流痕
流痕是指在产品表面呈波浪状的成型缺陷,是由于熔胶流动缓慢引起的一种蛙跳痕迹。
流痕的原因分析:
1、模温和料温过低
2、注塑速度和压力过低
3、流道和浇口尺寸过小
4、由于产品结构的原因,引起充填流动时,加速度过大
流痕解决方案
模具设计:
1、增大流道中冷料井的尺寸
2、增大流道和浇口的尺寸
3、缩短主流道尺寸或改用热流道
工艺条件:
1、增加注塑速度
2、增加注塑压力和保压压力
3、延长保压时间
4、增大模温和料温
九、雾斑
雾斑:浇口附近产生的云雾状色变。原因是熔胶破折(melt fracture)。
雾斑的原因分析:
浇口太小或进胶处型腔太薄,熔胶流量大,断面积小时,剪切速率大,剪切应力往往跟着提高,以致熔胶破折,产生雾班现象。
雾斑的解决方案
moldflow模拟,可以预测熔胶通过上述狭隘区时的温度、剪切速率和剪切应力。而moldflow一般都会提供各种塑料料温、剪切速率和剪切应力的上限。moldflow工程师可以根据分析结果作相应的调整,找出适当的浇口尺寸和进胶处型腔壁厚,从而消除雾斑。
十、银纹
银纹是指水分、空气或炭化物顺着流动方向在制件表面呈现发射状分布。
银纹产生的原因:
1、原料中水分含量过高
2、原料中夹有空气
3、聚合物降解:材料被污染;料筒温度过高;注塑量不足
银纹解决方案
材料:注塑前先根据原料商提供数据干燥原料
模具设计:检查是否有充足的排气位置
成型工艺:
1、选择适当的注塑机和模具
2、切换材料时,把旧料完全从料筒中清洗干净
3、改进排气系统
4、降低熔体温度、注塑压力或注塑速度
十一、凹痕
凹痕是指制件在壁厚处出现表面下凹的现象。
凹痕形成的原因分析:
1、注塑压力或保压压力过低
2、保压时间或冷却时间过短
3、熔体温度或模温过高
4、制件结构设计不当
凹痕解决方案
结构设计:
1、在易出现凹痕的表面进行波纹状处理
2、减小制件厚壁尺寸,尽量减小厚径比,相邻壁厚比应控制在1.5~2,并尽量圆滑过渡
3、重新设计加强筋、沉孔和角筋的厚度,它们的厚度一般推荐为基本壁厚的40-80%
成型工艺:
1、增加注塑压力和保压压力
2、增加浇口尺寸或改变浇口位置
十二、熔接痕
熔接痕是指两股料流相遇熔接而产生的表面缺陷。
熔接痕产生原因分析:
制件中如果存在孔、嵌件或是多浇口注塑模式或是制件壁厚不均,均可能产生熔接痕。
熔接痕解决方案
材料:增加塑料熔体的流动性
产品设计:调整产品结构和壁厚分布
模具设计:
1、改变浇口的位置
2、增设排气槽
工艺条件:
1、增加熔体温度
2、降低脱模剂的使用量
十三、缩短成型周期
运用moldflow软件,可以准确的预测出充填时间、保压时间、冷却时间,再加上开合模的时间,就是成型周期。并可通过优化产品壁厚、模具结构和工艺条件,来缩短成型周期,提高生产率。
十四、翘曲变形
塑料件设计和生产中遇到最多和最难解决的问题就是翘曲变形。
制品翘曲的主要原因:
1、模具结构:浇注系统、冷却系统与顶出系统等。
2、产品结构:塑件壁厚的变化、具有弯曲或不对称的几何形状、加强筋及boss柱设计不合理等。
3、生产工艺:塑件尚未完全冷却就顶出,注射和保压曲线不合理等因素。
4、塑胶材料:塑件材料有、无添加填充料的差异,收缩率的大小等。
moldflow将产品的翘曲变形归纳为四个主要因素:
1、冷却不均匀:冷却水路设计不合理,使产品不能获得均匀的冷却。
解决方案:优化冷却水路
2、收缩不均匀:产品各处收缩不一致。
解决方案:更改材料、产品结构、浇口数量和位置、保压曲线
3、纤维取向不均匀:当纤维取向不均匀引起产品大的翘曲变形。
解决方案:浇口数量和位置、产品结构
4、角落效应:深盒状产品角落处热量集中,收缩较大,带来弯曲变形。
解决方案:加强角落处冷却、减薄角落处壁厚。
, 255,255,255); text-indent: 0px; -webkit-text-stroke-width: 0px">
焦痕是指型腔内气体不能及时排走,导致在流动最末断产生烧黑现象。
烧焦原因, :
1、型腔空气不能及时排走
2、材料降解:过高熔体温度;过快螺杆转速; 流道系统设计不当
烧焦解决方案:
模具设计:
1、在容易产生排气不良的地方增设排气系统
2、加大流道系统尺寸
工艺条件:
1、降低注塑压力和速度
2、降低料筒温度
3、检查加热器、热电偶是否工作正常
五、飞边
飞边是指在模具分型面或顶杆等部位出现多余的塑料。
飞边产生原因:
1、合模力不足
2、模具存在缺陷
3、成型条件不合理
4、排气系统设计不当
飞边解决方案
模具设计:
1、合理设计模具,保证模具合模时能够紧闭
2、检查排气口的尺寸
3、清洁模具表面
注塑机:设置适当大小吨位的注塑机
成型工艺:
1、增加注塑时间,降低注塑速度
2、降低料筒温度和喷嘴温度
3、降低注塑压力和保压压力
六、分层起皮
分层起皮是指制件表面能被一层一层的剥离。
分层起皮原因分析:
1、混入不相容的其他高分子聚合物
2、成型时使用过多的脱模剂
3、树脂温度不一致
4、水分过多
5、浇口和流道存在尖锐的角
分层起皮解决方案
材料:避免不相容的杂质或受污染的回收料混入原料中
模具设计:对所有存在尖锐角度的流道或浇口进行倒角处理
工艺条件:
1、增加料筒和模具温度
2、成型前对材料进行恰当的干燥处理
3、避免使用过多的脱模剂
七、喷流痕
喷流痕(jetting):由于熔胶流动太快引起的一种喷射痕迹,一般呈蛇纹状。
喷流痕原因分析:
1、浇口尺寸太小,又正对着截面积很大的产品面;
2、充填速度太快
喷流痕解决方案
模具设计:
1、增大浇口尺寸
2、将侧浇口改为搭接式浇口
3、浇口正前方增加挡料销
工艺条件:降低刚通过浇口处的充填速度
八、流痕
流痕是指在产品表面呈波浪状的成型缺陷,是由于熔胶流动缓慢引起的一种蛙跳痕迹。
流痕的原因分析:
1、模温和料温过低
2、注塑速度和压力过低
3、流道和浇口尺寸过小
4、由于产品结构的原因,引起充填流动时,加速度过大
流痕解决方案
模具设计:
1、增大流道中冷料井的尺寸
2、增大流道和浇口的尺寸
3、缩短主流道尺寸或改用热流道
工艺条件:
1、增加注塑速度
2、增加注塑压力和保压压力
3、延长保压时间
4、增大模温和料温
九、雾斑
雾斑:浇口附近产生的云雾状色变。原因是熔胶破折(melt fracture)。
雾斑的原因分析:
浇口太小或进胶处型腔太薄,熔胶流量大,断面积小时,剪切速率大,剪切应力往往跟着提高,以致熔胶破折,产生雾班现象。
雾斑的解决方案
moldflow模拟,可以预测熔胶通过上述狭隘区时的温度、剪切速率和剪切应力。而moldflow一般都会提供各种塑料料温、剪切速率和剪切应力的上限。moldflow工程师可以根据分析结果作相应的调整,找出适当的浇口尺寸和进胶处型腔壁厚,从而消除雾斑。
十、银纹
银纹是指水分、空气或炭化物顺着流动方向在制件表面呈现发射状分布。
银纹产生的原因:
1、原料中水分含量过高
2、原料中夹有空气
3、聚合物降解:材料被污染;料筒温度过高;注塑量不足
银纹解决方案
材料:注塑前先根据原料商提供数据干燥原料
模具设计:检查是否有充足的排气位置
成型工艺:
1、选择适当的注塑机和模具
2、切换材料时,把旧料完全从料筒中清洗干净
3、改进排气系统
4、降低熔体温度、注塑压力或注塑速度
十一、凹痕
凹痕是指制件在壁厚处出现表面下凹的现象。
凹痕形成的原因分析:
1、注塑压力或保压压力过低
2、保压时间或冷却时间过短
3、熔体温度或模温过高
4、制件结构设计不当
凹痕解决方案
结构设计:
1、在易出现凹痕的表面进行波纹状处理
2、减小制件厚壁尺寸,尽量减小厚径比,相邻壁厚比应控制在1.5~2,并尽量圆滑过渡
3、重新设计加强筋、沉孔和角筋的厚度,它们的厚度一般推荐为基本壁厚的40-80%
成型工艺:
1、增加注塑压力和保压压力
2、增加浇口尺寸或改变浇口位置
十二、熔接痕
熔接痕是指两股料流相遇熔接而产生的表面缺陷。
熔接痕产生原因分析:
制件中如果存在孔、嵌件或是多浇口注塑模式或是制件壁厚不均,均可能产生熔接痕。
熔接痕解决方案
材料:增加塑料熔体的流动性
产品设计:调整产品结构和壁厚分布
模具设计:
1、改变浇口的位置
2、增设排气槽
工艺条件:
1、增加熔体温度
2、降低脱模剂的使用量
十三、缩短成型周期
运用moldflow软件,可以准确的预测出充填时间、保压时间、冷却时间,再加上开合模的时间,就是成型周期。并可通过优化产品壁厚、模具结构和工艺条件,来缩短成型周期,提高生产率。
十四、翘曲变形
塑料件设计和生产中遇到最多和最难解决的问题就是翘曲变形。
制品翘曲的主要原因:
1、模具结构:浇注系统、冷却系统与顶出系统等。
2、产品结构:塑件壁厚的变化、具有弯曲或不对称的几何形状、加强筋及boss柱设计不合理等。
3、生产工艺:塑件尚未完全冷却就顶出,注射和保压曲线不合理等因素。
4、塑胶材料:塑件材料有、无添加填充料的差异,收缩率的大小等。
moldflow将产品的翘曲变形归纳为四个主要因素:
1、冷却不均匀:冷却水路设计不合理,使产品不能获得均匀的冷却。
解决方案:优化冷却水路
2、收缩不均匀:产品各处收缩不一致。
解决方案:更改材料、产品结构、浇口数量和位置、保压曲线
3、纤维取向不均匀:当纤维取向不均匀引起产品大的翘曲变形。
解决方案:浇口数量和位置、产品结构
4、角落效应:深盒状产品角落处热量集中,收缩较大,带来弯曲变形。
解决方案:加强角落处冷却、减薄角落处壁厚。
展望未来,和轩公司将一如既往地与广大客户共用网路资源,以优质的产品、合理的价格、真诚的服务、超前的经营理念与客户真诚合作、互惠互利拓展市场、共同发展。
声明:本网站所收集的部分公开资料来源于互联网,转载的目的在于传递更多信息及用于网络分享,并不代表本站赞同其观点和对其真实性负责,也不构成任何其他建议。本站部分作品是由网友自主投稿和发布、编辑整理上传,对此类作品本站仅提供交流平台,不为其版权负责。如果您发现网站上所用视频、图片、文字如涉及作品版权问题,请第一时间告知,我们将根据您提供的证明材料确认版权并按国家标准支付稿酬或立即删除内容,以保证您的权益!联系电话:010-58612588 或 Email:editor@mmsonline.com.cn。
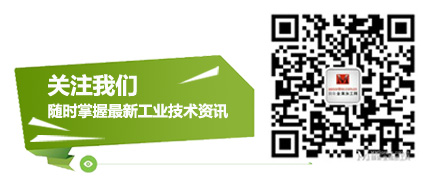
- 暂无反馈