西门子PLC S7-300在氧化铝厂中的应用
氧化铝生产自动监控系统以工业控制计算机、可编程逻辑控制器及现场仪表构成三级监控系统。可编程逻辑控制器选用西门子公司的s7-300系列plc,根据工艺流程在电控室设立3个控制站。
1 引言
氧化铝车间现场石灰或矿土粉尘环境恶劣,车间的自动化控制显得尤为重要。上位机的数据记录及趋势显示功能为车间工作人员积累工艺经验提供了良好的条件,有助于提高生产工艺技术,为管理提供依据,促进企业管理的规范化和设备故障的自动监测,确保工厂的安全生产。
氧化铝生产自动监控系统以工业控制计算机、可编程逻辑控制器及现场仪表构成三级监控系统。可编程逻辑控制器选用西门子公司的s7-300系列plc,根据工艺流程在电控室设立3个控制站。工业机采用wincc作人机界面,通过mpi协议与各站进行数据通信,完成数据采集、处理、监测及控制功能。中央控制室分为服务器和客户机,客户机主要完成系统组态及控制参数的在线修改、监控、报表显示及打印等功能;服务器主要完成对整个氧化铝厂的数据处理。本系统的服务器采用冗余设计,两个服务器互为备用。
2 工艺流程
氧化铝厂的工段主要有原料磨、溶出、赤泥沉降、控制过滤、分解分级及种子过滤、蒸发、成品过滤、焙烧及氧化铝包装堆栈工段等。而各个工段中所要实现自动化控制的设备具有很大的类似性。我们选取其中比较有代表性的原料磨车间的短路上料、石灰消化工段与氧化铝包装堆栈工段来说明整个plc控制系统的构成。
短路上料与石灰消化工段的距离较近,短路上料工段是为其它工段运送原料,通过三通留子将生石灰运到石灰消化工段,而在石灰消化工段中,将生石灰与热水在化灰机中混合、搅拌,生成石灰乳。氧化铝包装堆栈相对其它两个工段是独立的,与其它两个工段相距较远,在氧化铝包装堆栈工段,主要是对贮存在氧化铝大仓里的最后产品——氧化铝粉末进行打包处理。
3 自动化方案设计
3.1 设计思想
选用siemens公司s7-300 plc作为现场控制单元。根据氧化铝生产各个工艺流程在电控室设置了三个控制主站,通过mpi将现场监测仪表采集的信号送到电控室的服务器。整个自动化监控系统构成scada(superv-isory control and data acquisition)系统,完成数据采集、处理、监视及对现场设备进行控制的功能。系统结构如图1所示。
图1 plc控制系统结构图
(1)设备层。设备层主要是指现场车间的设备、仪表等被控对象。在氧化铝厂的工艺流程中用到的设备种类繁多,动力执行机构如化灰机、板式给料机、脉冲控制仪、鼓风机、皮带机、气动调节阀等,现场仪表如温度传感器、雷达物位计、流量计等。
(2) 下位机plc。下位机plc的主要作用体现在两方面。
一是对现场某些重要变量进行监视,对现场被控设备进行远程控制。需要监视的重要变量如某些大罐大仓的液位、物位,管道压力、流量,焙烧炉温度,以及动力设备的上电状态等;而对现场设备的控制包括对脉冲控制仪、鼓风机等动力设备的远程启停控制,对皮带的变频调速,对调节阀开度的控制等。
二是与上位机人机界面(hmi)软件的连接。将设备层的有关信息和数据传入上位机,使得操作员通过人机界面软件实现对现场设备参变量的集中监视,实现对现场设备的远程控制。
(3)上位机hmi软件wincc。wincc是按照客/服(c/s)系统设计的。本系统采用三个客户机和两个冗余的服务器组成。客户机通过访问服务器中的数据,并将这些数据结合在一起显示,使得多画面任务的系统得以轻松解决,提高了系统的可靠性。
3.2 分布式控制站设计
本系统共设三个plc分布控制站。plc1站对短路上料工段进行监控;plc2站对石灰消化工段进行监控;plc3站对氧化铝包装堆栈工段进行监控。
3.3 现场控制柜功能设计
各现场控制柜具有两部分功能,一是进行现场的手动操作,二是与各个远程rio站连接,将各设备状态信号传送到plc。现场手动操作具有比远程更高的优先权,只有将状态开关打到自动状态,自动控制才起作用。所以在接入自动监控系统前,首先要完成对现场各控制柜的状态转换。
4 系统硬件实现
4.1 中央控制室
中央控制室设有两台冗余服务器和三台客户机、一台彩色激光打印机等。服务器均采用研华工控机配置为intel p4 cpu/2.8ghz/512m ram/80g,客户机均采用研华工控机配置为intel p4 cpu/1.6ghz/512m ram/40g,服务器和客户机均装有windows2000 sever/professional操作系统和step7 5.4和wincc 6.0软件。
4.2 plc系统配置
plc是该控制系统的核心,控制过程中全部的输入输出量都要经过plc的处理,所有继电器的动作都由plc的输出控制来完成。现场三个西门子s7-300 plc站的详细配置内容如附表所示。
每个s7-300 plc都只有一个机架,水平安装在控制柜中。各模块的安装顺序为电源模块ps、cpu模块、数字量输入模块di、数字量输出模块do、模拟量输入模块ai从左到右依次排列。
5 系统软件设计
整个系统软件分为上位机监控软件和plc编程软件。
5.1 上位机监控软件
本系统采用1024点的siemens wincc组态软件对系统进行监控。三台客户机的主画面分别显示三个工序的主画面,主画面动态显示车间的整个工艺流程,包括显示所有的开关量状态和模拟量的实时值。各个工序阶段形象逼真。在工艺流程画面的上方是一排系统功能按钮,用鼠标点击就可进入相应的画面。分画面还包括报警表格和各模拟量趋势图,整个系统的所有开关量和模拟量都在各个画面中体现出来,监控系统还具备了实时故障报警和历史数据归档功能。
图2 短路上料工段工艺流程
短路上料工段主要实现对于分布在现场的皮带机、风机、板式给料机、三通留子等各类电机的远程控制,以及石灰大仓的物位在上位机上的显示。
图3 石灰消化工段工艺流程
石灰消化工段主要实现车间里各个电机、气动调节阀的远程控制;各个流量计、液位雷达、物位雷达数据在上位机上的显示;相关电机启停、液位、物位的报警及趋势在上位机上的显示;上位机操作人员操作级别的划分。
氧化铝包装堆栈工段主要实现对现场皮带、风机、电动风阀、脉冲控制仪等各类电机的远程控制;现场仪表数据在上位机上的显示;相关电机启停操作以及氧化铝大仓物位的报警记录在上位机上的显示;现场仪表数据趋势图在上位机上的显示。
5.2 plc编程软件
本系统plc的编程使用step7 5.4编写,实现plc对过程数据的初步处理。在step7中,有三种编程语言可用来编程,分别是梯形图(lad)、语句表(stl)、功能块(fbd)。plc的程序主要由块组成,他们存放在block目录下,cpu中的程序就是具有特定功能和特定结构的块。主要包括组织块ob,数据块db,功能fc与功能块fb。主程序中调用其它功能块程序,主程序的编写只能在ob1、ob85等块中,程序编写采用功能块的形式,比较容易阅读和修改。fc功能块之间可以相互调用,但是它执行时必须在主程序中被调用,如图4所示。
图4 step7编程所含块结构图
根据信号表分配的输入输出点的不同,将程序的编写分为数字量和模拟量两种。主程序中编写数字量的逻辑控制,子程序中编写模拟量的转换和储存(并在主程序中调用),数字量控制为逻辑控制,为便于上位机控制,在每个逻辑输出之前都串联一个m位,此位由上位机控制其状态。模拟量需要的是状态显示,在子程序中编写它的a/d转换。aiw作为输入端,将最后数据保存在db块。
fc1块主要是模拟量的转换,现场的传感器将模拟量实际值转换成4~20ma信号,而ai模块将4~20ma信号经过a/d转换,变成一个内码数0~27648。plc读取的端口数字仅仅是一个内码值,这就需要编程将此内码数变成实际值送上位机显示。公式如下:
实际值= ×(实际值上限-实际值下限)+实际值下限。
图5 fc1模拟量部分程序
图5是fc1块的部分程序,网络1是将模拟量首先存入temp4;网络2是判断temp4值的大小,如果大于27648将27648赋予它,如果小于0将0赋予它,保证数在0-27648之间,并存入temp5;网络3是将temp5的整数格式转换变为双整数,然后将双整数变为实数。
为了防止石灰乳过满后在无人操作的情况下产生溢出,我们在控制系统中加入了连锁功能,当两个石灰乳槽中有任何一个液位高于3.65m时,系统会自动停止石灰仓下的定量给料机,定量给料机停止6分钟后自动关闭热水槽电动阀,热水停止4分钟后自动停止化灰电机。
6 结束语
本系统已投入实际运行,自投入运行以来,控制系统运行稳定可靠,设备工作状况良好,使用及维护简捷方便,各项指标均达到了设计要求,操作人员的工作量和劳动强度大大降低,能源和设备的利用率得到提高,解决了氧化铝生产环境差,设备分散、复杂、难以控制的难题,同时实现了节约能量、降低能耗,受到厂方的好评。
声明:本网站所收集的部分公开资料来源于互联网,转载的目的在于传递更多信息及用于网络分享,并不代表本站赞同其观点和对其真实性负责,也不构成任何其他建议。本站部分作品是由网友自主投稿和发布、编辑整理上传,对此类作品本站仅提供交流平台,不为其版权负责。如果您发现网站上所用视频、图片、文字如涉及作品版权问题,请第一时间告知,我们将根据您提供的证明材料确认版权并按国家标准支付稿酬或立即删除内容,以保证您的权益!联系电话:010-58612588 或 Email:editor@mmsonline.com.cn。
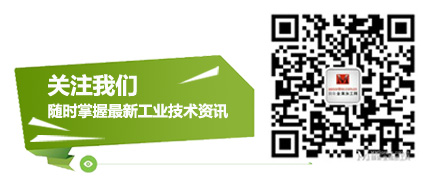
- 暂无反馈