中国造船技术主要差距与应对措施
【编者按】船舶业要想持续第一,就要培育一批具有自主知识产权的船舶配套设备自有品牌,加快发展船舶关键设备和材料的制造水平,提高高端造船装备的攻关技术。鼓励船舶配套企业的兼并重组,改变“多而散、小而弱”的行业格局,提升船舶配套行业整体竞争力。
自2010年以来,中国造船完工量、新接订单量和手持订单量三项指标连续三年位居世界第一。中国造船行业飞速崛起,技术水平有较大提高,但与世界先进造船国相比还存在较大差距。造船是劳动、技术、信息和资本密集型行业,在全球市场一体化的今天,各国造船企业在技术、性能、质量和服务等范围内展开了全方位的角逐。中国造船行业虽然在“量”上领先,然如何从“量变”到“质变”,并针对与国外造船技术主要差距采取应对措施,真正从造船大国迈向造船强国很值得研究。
主要差距
设计开发能力不足
自改革开放以来,中国先后引进100多项船舶和船用设备设计制造技术,但多数造船企业并未重视对引进技术的消化吸收和自主创新,中国船型设计开发能力仍显不足。
设计技术落后。船舶设计软件大多依赖国外引进,造船核心技术的知识产权归属国外造船强国;自主设计船舶往往用钢量偏高,经济指标偏低,生产设计深化程度约为发达国家的50%~60%,设计差错率则远远高于发达国家。在所造船舶中,自主开发产品不多,大多船舶的原始设计来自国外,特别在高新技术船舶方面,仍未摆脱依赖船东或国外设计院所的被动局面。
船型开发薄弱。由于核心技术缺乏和对技术创新能力建设的不足,不少造船企业技术力量主要为应付生产任务,处于“先合同后设计,边设计边建造”和“来料加工”的被动局面,极少技术储备和技术开发。已开发的内河标准船型,主要考虑船闸通过率,而对航道水深利用率、码头岸线使用率和船舶载货量考虑较少,船东造船热情不高。
自主设计萎缩。能够自主设计和开发建造国际船舶16大类中的6类,有8类能够建造但只能购买设计。一些民营造船企业根本未设设计开发部门,靠拿他人的设计图造船,市场适应力更差。
精度控制技术薄弱
目前,日韩造船企业几乎达到分段100%无余量上船台,除艉柱分段外,所有分段精度控制成功率为80%~95%,大合拢间隙基本控制在5±3mm,最大为12mm。中国在精度控制技术方面与先进造船国相比,存在一定差距,部分造船企业分段造船大合拢间隙有时高达20~50mm。专家评价,中国造船企业在精度造船和综合管理水平方面要比日韩造船企业落后10年以上。
在造船模式方面,中国造船行业的整体水平大致处于国外上世纪90年代中期水平,由传统的“分段制造”向“分道建造”过渡阶段,而日韩造船企业已经处于壳舾涂一体化的“集成制造”阶段。在钢材利用率方面,日韩等国造船企业对原材料的利用率超过90%,中国为85%~88%。在区域涂装技术方面,中国船舶涂装工时消耗率为0.85h/m2,日本则为0.25h /m2,油漆材料消耗是日本的1.24倍。在区域舾装技术方面,日韩的预舾装率已达95%左右,中国只有70%。
造船生产效率低下
中国造船行业生产效率大大低于发达国家。有资料表明,造船行业生产效率约为发达国家的1/7~1/10,若按人均产值或人均产量对比,仅为发达国家的1/20或更低些。有研究资料指出,目前9家大型造船企业的造船水平与国外的差距约为14年。在人均年造船吨位、人均年产值和生产效率3项指标上,造船企业与国外先进造船企业相差5~7倍。据测算,如果日本生产效率为1,韩国为2/3,中国则只有1/7~1/5。中国在分段建造过程中尚未做到跟踪补涂,分段二次除锈比例达60%~80%,甚至达100%,涂料消耗系数达1.9~2.0。而日韩造船企业普遍采用机械化钢板预处理、分段制造过程中跟踪补涂方式,分段二次除绣面积在20%以下,涂料消耗系数仅为1.2~1.5。中国造船企业的大量浪费、重复施工和返工,使工时浪费达55%,实际工时约为日本造船企业的8~10倍。
信息集成技术欠缺
上世纪90年代中期,日本大型造船企业在推进计算机集成制造技术的实体化应用上取得重要进展,节省人工50%,缩短工期20%。韩国造船行业采用TRIBON系统,使设计周期缩短25%,建造周期缩短10%。中国造船行业自上世纪80年代初开始实施CASIS、CADIS、CMI-S的3C工程,为中国造船行业在信息化建设中打下技术和思想基础。但由于条件限制和发展局限性,中国信息集成技术方面存在如下问题。
缺乏标准体系。技术、管理和工作标准体系的缺乏,造成各造船企业制定的实用标准有局限性,影响企业信息化的建设发展。
设计与生产脱节。设计院所和造船企业的脱节以及传统习惯的影响,造成诸多重复劳动和错误的出现,并行协调(设计院所与造船企业,造船企业内部生产部门之间)不够顺畅,生产效率和产品质量跟不上形势要求。
代码和接口标准不统一。代码不统一造成行业内部、企业之间和企业内部在信息化建设中资源共享困难。接口标准不统一使信息数据重复输入,数据错误率上升,降低信息资源的利用率,出现资源浪费和信息“孤岛”。
仿真技术研究和应用深度不够。难以将分散在大量设计图上的二维信息汇总成三维图像系统;无法实现利用计算机进行设计信息验证、开发高精密度的产品以及从构件自动展开到用于船体材料切割的参数自动输出等高效流畅的信息一体化;无法满足对船舶结构、管系、舾装、电力布置、虚拟仿真、生产计划、设备采购进行集成和简化的要求。
配套设备认知度低
长期以来,中国在船用设备领域研发投入严重不足,船舶配套业总体技术水平严重滞后;船用核心部件大部分需要依赖从国外进口解决;部分产能是授权许可证生产,产量满足不了需求;自行设计制造的部分船用设备产品品牌认知度很低,无法在世界范围内享受维修等配套服务,从而得不到国际船东的认可,只能为沿海小型船舶和内河船舶配套。据统计,中国造船行业配套设备本土化率平均不到40%,其中,万吨级轮船的柴油机本土化率不到20%;重要电子系统的本土化率不到17%。而日本造船行业配套设备本土化率达98%~100%,韩国超过90%。
目前,国际海事新规频繁出台,产品升级换代迫在眉睫,国际上绿色环保、节能减排、安全可靠、智能化和集成化的船舶及海工配套产品不断出现,更新换代速度明显加快,对船舶配套技术提出了更高要求。中国众多造船企业基本上是“组装厂”,船舶配套业自主研发能力薄弱,船舶关键设备和系统长期依赖引进。日韩和欧盟等加大技术研发力度的同时,加强对中国技术封锁,为占领船舶配套市场采取低价竞争策略,给处于不利地位的中国船舶配套业带来严峻挑战。
生产管理方式落后
中国大部分造船企业基本上还是沿用计划经济体制下的传统管理模式,在管理信息化方面没有从管理理念、组织模型和业务流程等根本问题上进行改造,而仅仅是在原有管理方法下采用信息技术手段。先进的造船技术要求船舶的基本设计、船体结构设计、舾装工程设计、全船和区域的综合布置设计,三维立体模型的共用数据库和各车间的生产信息等都实现计算机化,达到制造过程的标准化和模块化,自动化和半自动焊接技术几乎覆盖所有焊接作业。中国造船企业在生产管理、物料需求和供应管理、资源计划和生产成本控制等方面远远落后于现代造船行业的发展要求。
应对措施
加大设计开发创新
造船企业可以通过投资和并购欧美、日韩大型造船企业和船舶设计院所来迅速掌握海工装备、高技术船舶、配套设备等领域的先进技术。船型开发应服务于船东和造船企业的实际需求,加大对关键共性技术的研发力度。国家有关主管部门应建立设计资质管理机制,对船舶研发机构“扶优汰劣”。造船企业可以建立扶持基金,拓展高端船舶产品的研发空间。
建立行业规范标准
2008年国际金融危机爆发以来,中国造船行业遭遇1000多起涉外贸易纠纷,在这些案件的仲裁中,中国造船企业95%败诉。究其原因除了以伦敦作为海外主要仲裁地和缺乏合同意识外,最主要是中国造船行业缺乏规范的行业标准,而日韩造船企业鲜有此类麻烦,其做法值得借鉴。2002年,日本成立旨在提高日本造船行业国际竞争力的智库组织“造船产业竞争战略会议”,旗下拥有日本船舶标准协会、日本造船工业会、日本舶用工业协会和日本舶用机关整备协会等30多家外围团体,负责制订日本造船行业的竞争战略及船舶标准,参与应对及处理WTO、OECD等国际组织中涉及日本及第三国的造船纠纷,研究韩国、中国造船行业发展动态。中国应建立造船行业标准体系,包括技术标准体系、管理标准体系和工作标准体系。应统一代码和接口标准,建立和充实相关数据库,实现造船行业内部、企业之间、企业内部在信息资源共享,信息集成能自动更改设计错误,自动无缝抽取有关信息生成物料清单以供后续工序或管理软件应用。
提高制造业水平
从提升造船效益和打造企业核心竞争力出发,中国船舶配套企业需重视造船装备水平的提升,重点依托中国市场需求,推进关键船舶配套设备、海工装备专用系统和设备以及特种材料的制造,提高产业核心竞争力。
声明:本网站所收集的部分公开资料来源于互联网,转载的目的在于传递更多信息及用于网络分享,并不代表本站赞同其观点和对其真实性负责,也不构成任何其他建议。本站部分作品是由网友自主投稿和发布、编辑整理上传,对此类作品本站仅提供交流平台,不为其版权负责。如果您发现网站上所用视频、图片、文字如涉及作品版权问题,请第一时间告知,我们将根据您提供的证明材料确认版权并按国家标准支付稿酬或立即删除内容,以保证您的权益!联系电话:010-58612588 或 Email:editor@mmsonline.com.cn。
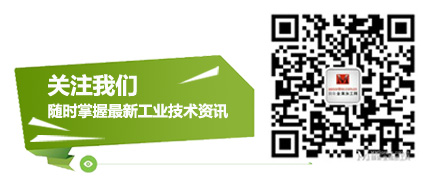
- 暂无反馈