碳参杂涂层在摩擦学的应用前景
金属材料热变形的目的是降低材料的变形抗力,提高塑性,有利于成形过程的稳定进行。传统的热变形方法通常是将坯料从加热炉内移至冷模或预热的模具中进行。在多数情况下,热变形时的模具预热温度远低于坯料温度,在成形过程中,由于坯料与模具之间的温差较大,会使坯料温度急剧降低,导致材料变形抗力增加,塑性降低。尤其是对于小型零件或表面积与体积比很大的的带窄肋,薄腹板的零件,薄壁处温度的降低是非常快的。
在成形过程中,坯料温度的降低会引起材料塑性流动能力降低,变形抗力提高,不仅使设备功率增加,增加成本,降低模具的使用寿命,而且由于材料变形温度的降低,会在坯料中产生不均匀的温度场,形成难变形区或局部变形区,从而引起材料组织与性能的不均匀。虽然通过将坯料加热到实际变形温度以上,或经过多火次成形,可以适当解决坯料在变形过程中温度降低的问题,但是,这样不仅浪费能源,增加坯料的加热时间,引起金属组织粗大,塑性和强度降低,并且由于零件表面氧化层,脱碳层或其它缺陷层加厚,需要加大加工余量,从而使材料利用率降低,增加了机械加工的工时,以及零件的制造成本。这一点对于有色金属材料表现得更为突出。
等温成形的工艺实质
等温成形是一种新兴工艺,它与常规成形的主要不同点在于,等温成形是把模具的温度控制在和毛坯加热温度大致相同的范围内,使毛坯在温度基本不变的条件下完成成形的全过程。
这种工艺由于减少或消除了模具激冷和材料应变硬化的影响,不仅变形抗力很小,而且有助于简化成形过程,以及可能生产出满足复杂零件要求的精密锻件。因此,等温成形具有材料利用率高,机械加工费用少,适用范围广等突出的优越性。
随着航空工业的迅速发展,将更多地使用钛合金。但是由于钛合金的锻造温度范围窄,变形抗力大,用常规的成形方法成形很困难。钛合金的流动应力随着变形温度的降低或变形速度的增加而迅速增大,因此,等温成形是最适用的。
等温成形工艺的特点
等温成形由于克服了常规热变形过程中坯料温度变化的问题,因此具有如下一些特点:
降低材料的变形抗力
在等温成形过程时,由于坯料与模具的温度基本一致,因此坯料的变形温度不会降低,在变形速度较低的情况下,材料软化过程进行得比较充分,使材料的变形抗力降低。此外,也可以使用具有一系列优良的工艺和使用性能的玻璃润滑剂,进一步降低变形抗力,可选用占用空间小,节约能源的低功率设备。
提高材料的塑性流动能力
等温成形的突出特点之一是可提高材料的塑性流动能力。由于等温成形时坯料温度不会降低,而且变形速度是比较低的,从而延长了材料的变形时间,可使材料的软化过程充分进行,提高材料的塑性流动能力,并使缺陷得到愈合。这就使形状复杂,具有窄肋,薄腹零件的成形成为可能,也为成形低塑性的难变形材料提供了有效的手段。
成形尺寸精度高、表面质量好、组织均匀、性能优良
等温成形时,由于坯料变形温度基本保持恒定,可以使材料在较低的变形温度下进行成形加工,而且可以采用一火次成形。等温成形时的坯料加热温度比常规热变形低 100~400℃,加热时间缩短2/3~1/2,从而减少了氧化,脱碳等缺陷,提高了制品的表面质量。由于坯料内温度分布比较均匀,在良好的润滑条件下 可使坯料的变形均匀,因而产品组织比较均匀,可以得到最佳的使用性能。此外,由于材料变形抗力低,变形温度波动小,从而减少了模具的弹性变形,有利于制品几何尺寸的稳定与控制。当采用较低的变形速度进行成形时,由于材料的软化过程比较充分,故使成形件的内部残留应力小,从而使成形件在冷却以及热处理过程中变形减小,提高了制品的尺寸精度。
模具使用寿命长
虽然等温成形,尤其是等温成形时所用模具材料及加工费用较高,加工精度的要求也较高,但是在等温成形过程中,由于模具是在准静载荷,低压力,无交变热应力条件下进行工作的,并且可以使用一系列具有优良的工艺和使用性能的润滑剂,因此模具的使用寿命比常规热变形模具高。等温成形零件通常采用一道工序进行成形,只需要一套模具,而常规热变形一般需要多道工序,需要多套模具。 因此,总体来说,采用等温成形可提高模具使用寿命,降低模具成本。
材料利用率高
等温成形可以通过减少加工余量,提高产品尺寸精度来减少金属消耗。例如,生产同一涡轮发动机零件,等温成形所用的原料只有常规热模锻的1/3左右。
螺旋桨零件的工艺分析及模具结构设计
螺旋桨锻件的工艺分析
螺旋桨锻件是舰艇推进器的关键零件,不仅要有高的力学性能,而且外形复杂,主轴上的6个桨叶在径向上呈发射形,且扭成倾斜角度 50℃,从叶根部分厚度 4 mm逐渐减薄到叶顶部分厚度 1。5 mm。这样的零件形状除了采用高速锤成形方法之外,还可采用等温成形。前者需要高速锤设备,后者要设计专用的等温成形模具,在投资方面,后者比前者节省。
螺旋桨模具结构设计
根据螺旋桨的几何特征,模具的分模面必须在桨叶的轮廓线上,这样,凹模就要用组合镶块的结构,等温成形后的锻件才能脱模。由于桨叶是螺旋面组成的,故分模面也为与之相应的空间曲面。
声明:本网站所收集的部分公开资料来源于互联网,转载的目的在于传递更多信息及用于网络分享,并不代表本站赞同其观点和对其真实性负责,也不构成任何其他建议。本站部分作品是由网友自主投稿和发布、编辑整理上传,对此类作品本站仅提供交流平台,不为其版权负责。如果您发现网站上所用视频、图片、文字如涉及作品版权问题,请第一时间告知,我们将根据您提供的证明材料确认版权并按国家标准支付稿酬或立即删除内容,以保证您的权益!联系电话:010-58612588 或 Email:editor@mmsonline.com.cn。
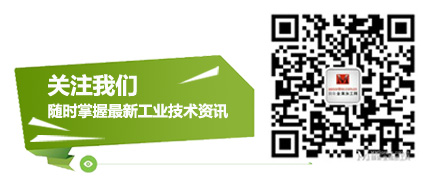
- 暂无反馈