车用复合材料--更轻更灵活的解决方案
【编者按】Frost & Sullivan公司在2012年发表的一份报告中指出,车用碳纤维复合材料的市场价值到2017年可能会增长到9550万美元,年复合增长率(CAGR)达30.6?%。这份题为《车用碳纤维复合材料市场供应链分析》(Supply Chain Analysis of the Automotive Carbon Fiber Composites Market)的研究报告指出,2010年这一市场的总收入已经达到了1470万美元。Frost & Sullivan表示,燃油效率和低碳排放法规在促进车用轻量复合材料部件替代金属部件方面发挥了重要作用。
Frost & Sullivan的资深研究分析师Sandeepan Mondal预计,热塑性塑料比热固性材料更有优势,因为它们比热固性塑料更容易回收。由于废弃物法规和零部件回收的能力对材料选择的影响越来越大,这一点就变得加重要了。
市场对这两种材料的巨大需求成为两宗重大收购事件的主要推动因素。最近的一次发生于2013年1月,荷兰TenCate公司表示即将收购Amber复合材料公司(Amber Composites)。这家荷兰公司发表了一份声明说:“全球复合材料市场的一个主要组成部分就是热固性材料,TenCate在这一市场的主要业务集中于航空、航天和雷达整流罩的应用领域。”
TenCate补充说:“收购Amber复合材料公司将帮助我们加快在欧洲热固性复合材料市场的业务推进。因此,收购Amber后,TenCate在欧洲的热固性和热塑性复合材料领域及其主要下游市场——工业和车用复合材料、模具材料和航空航天市场——增大了市场占有率。”
第二宗收购在2012年,Cytec收购了Umeco。Cytec工业材料公司(Cytec Industrial Materials)全球汽车市场经理Alexander Aucken说:“这次收购有助于我们实现在工业材料(包括汽车)市场设定的增长目标,这一市场拥有巨大的增长潜力和价值创造空间。”
在收购完成之前,氰特已经像他所说的“拥有热固性和热塑性复合材料的全系列产品。” Umeco的生产能力将有助于氰特发展和扩大它的产品系列。
Aucken没有透露氰特在车用热塑性塑料和热固性塑料方面的发展策略。但是他说:“我们在工业汽车市场的战略规划制定地非常周详,而且进展顺利。我们与捷豹路虎(Jaguar Land Rover)的联盟是该战略规划的一部分。汽车市场不断变化,我们在高端汽车和赛车市场供应先进复合材料的悠久历史正在延续,并且还在不断开发新的复合材料以满足市场的需求。适于量产的材料、生产工艺和自动化工艺的开发,以及供应链的集中管理,是我们未来在这一市场与捷豹路虎以及其他与我们合作的汽车公司共同增长的基石。”
Aucken认为,随着汽车工业在复合材料设计和生产方面不断获取经验,复合材料的使用以及对结构一体化的需求将会越来越多。把正确的材料应用到正确的应用中,再把他们连接起来,也就是采用相互匹配的模具、热固性复合材料(预浸料模压成型和树脂传递成型/RTM)及热塑性复合材料。这种做法让多材料汽车解决方案逐渐成为行业规范。
优点和缺点
同时拥有热固性和热塑性材料两方面的经验一定会给Cytec和TenCat带来巨大的帮助,因为有些设计者喜欢用热固性材料,而有些喜欢用热塑性材料。亨斯迈先进材料公司(?Huntsman Advanced Materials)的市场经理Klaus Ritter解释说,部件设计的过程通常也是评估每种复合材料的好处和坏处的过程。
“热塑性复合材料具有三大优势。”Ritter说,“首先,热塑性塑料加强的抗冲击性能是热固性复合材料无法匹敌的。热塑性塑料可以加快预浸渍纤维材料的加工速度,最重要的是,它拥有随时进行产品重塑的能力。但是,由于热塑性塑料原本是固态的,纤维的浸润比较困难。浸润需要用到特殊的技术和设备。这相对地提高了预浸渍的成本,而加工所需温度较高,也增加了日常生产成本。”
Ritter继续说到:“热塑性塑料的其他缺点包括其蠕变性和较高的内部张力,这是由于热塑性塑料和增强纤维从很高的加工温度冷却下来时,它们之间不同的热膨胀引起的。而单向增强件的问题就比较小,复杂的三维形状就存在很大的问题,还会导致表面质量的下降。”
“热固性复合材料的加工时间通常比较长,现在可以采用热压罐外高压RTM(树脂传递成型)快速成型方法实现五分钟循环(一分钟注射,两分钟固化),对于不太复杂的压塑成型操作,每个部件只需要两分钟(固化只需要一分钟)。”他说。
据Ritter介绍,在结构应用中,纤维增强环氧树脂制成的热固性复合材料的机械性能和抗腐蚀性能“甚至比金属部件还要高,重量则比金属轻得多。热固性复合材料良好的纤维浸润性能和相对较低的加工温度有助于降低投资成本,并保持最佳的产品质量和机械性能。”
Ritter称,热固性复合材料具有最低的蠕变变形,它们“将外形和功能结合在一起,制造出非常轻的结构部件。无论汽车零部件是碳纤维外观还是喷涂表面,都可以得到非常好的表面质量。然而,毒性问题通常被看作几种热固性材料系统的一个缺点。”
据迈图专用化学品公司(Momentive Specialty Chemicals)全球运输市场部总监Francis Defoor说,热固性或热塑性材料哪种更好,这个提问本身就是错误的。他说,“这是一个比简单地选择一种树脂和一种增强材料更为复杂的问题。要根据特定的应用和环境选择合适的材料。材料的选择取决于你是需要一个很好的装饰部件还是结构部件;是要适应特定的几何形状还是满足特定的成本目标。”
Defoor赞同传统热固性树脂需要长时间固化的说法,但是现在可以实现两分钟一次的加工周期,且不牺牲其他性能。在一篇标题为《下一代车用复合材料结构量产用先进热固性基体树脂技术》(Advanced Thermosetting Resin Matrix Technology for Next Generation High Volume Manufactureof Automotive Composite Structures)的论文中,Roman W. Hillermeier博士、Tareq Hasson博士、Lars Friedrich?和Cedric Ball认为,环氧复合材料可以与传统材料去竞争的,例如钢和铝。
在这篇文章的摘要中,作者们称:“…新技术是独一无二的,因为它们具有足够长的注射加工窗口,可以很好地浸润增强纤维,同时还可以实现极短的固化周期。这项研究的结果表明,采用现在的创新树脂材料和加工技术,结构复合材料部件能够以较低的成本进行大批量生产。”迈图公司表示,新推出的快速固化系统EpikoteTM Binder 05475/Epikure 05500固化剂,能够借助RTM或液体压缩成型工艺帮助汽车制造商实现更高的生产率。
塞拉尼斯公司(Celanese)的工程塑料业务泰科纳(Ticona)认为,热塑性塑料带是减轻重量的关键。
在2012年JEC美国复合材料展览会上,泰科纳的技术投放经理(technology launch manager)Michael Ruby发表了一篇关于玻纤增强热塑性复合材料单向带的技术文章,文章的题目为《采用单向织物和单向层压带提高D-LFT复合材料的冲击性能》(Improving impact performance in D-LFT composites with UD-Tape based fabrics & laminates),该文概括了泰科纳在汽车车身底板护罩(underbody shield,英文简称UBS)方面的研究,描述了提高复合材料硬度/强度和抗冲击性能的方法,即采用连续原丝、玻纤增强热塑性复合材料单向带生产纤维织物以及定制层压坯料。
泰科纳认为,热塑性聚合物与连续纤维复合材料结合使用,可以生产出轻量且耐用的部件。泰科纳说,这些部件能够减轻重量、降低成本,而且能够在极端环境下使用。
该公司开发了一种采用长纤维增强热塑性复合材料在线配混技术(D-LFT)制成的汽车车身底板护罩。所用复合材料采用连续纤维半成品织物和层压材料增强,以提高硬度和抗冲击性能。
碳纤维
企业之间竞争的增强和更快的固化周期很可能会促使更多的汽车设计者采用增强聚合物。部件的整合已经进行了很多年。正如Axon汽车公司(Axon Automotive)正在证实的,此领域内还有很多工作可做。
英国公司Axon开发了一种城市汽车,这款B级车尺寸的车型大小非常接近于雪铁龙C1,但是据说整个车身框架的重量只有50公斤。
轻型汽车可以将油耗和尾气排放降到最低,市场对轻型汽车的需求促使该公司开发了“黑车身”碳纤维复合材料系统。据说,一辆城市汽车的“黑车身”系统仅重50公斤;一辆中型轿车则仅重80公斤。Axon还说,能够快速建立经济性汽车平台的方法,还有可以随着需求变化而增加的最佳初始产量有着巨大的发展潜力。
“结构整合度越高,需要制造的部件就越少。”Axon公司总经理Steve Cousins解释说。
Cousins说,在一副经典的白车身中有350个部件,而Axon公司的黑车身中的部件数量则较少,制造速度要快得多。据Cousins介绍,一个3米高的横梁只需要10分钟的灌注成型时间。
Axon采用Axontex技术制造非常轻但强度和硬度非常高的复合材料结构梁。该公司表示这一系统不仅能够满足所有的硬度和碰撞标准,而且可以在外部车身板中采用任何你所需要的材料,从钢材到热塑性塑料以及介于两者之间的任何材料。该公司与斯高特巴德(Scott Bader)合作开发的碳纤维复合材料树脂系统Crestapol 1250 LV已被用于其城市汽车的车身框架中,用以实现更低的成本和更高的强度。
福特汽车公司也在使用碳纤维材料,该公司正与陶氏汽车系统(Dow Automotive Systems)合作研究先进的碳纤维复合材料在量产车中的应用。福特公司提高燃油效率战略的主要内容之一就是,到2020年,将新的汽车和卡车重量减少750磅(约340公斤)。
福特公司首席技术官和副总裁Paul Mascarenas解释说,有两种方法可以减少汽车的耗油量:研究和创新。他们正在“研究如何提高燃油到动力的转化效率,以及降低动力传动系需要做的功。”
“福特主要通过减小发动机和电气设备的尺寸来解决转化问题,而整备质量的降低和动力学性能的提高才是降低能耗的关键。"他说,"福特正在对一系列新的材料、改进的设计流程和新的制造技术进行调查,它们能够令汽车满足日益严格的安全和质量标准,同时减轻重量。”
“我们通过使用轻量高强度的聚合物和结构连接技术已经取得了一定的进展,因此与福特公司的合作顺理成章。”陶氏汽车系统研发总监Florian Schattenmann补充说。
陶氏汽车和福特公司已经签订了一份合作开发协议,双方将在几个领域内展开合作,携手研发。这个研发团队将致力于建立一个经济的车用碳纤维资源,并开发适合量产车的零部件制造方法。这次合作将结合协议双方最突出的优势,包括福特在设计、工艺和量产车生产上的能力和经验,以及陶氏汽车在研发、材料科学和聚合物量化加工方面的优势。
这次的联合开发还将利用陶氏化学公司通过与土耳其碳纤维生产商AKSA以及美国能源部橡树岭国家实验室(ORNL)的合作所展开的研究工作。
如果这次的合作能够获得成功,那么碳纤维零部件可能会在本世纪后期出现在福特的新车中。产品开发团队的目标就是满足50 mpg(英里/加仑)以上的新燃油效率标准,以及延长电动汽车的里程。
回收
现在设计者们在聚合物和增强材料的选择上非常挑剔。但是,位于英国Bristol市的国家复合材料中心(National Composites Centre)的业务支持工程师Nigel Keen说,相比于可回收的特性,加工速度才是目前对热塑性塑料最有利的因素。因为现在无论是热塑性塑料还是热固性塑料,都有了符合欧盟标准的回收解决方案。然而,回收仍然是一个难题,尽管汽车制造商在进行零部件设计时都已经考虑了这个问题。
据说,采用热固性材料可以实现百分之百的回收。Eco-Wolf公司市场销售部经理Bruce Ogilvy说,该公司的回收系统会变得越来越受欢迎,因为汽车行业面临着一个压力,那就是如何证明由热固性材料制造的零部件存在可行的回收方法。
“随着原材料成本不断增加,垃圾填埋的相关法规不断发展,对废弃物重新利用的能力变得越来越有吸引力。”Ogilvy说,“然而起初,用回收材料替代一定比例的纯料所节约的成本并不理想。因为,当垃圾填埋的成本降低时,其他的相关花费却增加了,所以,所降低的成本就成了主要的考虑因素。我们目前正与一些公司合作建立纤维回收工厂,既回收玻纤增强材料,也回收碳纤维复合材料。“
Eco-Wolf公司的回收系统主要包括两部分,一个是Eco粉碎机(Eco-Grinder),这台设备结构坚固,其专门的设计可在应对材料磨蚀性的同时保持玻纤或其他天然纤维的完整性。这使纤维得以重新添加到新产品中。
第二部分是一台Eco分散浸润机(Eco-Dispensing Macerator)。这是一台气动设备,可以将来自Eco粉碎机的材料计量后输送到已有的分散设备中,并从那里根据操作员的要求注射到树脂流中。Eco-Wolf公司提供一种适配器,可以重新利用废料而不改变树脂系统。
Ogilvy说Eco-Wolf“开发了一种独一无二的碳纤维加工方法,因为在碳纤维回收过程中无需进行加热,因此不会显著降低碳纤维的拉伸强度。”最终,设计者可能会被迫作出妥协。这是因为,聚合物和碳纤维材料的选择可能会在某种程度上取决于工艺实现自动化的难易程度。此外,尽管固化时间在某些工艺中已经缩短,但是在汽车工厂内引入一种新的复合材料生产工艺并不是简单地找出所有变量,例如设计、材料、尺寸和成本,就可以了。对于二次工艺的影响也必须有深入地了解,例如喷涂工艺。看着汽车制造商如何实现未来的减重目标是一件很有意思的事。
声明:本网站所收集的部分公开资料来源于互联网,转载的目的在于传递更多信息及用于网络分享,并不代表本站赞同其观点和对其真实性负责,也不构成任何其他建议。本站部分作品是由网友自主投稿和发布、编辑整理上传,对此类作品本站仅提供交流平台,不为其版权负责。如果您发现网站上所用视频、图片、文字如涉及作品版权问题,请第一时间告知,我们将根据您提供的证明材料确认版权并按国家标准支付稿酬或立即删除内容,以保证您的权益!联系电话:010-58612588 或 Email:editor@mmsonline.com.cn。
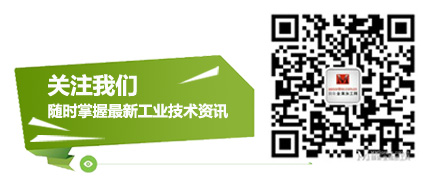
- 暂无反馈