铝合金模锻件的高速切削加工
随着加工制造业的飞速发展,铝合金高速切削成为企业的首选。一直以来,高速切削往往局限于铝板类毛料,由于铝合金模锻件余量不均匀经常会导致高速加工切削不连续,继而形成断续切削,对刀具磨损十分严重,同时会引起刀具折断从而打伤零件的现象。由于航空类铝合金零件生产中模锻件仍然是设计的首选毛料,为保证数控加工产能翻倍的目标,此类零件采用高速铣切加工势在必行。本文将以某机零件加工方案为例分析论证模锻件高速铣加工的可行性。
零件介绍
该零件为某机翼内骨架的重要组成部分,在机翼内起龙骨的作用,是重要受力件。该零件材料牌号状态为7B04 T74,外廓尺寸为2430mm×236mm×42mm ;零件上有2 个φ 12H9 工艺孔用于加工及装配时定位;腹板厚度为3~5mm,腹板上有10 个φ 76~116大小不等的通孔;缘条厚度尺寸为4.5mm ;整个零件中间13 根(厚度为3mm)加强筋。零件实样如图1 所示。
零件工艺性分析
零件材料属于高强度超硬形变铝合金,为Al-Zn-Mg-Cu 系合金,是一种可热处理强化的铝合金。它具有比强度高、断裂韧性好、工艺性能优良等特点,其相应的化学成分( 重量百分比) 为:5.7%Zn,2.3%Mg,1.43%Cu,0.2%Cr。其加热模锻的工艺特点是塑性较差、流动性差、粘附性大、模锻不易成形;并且对变形速度和变形程度十分敏感,随着变形速度的增加而急剧下降;锻造温度范围窄,始、终锻温度要求严格[1]。
锻件经过淬火及人工时效处理后σ b = 450~540MPa ;由于金属晶体间的各向异性,锻造过程中由于各部分冷热收缩不均匀以及金相组织转变的体积变化,使毛坯内部产生了相当大的内应力。毛坯内应力暂时处于相对平衡状态,切削去除一些表面材料后就打破了这种平衡,内应力重新分布,此时加工后的零件就明显地发生变形。
内应力指的是当外部的载荷去除后,仍残存在工件内部的应力。内应力因金属内部宏观的或微观的组织发生了不均匀的体积变化而产生,其外界因素就来自热加工和冷加工。具有内应力的零件处于一种不稳定的状态,它内部组织有强烈的倾向要恢复到一个稳定的没有内应力的状态,即使常温下零件也不断地进行这种变化,直到内应力消失为止。
残余应力是指受工艺过程的影响,在没有外力作用的情况下,在零件内部所残余的应力彼此保持平衡,零件切削加工后各部分残余应力分布不均匀,使零件发生变形,影响零件的形状和尺寸精度[2]。其产生的原因可分为3 种情况:
这种残余应力是零件在加工过程中最常出现的。当施加外载时,若零件的一部分区域发生不均匀塑性变形,卸载后该部分就产生残余应力;同时,由于残余应力必须在整个零件内达到自相平衡,致使零件中不发生塑性变形的那一部分区域也产生残余应力。
零件在热加工过程中常出现这种残余应力,这种残余应力是由于零件在热加工中的不均匀塑性变形与不均匀的体积变化而产生的。这种残余应力是由于从零件表面向内部扩展的化学或物理的变化而产生的,金属材料的化学热处理、电镀、喷涂等加工均属此例。
此零件属于典型的单面加工肋板类,零件加工以一面两孔定位,零件外形为机翼理论外缘,零件头部外形有33°闭斜角。零件内形相对开敞,可以用φ 30 以上刀具粗加工,零件底角半径R 为4mm,缘条与筋条间转角半径R 为8mm, 局部位置凸台与缘条间距离为8.5mm。
工艺方案设计
在普通数控铣加工中,由于采用低转速、低进给、大切深、低速加工的方式,零件变形比较大,零件粗加工后最大侧弯变形为6mm,最大翘曲变形为20mm,最大弯曲变形为5mm。
1 加工工序设计
为了满足产品尺寸精度及加工质量,在此设计出比较繁琐的工序来抵消零件变形带来的影响:
(1) 粗铣底平面,留工艺余量5mm;
(2) 制2 个φ 12 工艺孔至φ 10H 9;
(3) 以一面两孔定位粗铣零件内外形(内外形各留工艺余量5mm,腹板及缘条高度方向各留工艺余量5mm);
(4) 零件加热校正腹板底面平面度,保证在2mm 之内;
(5) 加工零件底面,去除工艺余量3mm(仍然保留2mm 工艺余量);
(6) 再次以一面两孔定位铣零件内外形(内外形各留工艺余量2mm,腹板及缘条高度方向各留工艺余量1mm);
(7) 零件加热校正腹板底面平面度,保证在1mm 之内;
(8) 加工零件底面,去除工艺余量,腹板底面到位;
(9) 扩大零件2 个工艺孔至φ 12H 9;
(10)以底面及两工艺孔定位精加工零件内外形。
为了满足加工要求,使用3 套工艺装备。其中一套为钻模,用于两次加工零件工艺孔;一套为数控用真空铣夹,用于零件粗加工;一套为数控用真空铣夹,用于零件精加工。
2 加工质量分析
(1)腹板弯曲变形比较大,平面度达到2mm,需要多次加热校正。
(2)尺寸精度在±0.3mm 之内,基本满足零件尺寸公差。
(3)表面粗糙度R a 大部分在3.2μm 之内,局部为6.3μm,甚至更差,需要钳工整体抛光处理。
(4)受切削力及切削热影响,内应力比较大,表面处理后的零件平面度有变坏的现象,同时伴有侧弯现象。
4 高速切削工艺方案特点
通常把切削速度比常规切削速度高5~10 倍以上的切削称为高速切削。目前高速铣机床加工铝合金切削线速度为1000~7000m/min。
在高速切削状态,随着切削速度的提高,切削力下降,加工表面质量提高;切削热大部分由切屑带走,工件基本保持冷态。而刀具寿命随着切削速度的提高而下降[2]。
与常规切削相比,高速切削具有下列优点:
(1) 加工效率高。随着切削速度的大幅度提高,进给速度也相应提高5~10 倍。金属去除率可达到常规切削的3~10 倍。同时机床快速空行程速度的大幅度提高,也减少了非切削的空行程时间,极大地提高了机床的生产率。
(2) 切削力降低。在切削速度达到一定值后,切削力可降低30%以上,尤其是径向切削力的大幅度减少,特别有利于薄壁细肋等刚性差零件的精密加工。
(3) 工件热变形减小。高速切削刀具热硬性好,95% ~98%以上的切削热被切屑飞速带走,工件可基本上保持冷态,可进行高速干切削,不用冷却液,减少对环境的污染,能实现绿色加工。
(4) 已加工表面质量高。高速切削时,机床的激振频率特别高,它远远离开了“机床- 刀具- 工件”工艺系统的固有频率范围,工作平稳振动小。
(5) 有利于保证零件的尺寸、形位精度。
(6) 能保证刀具和工件保持低温度,延长了刀具的寿命。在高速切削中切削量浅,切削刃吃刀时间短,进给比热传播的时间快。刀具和主轴上的径向力低。能减小主轴轴承、导轨和滚珠丝杠的磨损,对主轴轴承的冲击小。可以使用悬伸较长的刀具,振动风险小。
(7) 加工成本大大降低。高速加工提高了加工效率和加工质量,减少了打磨修整工序。
5 工艺方案设计
在高速切削加工中,由于采用高转速、小进给、小切深、高速加工的方式,零件变形小,粗加工后最大侧弯变形在1mm 之内,最大翘曲变形为3mm,最大弯曲变形为1mm[3]。6 加工工序设计以底面及两工艺孔定位精加工零件内外形,在此设计出比较简洁的工序:
(1) 粗铣底平面,留工艺余量2mm;
(2) 制零件2 个φ 12H 9工艺孔;
(3) 以一面两孔定位粗铣零件内外形(内外形各留工艺余量2mm);
(4) 校正底面,保证平面度1mm;
(5) 加工零件底面,去除工艺余量2mm,零件底面到位;
(6) 精铣零件内外形。
7 编程中的注意事项
(1)设置每层最大切深,分层加工。此类铝合金零件每层深度为3~5mm。
(2)设置拐角强制圆弧过渡。 走刀轨迹不能存在直角和锐角。保证刀具切削过程的连续性和平稳性。3 为“High Speed Milling”开关打开/关闭的区别(圆角半径1mm)。
(3)设置进退刀宏指令。
高速铣环切时经常使用螺旋进刀的方式。螺旋进刀即刀具的中心沿着一条螺旋线运动至零件的腹板表面的加工方式。这种方式减小了加工过程中零件对刀具的抗力,同时可以保证刀具的底刃在加工中能够切除移动轨迹上的零件材料。
退刀可采用轴向抬刀到安全平面或切向圆弧退刀方式。
8 加工质量分析
(1)腹板弯曲变形比较小,平面度控制在0.3mm 之内,满足设计要求。
(2)尺寸精度在±0.2mm 之内,满足设计要求。
(3)表面粗糙度R a 在3.2μm 之内,满足设计尺寸要求。
(4)内应力比较小,热表工序后平面度保持稳定。
2 种工艺方案对比
按照上述2 种工艺方案,从生产效率及加工质量2 个方面分析对比。
1 生产效率对比
按照普通数控加工方案需要10个工艺过程才能完成,而高速铣加工仅用6 个工艺过程;从工装使用上看,普通数控加工需要3 套工装,而高速铣加工仅用1 套工装;从加工效率上看,高速铣切削时间远低于普通数控铣切削时间。
2 产品质量对比
2 种方案加工的产品,质量也有很大差异。从尺寸精度看,普通数控切削后零件尺寸精度在±0.3mm之内,而高速切削后尺寸精度在±0.2mm 之内;从表面粗糙度看,普通数控切削后R a 在3.2~6.3μm 之间,而高速切削后零件表面粗糙度R a 在1.6~3.2μm 之间。其差异的重要原因在于切削过程中产生的积屑瘤及鳞刺的影响。
3 积屑瘤对尺寸精度的影响
积屑瘤是指切削钢、铝合金等塑性金属时,在切削速度不高,而又能形成带状切削的情况下,常常有一些从切屑和工件上来的金属冷焊(粘结)层积在前刀面上,形成硬度很高的楔块,它能够代替刀面和切削刃进行切削,这一小块称为积屑瘤[2]。积屑瘤减低尺寸精度和增加已加工表面的粗糙度。切削速度不同,积屑瘤所能达到的最大尺寸也不同。
4 鳞刺对表面粗糙度的影响
鳞刺是在已加工表面上的鳞片状毛刺。在较低及中等切削速度下用高速钢、硬质合金或陶瓷刀具切削常用塑性金属都会产生鳞刺,顺着切削方向、垂直于加工表面的鳞刺显微剖面。鳞刺是获得较小粗糙度表面的一大障碍。切削速度高,积屑瘤不再生成的情况下鳞刺的高度大大减小。可以获得已加工表面粗糙度小至R z0.1~0.05μm。
今后工作方向
铝合金模锻件高速铣加工必将成为今后此类零件切削加工的重要手段,实现其工作的必要条件是零件结构工艺性好、材料毛坯基准稳定、易于定位装夹、无人工干预的高效数控加工程序。无人工干预的高效数控程序不能简单地受技术人员的个体差异而影响,应该按照机床及其使用刀具逐步建立并完善切削参数数据库,保证所有技术人员的程序都能够适应机床的功率及扭矩的需要,同时要能够最大程度地发挥机床的切削效率。
结论
通过对上述2 种不同的切削方案进行对比和分析,可以得出以下结论:高速数控铣切加工铝合金模锻类零件无论从生产效率方面还是产品质量方面都有很大的提升,并且能够节约生产成本。高速铣切加工铝合金模锻类零件的工艺方案是可行的,而且它是一种环保的绿色加工方式,具有一定的先进性,值得在后续的生产中加以推广使用。
声明:本网站所收集的部分公开资料来源于互联网,转载的目的在于传递更多信息及用于网络分享,并不代表本站赞同其观点和对其真实性负责,也不构成任何其他建议。本站部分作品是由网友自主投稿和发布、编辑整理上传,对此类作品本站仅提供交流平台,不为其版权负责。如果您发现网站上所用视频、图片、文字如涉及作品版权问题,请第一时间告知,我们将根据您提供的证明材料确认版权并按国家标准支付稿酬或立即删除内容,以保证您的权益!联系电话:010-58612588 或 Email:editor@mmsonline.com.cn。
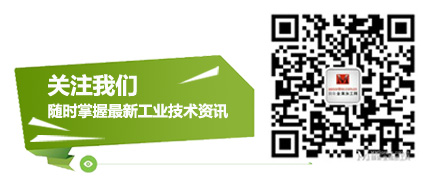
- 暂无反馈