工程轮辋的节能制造工艺
【编者按】工程轮辋这种成组冷滚压生产工艺的研制成功,为工程车轮行业带来一场节能环保的技术革命。成组冷滚压成形工艺生产多件式工程车轮工艺可行,高效、节能、环保,会给车轮行业带来巨大的经济效益,是工程车轮行业未来的发展趋势。
由于工程机械的使用场合环境恶劣,工程轮辋受力较大,一般工程车辆轮辋采用高强度厚钢板制造,钢板厚度为10~16mm,多件分别成形后焊接在一起而成。传统的成形需要加热,会造成能源浪费、空气污染、表面氧化皮缺陷及效率降低等问题。因此,如何提高生产效率、节能环保、降低成本是工程车轮行业首要研究的技术课题。
传统的工程轮辋成形工艺
传统的工程轮辋成形工艺,是把大板切成条料、卷筒、焊接制坯成圆筒,再热压成形,通过金属加工、装配,焊接成轮辋。其特点在于单件热压零件,再组装焊接。加热成形,造成能源浪费、效率低,热压氧化皮造成表面缺陷。热压成形工件如图1所示。
图1 热压工件
节能环保成形工艺
与传统工艺不同的是,节能环保成形工艺把热压成形改为成组冷滚压成形(见图2),再通过金属加工、装配,焊接成轮辋。这种工艺的特点在于两个零件成组同时冷滚压成形,然后切开成两个工件,从而提高了生产效率,也没有氧化皮造成的表面缺陷,达到节能降耗的目的。
图2 成组冷滚压件
经济效益分析
传统的工程轮辋用热压成形工艺,用液压机压形,用电或天然气加热,如一台功率500kW的中频电炉,每小时最多可以生产30件,班产量240件。两件组合后,只相当于120套车轮,每件的加热成本大约16元,每套32元。采用成组冷滚压成形技术班产量可以达到400套,效率提高三倍以上,而且不需要加热,表面质量好,减少了修磨。我国2011年生产大约30万台装载机,需要120多万套车轮。如果每套节约32元,一年可节约费用3840万元。
这种冷滚型工艺在商用车车轮和乘用车车轮行业已经普遍应用,但由于工程车轮轮辋太厚,对焊缝处理和冷滚型设备能力的要求较高,相对投资较大。热压容易成形,投资少,进入制造领域的门槛低,应用广泛,但不符合节能环保、绿色制造的理念。
声明:本网站所收集的部分公开资料来源于互联网,转载的目的在于传递更多信息及用于网络分享,并不代表本站赞同其观点和对其真实性负责,也不构成任何其他建议。本站部分作品是由网友自主投稿和发布、编辑整理上传,对此类作品本站仅提供交流平台,不为其版权负责。如果您发现网站上所用视频、图片、文字如涉及作品版权问题,请第一时间告知,我们将根据您提供的证明材料确认版权并按国家标准支付稿酬或立即删除内容,以保证您的权益!联系电话:010-58612588 或 Email:editor@mmsonline.com.cn。
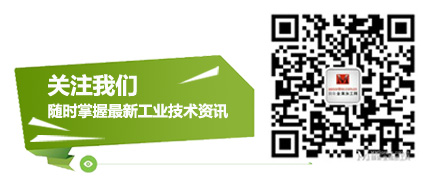
- 暂无反馈