《国家重大技术装备三十周年》成果
1983年7月12日,国务院下发《关于抓紧研制重大技术装备的决定》(国发[1983]110号文件),提出发展重大技术装备的战略任务,并成立了国务院重大技术装备领导小组,统一领导、协调重大技术装备工作。从“110号文件”出台开始,我国重大技术装备发展就被提升到国家战略的高度。期间陆续确定了包括“单机容量百万千瓦级的大型核电站成套设备”、“宝山钢铁总厂第二期工程成套设备”、“2000万吨级大型露天矿成套设备”、“30万吨乙烯成套设备”、“沙漠和海上石油钻采成套设备”、“大型煤化工成套设备”、“制造大规模集成电路的成套设备”、“三峡水利枢纽工程成套装备”、“超、特高压输变电装备”、“大型化肥成套设备”等国家重大技术装备国产化项目。根据各个阶段我国装备发展的具体情况,国家相继出台了《国务院关于加快振兴装备制造业的若干意见》、《装备制造业调整和振兴规划》、《国务院关于加快培育和发展战略性新兴产业的决定》、《高端装备制造业“十二五”发展规划》等政策措施,有力的促进了我国重大技术装备产业的发展。
今年恰逢“110号文件”发布30周年。三十年来,我国企业通过自主创新,对外合作,引进、消化、吸收、再创新,技贸结合等形式,开展了多项涉及我国国民经济命脉的重大技术装备的研制工作,使我国重大技术装备的发展具备了相当规模和基础,成为我国经济发展的重要产业。在此对这些成果进行梳理,汇总,以便总结经验,促进重大技术装备更好发展。
一、超、特高压输变电成套设备
1998年以后,我国在输变电设备制造领域依托三峡水电站送出工程、西北750kV交流输变电示范工程,全面掌握了500kV交直流和750kV交流输变电关键设备制造技术,使国内输变电设备的设计、制造和试验能力得以大幅度提升;依托1000kV特高压交流输电试验示范工程和±800kV特高压直流输电示范工程,成功研制了具有自主知识产权的1000kV特高压交流和±800kV直流输变电成套设备,实现了我国特高压输电装备的跨越式发展,确立了我国在世界特高压输电领域的领先地位。
(一)、±500kV高压直流输电工程和技术装备
直流输电工程在我国起步较晚,20世纪八九十年代建成的两个±500kV高压直流输电工程的设备和技术全部依赖进口。“九五”期间,根据三峡工程输电需求,国家依托三峡—常州±500kV直流输电工程开始开展研究,消化、吸收国外±500kV直流输电成套设备技术。后来通过三峡—广东、贵州—广东、三峡—上海等±500kV直流输电工程的建设,国内制造企业在直流输电装备制造技术和制造能力方面实现了跨越。先后通过联合设计、独立制造的方式研制了换流变压器、平波电抗器和大功率晶闸管元件,本土化率从开始时的30%逐步提升,在大功率晶闸管、换流阀制造和换流站成套设备与设计技术方面取得了重大的突破,自“灵宝背靠背”工程开始,实现了成套装备100%的本土化。彻底改变了高压直流输电设备依赖进口的历史。
(二)、750kV交流输变电工程和技术装备
2003年,国家将公伯峡水电站送出官亭—兰州东750kV交流输变电示范工程成套设备及“750kV交流输变电成套设备研制”列入“十五”国家重大技术装备研制项目。这是我国首个750kV交流输变电示范工程,在建设过程中,各相关单位应用数值分析、物理仿真、真型试验和现场测试等方法,研究并掌握了750kV交流输变电工程涉及的高海拔重污秽的绝缘配合、电网稳定和主变压器等全套电气设备的设计、制造、施工、调试以及电网安全自动控制等系列核心技术;自主研制了750kV自耦变压器、电抗器、断路器、隔离开关、避雷器、变压器套管、电容式电压互感器、绝缘子、自动控制保护、杆塔及金具、扩径导线和耐热母线等设备;首次采用Q420高强钢、扩径耐热母线、六分裂扩径导线和大吨位绝缘子等,全面掌握了世界上海拔最高(海拔3000m、长度140.7km)、运行电压最高的输变电技术。该示范工程的成套设备顺利通过了满负荷试验,运行安全可靠,实现了“一次性制造成功、一次性安装成功、一次性投运成功”的预期目标。项目成果荣获2007年度“国家科学技术进步奖一等奖”。目前,750kV交流输变电关键技术研究和核心设备的研制成果在后续建设的750kV工程中被广泛应用,750kV交流输电线路已成为我国部分电网的主网架。
(三)特高压输电工程和技术装备
特高压输电技术通常是指直流电压±800kV、交流电压1000kV及以上的输电技术。一回特高压交流线路可输电电力500万kW,是500kV交流线路输送能力的5倍;一回特高压直流线路可输送电力640万kW,是±500kV级直流线路输送能力的2倍,输电距离可达2500km。
1000kV特高压交流输电技术装备依托晋东南—南阳—荆门1000kV特高压交流输电试验示范工程开展研制工作,自主完成了1000kV主变压器、电抗器、全封闭组合电器、隔离开关、避雷器、变压器套管、电容式电压互感器、绝缘子、自动控制保护以及扩径导线等主设备的研究、试验和制造任务。通过试验示范工程的建设,我国特高压交流输变电设备的自主创新取得了重大突破,全面掌握了特高压交流输变电设备的核心技术,形成了完整的技术标准和试验规范,主要产品的设计、制造和试验达到了世界领先水平,创造了多项世界第一。
±800 kV特高压直流输电技术装备的依托工程包括云南—广东±800 kV特高压直流输电示范工程,向家坝—上海±800 kV特高压直流输电示范工程,锦屏—苏南±800 kV特高压直流输电工程,在世界上首次完成了±800kV直流输电工程的系统研究、成套设计和工程设计;确定了工程主接线、主设备型式、绝缘水平、无功配置等技术参数和方案,制定了特高压直流输电的功能规范和设备规范,首次编制了具有自主知识产权的特高压直流输电技术标准,在工程建设与设备研制中创造了多项世界第一。通过示范工程的国产化建设,使我国掌握了具有国际先进水平和自主知识产权的特高压直流输电成套设备设计制造的核心技术,工艺装备和综合试验能力跃居世界先进行列,形成了特高压直流输电设备批量生产能力,促进了国内企业创新能力、设计制造水平和管理水平的全面提升。
二、千万吨级大型露天矿成套设备
大型露天矿成套设备是为我国大型露天矿(煤矿、铁矿、铜矿等)剥、采、运工艺过程提供的成套装备,包括年产1000万t级和2000万t级露天矿单斗—汽车开采工艺及连续、半连续开采工艺的成套设备。
1983年,“年产千万吨级大型露天矿成套设备”被国务院《关于抓紧研制重大技术装备的决定》(110号文件)列为首批入选的项目。30年来,我国大型露天矿成套设备基本完成了包含间断、轮斗连续、半连续三种开采工艺,完成了年产1000万t级和2000万t级两个等级的成套设备研制,基本满足了我国大型露天矿的需要,把大型露天矿成套设备的设计和制造水平提高到了一个新的水平。
1000万t级大型露天矿成套设备采用自行设计研发的技术路线,主要攻关三套工艺装备及辅助设备:一是单斗—汽车工艺装备,包括钻孔直径为150、250、310mm牙轮钻机,8 m³、10 m³机械式矿用挖掘机(电铲)、100t电动轮矿用自卸车等主采设备;二是连续开采工艺设备,包括1500~2000m³/h斗轮连续开采成套设备,主要有斗轮挖掘机、装载机、胶带运输机、排土机、电缆车、漏斗车等装备;三是半连续运输设备,包括胶带运输机、卸料小车、自动控制系统等;实现了千万吨级露天矿“单斗—汽车”开采工艺成套设备的国产化,于1987年9月27日通过国家鉴定。
1988年8月,2000万t级大型露天矿成套设备被纳入国家重大技术装备大型露天矿成套设备研制项目。该项目采用国内自行研制与引进技术、合作生产相结合的技术路线,包括3个子项,39个课题。根据项目分工,各有关承制单位分别完成钻孔直径380mm的牙轮钻机,斗容为16m³、27 m³机械式挖掘机,154t电动轮自卸车,3600m³/h斗轮挖掘机成套设备。
进入21世纪后,我国大型露天矿成套设备在引进技术、消化吸收和自主创新方面持续发展,自行设计、制造及集成了更大规格的单斗—汽车成套设备,品种规格不断被刷新。相继研制成功了具有自主知识产权的220t、300t、363t等系列交流传动电动轮自卸车和斗容分别为55m³、75 m³的矿用挖掘机,标志着我国大型露天矿单斗—汽车成套设备产品实现了从“跟随”到“引领”的质的飞跃。
HMTK600B 型(363吨)电动轮自卸车是目前世界上吨位最大、整车性能最先进、运载效率最高的电动轮自卸车。整车长15.79米,宽9.45米,占地面积相当于两个羽毛球场地,高7.8米;其空车重量237吨,额定载重量363吨,整车满载重量600吨(相当于10节火车车皮的载重);额定爬坡度8-12%,最高车速64千米/小时,最小转弯半径17.8米。广泛适用于大型露天煤矿、铁矿及有色金属等矿山的物料运载,能够与35m³-75m³的电铲高效配套使用,满足矿山高效率、低能耗物料运载的需求。
WK-75大型矿用挖掘机主要用于各种大型露天矿山的采掘和剥离作业,是单斗挖掘机-卡车工艺系统(间断开采工艺系统)和单斗挖掘机-(卡车)-破碎站-带式输送机工艺系统(半连续开采工艺系统)中必备的采掘设备。该机总长37.5米,宽17.3米,占地面积比一个篮球场还要大;从履带到顶部,高23.5米;总重量近2000吨;既可与326~400t以上的矿用自卸车配套使用,也可以与9000吨/小时及以上自移式破碎站系统配套使用。一斗可以挖掘135吨的物料,最大生产效率达到12000吨/小时,煤炭开采量达500万吨/年。
三、煤矿综合机械化开采成套装备
煤炭是我国的主要能源,目前分别占我国一次能源生产和消费总量的76.6%和69.4%。近十年来,我国煤炭开发进入了高速发展期,产量逐年增加, 2012年全国原煤产量36.3亿吨,占世界煤炭产量的50%,位居世界第一,近十年来世界煤炭产量增长的80%是中国生产的,与此同时我国也逐渐变成了世界最大的煤炭消费国,这种形势带动了我国煤炭开发技术与装备的快速发展。
我国自建国以来,井工开采采煤工艺的发展历经爆破采煤工艺(简称炮采)①、普通机械化采煤工艺(简称普采)②、综合机械化采煤工艺(简称综采)③等阶段,70年代开始引进综采成套装备④,几十年来走出了一条引进、消化、吸收、再创新的煤炭综采装备的发展道路。回顾综采发展过程,大致可分为三个阶段,第一阶段自上世纪70年代初期至80年代中期,以引进、消化、吸收国外综采技术为主。1970 年1月28日, 我国引进的第一套全工作面综采设备在大同煤峪口矿8710 工作面开始工业性试验, 正式拉开了我国采煤史上一场影响深远的革命性变革的帷幕。第二阶段自上世纪80年代中后期至2003年前后,是中低端自主发展与高端引进的时期。在前期引进的基础上,我国逐渐掌握了综采装备的研制技术,进入自主生产阶段,综采装备在我国得到大面积推广应用,逐步建立了自主知识产权的综采工作面成套装备技术体系。但是国外在90年代初发展的以液压支架电液控制系统等为基础的综采装备长期以来一直占据我国煤机市场的高端市场部分。第三阶段自2003年前后至今,是高端综采装备国产化和自主创新阶段。国家在此阶段对煤炭开采装备技术的发展给予了很大支持,陆续组织开展了一系列技术攻关,取得了“年产600万吨综采成套装备技术”、“大倾角煤层综采综放成套装备关键技术”、“0.6m~1.3m复杂薄煤层自动化综采成套技术与装备”、“高端液压支架及其先进制造关键技术”、“年产千万吨大采高综采成套装备”和“大采高综采放顶煤⑤成套技术与装备”等一大批重大技术成果,支撑了煤炭工业的技术进步和快速发展。下面简要介绍三项重大成果。
1、600万吨综采成套技术与装备
2003年起,国家组织了“年产600万吨综采成套装备研制”的项目攻关研究,该项目是当年国家十项重大技术装备研制攻关其中之一,由煤炭科学研究总院、神华集团、天地科技股份有限公司和其它煤机骨干制造企业联合承接。总体目标是攻克3.5~6.0m煤层一次采全高成套技术与装备,实现工作面年产600万吨。该项目以大采高综采岩层控制理论研究为基础,遵循系统设备与单件设备可靠性相匹配、采煤机落煤能力与输送机能力相匹配的原则,自主研发高可靠性液压支架、采煤机、刮板输送机以及带式输送机,集成创新了由“一个理论、四套装备”(36个关键元部件、16项创新技术)所构成的具有自主知识产权的年产600万吨能力的综采成套技术与装备,特别是该项目研制的具有自主知识产权的SAC型液压支架电液控制系统,打破了国外企业在此领域对我国的长期垄断地位,并迅速占领市场,2012年市场占有率达到55%,使得国外企业的液压支架电液控制系统在我国的市场占有率从2007年的100%降低到2012年的30%,同时将液压支架电液控制系统的价格降低到2007年2/3左右。项目成果获得国家科技进步二等奖。
2、大倾角煤层综采综放成套技术与装备
大倾角松软等复杂煤层开采是世界性煤炭开采重大技术难题,为攻克这一技术难题,天地科技股份有限公司与山东科技大学和山东能源新汶矿业集团等单位合作,经过长期“产学研”联合攻关,突破了大倾角和急倾斜工作面支护系统稳定性、采煤机牵引系统下滑磨损和控制等技术瓶颈,创新了设备与围岩耦合设计核心技术,攻克了设备关键元部件可靠性技术,形成了一整套集工作面成套设备三维动态设计、优化配套技术和先进制造于一体的复杂煤层综采综放工作面成套装备关键技术。项目创新研制的新型大倾角工作面液压支架及电液控制系统、大功率大倾角电牵引采煤机、刮板输送机成套装备,实现了35°~56°大倾角复杂煤层的安全高效生产,达到国际领先水平。本项目自2008年起,在山东能源新汶矿业集团福城煤矿和华丰煤矿等22个单位推广应用,在35°~56°大倾角和急倾斜松软等复杂煤层条件下实现综采综放安全高效开采,项目成果获得国家科技进步二等奖。
3、特厚煤层大采高综放成套技术与装备
大同和内蒙等主要煤炭基地赋存有大量14~20m特厚煤层,解决这类煤层的安全高效开采技术和装备是煤炭工业发展中面临的重大难题,为攻克这一难题,经中国煤炭科工集团、郑州煤矿机械集团和大同煤矿集团等十几个单位组成的产学研用攻关联盟的联合攻关,取得了重大创新成果。
该项目实现了年产千万吨特厚煤层大采高综放工作面成套装备全部国产化,提高了成套装备的配套性、适应性及可靠性。2011年,项目在大同塔山矿8105工作面完成了工业性试验,年产量达到1084.9万吨。
目前,我国高端液压支架、重型运输设备等开采装备核心技术已经处于国际先进水平,综采放顶煤开采装备技术处于国际领先地位。
注释:
① 爆破采煤工艺:在长壁工作面用爆破方法破煤和装煤、人工装煤、输送机运煤和单体支柱支护的采煤工艺叫爆破采煤工艺(简称炮采)。
② 普通机械化采煤工艺:在长壁工作面用机械方法破煤和装煤、输送机运煤和单体支柱支护的采煤工艺叫普通机械化采煤工艺(简称普采)。
③ 综合机械化采煤工艺:在长壁工作面用机械方法破煤和装煤、输送机运煤和液压支架支护的采煤工艺叫综合机械化采煤工艺(简称综采)。
④ 综采成套装备:包括采煤机(破煤、落煤),液压支架(空间支护),刮板输送机(装煤、运煤),转载机,破碎机,乳化液、喷雾泵组(液压支架动力源,提供31.5或37.5Mpa出口压力的乳化液),变电组合开关(采煤机、刮板输送机等电控装备的动力源,提供127伏、660伏、1140伏或者3300伏电压等级的动力电源)、顺槽控制中心等装备。
⑤ 综采放顶煤工艺:厚煤层煤炭开采技术之一。在厚煤层中,沿煤层(或分段)底部布置一个采高2-3米的长壁工作面,用常规方法进行回采,利用矿山压力的作用或辅以人工松动方法,使支架上方的顶煤破碎成散体后由支架后方(或上方)放出,并经由刮板输送机运出工作面(简称综放)。
四、我国港口机械成套装备技术水平跻身世界前列
自我国建国初始至80年代末期,我国港口机械一直处于比较落后的水平,仅能够研制生产一些5-10吨门座起重机、桥式起重机等港口装卸机械,而集装箱和散货装卸机械主要依赖进口。德国、日本、韩国等国家的企业产品占据了全球95%以上的市场份额,控制了港口机械的核心技术。
近三十年来,我国港口机械科研单位和专业制造厂,结合港口建设发展需要,通过对关键技术和装备组织科技攻关,具备了独立自主开发各类现代港口装卸设备的能力,涌现了一批以上海振华重工(集团)股份有限公司(ZPMC)为代表的港口机械骨干企业。目前,我国研制的大型集装箱装卸机械装备不仅应用于国内港口,而且出口到世界其它80多个国家和地区,占世界各大港口的市场份额达70%以上。
近年来,我国研制的一批具有世界先进水平、掌握自主知识产权的核心技术重大装备已获得大量应用:
1、 集装箱港口起重机
我国研制的超特大型巴拿马型岸边集装箱起重机(一般外伸距大于40米的岸桥称为超巴拿马型岸桥),外伸距达65-73.75米、吊具下能够起重80吨的双40ft集装箱和120吨的三个40ft集装箱,目前已应用到世界各大港口。以此为关键技术的“新一代港口集装箱起重机关键技术研发与应用”获国家科学技术进步一等奖。
2、 散货港口装卸机械
我国自主设计完成的国内最大的连续卸船机-曹妃甸3800吨/小时链斗式连续卸船机于2012年5月交货。该项目成功研发了链斗式连续卸船机的电控系统,实现全国产配套,包括首创的破断力为550吨的提升链条和6米直径的超大回转轴承。打破了国外对大型散料连续卸船设备供应的垄断。
我国独立设计、制造的世界最大装船机于去年完成组装,用于巴西里约热内卢阿苏大港。该项目共有两台机组。该批装船机具有臂架伸缩、回转、俯仰功能,是目前世界上最大的装船机,每小时额定装船为12000吨,最大装载能力达每小时15000吨。
2005年建成的上海港外高桥集装箱码头全自动化空箱堆场是中国第一个集装箱无人堆场。新研制的自动化轨道吊,实现了港口的高效率、高可靠、低成本运作,建立了港口机械机电新技术结合的典范,揭开了世界港口发展集装箱堆场自动化的新篇章。
目前,中远太平洋有限公司、上海振华重工(集团)股份有限公司与厦门海沧投资集团有限公司合作的中远厦门远海集装箱码头第四代全自动化码头项目已进入研制阶段。该项目位于厦门海沧保税港区,码头长约538米,纵深约308米,设计吞吐量为78万~91万标箱/年,其吞吐能力相比传统码头增加20%~40%。整个作业流程实行 智能化控制,现场作业无人参与,本项目的建成是国内首个无人智能环保型全自动化集装箱码头,对全球自动化码头装卸系统升级换代将树立自动化集装箱码头的新模式。
声明:本网站所收集的部分公开资料来源于互联网,转载的目的在于传递更多信息及用于网络分享,并不代表本站赞同其观点和对其真实性负责,也不构成任何其他建议。本站部分作品是由网友自主投稿和发布、编辑整理上传,对此类作品本站仅提供交流平台,不为其版权负责。如果您发现网站上所用视频、图片、文字如涉及作品版权问题,请第一时间告知,我们将根据您提供的证明材料确认版权并按国家标准支付稿酬或立即删除内容,以保证您的权益!联系电话:010-58612588 或 Email:editor@mmsonline.com.cn。
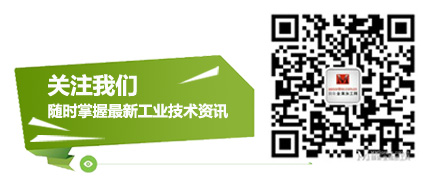
- 暂无反馈