切削刀片在火车轮车削时的结构优选法
【编者按】米哈伊洛夫·斯达尼斯拉夫·瓦西里耶为奇(科斯特罗马国立工艺大学)开发研制的新结构硬质合金刀片LNMX 301940,在车削异形工件时具有更高的寿命和断屑可靠性,并列出生产测试刀片在车削火车轮轮对工序时的结论。
在自动化生产中,金属切削工序的编制出现一个特殊问题,那就是切削刀具可靠性的提高和有利形状切屑的持久性获得。选择可塑材料的成型毛坯的车削工具有一重大难题。进给方向的改变导致运动切削力和剪切层截面尺寸的改变,在这些情况下,标准几何形状切削刀片像效果不大的铁块。这样的工序属于列车车轮的车削加工,车轮的备料来自专用钢,在加工时可控的混合切屑很难形成。通过研究,已磨损车轮使用的修复方法是轮对工作面外圆车削。已磨损车轮的可加工性由于硬化层(也称作滑履)的存在而急剧降低,这些情况发生在车轮与钢轨的急剧制动而产生的摩擦下。制造和修复火车轮是在专用的双刀架数控机床上进行的。轮圈轮廓的加工包括:与轴心45°进给加工倒角、辗压面的纵向车削和轮箍的轮廓(轮缘凸起部分,车轮在道轨上运动时的导向部分)的车削。
加工方式:吃刀量t = 5…7 мм,进给量s = 0,7…1,2 мм/об,切削速度v = 0,5…0,8 м/с.机车车轮的直径加工范围是750…1050 мм.在切削刀具的性质上,运用带立放装夹底座的左和右组合车刀。刀片做成对称性状,可以完全充分利用它们加工左右车轮。
加工车轮的基本问题包括,降低切削刀片的成本和切削操作中不可控带状切屑的生成。并且去除切削层上切屑对于提高刀具工作能力有着重要意义。操作测时表明,为了维持目前金属切削设备正常工作,由于加工时不良切屑形成,90%的情况下需要人为干预。长长的带状切屑缠绕在机床、刀具或零件上,挠伤轮子的已加工表面,堆满工作台,根据现场操作检查,这种加工过失是实际存在的,因此不能安排看管多机床的服务。同样存在新一代无人操作的车轮修整的自动化复合机床有效利用率的问题。
降低切削刀片的成本受到磨损车轮表面存在滑履的限制。在切削带有大量滑履的情况下,切削刃崩刃和刀片损伤的概率急剧增加。在机车车轮大批量生产的情况下,解决提高刀具工作能力和稳定获得有利形状切屑的课题有着重要实用意义。
解决这个课题最有效的途径是切削刀具结构的优选法。目前创造这样刀片的工作一直持续着,在大量的主要的工业试制研究中,一些主流公司提出了γ结构。现在推广的是沿切削刃周边做成负倒棱刃前角和折线形断屑槽的刀片(图-1)。
图-1 切削刀片LNMX 301940的标准几何形状;加工轮缘时切屑的形状;刀片前刀面磨损的特征
分析标准刀片的切削机制得出,在加工倒角和轮缘时切削层厚度а1 小于负倒棱刃的宽度,因此切屑绕过断屑槽以带状形状从车刀上流出。在纵向车削车轮表面时,接触可塑区域的切屑从断屑槽后壁流出,导致斜面上的切屑最多的弯曲变形并且增大切削力。一些数据结论证实了刀具前刀面的磨损特性——磨损月牙槽不在刀片的前刃面上,而是在断屑槽的凸台上。刀片的最大磨损处不由自主地处于与‘滑履’硬化层相互作用的区域,在这个位置发生裂纹,导致崩刃或刀片断裂。
除了刀具公司推出的带有折线形断屑槽的标准刀片和其它结构的可转位刀片。被广泛推广的是前刀面带有峰形花纹的刀片,这种花纹又被称作鱼骨。对这种刀片工作能力的研究表明,并不能成功解决加工倒角和轮缘区域时切屑折断的难题,而过度的切屑形变会导致切削力增大、出现震动、放射火花和降低刀具寿命。
分析火车轮的机械加工情况得出,试验途径探索到的最佳结构是立装夹持的可转位刀片,不考虑机械加工工艺与卷曲和折断的切屑的因果关系,不能够制定出可行的实际解决方案。在切屑成形的立体空间的控制和模型试验的基础上,或许可以得到有利形状的切屑,从而解决提高刀具寿命的问题。
在切削刀片设计时用的是系统分析法。对刀具观察得出,结构和功能方面之间存在必然的联系,并且构成统一整体。系统分析法提供了把刀具设计任务分成多部分并采取最佳方案的可能性。
根据刀具功能和结构特性的统计总和得出轮缘区域的特殊性,加工时的切削状况各不相同。确定了每次从这个区域脱离的切屑的最有利状况,计算刀片前刀面的几何参数,刀片刀刃工作时受到切削条件的变化不定以及刀具的耐磨性和强度的技术限制,使得切屑破碎存在折衷的解决办法。切屑卷曲和折断的预测在其工作中得到实现。
在轮缘剖面加工模拟的结果表明,剪切角改变4.1倍,剪切层的平均厚度和宽度在背吃刀量t=6mm的情况下分别改变2.5倍和2.4倍。在加工40°的倒角时参加切削的切削刃长度为11.1mm,在这个部分的剪切层厚度等于0.7mm。在滚道部分的外圆车削操作中,切削刃的长度减少到7.8mm,而剪切层厚度增大至1mm。随着0.4mm的剪切层厚度,在轮缘侧面的加工中参与的切削刃的最大长度为18.9mm(图-2)。
图-2. 火车轮轮边剖面加工示意图
不同的切削状况下,沿着刀片切削刃必将形成变化无常的参数,像硬化斜面以及与之毗邻的卷屑面。考虑到切屑形成的特点,在横向面纵向面都对称的刀片上,不同区域切削的刀片,其支撑面应当实现相应的收缩 。在结构中刀片能够随着刀片中心实现切削刃角度倾斜的分段变化。运用这个结构能够提高切屑的刚度,因此提高断屑的可能性,同样能够改善在“滑履”硬化层上切削刃切入的状况。使切屑变形的凸起部分位于刀片的周边的过渡区,这些凸起部分能够提高破碎宽厚切屑的稳定性,以及刀片的内部应力。
为了提高切屑的刚度和应力,在与正常的阻挠相互作用下必须保证切屑横切面相对于切屑螺旋面轴心回转。建立这些条件可以使切屑空间形成的控制方式,不仅依靠流出面,而且依靠前刀面和切屑横截面的卷曲。切屑形成的模拟过程显示,为了断屑稳定性,可以在减小主偏角的情况下合理的利用切屑向已加工面移动的自然走向。增大这些效果可以依靠建立特殊的沿切削刃变化几何角度的刀片形状。这样的前刀面可以实现可变的曲率以及前角的不断增大。切屑卷曲面的形状因刀尖附近的凸起部分而改变,从刀片的圆弧区域到中间凹陷的区域。用从刀尖削减的措施可以实现切削刃的曲线化和落差化。
在刀具的前刀面创造凹凸的良好的几何形状,这些球形凸起部分在刀具的工作能力中展现出很好的优势。切屑与刀具的接触面缩小,收缩率与切削力下降,有利地增加刀具寿命。刀尖的正前角不会降低刀具的强度,这样载荷在中部,在加工“滑履”的工序中相互作用,最大限度的增强有效切削刃的区域。可变的角λ与γ共同作用,在刀具切入“滑履”的情况下展示出良好的效果。刀具上的载荷不是瞬间的增加,而是逐渐增加。
为了缩小切削层厚度的范围,沿刀片切削刃需要在刀片三分之一位置处向刀片中间增加角φ,在加工轮缘时刀具平面角增加到 4°能够使中间的切削层厚度增加到0.08mm,也就是切削层厚度的分散范围减小到25?%。考虑到这种刀具的使用,倒角的最小宽度可以减小到0.4mm。
运用这些原理设计出了 LNMX?301940-60.用来批量测试的刀片已经用硬质合金РТ573, РТ33制成.刀片的测试已经在莫斯科轮对修复车间顺利完成。通过在生产条件下对刀片工作性能的研究得出,结构优选法能够提高刀具强度,并且能够在整个车轮轮廓加工中得到稳定的折断的切屑。在加工最宽的滚压面、倒角和轮缘顶端时发现,能够持续稳定的获得逗号形状的和双环螺旋线的折断的切屑。在问题最严重的部分——轮缘的型面车削中,顺利取得了折断的波浪形的切屑(图-3)。
图-3. 轮箍的加工和在最新结构刀片的切削下形成的切屑的典型形状
最新开发的复杂型面的刀片的结构,能够促使热机载荷沿刀具切削刃有利地分配,刀具的磨损相应均匀分配,从而提高刀具寿命。
刀具的车削耐用性,在高速切削时平均提高了3倍。运用这些新型的刀具提高了生产率和机加工可靠性,切削功率减少到30%。
声明:本网站所收集的部分公开资料来源于互联网,转载的目的在于传递更多信息及用于网络分享,并不代表本站赞同其观点和对其真实性负责,也不构成任何其他建议。本站部分作品是由网友自主投稿和发布、编辑整理上传,对此类作品本站仅提供交流平台,不为其版权负责。如果您发现网站上所用视频、图片、文字如涉及作品版权问题,请第一时间告知,我们将根据您提供的证明材料确认版权并按国家标准支付稿酬或立即删除内容,以保证您的权益!联系电话:010-58612588 或 Email:editor@mmsonline.com.cn。
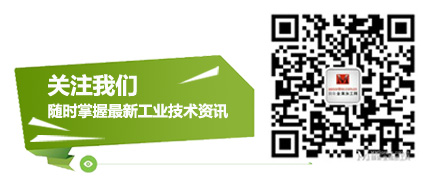
- 暂无反馈