制约制造业企业转型升级的瓶颈
作为老工业基地的重庆市,近年来大力推进传统制造业转型升级,一些企业纷纷上新设备、推新产品、拓新市场,但由于熟悉新设备、新技术的熟练工、技术工紧缺,使得新设备不能充分发挥效率,成为制约企业转型升级的一大瓶颈。
重庆秋田齿轮公司是一家变速齿轮制造企业,近年开始转向生产汽车、高档摩托车齿轮,并积极开拓海外市场,公司为此每年投入上千万元更新设备、开发新品,但技工短缺给企业升级带来了不小的障碍。公司副总经理李登平介绍,近3000名工人中,大部分是新招的农民工,技工不足10%,去年公司为加大高端产品出口,引进一批连线数控机床和新型磨床,但工人操作技能跟不上,影响到产品质量稳定性。
生产各类工程发电机的重庆赛力盟机电公司,去年从意大利引进新技术,新建一条生产线,开发轨道交通电机产品,但技工不足使升级效率大打折扣。公司副总经理莫隐侠说,制造业升级有三个关键要素,新设备、新技术和新人才,“目前人才短缺是企业最头疼的问题。因为新设备有钱就能买到,新技术可以引进,但掌握新设备的技工不是短时间就培养成的”。
产业技术工人“断档”,究竟原因何在?“传统制造企业待遇偏低,是技工紧缺的直接原因。目前,大多数企业还没有把劳动力当作资源要素来对待,仍然视工人为成本负担,并且想尽办法压缩这一成本。”重庆市人社局职业能力建设处处长宋飞说。
秋田齿轮公司人力部负责人张树瑜坦承,当前机械加工行业利润日渐微薄,尽管工资每年都在涨,但和其他行业相比增长幅度小得多,公司一线工人平均月工资目前只有2600元,技术工种月薪也不过3000元,对技能人才没有太大吸引力。
此外,不少制造类企业尤其是中小企业,只顾消费人才,不愿培养人才,缺乏在职培训技术工人的意识和机制,加剧了技工“断档”的问题。
宋飞透露,目前除国有大中型企业外,很多民营中小制造企业几乎不培养自己的技术工人队伍。虽然政府出台了支持在职培训的政策,包括企业计提职工教育经费可予税前扣除,为职工申请职业等级证书提供补助等,但不少企业为节省成本基本不搞提升培训。
重庆联英人才华新市场总监万晓冬说,一些中小制造企业不注重培训自己的技术工人,而是完全依赖社会招聘,一边招聘一边流失,陷入恶性循环。
声明:本网站所收集的部分公开资料来源于互联网,转载的目的在于传递更多信息及用于网络分享,并不代表本站赞同其观点和对其真实性负责,也不构成任何其他建议。本站部分作品是由网友自主投稿和发布、编辑整理上传,对此类作品本站仅提供交流平台,不为其版权负责。如果您发现网站上所用视频、图片、文字如涉及作品版权问题,请第一时间告知,我们将根据您提供的证明材料确认版权并按国家标准支付稿酬或立即删除内容,以保证您的权益!联系电话:010-58612588 或 Email:editor@mmsonline.com.cn。
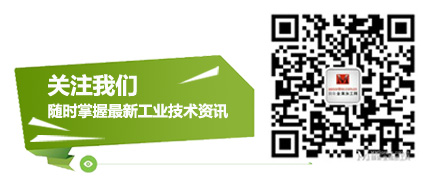
- 暂无反馈