模板钳工工艺学——模具的安装与调试1
一、冲模的安装1.准备工作
1)熟悉有关工艺文件,掌握冲模安装的方法和注意事项,适当了解冲压工艺规程和各工序的特点。
2)检查模具的安装条件。
3)选择压力机并检查其安装条件(如运转情况、技术状态等)。
4)选择好安装工具、量具及有关辅助用具。
(1)冲模上模的安装
1)利用模具的模柄进行安装连接。
2)利用模具的上模座进行安装连接。
3)既利用模柄又利用上模座来安装连接模具。
(2)冲模下模的安装 下模的安装形式与连接方法一般是利用垫块、压板和螺栓直接固定在压力机的工作台垫板平面上(其上有T形槽)。
(3)冲模安装的常见类型 各类冲模的安装见表5-2。
(4)安装要点
1)压力机及模座的安装面在安装前应擦拭干净。
2)将模具放在压力机台面规定的位置上后,可用压力机行程尺检查滑块底面至冲模上平面之间的距离是否大于压力机行程。 3)模具的闭合高度必须在压力机的最大装模高度(Hmax)和最小装模高度(Hmin)之间,即应满足关系式:Hmax-5
4)在双动压力机上安装拉深模时,有时需要过渡垫板,其作用有两点:一是连接拉深模和压力机;二是用来调节内、外滑块不同的闭合高度。
5)固定冲模的螺栓、螺母和压板应采用专用件,尽量不用替代品。
6)对于冲裁厚度小于2mm的冲裁模的安装,其凸模进入凹模的深度应不超过0.8mm;硬质合金模具应不超过0.5mm。
7)若在闭式压力机上安装使用气垫托杆顶件的模具,则在工作台规定的位置上预先插入气垫托杆,并将压力机的气垫充气,使托杆上升而进入模具的托杆孔内。
8)对于弯曲模和拉深模的安装,其方法与冲裁模基本相同。
二、冲模的调整与试模
1.冲模的调整
(1)模具闭合高度的调整 模具的上、下模安装到压力机上后,要调整模具闭合高度。
(2)凸模与凹模的配合调整 1)对于冲孔、落料等冲裁模具,将凸模调整到进入凹模刃口的深度为其被冲料厚的或略深一些就可以了。 2)弯曲模凸模进入凹模的深度与弯曲件的形状有关,一般凸模要全部进入凹模或进入凹模一定的深度,能够将弯曲件压制成形为止。 3)调整拉深模时,除考虑凸模必须全部进入凹模外,还应考虑开模后制件能顺利地从模具中卸下来,见图5-3,左半部分为模具闭合状况(HM),右半部分为模具开启状况(HK),制件高为h,模具开启后H>h。
4)有导向装置的模具,其调整过程比较简单,凸、凹模的位置可由导向零件决定,要求模具的导柱、导套要有良好的配合精度,不允许有位置偏移和卡住现象。
(3)其他辅助装置的调整 1)对于定位装置的调整,应时常检查定位元件的定位状态,假如位置不合适或定位不准确,应及时修整其位置和形状,必要时可重新更换定位零件。 2)对于卸料系统的调整,应使卸料板(或顶件器)与制件贴服;卸料弹簧或卸料橡胶块弹力要足够大;卸料板(或顶件器)的行程要调整到足够使制品卸出的位置;漏料孔应畅通无阻;打料杆、推料板应调整到顺利将制品推出,不能有卡住、发涩现象。
3)调节气垫压力,如冲模需要使用气垫,则应调节压缩空气到适当的压力。
(4)冲模辅助联动机构的调整 冲模辅助联动机构是指与模具安装有关的、除压力机以外的辅助工作机构,它所包括的内容对于不同的模具是不一样的。
2.试模
(1)试模的目的 模具装配完成后,要按使用要求在正常的生产条件下进行试模。
1)验证所用的设备是否合适,它包括冲压力是否足够和模具是否不用任何修整就能顺利地装到设备上使用。
2)验证该模具所生产的制品零件在形状、尺寸精度、表面质量等方面是否符合设计要求;确定冲压成形零件毛坯的形状、尺寸及用料标准。
3)验证该模具在卸料、定位、顶出件、排废料、送出料和安全生产方面是否正常可靠,能否进行生产性使用。
4)验证冲压工艺流程是否合理。 5)验证并确定工艺设计、模具结构设计的某些尺寸。
6)验证模具质量和精度,为模具投入正常生产作准备。
(2)试模操作要点 1)试模是一项不可缺少的重要工作。
2)试模的次数不宜太多,最好是一次成功,若不能做到,可在试冲一次之后把发现的问题充分解决了再试1~2次即可。
3)试冲的时间不宜过长,对于新装的模具初次试冲,时间应以能把所存在的问题暴露出来为前提。
4)一般要求的冲模须连续试冲20~1000件,精密多工位级进模必须连续冲1000件以上,对于大型覆盖件要求连续冲5~10件,贵重金属材料试冲数量可根据实际情况确定。 5)试模所用的材料性质、牌号及厚度需经检验,并符合技术要求。
6)试模成形件的表面不允许有伤痕、裂纹和皱褶等缺陷。 7)试模时最好通知用户到场,有利于用户对模具使用的全面了解和对模具验收的认可。
(3)试模后的要求 1)能顺利地安装到指定的压力机上去。
2)能稳定地冲制出合格的产品。 3)能安全地进行使用操作。
3.各类冲模试模过程中常见的问题及调整方法
声明:本网站所收集的部分公开资料来源于互联网,转载的目的在于传递更多信息及用于网络分享,并不代表本站赞同其观点和对其真实性负责,也不构成任何其他建议。本站部分作品是由网友自主投稿和发布、编辑整理上传,对此类作品本站仅提供交流平台,不为其版权负责。如果您发现网站上所用视频、图片、文字如涉及作品版权问题,请第一时间告知,我们将根据您提供的证明材料确认版权并按国家标准支付稿酬或立即删除内容,以保证您的权益!联系电话:010-58612588 或 Email:editor@mmsonline.com.cn。
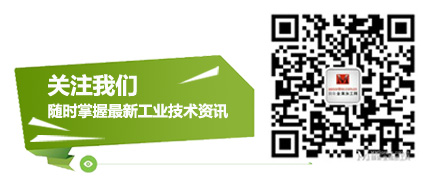
- 暂无反馈