应用热流道技术的特种注射模
由于注射制品的结构、形状与大小及加工生产要求,一些特种注射模必须采用热流道技术。最近,本公司致力于织物衬里、多型腔瓶盖和叠式注塑模的设计和生产。本文笔者对此工艺进行了扼要介绍。
1 织物衬里注塑模
汽车内饰用长条的织物衬里的聚丙烯注射件。前些年,这类制品的注射模具依赖进口。它必须用多个开关式热流道喷嘴串接,依次逐点地自动控制注射。在较低的注射压力下,让织物均匀覆贴在动模上。保证织物与塑料黏结复合。制品上无熔合缝,无明显的翘曲变形。这种在织物衬里上注射方法称为模内复合,即IML(in-mould lamination)注塑。国内俗称包布模。
注射从一端的开关式喷嘴开始,临近的喷嘴只有当熔料前沿经过它们时才打开。当最后的喷嘴将型腔充满后,所有的喷嘴必须打开,以实施保压过程。喷嘴的数目和热流道的几何参数应该用计算机模拟软件建立。从型腔的一端起始完成的熔料充填,也有从中央注射点向两侧推进。由注射机螺杆运动的作用,控制这些开关式喷嘴的顺序开放。也有用时间继电器控制的。
在型腔被熔体充填时,从相反方向与熔料前峰相遇是不允许的。这会使织物衬里萎缩起皱。用串接式的几个注射点,用传输料流的前峰,保证织物被均匀保压在模壁上。进而,在众喷嘴的间距和制件厚度确定后,必须对每个充填区提供相同的低压力降。
在IML模具内,从塑料层一边注射,织物放置在动模型腔内。脱模顶出系统和热流道系统必须设置在定模上。
热流道系统的开关式喷嘴由气缸闭合,而且顶出板也用气缸驱动,这可防止任何漏油污染织物衬里。制品的多余衬里在专用切割机床上切除。
动模上的织物衬里制品必须强化冷却。由于织物的绝热性能使注射制品冷却困难。织物衬里也使注射充模的料流不对称,导致向衬里翘曲变形。在定模的喷嘴区需加强冷却,来抵消朝中央的翘曲变形。
聚酯PET饮水或饮料的塑料瓶盖,生产批量很大。用高密度聚乙烯HDPE模塑,每个重2g。盖内有紧固螺纹。盖顶下有密封圈。瓶盖开启后,有紧箍环留在瓶颈上。瓶盖与紧箍环之间有6~8注射连接点。旋盖时扭断连接点。
这种瓶盖注射模,有强制顶出的脱模机构。有成型连接点的双滑块的侧向分型机构。用针点式浇口,在瓶盖中央的浇口痕迹很小。为提高生产率,参照进口模具,设计和生产了32腔瓶盖注塑模。
浇道所消耗的塑料量超过了模塑件的重量。如果采用冷流道系统,发达的浇道凝料,需专设机构将其从定模中顶出。大量的浇道凝料需要粉碎,再次加热熔化。而且这种回头料的质量差,只能小份额地混进新料再次塑化注射。因此这种多型腔的注射模,必须采用热流道技术。在提高生产率时,还能省物料,有利于压力传递,也缩短了注射周期。多腔瓶盖热流道注塑模,用32个顶针式喷嘴;有40个温度检测点。热流道系统的流道直径用聚合物流变学原理计算。
3 叠式注塑模
叠式注塑模相当于二副模具叠放组合在一起。这种模具需要有较长的主流道,输送熔料到模具中央的热流道板。叠式注塑模适用于成型形状扁平的薄壁和大批量的注塑件。
叠式注塑模有二个分型面。所需锁模力只提高了5%~10%。但多型腔的生产,使产量成倍增加。叠式注塑模的二个分型面要同时分型;还要二套脱模机构。如果采用冷流道注塑,还要脱出流道凝料,很难实现自动化模塑生产。采用了热流道技术后,叠式注射模才得到较多应用。
现今的叠式注塑模有二种结构类型。一种如图4所示,主流道由模具中央注入热流道板,再分流经喷嘴射入各型腔。它适用于中小型扁平的注塑件。单副的型腔数n =2、4…… ,整副模具有2n个型腔。另一种如图5所示,主流道由模具一侧绕道进入热分流板,再各喷嘴注射。它适用于大型扁平的注射件,不允许从模具中央进料。
这两种结构的叠式热流道注塑模,在主流道输送熔料过程中,都要流经一个分型面。必须在分型面的两侧,设置二个开关式的主流道喷嘴。在开模前,二个开关式喷嘴的阀芯关闭主流道。在模具闭合时,二个阀芯收起,主流道畅通。
声明:本网站所收集的部分公开资料来源于互联网,转载的目的在于传递更多信息及用于网络分享,并不代表本站赞同其观点和对其真实性负责,也不构成任何其他建议。本站部分作品是由网友自主投稿和发布、编辑整理上传,对此类作品本站仅提供交流平台,不为其版权负责。如果您发现网站上所用视频、图片、文字如涉及作品版权问题,请第一时间告知,我们将根据您提供的证明材料确认版权并按国家标准支付稿酬或立即删除内容,以保证您的权益!联系电话:010-58612588 或 Email:editor@mmsonline.com.cn。
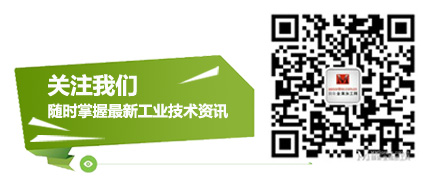
- 暂无反馈