切削用量智能化选择的神经网络建模
切削用量的选择是制定机械零件加工工艺中的一个重要方面,选择得恰当与否,将直接影响到成品的质量、生产率、加工成本等,然而由于影响切削用量的因素繁多,影响因素之间又相互交叉,相互制约,因而确定最佳切削用量较为困难。人们最初是根据经验来确定金属切削用量的,然而这种方法所确定的切削用量因人因厂而异,实际效益相差很大,而且由于各种新加工材料的不断涌现,以及数控加工机床、加工中心和柔性制造系统的应用,依靠经验来确定切削参数已远不能适应时代的发展。
随着人们对金属切削机理研究的不断深入,以及计算机技术的发展,人们建立起计算机辅助优化切削数据的程序系统,为选择最优切削参数提供了新的方法和手段。然而由于影响最佳切削参数的因素错综复杂,优化方法本身也存在优化效率和收敛于局部最优点的问题,因而最佳切削参数的确定受到一定的限制,在实际操作中要针对具体的问题建立相应的优化数学模型,步骤十分繁琐。目前利用计算机技术做成了各种切削数据库,为生产提供数据,这些数据比较准确、可靠,是人们长期经验的总结,但它们在应用时很大程度上受到所搜集的数据量和其包含的范围的影响。另一方面,从切削数据库检索的切削用量数据在应用中还要根据实际工作环境进行一定的调整,其本身也不具有推广应用能力。因此,目前这些切削用量确定方法求解的快速性和准确性受到一定的限制,对于实时的控制切削用量、实现机器的智能化选取切削参数有较大困难。作为人工智能研究领域的新技术——人工神经网络,具有非线性特性和信息分布性,在处理多输入和多输出系统时省去了传统建模方法所需的复杂的各变量相关性分析;神经网络具有大量信息的并行处理功能。因此神经网络非常适于用来代替人类基于经验的决策行为。
1 神经网络的非线性建模原理
对神经网络的理论研究表明,具有单隐层的前馈式分层神经网络可以以任意精度逼近任何非线性连续函数。因此,本文采用了前馈分层结构的BP网络实现非线性建模。
它是一个三层网络,n个输入单元对应输入模式的n个特征参数,m个输出单元对应系统输出,单隐层含有r个节点,在训练过程中网络采用多层误差修正梯度下降算法进行学习,通过使一个代价函数最小化过程完成输入到输出的映射。代价函数通常以系统误差表示。
网络通过反复学习,可以使代价函数达到要求的误差限度。至此,网络的非线性建模即告结束。
从总体性质看,此神经网络是一个由Rn→Rm空间的映射,而且是复杂的非线性映射,它能将Rn空间的一个子集连续地映射到Rm空间中去。对于n个输出,整个网络相当于一个隐式函数
2 切削用量选择的神经网络建模
运用神经网络智能化选择切削用量的基本思想是:金属切削加工中用量的选择受到多种因素的影响,其变化与组合众多,运用神经网络非线性映射能力,恰当选取影响切削用量选择的特征因素,建立切削用量和各影响因素之间的神经网络映射模型,运用机床过去运行数据进行学习,自动寻找规律并分布贮存于权值中,运行时对输入切削条件参数通过前向计算求解出最佳切削用量。
理想切削用量选择神经网络模型
排除人为及环境因素,影响切削用量选定的因素包括:加工方法、工件、刀具、切削液、机床及生产目标,因此建立理想网络模型。若可利用此理想网络模型实现非常广阔范围内的切削用量选择,那么在最佳切削用量的选取工作中完全可用此模型来代替工程师的工作。然而这种理想模型的实现是很困难的:其一,由于要搜集到理想模型所要求的如此完备和广泛的切削样本数据是不容易办到的,因此在训练过程中,会由于数据的缺乏,或奇异数据的存在,使网络找不到收敛点,且随着网络的增大,这种缺点将更加突出;其二,由于模型内要容纳的规律范围宽广,内容广泛,使网络更加容易陷于局部最小。由以上分析可知,对于理想的切削用量选择神经网络模型是不容易实现的,但我们可通过对理想模型针对某一问题具体化,使其变得有效可用。
车加工切削用量选择的神经网络模型
由于粗加工和精加工的目标和性质不同,因此影响切削用量选择的主要特征因素也不完全一致。为此,可针对粗加工和精加工的切削用量选择问题分别建一网络模型。对于切削用量三要素来说,切削深度,主要取决于加工余量,没有多少选择的余地,一般都也事先确定,但切削深度的变化会对切削速度和进给量造成重大影响,因此应将切削深度作为输入因素加以考虑。粗加工的输入特征因素为14个精加工的输入特征因素为13个,分别如图3和图4所示。输出特征因素为2个(切削速度、进给量)。
切削条件参数和输出参数(切削速度、进给量)进行了归一化处理,归一化函数为:
神经网络依据BP算法对样本数据进行学习,学习完成后,粗加工和精加工的车削用量参数网络模型便被建立起来,模型进行工作时,切削条件参数向量由输入层通过权值和作用函数传播到隐层,再由隐层通过权值和作用函数传播到输出层,在输出层求出切削速度和进给量
Ziu=0.9(Zi-Zmin)/(Zmax-Zmin)+0.05
式中,Zi,Ziu——某一切削条件参数或切削用量参数及其规一化值 Zmax=max{Zi}, Zmin=min{Zi}; i=1,2,…,k
由于网络的输出是归一化了的切削速度和进给量,因而在模型工作过程中,对网络输出进行了反归一化换算: Zi=(Ziu-0.05)(Zmax-Zmin)/0.9+Zmin
对于连续的特征向量如:工件材料硬度和强度,刀具材料的硬度和抗弯强度等,可直接运用归一化公式;而对于非连续的输入特征向量,则要首先对其进行编码、量化,然后再对编码值进行归一化处理。非连续输入特征向量的编码如表1。
网络模型的学习
用搜集到的样本数据对网络进行训练,以获得有效的网络工作模型。在网络的学习过程中,不断修改隐层节点数目,学习步长h和冲量因子a,加快网络的收敛速度,并最终找到能够满足收敛精度要求的最小规模网络。
粗加工网络参数值 精加工
网络参数值
神经网络模型 三层前向神经网络
学 习 算 法 BP 算 法
神经网络 输入层节点 14 13
模型的 隐层节点 21 17
拓扑结构 输出层节点 2 2
学习步长h 0.1 0.2
冲量因子a 0.2 0.25
训练误差 0.0001 0.0001
3 实例研究
在以上切削用量神经网络模型研究的基础上,我们开发了车削加工智能化最佳用量选择软件。现在车床CA6140上加工45钢,毛坯为直径f60的棒料,无外皮,外圆纵车,采用YT15可转位刀片,刀具前角12°,主偏角45°,刀杆尺寸16×25,刀具寿命60min,粗加工切削深度2mm,精加工切削深度0.5mm,加工表面完工粗糙度Ra3.2。将各切削条件输入软件中,输出粗加工切削速度120m/min,进给量0.6mm/r,精加工切削速度180m/min,进给量0.4m/r。采用所选用量进行加工,完全达到加工要求。
本文的研究表明,对于一个相关因素错综复杂的非线性系统,运用神经网络对其输入输出建立起映射关系是一种非常有效的方法。总之将神经网络用于切削用量的选择中,实现切削用量选择智能化,从而提高机床的智能化程度,将具有广阔的前景。
声明:本网站所收集的部分公开资料来源于互联网,转载的目的在于传递更多信息及用于网络分享,并不代表本站赞同其观点和对其真实性负责,也不构成任何其他建议。本站部分作品是由网友自主投稿和发布、编辑整理上传,对此类作品本站仅提供交流平台,不为其版权负责。如果您发现网站上所用视频、图片、文字如涉及作品版权问题,请第一时间告知,我们将根据您提供的证明材料确认版权并按国家标准支付稿酬或立即删除内容,以保证您的权益!联系电话:010-58612588 或 Email:editor@mmsonline.com.cn。
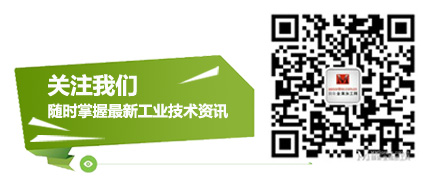
- 暂无反馈