汽车总装配线改造工艺分析(二)
6 制约重型车生产能力的主要因素
通过对工厂现状和新车型主要结构特征分析,制约生产能力因素,主要有下列几点:
1) 装配三线不具备双后桥重型车生产能力。
2) 由于装配线的桥链长度限制了工位数的增加,从而限制了生产能力的提高。
3) 拧紧工具扭矩不能满足重型车扭矩值的需求。
4) 为达到重型车扭矩值,必须要多次反复拧紧,增加了装配工时,影响下道工序。
5) 装配线工艺设计欠合理。
6) 产品结构的装配工艺性差。
产品结构中拧紧空间有限,如平衡轴连接,现有的风动工具无法使用,只有靠手工拧紧,从而增加了装配工时,并且无法保证拧紧扭矩。
7) 部分工艺装备的结构、柔性化生产较差,生产效率低,不能满足重型车的生产。
8) 随着重型车产量、品种、载重量的的增加,叉车能力已不能满足生产。
9) 总重为30t 的重型车的生产条件还欠缺。
10) 不具备双前桥重型车的生产能力。
7 三条装配线生产总重为30t及双后桥、双前桥重型车存在的主要问题
7.1 生产总重为30t重型车存在问题
总重为30t重型车,驱动形式有4×2。如:EQ1300系列,装备235kW柴油发动机,9档变速箱,变截面车架,全新结构保险杠,引进C800驾驶室,结构复杂,零部件装配紧凑,专用件300多种,零部件体积、重量大,装配难度大。
7.1.1 主要工艺流程
单后桥车型同装配三线的工艺流程,双后桥车型同装配一、二线的工艺流程。
7.1.2 存在主要问题
1)架结构特殊,前部翻转孔位销与前吊耳干涉,后部翻转孔处车架上翼面为斜面,车架宽度前宽后窄,翻转链不能直接使用,必须增加相应的翻转辅具,弥补以上不足,保证翻转工艺的通过性。
2)油箱链护网及悬挂吊钩不能满足大油箱的通过性。现在油箱链最大只能通过的油箱外形尺寸为1070×620×500。
3)胎链护网及悬挂吊钩不能满足大轮胎的通过性。目前轮胎链能通过的轮胎直径为1米。
4)由于驾驶室结构同现生产的差异较大,长度增加了150mm,宽度增加了115mm,重量也有增加,驾驶室地拖链、贮存小车及合件上线吊具均不能满足正常生产。
5)体积重量大的零部件较多,上线装配时无相应的起吊设备。如:消声器、传动轴、储气筒合件等。
6)现有前、后桥钢装台不适应多品种生产。
7)现有的发动机存放架、过跨小车及上线吊具均不能直接使用。
8)由于车轮结构的改变,车轮螺母拧紧机已不适用。目前的五头拧紧机只能适用于螺柱中心距为285.7mm的车轮装配,而EQ1300系列车轮的螺柱中心距为335mm;车轮装配吊具结构也需作相应改变。
7.2 生产双后桥、双前桥车重型车存在问题
双后桥、双前桥车重型车的主要特征:驱动形式6×4、8×4,10t级贯通式双后桥,2个独立前悬架,由1个转向机控制同步转向。
7.2.1 主要工艺流程
双后桥:
车架上线——平衡轴悬架上线(包括平衡轴分装)——后桥上线——中桥上线——前悬架合件上线(包括前桥分装)——底盘翻转——发动机、变速箱合件上线(发动机、变速箱分装)——制动系统密封性检测——润滑脂加注——油箱、轮胎装配(包括油箱、轮胎分装链)——驾驶室合件上线(包括驾驶室分装)——制动液、防冻防锈液加注——整车调整——整车下线
双前桥:
车架上线—平衡轴悬架上线(包括平衡轴分装)——后桥上线——中桥上线——第一前悬架合件(包括前桥分装)——第二前悬架合件上线(包括前桥分装)——底盘翻转——发动机、变速箱合件上线(包括发动机、变速箱分装)——制动系统密封性检测——润滑脂加注——油箱、轮胎装配(包括油箱、轮胎分装链)——驾驶室合件上线(包括驾驶室分装)——制动液、防冻防锈液加注——整车调整——整车下线
7.2.2 存在主要问题
(1) 装配线总装工艺性
1) 装配三线无中桥、平衡悬架、第二前桥合件上线点。
2) 三条总装线桥链短,装配用工位数少。
3) 装配二线生产双后桥时,前悬架、后桥上线途径不合理。因为前悬架、后桥通过一条单轨相对上线,距离短,限制了生产节拍。再者,平衡悬架、中桥由叉车往装配线倒运,物流状态较差。
4) 发动机变速箱对接工艺较落后。变速箱对接过程中第一轴易磕碰损坏,发动机需多次倒运,造成人力、物力的浪费。同时,吊装对接还存在不安全隐患。
(2)工艺装备
1) 后桥分装螺母拧紧机。目前能达到最大扭矩500N·m,而双后桥重型车平衡悬架分装扭矩为843N·m,已不能满足生产。
2) 后桥钢装台不能满足多品种的生产,板簧压平装置操作不便, 板簧支架间距不可调节。
3) 装配三线底盘翻转器能力不足。现在翻转能力为4t,由于双后桥、双前桥车重型车增加了平衡悬架等三大总成共5t,因此翻转能力必须提升到8t。
4) 产品结构的装配工艺性差,拧紧扭矩不能达到工艺要求,如平衡轴悬架联接等,受空间限制,现有风动工具无法使用,靠人工拧紧,扭矩没有保障,劳动强度大,装配工时大,是重型车装配的一大难点。
8 主要工艺方案
8.1 方案一:改造装配三线
8.1.1 总装配线改造
1)新建平衡悬架、中桥、后桥及2套前桥合件上线单轨,满足各大总成合理上线,平衡悬架合件(后桥合件)、前桥合件上线,各分别由2套过跨小车输送,从装配线右侧上线,中桥、后桥从装配线左侧上线。
2)改造6~8柱间3台手拉天车,右边供双后桥重型车储气筒合件上线用,左边供单桥重型车储气筒合件上线用。
3)增加重型车储气筒分装地增加平衡吊1台。
4)油箱链、轮胎链护网及悬挂吊具改造,加宽加深护网通道,改进悬挂吊钩结构,确保重型车大油箱、轮胎的通过性。
5) 驶室地拖链、贮存小车及合件上线吊具改造。加大地拖链强度,使贮存小车及合件上线吊具能适应窄型、CPB12、CPB12加长型、C800平头驾驶室的储存、分装及合件上线的要求。
7) 型车保险杠合件上线处增加一平衡吊。
8) 拆除总装线上润滑油加注机,润滑油加注在各总成分装地进行。从而增加了总装线上装配操作有效长度6米。
9) 建立发动机、变速箱对接阵地。发动机储存于环形地拖链上,运行系统由电脑全程监控,采用两台对接台,有自动找正、对中系统,8个自由度供调节使用,发动机、变速箱对接在对接台上完成后,通过过跨小车上线。提高了装配质量、分装节奏,减少总成倒运次数,同时适应多品种混流生产。
8.1.2 工艺装备
1)后悬架U 型螺栓拧紧采用无级可调式双头螺母拧紧机,扭矩值在300~1000N·m 之间可保证,U型螺栓中间距在190~300mm内可调,参数设置、修改简便快捷,拧紧结果自动识别,不合格自动报警,具有系统自检、零件标定、校正和故障自诊功能,适应多品种混流生产。
2)前、后桥及平衡轴钢装台采用可调式、自动压平装置,同时满足多种重型车生产,具有一定的柔性化生产能力。
3)翻转器改造。将其翻转的额定载荷由4t提升至8t。由于增加了三大总成的上线单轨,翻转器轨道需减短4m。
4)设计专用翻转辅具,保证底盘翻转同步、安全、可靠。
5)采用组合式发动机存放架、过跨小车及上线吊具,并具有一定的柔性化生产能力。
6)轮胎螺母拧紧机采用五轴组合式、轴距、扭矩可调的电动拧紧机。操作简便,能自动识别拧紧结果,不合格自动报警,适应多品种重型车生产。
7)平衡轴连接螺栓等处,需使用的电动特形装配工具,有待探索研发。目前,仍然由人工扳手拧紧,为解决这一瓶颈问题,采用双工位,使之得以缓解。
8.1.3 实施效果
装配三线改造后,工艺装备、装配工艺水平有了较大的提高。通过改造,提高了劳动生产率,降低了劳动强度,营造了优良的劳动环境。
1)具备了总重为30t(EQ1300 系列)系列车型以及双前桥重型车的批量生产能力;增加平衡悬架、中桥等17个装配工位后,双后桥重型车单品种生产能力将达到3.5万辆;同时,具备了双前桥重型车的批量生产能力。
装配线中、重型车生产能力(单一品种) (万辆/年)
2)通过改造提高了后桥分装(平衡悬架分装)的技术水平和自动化程度,提高了各大总成分装的柔性化程度。
3)使用的拧紧工具技术水平和功能上了一个新的台阶,提高了劳动生产力,并且使整车装配质量保证能力有了大的飞跃。
8.2 方案二:对装配二线进行局部改造
采用先进的工艺装备,科学、合理地调整三条装配线上产品的种类。
8.2.1 装配一线
采用先进的工艺装备调整产品的种类,提高双后桥重型车的生产能力。
1)后悬架U型螺栓拧紧采用无级可调式双头螺母拧紧机,扭矩值在300~1000N·m 之间可保证,U型螺栓中间距在190~300mm 内可调,参数设置、修改简便快捷,拧紧结果自动识别,不合格自动报警,具有系统自检、零件标定、校正和故障自诊功能,适应多品种混流生产。
2)前、后桥及平衡轴钢装台采用可调式、自动压平装置,同时满足多种重型车生产,具有一定的柔性化生产能力。
3)轮胎螺母拧紧机采用五轴组合式、轴距、扭矩可调的电动拧紧机。操作简便,能自动识别拧紧结果,不合格自动报警,适应多品种重型车生产。
4)采用先进的定扭、扭矩可控的装配工具。平衡轴连接螺栓等处,需使用的电动特形装配工具,有待探索研发。目前,仍然由人工扳手拧紧,为解决这一瓶颈问题,采用双工位,使之得以缓解。
5)整装配线上产品种类,最大限度地利用装配线的长度和人员,提高重型车产量。
声明:本网站所收集的部分公开资料来源于互联网,转载的目的在于传递更多信息及用于网络分享,并不代表本站赞同其观点和对其真实性负责,也不构成任何其他建议。本站部分作品是由网友自主投稿和发布、编辑整理上传,对此类作品本站仅提供交流平台,不为其版权负责。如果您发现网站上所用视频、图片、文字如涉及作品版权问题,请第一时间告知,我们将根据您提供的证明材料确认版权并按国家标准支付稿酬或立即删除内容,以保证您的权益!联系电话:010-58612588 或 Email:editor@mmsonline.com.cn。
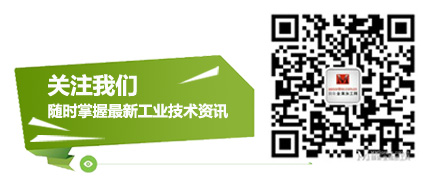
- 暂无反馈