机械粘砂 - 铸造工艺缺陷及其解决措施
定义和特征
机械粘砂又称为金属液渗透粘砂,是由液态金属或金属氧化物通过毛细管渗透或气相渗透方式钻入型腔表面砂粒间隙,在铸件表面形成的金属和砂粒机械混合的粘附层。清铲粘砂层时可见金属光泽。机械粘砂表面呈海绵状,牢固地粘附在铸件表面,多发生在砂型和砂芯表面受热作用强烈及砂型紧实度低的部位,如浇冒口附近,铸件厚大截面、内角和凹槽处。 鉴别方法
肉眼外观检查。机械粘砂可发生在各种砂型中,表面呈海绵状,可用喷、抛丸法清理,有时也要进行打磨。树脂砂型粘砂通常为机械粘砂。 形成原因
1.型砂和芯砂粒度太粗 2.砂型和砂芯的紧实度低或不均匀 3.型、芯的涂料质量差,涂层厚度不均匀,涂料剥落 4.浇注温度和浇注高度太高,金属液动压力大 5.上箱或浇口杯高度太高,金属液静压力大 6.型砂和芯砂中含粘土、粘结剂或易熔性附加物过多,耐火度低,导热性差 7.型、芯砂中含回用砂太多,回用砂中细碎砂粒、粉尘、死烧粘土、铁包砂太多,型砂烧结温度低 8.铸件开箱落砂太晚,形成固态热粘砂,尤其是厚大铸件和高熔点合金铸件 9.金属液流动性好、表面张力低。例如,铜合金中磷、铅含量过高,铸钢中磷、硅、锰含量过高 10.树脂砂型、芯表面未刷涂料或涂料质量差,涂层厚薄不均,浇注时砂粒间树脂膜气化,形成毛细通道,在金属液静压力、蒸气压和表面张力作用下,金属液或金属蒸气渗入毛细通道,形成机械粘砂 11.金属液中的氧化物和低熔点化合物与型砂发生造渣反应,生成硅酸亚铁、铁橄榄石等低熔点化合物,降低金属液表面张力并提高其流动性,使低熔点化合物和金属液通过毛细管作用机制,渗入砂粒间隙,并在渗透过程中,不断消蚀砂粒,使砂粒间隙扩大,导致机械粘砂 12.浇注系统和冒口设置不当,造成铸型和铸件局部过热。
防止方法
1.使用耐火度高的细粒原砂 2.采用再生砂时,去除过细的砂粒、死烧粘土、灰分、金属氧化物、废金属、铁包砂及其他有害杂质,提高再生砂质量。定期补充适量新砂 3.水是强烈氧化剂,应严格控制湿型砂水分,加入适量煤粉、沥青、碳氢化合物等含碳材料,在砂型中形成还原性气氛。但高压造型时应减少含碳材料加入量,以减少发气量 4.采用优质膨润土,减少粘土砂的粘土含量 5.型砂中粘结剂含量要适当,不宜过高。提高混砂质量,保证砂粒均匀裹覆粘结剂膜,并有适度的透气性。避免型砂中夹有团块 6.提高砂型的紧实度和紧实均匀性 7.浇注系统和冒口设置应避免使铸件和铸型局部过热。内浇道应避免直冲型壁 8.采用防粘砂涂料,均匀涂覆,在易产生粘砂部位适当增加涂层厚度。涂料中不得含有易产生气体、氧化及能与金属液和型砂发生反应的成分。尽量不采用通过反应可在铸件-铸型界面形成易剥离的玻璃状粘砂层的涂料或面砂来解决粘砂问题(例如在铸铁件型砂和芯砂中加入赤铁矿粉等) 9.适当降低浇注温度、浇注速度和浇注高度,降低上型高度和浇口杯高度,以减小金属液动压力、静压力及对铸型的热冲击 10.加强对铸钢等高熔点合金的精炼,净化金属液,降低合金液的氧化程度和吸气量,减少低熔点相形成元素(如铸钢、铸铁中的硫、磷,青铜中的磷、铅)的含量,控制会降低金属液表面张力、提高金属液蒸气压的元素(如铸钢、铸铁中的锰和硅,青铜中的铅)的含量。 11.对于大型厚壁铸件,适当提早开箱,加快铸件冷却,以防止固态粘砂 12.采用表面光洁的模样和芯盒。 补救措施 1.喷、抛丸清砂 2.打磨 3.电化学清砂,尤其适用于清除铸件深腔和精密铸件的严重粘砂。
声明:本网站所收集的部分公开资料来源于互联网,转载的目的在于传递更多信息及用于网络分享,并不代表本站赞同其观点和对其真实性负责,也不构成任何其他建议。本站部分作品是由网友自主投稿和发布、编辑整理上传,对此类作品本站仅提供交流平台,不为其版权负责。如果您发现网站上所用视频、图片、文字如涉及作品版权问题,请第一时间告知,我们将根据您提供的证明材料确认版权并按国家标准支付稿酬或立即删除内容,以保证您的权益!联系电话:010-58612588 或 Email:editor@mmsonline.com.cn。
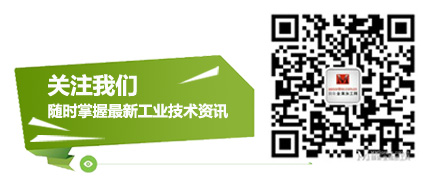
- 暂无反馈