基于PAM-CAST的镁合金轮毂低压铸造模拟
前言
镁是工业中最轻的常用金属材料,质量密度约为铝的2/3,铁的1/4。镁及镁合金还具有比强度高、刚度好、良好的阻尼系数、抗电磁干扰及屏蔽性好以及回收利用率高等优点,在汽车、航空、航天、电子等行业有着很大的应用潜力。因此,镁及镁合金被认为是21世纪最富于开发和应用潜力的“绿色材料”。根据西方汽车工业界的展望,在未来二十年里,平均每辆汽车上的镁合金用量将达到100~120kg,这比目前的2kg增长50倍以上,届时仅用于汽车的镁合金将超过500万吨,是目前全球镁年需求量(48万吨)的10倍。
汽车零件未来发展的目标是用近净形成形方法生产精密优质的铸件。低压铸造是近无余量铸造工艺,其特点是铸件充型平稳,并在压力下补缩、凝固,生成的铸件尺寸精度高,内部质量优良,以及生产率较高等优点,成为镁合金铸件生产的重要工艺。而在实际生产中往往会出现许多缺陷,如缩孔、缩松、裂纹等,这些缺陷对产品的使用构成了很大的危险,所以必须找到行之有效的方法消除或降低。这些缺陷与铸件的充型和凝固过程有很大的关系,通过对铸造过程的分析可以为消除这些缺陷提供科学的理论依据和方法。
商业铸造模拟软件PAM-CASTTM采用有限差分法能够对各种材料和浇铸工艺进行填充和凝固的3D模拟,并对流体通过的表面与坐标轴不完全一致的地方采用修正因子进行补偿,更真实地模拟流体在模型中的流动。本文运用此软件对镁合金轮毂低压铸造过程进行模拟并分析了充型与凝固过程的温度场、流场和液体分数的分布情况,进而预测各种可能出现的缺陷,并结合分析结果提出消除这些缺陷问题的方法。
模型的建立
使用CAD软件UG对轮毂实体造型,如图1所示。然后在PAM-CASTTM里进行表面网格的划分,并自动生成体网格。整个模型共划分了1,894,528个单元,在其中轮毂最薄的轮网部分保证有2-3个单元,以保证模拟的准确性,如图2。 在模拟中使用的镁合金为AZ91D,各种物理性能数据如表1,其中密度、比热、热传导率是温度的函数,表中只列出了在650 ℃左右的参数值。计算中采用的镁合金液浇注温度为690℃,初始模具的温度为420℃,内浇口速度为0.5m/s。
结果描述与分析
轮毂的整个填充过程在6.22s内完成,如图3,首先合金液体很平稳地填充了轮心部分,然后平缓地进入到轮辐中。在1.38s时合金液体前沿到达轮辐与轮网的连接处,并在2.13s时各个轮辐顶端间的合金液体汇合,此时的温度为640℃左右。在4.88s时浇注液体前沿到达轮网中部,此时合金液体温度为590℃左右。
在6.2s时合金液体到达轮网顶部,整个轮毂被全部充型。此时没有发生欠铸和冷隔缺陷,轮网上缘合金温度为580℃左右,处于可流动状态,下缘部位合金温度为630℃左右,上缘和下缘的温差为约50℃。在填充结束末轮心上端的合金温度仍然接近于浇注温度690℃。
在轮毂填充过程,当合金液体前沿到达轮辐中部时,由于凹槽的存在,使轮辐中部液体的流动减缓,凹槽内的气体可能被两端的液体所包围,产生气孔缺陷。
在填充过程完成后,凝固过程开始,并在136.25s时结束,如图6。在开始凝固阶段,轮网的凝固不是很平缓地逐渐进行,对应各轮辐之间部位的凝固先于轮辐部位,如图6-c。由于轮毂轮心的形状不是完全的轴对 称结构,其中三个区域,处于轮网部分的最后阶段凝固,所以预计会产生缩孔,如图6-d。因镁合金的容积热容量比较小,因此在轮辐中部区域会产生早期凝固现象,而在轮辐与轮网的连接处产生热节,于是在这些区域存在潜在的缩孔缺陷,如图6-f和图7。所以整个凝固过程不是理想的定向凝固,从而会降低轮毂质量。
缺陷的产生原因与消除方法
低压铸造生产中铸件比较容易产生一些铸造缺陷,其原因是多方面的,与铸造设备、模具、工艺和具体的操作有关,为了获得高质的镁合金铸件,必须对产生的质量问题做出正确的判断,找出真正的原因,并提出相应切实可行有效的改进措施,以提高铸件的质量。
在本文研究的镁合金低压铸造过程中,根据模拟的分析,预测出可能产生的缺陷有气孔和缩孔。
1.气孔:形成气孔的原因一般有两种,一种是在填充时,卷入气体形成的内表面光亮和光滑、形状较为规则的空洞。另一种是合金熔炼不正确或者精炼不够,气体溶解于合金中。压铸时,凝固很快,溶于金属内部的气体来不及析出,使金属内的气体留在铸件内而形成的空洞。
在填充过程中,轮辐中部产生的气孔属于上面介绍的第一种情况,其改善措施有:降低内浇口的速度; 改变轮辐的几何结构。
2.缩孔:铸件在凝固过程中,金属补偿不足所形成的呈暗色、表面粗糙、形状不规则的空洞。 轮毂在凝固过程中所形成的缩孔,主要是由于轮心部位和模具的设计不合理造成的。其改善措施有:改进轮心部位为完全轴对称结构;改善模具的冷却系统。
本文运用商用软件PAM-CASTTM对镁合金轮毂低压铸造进行了数值模拟,采用AZ91D作为研究合金,对填充和凝固过程中的各种变量分布情况进行了分析,包括温度场,速度矢量场和液体分数。进而预测了在此过程中可能出现的各种缺陷,并提出了消除这些缺陷而采取的措施。同时为实际生产准确地确定出填充和凝固时间。该模拟及分析结果对提高铸件质量、性能和生产效率,降低和消除铸造缺陷具有很重要的实际意义。
声明:本网站所收集的部分公开资料来源于互联网,转载的目的在于传递更多信息及用于网络分享,并不代表本站赞同其观点和对其真实性负责,也不构成任何其他建议。本站部分作品是由网友自主投稿和发布、编辑整理上传,对此类作品本站仅提供交流平台,不为其版权负责。如果您发现网站上所用视频、图片、文字如涉及作品版权问题,请第一时间告知,我们将根据您提供的证明材料确认版权并按国家标准支付稿酬或立即删除内容,以保证您的权益!联系电话:010-58612588 或 Email:editor@mmsonline.com.cn。
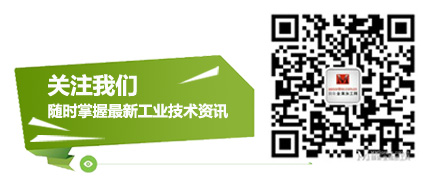
- 暂无反馈