轮式装载机工作装置的有限元分析
1、引言
装载机是工程机械的主要机种之一,广泛用于建筑、矿山、水电、桥梁、铁路、公路、港口、码头等国民经济各部门。国外装载机发展迅速,而我国装载机在设计上存在很多问题,其中主要集中在可靠性、结构设计强度等方面。由于采取“类比试凑”等设计方法在一定程度上存在盲目性,容易形成设计中的“人为”应力集中点,造成机构整体强度的削弱甚至破坏。按这种设计生产出的产品,外观上看上去很强壮、刚性很好,但却有内在的设计缺陷,使用过程中常因工作装置结构强度等原因,产生开焊、甚至断裂等破坏,致使工作装置报废,造成重大经济损失。
本文将以SDZ20型装载机为例,建立有限元模型,在典型工况下用MARC软件进行静态结构分析,获得工作装置整体的应力及变形分布。其结论对该种结构的优化设计有一定的指导意义。
2、工作装置结构受力破坏与力学特征
2.1工作装置的结构
工作装置由铲斗、动臂、横梁、支撑、摇臂、拉杆等组成。各构件之间由铰销联接,有相对转动。为了增强摇臂、支撑的刚度,在摇臂及支撑之间有筋板连接,在计算时,可以将其视为一体。动臂上铰点与装载机前车架铰接,中部铰点与举臂油缸铰接;摇臂上铰点与翻斗油缸铰接。用MARC对其做有限元静力分析中,认为工作装置各铰接处没有相对转动。动臂是工作装置的主要受力部件,其截面形状为矩形;又因其长、宽方向远大于厚度方向,故可以用板壳元对动臂进行离散。横梁截面为箱形,为焊接结构。摇臂和支撑也是焊接结构,其焊接板的截面均为矩形。考虑各构件的厚度远小于其它两个方向的厚度,可以认为均为板类零件。
2.2 结构受力与破坏特征
装载机整体结构为对称结构。分析装载机插入、铲起、举升、卸载等的作业过程可知,装载机载初铲时,工作装置受力最大。在整个工作过程中受到的外界载荷为不变载荷,主要是物料的重量以及机构自重。由于物料种类和作业的条件不同,装载机工作时铲斗切削刃并非均匀受载,一般可以简化为两种极端情况:(1)认为载荷沿切削刃均匀分布,并以作用在铲斗切削刃中点的集中载荷来代替均布载荷,称其为对称受载情况;(2)非对称受载情况,由于铲斗偏铲、料堆密集情况不均,使载荷偏于铲斗一侧,通常将其简化为集中载荷作用在铲斗最边缘的斗齿上。这两种处理方法都是偏于安全的。当结构受力超过其极限载荷,材料发生塑性变形直至开裂(焊接部位)或断裂。
3、有限元模型的建立及边界条件
工作装置作为装载机的主要工作部件,强度和刚度必须有充分的保证。根据工作装置的结构特征,建立起与其对应的有限元模型。
3.1单元类型的选取有限元网格划分
工作装置的各板厚度均匀,且长宽相比较小的多。根据经典薄壳理论假设,厚度小于中面轮廓尺寸1/5的为薄板。因此可以采用空间板壳单元进行网格划分。考虑四边形单元比三角形单元具有更高的计算精度,而三角形单元比四边形单元更利于拟合过渡,所以采用四边形单元与三角形单元混合进行网格划分。
有限元网格按照“均匀应力区粗划、应力梯度大的区域细划”的原则进行划分。按照给定尺寸自动划分后,对局部(如尖角和轴承孔等部位)进行细划。
3.2边界条件的施加
边界条件包括两方面:边界载荷和边界约束。取额定装载量,按静力等效的原则将力施加在铲斗尖内移约100mm处中部。在初铲转斗时,可认为举臂油缸和翻斗油缸都不动,动臂的两个铰销部位和摇臂的铰销部位无相对移动。
3.2.1边界载荷
额定装载为2×104N。联合铲取的工况进行加载。根据以上假设,可以计算出铲斗所受水平力Rx和垂直力Ry。
水平力(即插入阻力)的大小由装载机的牵引力确定
Rx=Pkpmax=4000N 式中,Pkpmax为装载机的牵引力。
垂直力(即铲起阻力)大小受装载机的纵向稳定条件的限制。
Ry=GL1/L=58800x1300/2615.8=26974N 式中,G——装载机自重,为6000kg(58800N)。
L1——中心到前轮水平距离,为1300mm。
L——垂直力作用点到前轮水平距离,为2615.8mm 。
考虑到铲斗的特殊性,对其变形及破坏不予考虑。根据圣维南原理,局部载荷不影响远处应力场的分布,可以知道,在铲斗尖部附近所施加的点载荷不会影响除去铲斗外的工作装置的应力分布。所以这种加载方式是可行的。
3.2.2边界约束
根据假设,举臂油缸和翻斗油缸不动。这样,在油缸与工作装置的铰接处和动臂与前车架的铰接处分别施加对应的边界条件。
3.3材料性能参数的确定
SDZ20型装载机工作装置构件所用的材料为16Mn(包括动臂、摇臂、支撑、横梁和各筋板、加强板)和Q235(拉杆),变形在弹性范围内,对应各构件分别施加所需材料常数:
4、结果分析
用MARC软件对工作装置进行有限元分析,得到整个工作装置的整体应力应变场、变形场分布。 由结果可知,该装置的结构完全满足了强度要求。各构件情况是:动臂的危险点在动臂下铰点及动臂与举臂油缸铰接处附近,应力值已经分别达到142.5MPa和118.9MPa,偏载时应力值达到184.5 MPa和153.6 MPa,是正载时的1.29倍,且偏载的一侧与横梁焊接部分出现应力集中,其值已达到100 MPa;摇臂的危险点在摇臂与拉杆铰接处,应力已达91.7 MPa;横梁的危险点在横梁与动臂的铰接处,应力值已达65.2 MPa;拉杆的危险点在与摇臂铰接处,应力值已达107.2 MPa。同时,在偏载时,动臂承载了由于偏载所产生的大部分扭矩,而其他构件在偏载时的应力集中相对减小。即使这样,最大值仍远小于屈服应力,设计是偏于安全的。
5、结论
通过对SDL20型装载机的工作装置两种典型工况的计算分析说明,该装置的设计完全可以满足各种使用条件下的装载量,而不会发生破坏现象。但也同时说明,应力分布不均匀,材料利用率低;在远小于屈服应力的情况下,有些构件没有发挥应有的作用,材料的经济性已被大大降低,造成材料的浪费。所以有必要对该装置进行优化,使得各构件应力分布均匀,提高材料的利用率。
声明:本网站所收集的部分公开资料来源于互联网,转载的目的在于传递更多信息及用于网络分享,并不代表本站赞同其观点和对其真实性负责,也不构成任何其他建议。本站部分作品是由网友自主投稿和发布、编辑整理上传,对此类作品本站仅提供交流平台,不为其版权负责。如果您发现网站上所用视频、图片、文字如涉及作品版权问题,请第一时间告知,我们将根据您提供的证明材料确认版权并按国家标准支付稿酬或立即删除内容,以保证您的权益!联系电话:010-58612588 或 Email:editor@mmsonline.com.cn。
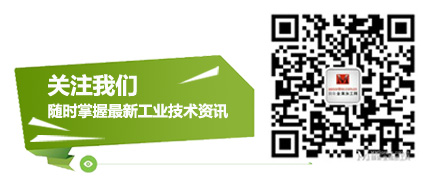
- 暂无反馈