高速切削加工的计算机数控(下)
通过补偿机床刚度和轨迹误差例如限制反转和预控制转速和转矩,有多种多样的调节结构可以提高生产率和零件加工精度。采用数字化驱动调节可以实现高分辨率的数字化转速和位置检测,可以实现更高阶的调节算法,尤其是通过预控制转速和转矩来补偿由惯性运动导致的轨迹误差,这在轨迹进给速度高、产生拖动误差时意义尤为重大。此外,它能够自动完成例如频率和圆度等多种检测,能够自动优化补偿例如借助神经网络进行象限误差补偿,可以连接直接直线驱动装置如直线电动机,可以用CNC处理器和驱动处理器来双重保障机床的安全性。
用于HSC的CNC功能
轨迹运动速度很高时,只有通过无拖动误差的调节策略才能满足加工精度的要求,并且速度增益在通常的Kv=1~4(m/min)/mm时没有阻尼存在,所以进给轴的插补控制意义重大。为了满足HSC的特殊要求,必需研究开发新的轨迹插补、速度控制以及几何变换方法。
上节说明了精确描述加工轨迹的高次插补方法和快速插补技术。除此之外,用于HSC的CNC必须满足以下要求:即超过100条程序段的速度预控制(前瞻功能),补偿机械误差;可进行几何变换(如夹紧时的修正或5轴变换);进给轴无拖动误差的调节以确保高的轨迹精度;在轨迹方向和轴向限制反向以保护机床,刀具长度、半径、类型不同时的补偿;在机床工作空间内能够安全操作。
速度预控制
速度预控制(前瞻)的任务,是识别速度不连续的程序段过渡和由轨迹弯曲所引起的进给轴过高的加速度。数控程序段的执行时间,比对切削加工速度必需的加速和制动梯度时间还要短。连续处理数控程序段的前提是具备一个处于预先监视下的程序缓冲区。需要注意的是,在轨迹进给速度高和程序段短的时候,技术上必需的低加速度会使速度预控制需要的前瞻距离增加到50至150条程序段。如果只有较小的前瞻缓冲区,就必须限制轨迹进给速度,以便使程序任何位置上的制动梯度时间都能得到遵守。
多轴变换与坐标变换实现刀具补偿
在旋转坐标系中的三维加工例如加工斜面,需要增加离线计算的程序中必需的数据量。同时需要在CNC程序中计算确定刀具参数如刀具类型、半径和长度。通过CNC内的几何变换,可以直接在机床上进行刀具补偿而省略后处理过程。
用球头铣刀作3轴加工,只能利用5轴铣床生产能力的一小部分。只有使用圆柱和圆环铣刀,才能发挥达到高的切削效率。为了在高质量加工任意轮廓表面的同时达到最大切削效率,要求它们相对铣刀轨迹有确定的空间方向。为保证刀具接触点落在轨迹上,在传统的用旋转轴确定刀具方向的5轴编程中必须插入许多中间步骤。
4轴和5轴变换承担在刀具方向改变时保持刀尖的空间位置不变的任务。编程的进给参数只涉及刀尖的空间轨迹。刀具的方向可以通过旋转轴位置、刀具方向矢量或欧拉角等编程确定。直接由CNC完成的对不同类型(如圆柱、圆环以及锥环)铣刀的空间几何参数的修正更具有补充作用,结果可以对相同的NC程序应用不同的刀具。
极坐标变换主要用于车削加工中心、非圆磨削以及高速铣削圆形或螺旋形零件。把旋转轴与直线移动轴相结合,可以避免改变直角坐标系各坐标轴方向以及引起理论轨迹的偏差。这种变换的一个重要优点,是进给的编程只与刀具轨迹有关,而不是象在旋转轴编程中那样与角速度有关。在这种变换中可以应用所有的插补方法(直线、圆弧、样条)编程。由CNC负责刀具补偿计算并监视轨迹方向和进给轴方向上的全部限制。
圆柱面变换使编程人员能够把圆柱表面的刀具轨迹视为虚拟的X-Y平面。此时所有几何表述和进给以零件表面为基准,与圆柱半径大小无关。
误差补偿
只要费用许可,就应当要求CNC系统补偿机床的静态误差、热误差以及进给轴调节的动态误差。这样能够达到零件的加工精度,过去机械补偿时需要花费高昂代价才能够达到。
对HSC技术的应用具有重要意义的误差补偿有:补偿由于丝杆转速高和进给轴速度高引起它们温度上升导致的热误差,补偿进给轴换向点处的摩擦误差(象限误差),补偿丝杆导程误差和测量系统误差,借助于插补技术补偿机床的角度和挠度变形误差,补偿间接测量的轴的松弛之处。
人员、机床和零件的安全
目前生效的安全保护条例,对几乎所有类型的机床都规定用罩壳封闭机床工作空间。这妨碍操作者在许多场合下必要地介入数控程序的运行。特别是在模型和模具制造中的大型机床上,操作者或机床安装调试人员在程序自动运行中熟练地进行鉴别或许还有校正是非常重要的。出于安全原因,这一要求只能通过CNC中规模庞大的限制和监视系统来实现。除了硬件监视的机床功能以外,首先包括对丝杆转速和进给运动进行的可靠的双通道监控。
3结束语
在高速切削加工的计算机数控中采用NURBS样条插补,可以克服直线插补时控制精度和速度的不足。通过高速计算机数控的速度预控制,多轴变换与坐标变换实现刀具补偿、误差补偿、劳动安全保护等其它功能,不仅能够提高进给速度和切削效率,而且能够提高复杂轮廓表面的加工精度和人员设备的安全性。高速切削加工对计算机数控系统提出的高新技术要求,只有应用数字化驱动调节和总线技术才能够实现。
声明:本网站所收集的部分公开资料来源于互联网,转载的目的在于传递更多信息及用于网络分享,并不代表本站赞同其观点和对其真实性负责,也不构成任何其他建议。本站部分作品是由网友自主投稿和发布、编辑整理上传,对此类作品本站仅提供交流平台,不为其版权负责。如果您发现网站上所用视频、图片、文字如涉及作品版权问题,请第一时间告知,我们将根据您提供的证明材料确认版权并按国家标准支付稿酬或立即删除内容,以保证您的权益!联系电话:010-58612588 或 Email:editor@mmsonline.com.cn。
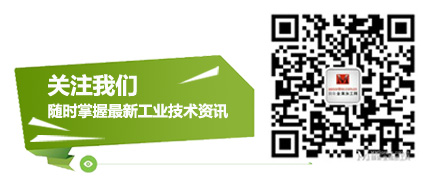
- 暂无反馈