CAD模型的输入及修补
一个有效的CAE分析,必须快速有效的建立有限元模型,而有限元模型的建立效率和质量很大程度上取决于你的CAD几何,如何快速地获取CAD几何,不是靠一般的有限元前处理器自带的可怜的实体建模工具,而是直接从CAD系统获取几何源,这一方面避免了重复建模,另一方面保证了设计与分析的一致性或叫CAD/CAE协同。所以现在的CAE前处理软件都提供了与CAD的数据转换接口:有能直接读取CAD原始文件格式的直接接口(如UG、Pro/E的.prt、CATIA的model、CATPart等),也有通过通用的中间数据格式(如:Parasolid、Acis、 STEP、VDA等)。是不是数据转换的问题解决了,其实不然,许多客户都在抱怨,化了很多钱买来了一大堆CAD接口,却还要为糟糕的模型花费很多的时间和精力来修补CAD几何。分析人员总在抱怨设计人员制作的CAD模型质量太差,有时甚至引起了设计部门和分析部门的扯皮。而且事实上,一般CAE前处理提供的CAD转换接口都有以下两个弱点:
1. 数据转换非常耗时。一个复杂的CAD模型往往要花费几十分钟、甚至几小时的时间。
2. 转换过来的模型质量差。经常会发生模型中的面丢失,甚至只流下辅助线,从而导致重复劳动。据统计,分析人员有50%-70%的时间化在重复劳动上。
CAD/CAE数据转换问题的类型和起因
引起数据转换问题主要起因有以下五类,而在许多情况下,它们之间又相互重叠和相互关联。
1. 结构上的
结构问题关心模型的外形、实体是否被正确定义和相互关联,例如,一个应该是三维实体的模型在目标应用中可能只有面了(甚至更糟,只有线框),这些问题可能是由于使用了不同的建模器(线框、曲面、实体或混合),或是由于在从源系统输出过程中没有被充分理解造成的。
模型在原始CAD系统中是一个实体零件,而在输出到下游的FEA应用时已没有了实体定义而在文件中只留下了辅助线。而通常的CAD接口只能按一个按钮(至多只有几个选项)
此时分析人员只能自己辨认和提取实体模型,或许准备从草图开始重新生成分析用的零件模型,对这个零件进行重建也许很容易,但是从用户质量保证(QA)的角度来讲他能接受吗?更重要的是,对于一个像发动机机体这样的大型复杂零件来讲是不切实际的,在这个例子中,数据交换是没问题的,所有数据被输出到文件中,也没有报告数据交换出错信息,但这些数据对接受者不可用。
2.精度
这或许许多数据转换问题的最主要起因,原因是不同的几何建模核心或者以一种固定的容差范围、或者提供一种变容差能力,使得用户可以根据自己的工作确定需要的精度。
有些系统采用绝对容差,如0.005mm或0.01mm,而另外一些系统采用相对模型尺寸的容差,如模型尺寸的10-4倍;还有一些针对不同的单位制采用不同的容差,而别的根本不考虑单位!
它带来的影响是,在一个较宽松的建模系统中可以很好表示的模型,在一个接受系统中由于容差太大而破损,这些实体看起来是不相连的,甚至超出所需容差限,还有严重的设计意图(design intent)问题,在一个系统中存在一条短的边或一个小的面,但是在一个下游的接受系统中由于一个较大的容差把它吞噬掉了。
3.现实性
典型的现实性问题是关于一个模型是否符合实际情况和有限元分析上能否划分网格,这样的问题通常反映在CAD模型中的特征问题,如刀棱边、细长面、带内部缺陷的实体、实体中的裂纹和紧箍面(材料厚度趋于0)等 。
问题的起因可能是用户或系统本身,可能是在进行布尔操作时实体位置错位留下一条细边,或发动机模型上打孔时由于延伸太远而在汽缸壁上切下一个钻孔缝。CAD系统失效也会产生现实性问题,如,一个实体建模操作的失败,可能会留下一个复制品,一个带缺陷的实体。
4.系统局限性
CAD系统和它基于的建模核心从容差要求、数学描述和几何复杂度来讲,具有不同的能力和复杂度层次 。
一个能生成高精度通用3D曲面的CAD系统通常会用上千个点来高度定义的曲面,这样的曲面在模型尺寸上会很大而且费时,有时会很难给下游使用。
通常发现许多非常复杂的几何在接受系统允许的容差范围内,可以被简化成基本曲面,如平面、柱面、锥面和球面,图7展示了一个被过度定义的曲面在允许的容差条件下可以用一种更基本的定义来描述。
还有对模型复杂读可接受的程度,在系统区分无效几何定义的标准上会有所不同,一个最能说明问题的例子是技术上无效的由3条边生成的退化NURBS曲面,有些系统能生成这样的实体,而有的系统则拒绝生成,还有的系统尽管不允许,为了防止生成这样的面,生成一个扭曲的四条边的曲面!
在复杂度问题上别的差别是面和边的连贯性,在某个特定的CAD系统中是否认为是不连续的。一个曲面在某个系统中可能是好的,但在下游系统中可能发现不连贯性,由此导致转换出错或应用失败,比如在一个不连续的面上划分网格是不可能的。
在当今的“宽容”建模器和别的系统之间的差别也是问题的起源,有可能在一个宽松系统中建立的有效模型可以在基于相同建模内核的系统间完全转换,而一旦模型输出到这个宽松环境外的系统时就会发现严重的问题。
5.转换和自动化
在任何一种转换方式中数据都有可能被曲解和错误转换,对于CAD数据转换标准如IGES和STEP,在所有的系统中实际使用时各不相同,它们会有自己的解释、模糊的描述,有时是不正确的实体,系统对给定标准下对实体的支持度也千差万别。所以这些会引起转换过程中潜在的问题,尤其是在完全自动化的过程中。
一个极好的比喻是语言翻译,拿一篇文章给三位翻译者去翻,就可能是三篇不同的文章,他们包含同样的信息,有或多或少的翻译贴切问题,但没有一个人能精确表达原文的意思。
除了这些,一个完全自动的过程总会产生‘垃圾进 – 垃圾出’的情况,CAD转换器还没有到这样智能的程度适应任何别的程序。
基本上,所有的系统在某些方面不尽相同,这意味着有很大的可能性产生协同性问题,出现在下游应用中。
展示的是关于现实性、精度和系统相关的协同性问题,一个简单的CAD零件似乎被成功地在两个系统之间进行转换,没有警告、出错和失败提示,下游的有限元分析师试图对这个零件进行网格划分,但失败了,这意味着将化大量的时间去解决这个协同性的问题。
在这个例子中问题的起因是有一个很小的特征面,极有可能在原始系统中在进行布尔连接操作时造成的,这个小的特征在原来的CAD系统中按其容差范围是完全可以接受的,而下游用户则面临着如何去除这条边,尽管从相对尺寸来讲是可以接受的,但会引起其它情况,带来设计意图问题。
数据转换问题的解决方案
就像别的严重问题一样,有两种可能的解决办法:防止和治疗。防止的措施有两个,首先,正确引导那些负责创建数据的人正确理解需求和这些数据可能的应用情况,其次,提供一些工具在引起严重问题之前自动设别那些可能出现的问题;治疗就是通过一种具备模型修补能力的转换工具解决模型导入问题。
1.从CAD源头进行防止
‘现实性’问题通过用户的细心建模、模型质量检查以及指定一定规范的流程和程序在一开始就防止生成一些不合实际的特征等方法加于避免,随着CAD软件的不断进步、修补程序中的缺陷、 程序更加健壮,就会减少建模过程中失效和不希望的缺陷。
‘系统’问题也在被改进,现在的软件正朝相互能理解的方向发展,大家更注意对方的特殊要求,但似乎能存在问题,即使所有的CAD系统基于同样的建模内核,所有软件共享数据格式和内部结构信息,系统问题在一段时间内仍将存在。
‘精度’问题仍是最严重的问题,因为它受整个软件的框架所制约,除非你改变软件的整个框架体系,或者采用一种新的建模内核,而这又要从商业角度考虑。
2.CAD模型质量检查
其实许多严重的下游问题起因于CAD中似乎微不足道的小的设计错误,比如,由布尔操作产生的一个小错误就可能会生成一个很小的几何,而它会引起网格算法和刀具路径生成器产生错误,但事实上在CAD系统中这完全是合理的。这样的错误是太容易发生了在设计中可能很难避免。
首先可以使用在源CAD系统中提供的模型质量和设计检查工具,这些检查工具可以是批处理方式运行或在CAD模型上生成图示化的检查报标示出所有用户认为可能引起协同性问题的设计问题。
像一些短的边、狭长面和差的面如果在早期能识别的话就可以被纠正,通过上游用户的简单重复工作可以大大改进下游接收数据的质量,研究表明,如果有合适的质量检查工具在上游被使用的话,就可以减少下游用户10%的重复工作量。
为了防止更多可能在下游应用中可能引起的问题,可以实施一种CAD模型质量检查机制,普信公司提供专门针对此类问题的解决方案,通过常规的诊断检查可以清楚地了解有那些错误发生和由谁造成的。
在模型检查中关心的其他焦点是减小CAD文件大小,有质量问题的模型通常会耗掉大量内存,通过这些检查可以发现由于采用不合理建模方法引起的问题,甚至有些就是由于建模器本身造成,所以,通过质量检查可以给CAD开发商反馈一些有价值的信息,让他们对系统进行改进。
3.修复和修补
尽管你在上游应用中使用了CAD质量检查工具来避免一些协同性问题,但仍有许多问题存在,如在前面已讨论过交换过程本身的、自动化和转换中的问题。依靠这种自动的非交互的交换工具有时会事情变得更糟,会使用户无所适丛。
解决的办法是采用一种数据交换工具,它能提供一种结合强大交互几何修补和操作的工具和服务的智能化的自动模型处理手段。
声明:本网站所收集的部分公开资料来源于互联网,转载的目的在于传递更多信息及用于网络分享,并不代表本站赞同其观点和对其真实性负责,也不构成任何其他建议。本站部分作品是由网友自主投稿和发布、编辑整理上传,对此类作品本站仅提供交流平台,不为其版权负责。如果您发现网站上所用视频、图片、文字如涉及作品版权问题,请第一时间告知,我们将根据您提供的证明材料确认版权并按国家标准支付稿酬或立即删除内容,以保证您的权益!联系电话:010-58612588 或 Email:editor@mmsonline.com.cn。
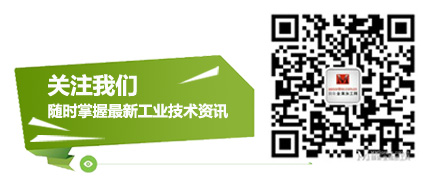
- 暂无反馈