模具结构对压铸件质量的影响与改进方法
引言
压铸模是进行压铸生产的主要工艺装备,生产过程能否顺利进行,铸件质量有无保证,很大程度上取决于模具结构是否合理。在压铸生产时,正确的压铸工艺是获得优质铸件的决定因素,压铸模则是正确选择和调整工艺参数的基础。压铸模结构、浇注系统、抽芯机构和冷却系统设计,直接影响铸件质量。
零件外形尺寸大,形状复杂,模具设计在630吨压铸机上生产。根据零件设计的模具有7处需抽芯,难度大。经试模,发现存在以下问题:①铸件表面质量差,有冷隔缺陷,充填不足,有缩孔;②3个内抽芯机构定位不稳,顶出机构易折断;③铸件变形量较大,质量不稳定。
模具结构改进
(1)针对问题①对浇注系统进行改进。由于原设计的浇道为开放式浇道,正对内浇口处的型腔尺寸较小,金属液与型腔瞬间碰撞后呈雾状,粘附于型腔壁上,使随后进入的金属液不能与它熔合而形成冷豆或冷隔缺陷,降低了表面质量。金属液在流动充填过程中,沿着铸件较长的一端充填时堵塞了溢流槽,影响整副模具的排气,而且在末端没有设置溢流槽和排气槽,使得金属液裹住空气,不能有效排气而形成气孔及缩孔,影响铸件质量。
改进后的模具结构,原开放式浇道改为导入式狭长浇道。把金属液引入型腔,在一侧设计了由宽到窄的浇道,起到了增压作用,使金属液在充填时,既有压力又有速度。为了使铸件的外表和内在质量更稳定,在动模较长一端型腔的末端,增设了溢流槽和排气槽。这样,溢流槽可积聚型腔内的冷金属和涂料,也加强了死角部位金属液的流动,排气槽又能使型腔内气流顺利排出,以引导金属液的充填。经过改进,对铸件末端的充填有很大帮助,铸件表面质量明显提高,气孔和缩孔现象基本消除。
(2)针对问题②对抽芯机构进行改进。原设计模具结构受浇道位置的限制,3个内抽芯只能设计为各自独立的斜推杆顶出机构,如图4、5所示。靠定位钉定位和推杆顶出,出现了定位不可靠现象。金属液冷却后对需抽芯型芯的抱紧力较大,在推出和脱模同时进行时,抽芯有一个横向力,推杆和型芯杆也有一个摩擦力,端面磨损较大,推杆受力后引起变形甚至折断,结构不稳定。同时由于铸件较长一端的2个单独推杆内抽芯定位不可靠,而造成铸件较长一端的形状、型孔位置不稳定。
改进后的模具在考虑改进浇注系统的同时,留出一定的位置,将2个单独的斜推杆内抽芯改为一个整体式斜销内抽芯。
采用整体式内抽芯后,锁紧力大,抽芯定位可靠,铸件的形状误差基本消除,解决了型芯位置不稳定和推杆磨损、易折断问题,提高了模具结构的稳定性。而在铸件另一端的1个单独内抽芯,抽芯机构改为型芯杆与推出机构同步推出的方案。
具体抽芯过程为:当模具闭合后,金属液充填完毕,铸件成型冷却,开模,推出机构推动上下顶板带动导轨向上移动,使型芯杆在动模镶块的斜孔内滑动,由于型芯杆与推出方向有一角度a,设推出距离为h,则抽芯距离L=h×tanα。在推出同时,固定型芯杆的滑块在水平方向也有一移动量S=h×tanα,当推出机构推出铸件一段距离后,设置在型芯杆上的型芯,逐渐脱离铸件,完成一次抽芯过程。经以上改进,模具结构更为合理,推出、脱模和定位更可靠,实用性较强,效果较佳。
(3)针对问题③对型芯增加冷却水管。由于铸件外形象U型架,壁厚不均匀,短的一端较厚,长的一端较簿,U型架底壁也较厚,因而压铸过程中铸件凝固冷却不一致,速度不均匀,导致铸件脱模后变形,不能达到铸件的尺寸精度。尤其是在模具工作一段时间后,模具温升过高,为了保证铸件质量,只能采用喷涂降温的方法,降低了生产效率,同时也增加了成本。由于模具一直处于高温状态下,加剧了模具表面的龟裂,缩短了模具的使用寿命。
为了获得合理的温度分布,在模具型腔内形成一个循环水流冷却系统,使模具有一个均匀的温度场。模具的冷却水道设置在动、定模温度较高的型腔区域。冷却水道的进水口设置在动模型芯温度最高、热量较集中的导入式浇道处,进到U型架较短的一侧后,沿着U型架底部,再由U型架较长一端出水。水道孔径为Φ10-12mm,距型腔底部约15mm。采用循环式冷却水道,使得循环水直接沿着型腔底部降温,具有冷却快、效率高、控制比较方便的特点,起到了平衡模具温度的作用,大大改善了铸件的成型质量,提高了铸件质量的稳定性,还能防止由于温度过高而产生粘模,延长了模具使用寿命。
结束语
通过对模具浇注系统、冷却系统和抽芯机构的改进,降低了维修率,提高了生产效率。模具在使用过程中,压铸工艺参数稳定,铸件质量符合要求,达到了预期效果。
声明:本网站所收集的部分公开资料来源于互联网,转载的目的在于传递更多信息及用于网络分享,并不代表本站赞同其观点和对其真实性负责,也不构成任何其他建议。本站部分作品是由网友自主投稿和发布、编辑整理上传,对此类作品本站仅提供交流平台,不为其版权负责。如果您发现网站上所用视频、图片、文字如涉及作品版权问题,请第一时间告知,我们将根据您提供的证明材料确认版权并按国家标准支付稿酬或立即删除内容,以保证您的权益!联系电话:010-58612588 或 Email:editor@mmsonline.com.cn。
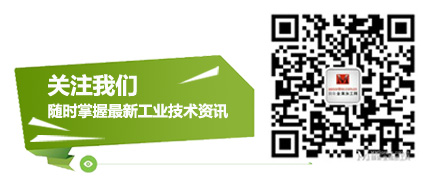
- 暂无反馈