DM32铝锰钴合金对压铸模具的要求
DM32铝锰钴合金具有纯度高、熔炼温度高、流动性差等特点,这就对模具的开发有了限制,主要要求如下:
一、 因铝温偏高,粘模倾向大,故对模具材料及热处理要求来格。
1、镶块、型芯等成形零件,选用质量高,适于表层氮化的热作模具钢,如瑞典8407、日本SKD61或美国精炼H13等(普通材料处理硬度过高极宜龟裂);淬火回火46~49HRC,氮化500~530HV。
2、顶针最好选用普通H13,淬火回火50-55HRC。
二、 因材料流动性差,模具设计尽可能减少流道转折, 保证流道畅通,对于复杂工件,推荐使用圆型浇道设计。
三、 常规模具设计,以内浇口到达工件各部位距离相近或相等为主要原则,此类模具设计,以避开直冲型腔,避免产生涡流、涡气为主导原则,因为有此问题,不仅容易造成冲蚀粘模,还会造成因工件密度不均而导致阳极氧化产生水纹。
四、 常规模具设计比较粗糙,此类模具流道与浇口设计要遵循以下原则:
1、 确保浇注系统截面积由直浇道到内浇口逐渐缩小,一般1:1.2~1.5,有分支浇道或分支浇口的,以总面积计算,并且要保证浇道的流畅;此操作可有效减少涡流、涡气环节。
2、 内浇口尽可能设于厚壁处,避免因内浇口处铝液过早凝固而影响铝液和压力的有效传递。
3、 尽量避免开设多个内浇口,因为铝液乱流可能对工件表面影响不大,但极易造成氧化水纹;如必须开设多个内浇口,则要首先考虑铝液开始充型部位不要互相撞击。
4、 普通模具内浇口厚度一般为1.0~2.5mm,此类模具因流动性差,内浇口厚度最低为1.5mm;内浇口过薄会造成进料口处涡气,形成气孔。
五、 环形浇注、环形排气在当前此类材料生产中是印证成功的一种进料排气模式,相近产品可以采用此法。
六、 脱模斜度:配合面外面最小脱模斜度为0°30″,内面1°;非配合面外部1°30″,内部2°,铸造圆角也大于普通模具设计。
七、 收缩率:收缩较大,计算规则如下(单位:mm):
较大限制收缩 较小限制收缩 无限制收缩 与分型面垂直
≤3 >3 ≤3 >3 ≤3 >3 ≤3 >3
0.3% 0.4% 0.4% 0.5% 0.6% 0.7% 0.7% 0.8%
八、 注意内浇口与工件的连接方式,对应工件缓冲长度低于15mm,不宜采取直接连接;工件允许情况下,尽可能采取底部45°角搭接方式(经过模流分析的有效充填模式),如冲蚀粘模,可逐步加大到70°角。不推荐使用内浇口中间设三角分流的充填模式(锥形浇注系统除外)。
九、 工件最薄压铸尺寸,面积低于35cm2,厚度最低不能超过1.2mm,超出压铸极限不能保证工件质量。
十、 凡属加工位置,保证顶针与工件持平,否则氧化后容易有气孔出现。
声明:本网站所收集的部分公开资料来源于互联网,转载的目的在于传递更多信息及用于网络分享,并不代表本站赞同其观点和对其真实性负责,也不构成任何其他建议。本站部分作品是由网友自主投稿和发布、编辑整理上传,对此类作品本站仅提供交流平台,不为其版权负责。如果您发现网站上所用视频、图片、文字如涉及作品版权问题,请第一时间告知,我们将根据您提供的证明材料确认版权并按国家标准支付稿酬或立即删除内容,以保证您的权益!联系电话:010-58612588 或 Email:editor@mmsonline.com.cn。
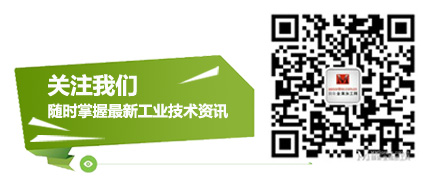
- 暂无反馈