模具热处理中存在的缺陷及预防
1.模具表面有软点
模具热处理后表面有软点,将影响模具的耐磨性、减少模具的使用寿命。
(1)产生原因
1)模具在热处理前表面有氧化皮、锈斑及局部脱碳。
2)模具淬火加热后,冷却淬火介质选择不当,淬火介质中杂质过多或老化。
(2)预防措施
1)模具热处理前应去除氧化皮、锈斑,在淬火加热时适当保护模具表面,应尽量采用真空电炉、盐浴炉和保护气氛炉中加热。
2)模具淬火加热后冷却时,应选择合适的冷却介质,对长期使用的冷却介质要经常进行过滤,或定期更换。
2.模具热处理前组织不佳
模具最终球化组织粗大不均、球化不完善,组织有网状、带状和链状碳化物,这将使模具在淬火后易产生裂纹,造成模具报废。
(1)产生原因
1)模具钢材料原始组织存在严重碳化物偏析。
2)锻造工艺不佳,如锻造加热温度过高、变形量小、停锻温度高、锻后冷却速度缓慢等,使锻造组织粗大并有网状、带状及链状碳化物存在,使球化退火时难以消除。
3)球化退火工艺不佳,如退火温度过高或过低,等温退火时间短等,可造成球化退火组织不均或球化不良。
(2)预防措施
1)一般应根据模具的工作条件、生产批量及材料本身的强韧化性能,尽量选择品质好的模具钢材料。
2)改进锻造工艺或采用正火预备热处理,来消除原材料中网状和链状碳化物及碳化物的不均匀性。
3)对无法进行锻造的碳化物偏析严重的高碳模具钢可进行固溶细化热处理。
4)对锻造后的模坯制定正确的球化退火工艺规范,可采用调质热处理和快速匀细球化退火工。
5)合理装炉,保证炉内模坯温度的均匀性。
3.模具产生淬火裂纹
模具在淬火后产生裂纹是模具热处理过程中的最大缺陷,将使加工好的模具报废,使生产和经济造成很大损失。
(1)产生的原因
1)模具材料存在严重的网状碳化物偏析。
2)模具中存在有机械加工或冷塑变形应力。
3)模具热处理操作不当(加热或冷却过快、淬火冷却介质选择不当、冷却温度过低、冷却时间过长等)。
4)模具形状复杂、厚薄不均、带尖角和螺纹孔等,使热应力和组织应力过大。
5)模具淬火加热温度过高产生过热或过烧。
6)模具淬火后回火不及时或回火保温时间不足。
7)模具返修淬火加热时,未经中间退火而再次加热淬火。
8)模具热处理的,磨削工艺不当。
9)模具热处理后电火花加工时,硬化层中存在有高的拉伸应力和显微裂纹。
(2)预防措施
1)严格控制模具原材料的内在质量
2)改进锻造和球化退火工艺,消除网状、带状、链状碳化物,改善球化组织的均匀性。、
3)在机械加工后或冷塑变形后的模具应进行去应力退火(>600℃)后再进行加热淬火。
4)对形状复杂的模具应采用石棉堵塞螺纹孔,包扎危险截面和薄壁处,并采用分级淬火或等温淬火。
5)返修或翻新模具时需进行退火或高温回火。
6)模具在淬火加热时应采取预热,冷却时采取预冷措施,并选择合适淬火介质。
7)应严格控制淬火加热温度和时间,防止模具过热和过烧。
8)模具淬火后应及时回火,保温时间要充分,高合金复杂模具应回火2-3次。
9)选择正确的磨削工艺和合适的砂轮。
10)改进模具电火花加工工艺,并进行去应力回火。
4.模具淬火后组织粗大
模具淬火后组织粗大,将严重影响模具的力学性能,使用时将会使模具产生断裂,严重影响模具的使用寿命。
(1)产生的原因
1)模具钢材混淆,实际钢材淬火温度远低于要求模具材料的淬火温度(如把GCr15钢当成3Cr2W8V钢)。
2)模具钢淬火前未进行正确的球化处理工艺,球化组织不良。
3)模具淬火加热温度过高或保温时间过长。
4)模具在炉中放置位置不当,在靠近电极或加热元件区易产生过热。
5)对截面变化较大的模具,淬火加热工艺参数选择不当,在薄截面和尖角处产生过热。
(2)预防措施
1)钢材入库前应严格进行检验,严防钢材混淆乱放。
2)模具淬火前应进行正确的锻造和球化退火,以确保良好的球化组织。
3)正确制定模具淬火加热工艺规范,严格控制淬火加热温度和保温时间。
4)定期检测和校正测温仪表,保证仪表正常工作。
5)模具在炉中加热时应与电极或加热元件保持适当的距离。
声明:本网站所收集的部分公开资料来源于互联网,转载的目的在于传递更多信息及用于网络分享,并不代表本站赞同其观点和对其真实性负责,也不构成任何其他建议。本站部分作品是由网友自主投稿和发布、编辑整理上传,对此类作品本站仅提供交流平台,不为其版权负责。如果您发现网站上所用视频、图片、文字如涉及作品版权问题,请第一时间告知,我们将根据您提供的证明材料确认版权并按国家标准支付稿酬或立即删除内容,以保证您的权益!联系电话:010-58612588 或 Email:editor@mmsonline.com.cn。
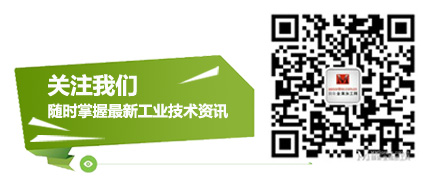
- 暂无反馈