模具失效主要形式
实际出产中,模具失效主要有三种形式:
①热疲惫龟裂损坏失效;
模具热疲惫龟裂失效 压铸出产时,模具反复受激冷激热的作用,成型表面与其内部产生变形,相互牵扯而泛起反复轮回的热应力,导致组织结构二损伤和丧失韧性,引发微裂纹的泛起,并继承扩展,一旦裂纹扩大,还有熔融的金属液挤入,加上反复的机械应力都使裂纹加速扩展。 为此,一方面压铸起始时模具必需充分预热。另外,在压铸出产过程中模具必需保持在一定的工作温度范围中,以免泛起早期龟裂失效。同时,要确保模具投产前和制造中的内因不发生题目。因实际出产中,多数的模具失效是热疲惫龟裂失效。
②碎裂失效
碎裂失效 在压射力的作用下,模具会在最薄弱处萌生裂纹,尤其是模具成型面上的划线痕迹或电加工痕迹未被打磨光,或是成型的清角处均会最先泛起细微裂纹,当晶界存在脆性相或晶粒粗大时,即轻易断裂。而脆性断裂时裂纹的扩展很快,这对模具的碎裂失效是很危险的因素。为此,一方面凡模具面上的划痕、电加工痕迹等必需打磨光,即使它在浇注系统部位,也必需打光。另外要求所使用的模具材料的强度高、塑性好、冲击韧性和断裂韧性均好。
③溶蚀失效
熔融失效 前面已讲过,常用的压铸合金有锌合金、铝合金、镁合金和铜合金,也有纯铝压铸的,Zn、Al、Mg是较活泼的金属元素,它们与模具材料有较好的亲和力,特别是Al易咬模。当模具硬度较高时,则抗蚀性较好,而成型表面若有软点,则对抗蚀性不利。
致使模具失效的因素良多,既有外因(例浇铸温度高低、模具是否经预热、水剂涂料喷涂量的多少、压铸机吨位大小是否匹配、压铸压力过高、内浇口速渡过快、冷却水开启未与压铸出产同步、铸件材料的种类及成分Fe的高低、铸件尺寸外形、壁厚大小、涂料类型等等)。也有内因(例模具本身材质的冶金质量、坯料的锻制工艺、模具结构设计的公道性、浇注系统设计的公道性、模具机(电加工)加工时产生的内应力、模具的热处理工艺、包括各种配合精度和光洁度要求等)。 模具若泛起早期失效,则需找出是哪些内因或外因,以便今后改进。 但在实际出产中,溶蚀仅是模具的局部地方,例内浇口直接冲洗的部位(型芯、型腔)易泛起溶蚀现象,以及硬度偏软处易泛起铝合金的粘模。 压铸出产中常遇模具存在的题目留意点:1、 浇注系统、排溢系统
例(1)对于冷室卧式压铸机上模具直浇道的要求:
① 压室内径尺寸应根据所需的比压与压室布满度来选定,同时,浇口套的内径偏差应比压室内径的偏差适当放大几丝,从而可避免因浇口套与压室内径不同轴而造成冲头卡死或磨损严峻的题目,且浇口套的壁厚不能太薄。浇口套的长度一般应小于压射冲头的送出引程,以便涂料从压室中脱出。
② 压室与浇口套的内孔,在热处理后应精磨,再沿轴线方向进行研磨,其表面粗拙≤Ra0.2μm。
③ 分流器与形成涂料的凹腔,其凹入深度即是横浇道深度,其直径配浇口套内径,沿脱模方向有5°斜度。当采用涂导入式直浇道时,因缩短了压室有效长度的容积,可进步压室的布满度。
(2)对于模具横浇道的要求
① 冷卧式模具横浇道的进口处一般应位于压室上部内径2/3以上部位,以免压室中金属液在重力作用下过早进入横浇道,提前开始凝固。
② 横浇道的截面积从直浇道起至内浇口应逐渐减小,为泛起截面扩大,则金属液流经时会泛起负压,易吸入分型面上的气体,增加金属液活动中的涡流裹气。一般出口处截面比入口处小10-30%。
③ 横浇道应有一定的长度和深度。保持一定长度的目的是起稳流和导向的作用。若深度不够,则金属液降温快,深渡过深,则因冷凝过慢,既影响出产率又增加回炉料用量。
④ 横浇道的截面积应大于内浇口的截面积,以保证金属液入型的速度。主横浇道的截面积应大于各分支横浇道的截面积。
⑤ 横浇道的底部两侧应做成圆角,以免泛起早期裂纹,二侧面可做出5°左右的斜度。横浇道部位的表面粗拙度≤Ra0.4μm。
(3)内浇口
① 金属液入型后不应立刻封锁分型面,溢流槽和排气槽不宜正面冲击型芯。金属液入型后的流向尽可能沿铸入的肋筋和散热片,由厚壁处想薄壁处填充等。
② 选择内浇口位置时,尽可能使金属液流程最短。采用多股内浇口时,要防止入型后几股金属液汇合、相互冲击,从而产生涡流包气和氧化夹杂等缺陷。
③ 薄壁件的内浇口厚件要适当小些,以保证必要的填充速度,内浇口的设置应便于切除,且不使铸件本体出缺损(吃肉)。 (4)溢流槽
① 溢流槽要便于从铸件上去除,并尽量不损伤铸件本体。
② 溢流槽上开设排气槽时,需留意溢流口的位置,避免过早梗阻排气槽,使排气槽不起作用。
③ 不应在统一个溢流槽上开设几个溢流口或开设一个很宽很厚的溢流口,以免金属液中的冷液、渣、气、涂料等从溢流槽中返回型腔,造成铸件缺陷。
2、 锻造圆角(包括转角) 铸件图上往往注明未注圆角R2等要求,我们在开制模具时切忌忽视这些未注明圆角的作用,决不可做成清角或过小的圆角。锻造圆角可使金属液填充顺畅,使腔内气体顺序排出,并可减少应力集中,延长模具使用寿命。(铸件也不易在该处泛起裂纹或因填充不顺而泛起各种缺陷)。例尺度油盘模上清角处较多,相对来说,目前兄弟油盘模开的最好,重机油盘的也较多。
3、 脱模斜度 在脱模方向严禁有人为造成的侧凹(往往是试模时铸件粘在模内,用不准确的方法处理时,例钻、硬凿等使局部凹入)。
4、 表面粗拙度 成型部位、浇注系统均应按要求当真打光,应顺着脱模方向打光。因为金属液由压室进入浇注系统并填满型腔的整个过程仅0.01-0.2秒的时间。为了减少金属液活动的阻力,尽可能使压力损失少,都需要流过表面的光洁度高。同时,浇注系统部位的受热和受冲蚀的前提较恶劣,光洁度越差则模具该处越易损伤。
5、 模具成型部位的硬度 铝合金:HRC46°左右 铜:HRC38°左右 加工时,模具应尽量留有修复的余量,做尺寸的上限,避免焊接。
压铸模具组装的技术要求:
1、 模具分型面与模板平面平行度的要求。
2、 导柱、导套与模板垂直度的要求。
3、 分型面上动、定模镶块平面与动定模套板高出0.1-0.05mm。
4、推板、复位杆与分型面平齐,一般推杆凹入0.1mm或根据用户要求。
5、模具上所有流动部位流动可靠,无凝滞现象pin无串动。
6、滑块定位可靠,型芯抽出时与铸件保持间隔,滑块与块合模后配合部位2/3以上。
7、浇道粗拙度光滑,无缝。
8、合模时镶块分型面局部间隙<0.05mm。
9、冷却水道畅通,进出口标志。
10、成型表面粗拙度Rs=0.04,无微伤。
声明:本网站所收集的部分公开资料来源于互联网,转载的目的在于传递更多信息及用于网络分享,并不代表本站赞同其观点和对其真实性负责,也不构成任何其他建议。本站部分作品是由网友自主投稿和发布、编辑整理上传,对此类作品本站仅提供交流平台,不为其版权负责。如果您发现网站上所用视频、图片、文字如涉及作品版权问题,请第一时间告知,我们将根据您提供的证明材料确认版权并按国家标准支付稿酬或立即删除内容,以保证您的权益!联系电话:010-58612588 或 Email:editor@mmsonline.com.cn。
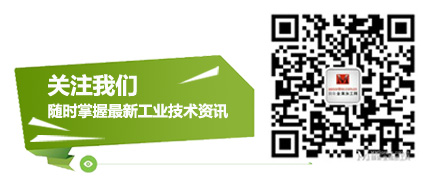
- 暂无反馈