汽车塑料管材/管件的成型加工技术
汽车塑料管材/管件主要包括进气管组件及排气管组件,这些管材/管件的塑料化不但可以减轻汽车重量及降低制造成本,而且也能大大提高汽车性能,是汽车科技进步的必然发展趋势。汽车塑料管材/管件的形式及规格较多,性能要求各有差异,成型工艺也不同。因此,根据管材/管件的使用条件和性能要求,采用科学的成型加工工艺,使之达到最佳的性能,是加工商应该也必须注意的问题。本文介绍了几种重要的汽车塑料管材/管件的成型加工方法。
塑料进气歧管的成型加工
进气岐管是一种形状复杂的中空件,基本功能是将汽油和空气按照一定比例混合变成“混合气”,再将混合气分配到发动机的各个气缸中,使之充分燃烧。进气岐管可由铝合金和塑料制成,然而塑料歧管较铝合金歧管具有很多优势,包括:塑料进气歧管的内壁比较光滑,有利于提高进气充量,可使发动机的动力性较铝合金进气歧管提高3%~5%;塑料进气歧管的管壁更薄,一般仅为2.5~3mm,而铝合金进气歧管的壁厚一般大于4mm;通过采用塑料取代金属,使得进气歧管减轻了约40%的重量,从而提高了燃油效率并减少了排放;塑料进气歧管的生产成本通常比铝合金进气歧管低20%~35%;塑料进气歧管的残余应力低,因而具有更好的力学性能。正是因为这些优势,如今在欧美等发达国家,大约有90%的进排气异侧的自然吸气发动机都使用了塑料进气歧管。此外,随着欧Ⅳ排放标准的实行,要求新型的发动机进气歧管必须配备电控可变进气阀等复杂的内部控制机构。由于金属进气歧管难以满足这一要求,因此进气歧管的塑料化是大势所趋,并且开发性能优异的塑料进气歧管是适应未来发动机技术进步的必然要求。下面介绍几种塑料进气歧管的成型方法。
1.可熔芯注射成型
可熔芯注射成型是“可熔型芯注射中空塑料成型”的简称,适于加工内部具有交叉复杂的管道、凹槽或切槽而难以脱模的进气歧管。该工艺利用低熔点的金属(或者易溶于化学溶剂的聚合物)作为注塑模具的型芯来生产,满足了进气歧管内外表面形状复杂、内壁光洁以及内部尺寸精确的要求。可熔型芯注射成型进气歧管由于内壁光滑,减少了液体/气体的流动阻力,从而降低了能耗。另外,岐管各部位的壁厚可根据强度要求进行设计,不仅设计空间大,而且有利于降低塑料原料的消耗量,达到进一步减轻重量及降低成本的目的。
可熔芯注射成型的基本原理是:先用低熔点合金(如低熔点(138℃)的锡/铋合金或者易溶于化学溶剂的聚合物)制成可熔型芯,然后把可熔型芯放入模具中进行成型,制件从模腔中取出后,对其加热将可熔型芯熔化,或者将其溶于化学溶剂。这种技术的关键是:塑料注射时,型芯不能熔化;用作型芯的金属的熔体以及用来溶解型芯的介质不能腐蚀塑料;在熔化型芯的温度下,制件不能发生变形。此外,加工商还应了解和注意:在可熔芯成型工艺中,型芯仅仅作为模壁,且充模过程不因固态嵌件而改变;由于金属合金型芯与聚合物型芯的热性能大不一样,故其所要求的压力也有所不同;聚合物型芯起到隔绝壁的作用,并且在成型制件中产生非常薄的流体表皮,而金属型芯成为散热点而在制件上形成相对厚的流体表皮;如果塑料熔体流过型芯时,型芯表面已熔化,将会产生流动的根本性变化。
德国宝马汽车公司于20世纪80年代率先采用熔芯法成功生产出玻璃纤维增强尼龙进气歧管,从而开启了改性尼龙在进气歧管中的大规模应用。而德国福吕登伯格公司则利用熔芯法生产出了BMC材料的进气歧管,这种歧管的内表面十分光滑,有助于空气流入,可使发动机的效率较金属歧管提高15%,且歧管质量减轻了1kg。
2.注射焊接成型
(1)注射振动摩擦焊接成型
在设计塑料进气歧管时,可将结构复杂的进气歧管拆分为结构相对简单、能一次注塑成型的两片或多片,然后利用摩擦焊机将各片焊接起来,构成完整的塑料进气歧管。目前绝大多数塑料进气歧管生产厂家都采用振动摩擦焊接技术。其主要优点是生产效率高、成本低和灵活性高,缺点是焊缝处的强度低、外观不好以及气体流动性相对较差。
(2)注射激光焊接成型
激光焊接法比振动焊接法成型条件温和,制品焊接质量好,残余应力小,可以焊接异形曲面,生产效率高,而且可以制得结构和形状更复杂的进气歧管。为适应激光焊接,许多材料厂家投入相当大精力开发用于进气歧管的激光焊接尼龙牌号。例如,拜耳材料科技推出了3个可激光焊接的黑色玻纤增强尼龙6牌号;杜邦公司开发出激光焊接尼龙66配混料;巴斯夫推出的激光焊接尼龙6牌号Ultramid B3GLT的激光透过率高达72%,可缩短制造形状复杂的进气歧管时的焊接时间。
3.模具滑动注射成型
模具滑动注射成型的原理是:采用将管材/管件一分为二的产品设计,首先在同一模具中将两部分分别注塑成型成半成品;然后将两部分半成品在模具中滑动至对合位置;二次合模,在制品的两部分结合缝再注射塑料熔体(二次注射),最后得到完整的中空制品。与吹塑工艺相比,该法成型的管材/管件具有表面精度高、尺寸精度高、壁厚均匀及设计自由度大的特点。在制造形状复杂的中空制品时,模具滑动注射中空塑料成型法与超声波焊接相比的优点是:不需将半成品从模具中取出,因而可避免半成品在模具外冷却所带来的制品形状精度下降的问题,同时亦可避免焊接法因局部应力产生而造成的熔接缝区强度下降的问题。
4.管件组件的注射焊接复合成型加工
巴斯夫与丰田汽车公司合作采用一种玻璃纤维强化的Ultramid聚酰胺制造进气歧管组件,首先采用“可熔芯成型法”生产进气歧管,然后用“振动焊接”工艺将有关的3个部件连接为一体。这种进气歧管组件因歧管长度可变并加强了空气补给,从而显著提高了发动机在加速等方面的性能;通过与相邻组件(如空气滤清器壳体、气门罩盖或发动机罩盖等)的功能性整合,实现了多个部件的一体化,从而大大降低了重量与成本。
另外,巴斯夫也与MANN+HUMMEL公司合作开发出了第一款在直接喷射式汽油发动机中应用的塑料可变进气歧管组件,该组件已经被用于新型奥迪A2 4.0 FSI 4V系列的生产中。这种新开发的歧管的下部和内部零件均由Ultramid B3WG6加工而成,由于材料在尺寸、热学和化学方面良好的稳定性,并通过注塑成型和振动焊接对两种产品进行加工,从而确保了组件具有理想的耐爆破压力。
3D异型管挤吹成型
3D挤吹异型管成型设备是为适应成型形态复杂的异型管而发展起来的一种设备,主要具有以下优点:对合模力的要求较低;切除料边的工作量减少;不必对成型品的外部直径重新修正;成型品的管壁厚薄比较均匀,管子整体强度趋于一致,从而提高了使用寿命。
汽车工业对形态复杂输送管件的需求增加,推动了3D挤吹异型中空管设备的发展。3D挤吹异型中空管的成型工艺是:型胚挤出后,被预吹涨并贴紧在一侧模具壁上,挤出头或模具按成型编制的程序进行2轴或3轴的转动,当类似肠形的型胚充满模腔时,另一侧模具闭合并包紧型胚,使之与后续的型胚分离,这时整个型胚被吹胀并贴紧在模腔的壁上以完成成型。
目前,国外使用3D异型管挤吹设备生产汽车用复杂外形管已十分普遍,在我国也有多家汽车主机厂引进了3D异型管吹塑设备。例如,沈阳金杯汽车公司引进了SIG Blowtec水平3D挤吹异型管塑料成型机,用来制造汽车进气管。
汽车复合管多层共挤成型
在汽车行业,现在已越来越多地使用多层复合管来代替单层塑料管,尤其是燃油管,高阻隔性的多层共挤管已成为其发展方向。纳米高阻隔技术应用于多层复合汽车燃油管,可通过降低燃油管对汽油、甲醇和有机溶剂的渗透率,进一步提高管子的阻隔性能,来符合越来越严格的汽车燃油挥发泄漏量的标准。例如,意大利菲亚特(Fiat)汽车公司用PA纳米复合材料作为燃油管阻隔材料替代原来的PVDF阻隔材料,使得管子对汽油的阻隔性提高了3倍。这种多层燃油管的层结构包括PA12外层、PA6/PA12共聚物粘结层、含2%纳米粘土的PA6/PA66共聚物阻隔层以及PA66内层,由于全都是PA材料,十分便于回收。
声明:本网站所收集的部分公开资料来源于互联网,转载的目的在于传递更多信息及用于网络分享,并不代表本站赞同其观点和对其真实性负责,也不构成任何其他建议。本站部分作品是由网友自主投稿和发布、编辑整理上传,对此类作品本站仅提供交流平台,不为其版权负责。如果您发现网站上所用视频、图片、文字如涉及作品版权问题,请第一时间告知,我们将根据您提供的证明材料确认版权并按国家标准支付稿酬或立即删除内容,以保证您的权益!联系电话:010-58612588 或 Email:editor@mmsonline.com.cn。
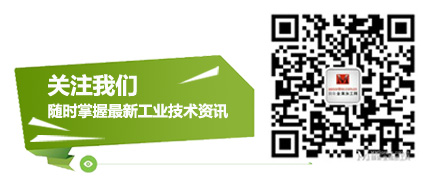
- 暂无反馈