感应熔炼技术在铸铁生产中的应用及发展
熔炼技术是铸铁生产的关键环节之一,其设备一般采用冲天炉较多。1个时期以来,感应熔炼炉得到迅速发展,在电力充足的情况下,日渐取代冲天炉。目前,无芯工频感应炉容量已达110 t,有芯工频感应炉容量则高达270 t。近年来,中频感应炉的发展及其所呈现的优越性,给铸铁生产注入了新的活力。
1 2种感应熔炼炉
目前,在铸铁生产中应用最多最普遍的感应熔炼炉有工频感应炉和中频感应炉。
工频感应炉能使金属熔化和升温,且加热均匀烧损少,便于调节铁液的成分、污染小。但工频感应炉熔化冷料速度慢、不利于造渣、冷炉启动需启动块、生产不够灵活、故一般常用于金属和合金的重熔与升温。另外,工频感应炉功率因数低,需配置大量补偿电容器,也增加了占地面积和设备投资。
中频感应炉则电效率和热效率高、熔炼时间短、省电、占地面积较少、投资较低,易于实现过程自动化和具有生产灵活性。
中频感应炉适合熔炼铸铁,特别适合熔炼合金铸铁、球墨铸铁和蠕墨铸铁。它对炉料的适应性也较强,炉料的品种和块度可在较宽的范围内变动。应该指出,虽然中频感应炉优点较多,发展较快,但工频感应炉则在铁液贮存、保温、调整合金成分和过热升温等方面,仍不失为1种良好的设备,尤其是作为高炉、冲天炉等熔炼炉的双联用炉仍然得到广泛应用。世界上最著名最大的离心球墨铸铁管生产厂家,法国的木松桥公司就采用工频感应炉与高炉双联工艺,而日本久保田公司则采用工频感应炉与冲天炉双联工艺。首钢铸造厂早在80年代初,就在国内首先采用了工频感应炉与高炉或冲天炉双联工艺,试制成功连续铸造铸态球墨铸铁管,并在以后的生产提供着高温优质铁液,一直延用至今,效果良好。
2 中频感应炉的发展
目前,工频感应炉向大容量发展已基本停止,中频感应炉的发展则令人瞩目。
2.1 静力变频器
中频感应炉的发展得益于静力变频器的使用,这种变频器和磁力变频器比较,其效率高达95%~98%。作为感应炉使用的变频器额定功率不断提高,近来,9 000 kW变频器已投产,把它联接在容量为12 t的炉子上,熔化铁液的生产率可达18 t/h;将中频感应炉功率密度每吨熔化能力提高到1 000 kW,能使熔化期缩短到35 min。感应炉的熔化率是随炉子的容量变化而变化,一般中频感应炉熔化铸铁的熔化率为0.4~35 t/h。例如,使用2 t容量的炉子,可得到2~2.38 t/h的熔化率,使用12 t的炉子则可达到18~21 t/h的熔化率;而采用工频感应炉熔化冷料的熔化率,1.5 t炉为0.75 t/h、3 t炉为1.5 t/h、5 t炉为2.5 t/h,10 t炉只有4 t/h。可见中频感应炉的熔化率远远超过了工频感应炉,这就为在选择铸铁生产熔炼设备时可以以小代大,使用较小容量的中频感应炉代替较大容量的工频感应炉创造条件,中频炉取代工频炉既减少了用地,又降低了投资,也保证了铁液的连续供应,对于连续作业、生产能力较大的铸铁生产均十分有利。将中频感应炉用于连续铸造或离心铸造球墨铸铁管生产的铁液熔炼,用它取代冲天炉,或与高炉、冲天炉进行双联,其生产能力将可得到充分发挥。例如,国内有1个离心球墨铸铁管生产厂家,就是采用了10 t中频感应炉与高炉双联工艺,对铁液进行升温和调整成分,将贮存的高炉铁液从1300 ℃升温到1520 ℃,大约需要27 min。该炉频率100~200 Hz,功率为2 500 kW。
中频感应炉电效率和热效率高,不但提高了熔化率、缩短了熔化时间,其单位电耗也相应降低。与工频感应炉相比,其电耗可从700 kW.h/t降低到515~580 kW.h/t。有关资料表明,在考虑炉渣的熔化和过热所需能量损失的情况下,中频感应炉冷启动时,单位电耗约582 kW.t/h,热炉操作时,单位电耗为505~545 kW.h/t,如果连续加料操作,则单位电耗仅为494 kW.h/t。
2.2 生产灵活性
中频感应炉在生产安排上有较大的弹性,熔化操作有较大的灵活性。对于工频感应炉,要求不间断地连续工作,因为间断会增加冷启动,冷启动不但增加熔化时间和能源消耗,且每1次都还必须使用启动块。而中频感应炉在间断短时间使用时,则可不使用启动块就进行冷启动,更换炉料十分方便,铁液又可完全倒空,能实现在短时间内的材质更换,有利于生产组织安排。这为单件小批量生产带来有利条件。例如,钢铁冶金企业中的行业性机修厂,主要承担钢铁企业所需的备品、备件及大宗消耗件的生产,并承担一些非标准设备的制造,又多是单件小批量生产,品种较多,材质要求经常变换。在这方面中频感应炉所具有的生产灵活性,弥补了工频感应炉及其它熔炼用炉的不足。
2.3 炉体结构
随着中频感应炉功率密度的不断提高,也就对炉子的安全运行、提高炉衬寿命和降低噪音等要求越来越高,炉体结构的合理性也就越来越为人们所重视,其中重型钢壳炉具有耐久性强、效率高、生产率高且噪音小、易于维修等许多优点。
重型钢壳炉与框架炉不同,它是设置有多个较大检查口的高强度环型钢壳,炉子运行时,检查口是关闭的,检修时则每个检查口均可打开。重型钢壳炉内部结构结实,可以避免倾斜出铁浇注可能引起的变形,延长了炉衬寿命,而且由于封闭的坚固炉壳及其内部可增加吸音隔离材料,使得工作噪音大大降低。结实的钢壳还能够有效地保护感应线圈避免飞溅金属的危险,使炉子在运行过程中具有最大的安全性。为了有效地隔热保温并提高炉衬寿命,重 型钢壳炉还在顶部和底部分别设置了冷却环,起到了均匀炉衬温度,降低热膨胀作用。低能耗、高强度的不锈钢冷却环,大大提高了炉子效率。
重型钢壳炉不仅有坚固的钢壳,而且设计了专门用于感应熔炼的厚壁管结构线圈,并通过正确选择感应线圈的匝间距离使得线圈的转换效率最高、电阻最小。1方面,厚壁感应线圈载流截面大、壁厚均匀、不易发生因电弧和膨胀引起的破坏,另1方面,线圈采用特殊的支撑系统,每1匝都被牢牢锁紧,刚性好,减少了由于电磁力引起的振动,大大延长了炉衬的使用寿命。另外,这种感应线圈的周围覆盖了50%的磁轭,有效地改变了磁场的分布。同时隔离缓冲垫也降低了噪音和振动,增加了磁轭的效率。重型钢壳炉还采用感应线圈延伸并超过炉衬底部的加长线圈设计,从而使得从炉体顶部到底部之炉料负载与磁场的耦合非常均匀,提高了能量转换效率,也减少了因磁场产生的搅拌力对底部炉衬的影响。
合理的炉体结构十分重要,重型钢壳炉只是其中1种。不少厂家都在致力改进炉体结构,以适应中频感应炉的应用与发展。
2.4 除渣与修炉
中频感应炉生产率高,熔化期可缩短到35 min左右,为了最大限度利用炉子的功率,必须尽可能快地除渣。采用撇渣器或人工除渣,效果均差且时间较长,劳动条件恶劣。为了解决这个非常费时而又繁重的作业,出现了1种炉子后倾出渣方法,即通过炉体顶部后边 的开槽将炉渣倒入运输车里,这种方法既快捷又方便。炉子后倾角度一般为20 °~25 °。
中频感应炉工作1个炉役后,必须进行拆除和修炉。为了缩短更换耐火材料炉衬的停炉时间,必须考虑机械化,振动筑炉和炉衬推出机也就成了大型感应炉的主要配件。炉衬推出机可以在耐火材料炉衬完全冷却之前将其推出,进一步缩短了修炉时间,改善了劳动环境。
2.5 双供电电源与控制系统
中频感应炉的1个独特发展是用1套供电系统向2台炉子供电,实现了无生产间隔作业的工作制度。实践证明,1台感应炉的总有效功率通常在整个熔化期不能被充分利用,在测定铁液温度、取样、除渣、出铁、尤其是在浇注的情况下,都要降低功率或切断电源。如果浇注周期较长,利用率只有50%左右,这表明要想达到所需要的生产率,电源设备的额定功率需是利用率为90%的1.8倍。为了解决这个问题,研制成功了1种双电源系统。该系统使用2个相同的换流器和电容器组,每台炉用1组,但都用共同的整流器和变压器来供电,每个换流器均可单独控制,能够将总有效功率以任意比例分配到2台炉子里。这种系统除对1台炉子保温提供充足的电力外,其余功率都可用于第2台炉子进行铁液熔炼。一旦熔炼炉准备浇注,其换流器的功率立即降低到保温水平;此时另1台炉子则倒空,然后重新装冷料,提高换流器的功率,开始新的熔炼。如有必要,可将总有效功率接到1台炉子上,另1台炉子停用;或将总有效功率平均分配到2台炉子上,使其同时熔炼。例如,美国应达公司DUAL-TRAK双供电电源及控制系统,就是可同时向2台炉子供电,且输送给2台炉子的功率是无级分配的。采用这种电源可同时向1台炉子输送熔化功率,向另1台炉子输送保温功率,使电源利用率达到100%。这种电源向2台炉子同时送电,完全避免了切换开关或另加1套电源,不必在熔炼中将电源切换到保温炉子上以保持必要的浇注温度,从而使中频炉实现了熔化和保温2种功能。当1台炉子处于维修状态时,电源可与这台炉子隔离,而只给另1台炉子供电,也增加了安全性。
应该提到的是,配有双供电电源与控制系统的中频感应炉,即使在1台炉子烘炉时,也能保证另1台炉子正常生产,从而实现铁液的及时连续供应,这也是工频感应炉无法比拟的。首钢铸造厂1变2炉实践证明,2台10 t工频感应炉使用1套电源供电,在1台炉子烘炉时,另1台炉子也不能生产。如果1次烘炉约需3天时间,则1年当中约1个月不能生产,影响极大。为了实现能够连续生产的目的,1是增加工频感应炉数量,2是增加1套烘炉电源设备。首钢铸造厂在建设离心球墨铸铁管车间时,就是在原有1变2炉基础上增加1台工频感应炉及相应的电源设备;国内另1个离心球墨铸铁管生产厂家则在原有1变2炉基础上,拟增加1套烘炉电源设备。无论采用如上所说的哪种措施,都要增加相应的设备与设施,也就增加了占地与投资。中频感应炉双供电电源与控制系统的应用,不但同时保证了熔炼和保温,也同时实现了烘炉不停产。
2.6 自动化程度
中频感应炉采用计算机控制系统,自动化程度较高。对于大功率中频感应炉,熔化期非常短、过热率非常大,只有采用计算机控制系统才能发挥设备潜力,才能对工厂和操作人员提供最有效的保护。25~30 ℃/min速率过热熔化炉料的炉子,在满功率状态几分钟无人看管,很可能造成灾难性事故。目前,大型中频感应炉已装备了比较完整的计算机辅助监视和控制系统,其主要内容包括:
(1)当炉子坩埚中铁液达到预编程温度时,保证自动降低炉子功率;
(2)炉子固定在测重仪上,测重仪为计算机提供炉子里金属炉料的质量数据;
(3)监测、计算和控制铁液温度;
(4)为新炉衬提供自动烧结程序;
(5)确定达到要求的铁液成分所需要的碳、硅及其他添加元素的数量;
(6)包括1台自动冷启动装置在内的其他有用的必要的功能。
另外,安装自动化机械装料系统也是发挥大功率中频感应炉全部潜力所不可缺少的。一般安装在轨道上可做横向和纵向移动或绕枢轴转动的振动给料系统最为合适。
高效中频感应炉的熔化处理系统是由熔化处理机监控整个熔化过程所需的功能及操作程序的,这个处理系统是由1个带有彩色监控器的微处理机组成的。工作时,在炉子装料系统和称重系统的共同作用下,自动计算熔化到浇注温度所需的功率,控制熔化期炉子熔化过程所需能量的吸收。在电桥的作用下,实现炉子熔化过程的自动装料;熔炼完毕铁液达到浇注温度,处理系统能够自动转换保温过程,可以用最小的能量达到预想的过热度;通过附加程序,在最利于保护炉衬的情况下,自动控制炉子冷启动和炉衬耐火材料的烧结过程。
熔化处理系统能够对电源和炉体进行全面自诊断,如果非正常状态启动了系统报警,该处理系统可以提供问题所在,并可将这些故障信息存储起来,也可与打印机相连进行打印保留。
3 结束语
中频感应炉比工频感应炉具有更多优点,它适合熔炼各种铸铁,特别适合熔炼合金铸铁和球墨铸铁,近年来在铸铁生产中已愈得到广泛的应用。该炉生产率高、节能省电且有较大生产灵活性,对于诸如钢铁冶金企业等行业机修厂及其他单件小批量生产极为有利;它自动化程度高且配有双供电电源与控制系统,同时具有熔炼和保温的功能,对于诸如铸铁管生产的连续作业也很适用,其应用前景必然看好。
中频感应炉的新发展,应引起我国感应炉设计和制造厂家的重视与关注,努力加大自我研制开发的力度,适当辅以引进消化、提高创新,尽快把我国感应炉熔炼技术和设备提高到一个新水平。
声明:本网站所收集的部分公开资料来源于互联网,转载的目的在于传递更多信息及用于网络分享,并不代表本站赞同其观点和对其真实性负责,也不构成任何其他建议。本站部分作品是由网友自主投稿和发布、编辑整理上传,对此类作品本站仅提供交流平台,不为其版权负责。如果您发现网站上所用视频、图片、文字如涉及作品版权问题,请第一时间告知,我们将根据您提供的证明材料确认版权并按国家标准支付稿酬或立即删除内容,以保证您的权益!联系电话:010-58612588 或 Email:editor@mmsonline.com.cn。
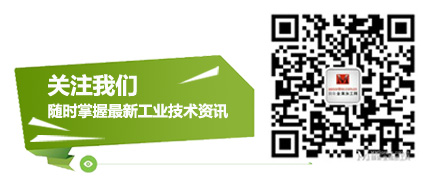
- 暂无反馈